Wie Verbundforschung in Baden-Württemberg gelingen kann
Schwaben haben einen Ruf als findige Tüftler. Zwei aktuelle Beispiele zeigen, wie Unternehmen und Institute in Baden-Württemberg gemeinsam forschen.
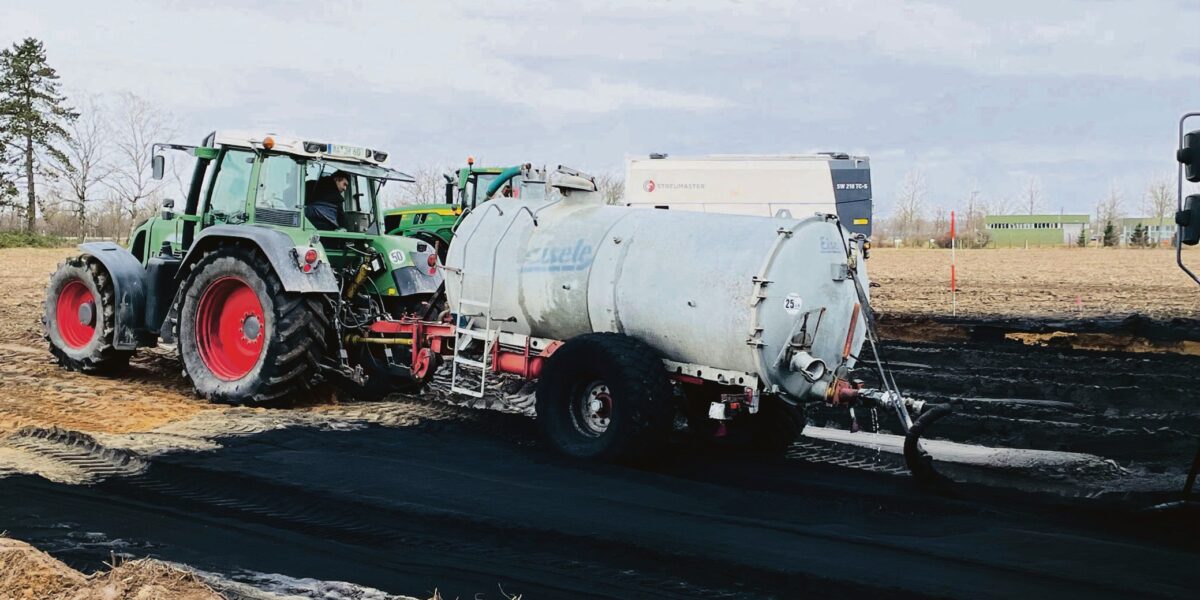
Das BMBF-Projekt PFClean mit Forschenden der Universität Stuttgart erprobt, wie im Boden eingebrachte Aktivkohle schädliche Substanzen binden und so das Grundwasser schützen könnte.
Foto: Vegas, Uni Stuttgart
In Baden-Württemberg, das sich nebenbei selbst „The Länd“ nennt, hat Forschung einen hohen Stellenwert. Die interdisziplinär ausgerichtete Hochschullandschaft ist der fruchtbare Boden, auf dem alles gut wachsen kann. Grundlagenforschung, wie sie beispielsweise im „Cyber Valley“ rund um Stuttgart und Tübingen stattfindet, sind hier genauso wichtig wie die anwendungsorientierte Forschung. Aber die hiesige Wissenslandschaft kann noch mehr: Unternehmen arbeiten gerne mit der Wissenschaft zusammen – sie probieren gemeinsam neue Dinge aus. Ob das nun der rege Austausch im Heilbronner Innovation Park Artificial Intelligence (IPAI) zu künstlicher Intelligenz ist. Oder der Rahmen, den die ARENA 2036 in Stuttgart schafft, wo Firmen mit Forschern auf Augenhöhe im Automotive-Bereich arbeiten.
Stuttgart: Forschungsprojekt soll Boden von chemischen Schadstoffen reinigen
Im Forschungsprojekt „PFClean“ soll die Sanierung persistenter perfluorierter und polyfluorierter Alkylverbindungen vorangebracht werden. Die Ergebnisse könnten allen helfen, die belastete Böden haben. „Wir beschäftigen uns mit dem Ausbreitungs- und Transportverhalten von Schadstoffen. Daraus entwickeln wir Technologien, um diese Schadstoffe aus Boden und Grundwasser herauszubekommen, die wir an zwei Pilotstandorten erproben“, erläutert Claus Haslauer, Hydrogeologe und Leiter der Versuchseinrichtung zur Grundwasser- und Altlastensanierung an der Uni Stuttgart.
