Ein Fassaden-Puzzle mit Sonderformaten
3D-Planung, Erweiterungsinvestitionen und vor allem das Know-how bei der Fertigteilproduktion aus Textilbeton waren wesentliche Auftragnehmerqualitäten, die die Zusammenarbeit von der Beton- und Naturstein Babelsberg GmbH (BNB) mit dem Architektenbüro von Oliver Collignon bei dem Bauprojekt der U-Bahnstation Rotes Rathaus in Berlin zum sichtbaren Erfolg führten. Das besondere an dem Projekt stellt uns BNB-Geschäftsführer Manuel Vöge im Interview vor.
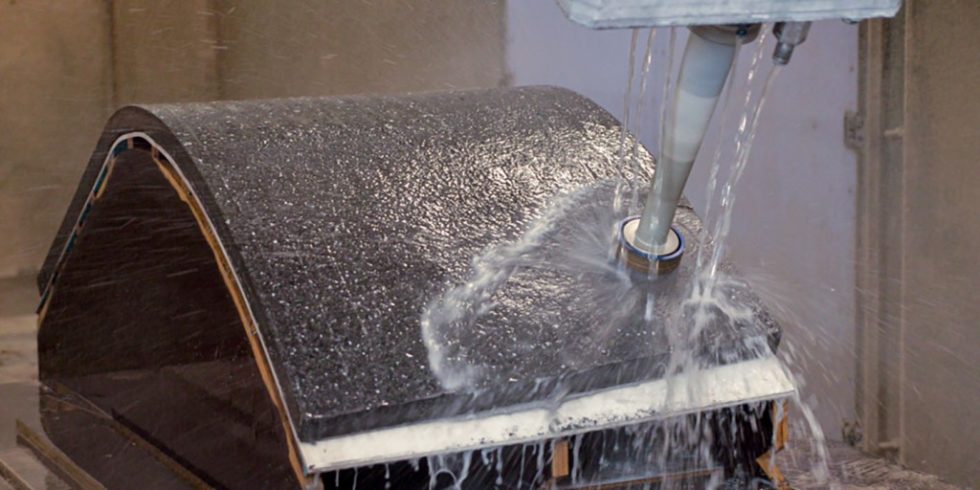
Mit der CNC-Fräse werden die Textilbetonteile bearbeitet.
Foto: BNB
Das legendäre Berliner Rote Rathaus hat ober- und unterirdisch eine starke italienische Komponente. Während das vierflügelige Backsteingebäude im Stil der frühitalienischen Renaissance seit 150 Jahren das Stadtbild prägt, sorgt erst seit wenigen Monaten in der gleichnamigen neuen U-Bahnstation ein Baustoff aus Italien für wirkungsvollen Kontrast: dunkler Marmorkies in schwarzen und weißen Terrazzoplatten. Mit über 6.500 Fertigteilen hat die Beton- und Naturstein Babelsberg GmbH (BNB) jetzt eines der bisher größten deutschen Textilbeton-Projekte abgeschlossen. Die Herausforderungen bei dem Projekt kennt BNB Geschäftsführer Manuel Vöge.
Jedes Großprojekt hat seine Vorgeschichte…
… dieses bis auf die Tatsache, dass wir seit fast zehn Jahren bei Fertigteilen auch auf Textilbeton setzen, eher nicht. Das Architekturbüro war uns zuvor völlig unbekannt, obwohl Oliver Collignon und ich, wie wir jetzt wissen, in Berlin voneinander nur wenige Straßen entfernt wohnen. Der für uns größte Auftrag in der 50-jährigen Firmengeschichte von BNB begann 2016 mit einem vagen Anruf: „Kennt ihr in Europa jemanden, der Erfahrungen mit geschliffenen Textilbetonfassaden hat…?“ Wir hatten.
Der Auftrag hat Ihre Firma vier Jahre lang stark in Anspruch genommen. Was waren die besonderen Herausforderungen?
Zweifelsfrei Dauer, Volumen und Schwierigkeitsgrad: Nur wenige der Terrazzo-Elemente konnten von der Stange produziert werden. Sonderformate mit Krümmungen haben das Fassaden-Puzzle mit schlussendlich rund 3.500 Teilen in Schwarz und Weiß bestimmt. Das musste vorher alles in 3D geplant und berechnet werden. Um den Durchlauf von täglich bis zu sechs, in Spitzenzeiten sogar noch weit mehr Teilen zu sichern, haben wir eine neue Halle gebaut und mehrere neue Mitarbeiter eingestellt. Parallel dazu musste ein zweiter fünfachsiger CNC-Automat angeschafft werden. Ganz wichtig für die immer gleichbleibende Materialzusammensetzung in entsprechenden Qualitäten, Farben und Oberflächen: Wir mussten die gesamte Zulieferlogistik neu überdenken.
Sonderformate in Textilbeton
An beiden Bahnsteigkanten auf 120 Meter Länge sieben Fassadenteile übereinander – warum wurden so viele Sonderformate benötigt?
Der Architekt hat uns drei weitere besondere Aufgaben gestellt, die wir bisher so noch nicht umgesetzt hatten: Ein Kriterium für das besonderes dynamisches Erscheinungsbild dieses Bahnhofs sind beispielsweise schwungvolle Fassadenteile, mit denen die Kanten hin zu den Fahrtreppen-Schächten abgerundet werden. Ein andere Schwierigkeit war das leichte Gefälle des Bahnhofs und die darauf resultierenden Herausforderungen an ein einwandfreies horizontales Fugenbild. Wir haben dieses Problem durch exaktes Aufmaß, Überleitung in CNC-Daten und letztlich CNC-Schliff gelöst. Die dritte Herausforderung: Sämtliche Platten der Vorhangfassade mussten mit Blick auf die TÜV-Sicherheitsprüfungen am Schalungsbeton vollständig abnehmbar sein.
Die drei neuen U-Bahnhöfe in der alten Mitte Berlins sind Zeugnisse modernsten Bauens und Touristenmagnete zugleich. Sie sind beim weiteren Ausbau der Metrolinien wieder mit dabei?
Wenn man dazu unser Know-how und unsere Potenziale als innovativer Fertigteilhersteller benötigt, dann wieder gern. Mit Blick auf die vier Jahre „unter Tage“ ließe sich inzwischen auch einiges an Aufwand optimieren – beispielsweise die Baustellenlogistik. Wir würden dann eine CNC-Fräse vor Ort einsetzen. Leichtbaufassaden sind für uns auch über den Verkehrsbau hinaus ein Forschungs- und Entwicklungsschwerpunkt. Weitere sind im Teamwork mit Wissenschaftspartnern zwischen Berlin, Leipzig und Braunschweig Fassetten des grünen Betons. Wir sind sicher, dass durch stärkere Nachhaltigkeitszwänge im Bau die von uns begleiteten Themen Recycling- und Geopolymerbeton in den nächsten Jahren mehr denn je gefragt sein werden. Wir setzen diese zertifizierten Materialien mit geringerem CO2-Fußabdruck heute schon für Fertigteile im Outdoor-Bereich ein. Da ist noch viel Luft nach oben, sage ich mal an die Adresse von Architekten, Planern und Bauherren gerichtet.
Das könnte Sie auch interessieren:
Recycelter Beton ist einsatzbereit