Seine neuesten Untersuchungen konzentrieren sich auf zwei typische PFAS-Schadensfälle: Im Rheintal bei Rastatt wurden Abfälle der Papierindustrie großflächig als Dünger aufgebracht, die perfluorierte und polyfluorierte Alkylverbindungen enthalten. PFAS ist der Sammelbegriff dieser chemisch äußerst stabilen Stoffe, die Oberflächen schmutz-, wasser- und fettabweisend machen. Am zweiten Standort war ein 30 Stunden andauernder Großbrand im Jahr 2008 in Reilingen die Ursache: Bei diesem lokalen Schadensfall wurde PFAS-haltiger Feuerlöschschaum verwendet, der teilweise versickerte. Die Gemeinden wissen von der Problematik und informieren die Bürger in Gemeindeversammlungen.
Lesen Sie auch: Das wirtschaftsstarke Ländle setzt auf drei „Leuchttürme der Forschung“
Und: Die Verbindungen treten nicht nur dort auf. Sie sind in der Umwelt so weit verbreitet, dass man sie auch schon am Polarkreis in Eisbärenfett gefunden hat. Sie sind sogar im menschlichen Blut nachweisbar. Haslauer und seine Projektpartner haben deshalb das Verbundprojekt „PFClean“ aufgesetzt, das vom BMBF gefördert wird und über drei Jahre läuft. „In dem Projekt werden wir vier Verfahren weiterentwickeln beziehungsweise anpassen, die geeignet sind, um PFAS aus dem Untergrund auszuschleusen“, sagt Haslauer. Helfen sollen thermische, chemische, mikrobielle Verfahren oder eine Kombination aus allen. Davon funktionieren manche im Grundwasser und manche im Boden. Bis 2026 sollen die Technologien an den beiden Pilotstandorten bis zur Umsetzungsreife gebracht werden.
Mehr als ein halbes Dutzend Verbundpartner aus Wirtschaft und Wissenschaft
Lösen müssen die Verbundpartner eine Vielzahl von Problemen. „Zum einen ist es eine große Schadstoffgruppe: Es gibt mindestens 5000 Einzelsubstanzen, von denen man aber für nur 30 bis 50 Einzelsubstanzen analytische Standards hat“, sagt Haslauer. Eines der beforschten Verfahren ist die Immobilisierung: „Immobilisierung bedeutet, dass ich den Schadstoff zum Beispiel mit Aktivkohle im Boden halte. Und dadurch verhindere, dass er ins Grundwasser gelangt“, macht Haslauer deutlich. Ein weiteres Verfahren nimmt die Ausleitung aus dem Grundwasser in den Blick. Mit einem sogenannten Funnel-and-Gate-System, das wie eine Art Filter funktioniert. Spundwände werden in den Boden gerammt, die das Grundwasser einem „Tor“ zuführen, durch das das Grundwasser fließt und beim Passieren gereinigt wird. „PFAS ist ein recht neuer Kontaminant. Deshalb ist jede Erfahrung, die wird sammeln können, wichtig“, meint der Umweltingenieur. „Wir haben für das Projekt Experten aus verschiedenen Bereichen zusammengeführt, die sich ergänzen“, sagt Haslauer.
Lesen Sie auch: Innovationen aus dem baden-württembergischen Mittelstand
Partner kommen teils aus der Wirtschaft: Arcadis etwa ist ein internationales Ingenieurbüro, das Erfahrung in der Erkundung und Sanierung von PFAS-Schadensfällen hat. Die Altlastensparte der Geiger Entsorgung GmbH ist dabei. Die Sax+Klee GmbH aus Mannheim bohrt den Zirkulationsbrunnen, den die Industrie Engineering GmbH baut. Firma Wirtgen hat dabei geholfen, Immobilisierungsmaterial in den Boden einzuarbeiten. Von wissenschaftlicher Seite sind außerdem das Technologiezentrum Wasser dabei, die Universität Tübingen und die PFAS-Geschäftsstelle des Landratsamts Rastatt. Immerhin liegt seit mehr als einem Jahr ein Beschränkungsvorschlag zur europaweiten Herstellung und Verwendung von PFAS vor. Dennoch warnten Industrievertreter kürzlich vor einem Totalausstieg.
Ellwangen: Batteriehersteller Varta in der Krise
In Ellwangen in Ostwürttemberg hat die Varta AG ihren Stammsitz. Das Unternehmen gibt es seit knapp 140 Jahren, mit vielen Hochs und Tiefs. „Klar ist: Wir stehen vor Herausforderungen und werden sie meistern“, sagt Pressesprecher Christian Kucznierz, Was er damit meint: Der hoch verschuldete Konzern steckt mitten in einem Restrukturierungsprozess, verhandelt mit seinen Kreditgebern über ein neues Sanierungskonzept. Im Zuge dessen musste Varta im letzten Jahr einen Sparkurs einleiten und dabei auch Arbeitsplätze abbauen. Heute sind es weltweit noch 4200 Beschäftigte. Die Krise des Batteriekonzerns ist eine Kombination unterschiedlicher Faktoren: höhere Kosten infolge des Ukrainekriegs, die Verschlechterung der Konsumlaune und Veränderungen in der Lieferkette bei einigen Kunden. Hinzu kam dieses Jahr im Februar auch noch ein Cyberangriff, der zumindest bei den internen Prozessen immer noch nachwirkt. Er hat die angespannte Finanzlage noch verschärft. Seit Mai hat das Unternehmen einen neuen CEO. Michael Ostermann bringt Erfahrungen aus dem Batterie- und dem Automotive-Bereich mit, kennt sich mit Restrukturierungsprozessen aus.
Lesen Sie auch: Wie das Lithium in die Batterie kommtVarta produziert seine Zellen hoch technisiert in Deutschland. Für die Produktion einer Lithium-Ionen-Knopfzelle etwa wird mehr als die Hälfte von insgesamt 52 Produktionsschritten auf einer Maschine gefertigt. „Der hohe Automatisierungsgrad ist einer der Gründe, warum sich die Produktion am Standort Deutschland rechnet“, erläutert der Pressechef. Produziert wird im sogenannten Varta-Dreieck. In Ellwangen werden Hörgerätebatterien und großformatige Lithium-Ionen Rundzellen hergestellt. Eine Energiespeicherproduktion befindet sich in Neunheim, einem Ellwanger Stadtteil. Aus dem Werk Nördlingen in Bayern kommen Lithium-Ionen Knopfzellen und ebenfalls Energiespeicher. In Dischingen stellt Varta Haushaltsbatterien für eine Vielzahl von Geräten her.
Forschung und Entwicklung am Stammsitz in Baden-Württemberg
„Wir spielen als Batterieindustrie eine wichtige Rolle zur Sicherung der wirtschaftlichen Widerstandsfähigkeit Europas“, betont Kucznierz. Denn: Batterietechnologie ist eine Schlüsseltechnologie. Ohne sie kann die Mobilitäts- und Energiewende nicht gelingen. Es gibt auch gute Nachrichten aus Ellwangen: Forschung und Entwicklung nehmen bei Varta einen hohen Stellenwert ein. 2020 zum Beispiel erhielt Varta von Bund, Baden-Württemberg und Bayern für ein EU-Projekt Förderzusagen in Höhe von 300 Mio. €. Unter anderem wurden damit Lithium-Ionen-Zellen mit höherer Energiedichte bis zur Marktreife entwickelt.
Lesen Sie auch: Warum Deutschland zum Mekka für Lithium werden kann
Das jüngste F+E-Projekt geht gerade in die Startlöcher. Es heißt Entise und erhält eine Förderung des Bundesforschungsministeriums von insgesamt 7,5 Mio. €. Varta und 14 Partner aus Industrie und Wissenschaft erarbeiten umweltverträgliche Alternativen für die Lithium-Ionen-Technologie. Sie soll durch Natrium-Ionen ersetzt werden. Natrium steckt etwa in Kochsalz, ist also leichter verfügbar als das teure Lithium. „Die Idee ist, dass am Schluss eine Zelle für die stationäre Energiespeicherung entsteht, die auch in industriellen Maßstäben produziert werden kann“, fasst Kucznierz zusammen. Dafür liefern die Partner Rohmaterial wie Anoden, Elektrolyte, die in einem Demonstrator zusammengebaut werden. Natrium-Ionen-Technologien gibt es bereits. „Aber nun geht es darum, diese zu verbessern“, so Kucznierz. Der Projektstart war am 1. Juni 2024, die Laufzeit beträgt drei Jahre.
Ein Beitrag von: