Neue Betonrezeptur spart enorme Baukosten
Immer mehr Gebäude bestehen aus Beton, dabei ist dieser Baustoff bereits das meistgenutzte Baumaterial auf der Welt. Schlankere Strukturen, kostengünstigeres Bauen und Materialeinsparungen sind jetzt mit einer neuen Betonrezeptur für selbstvorgespannte Betonelemente möglich.
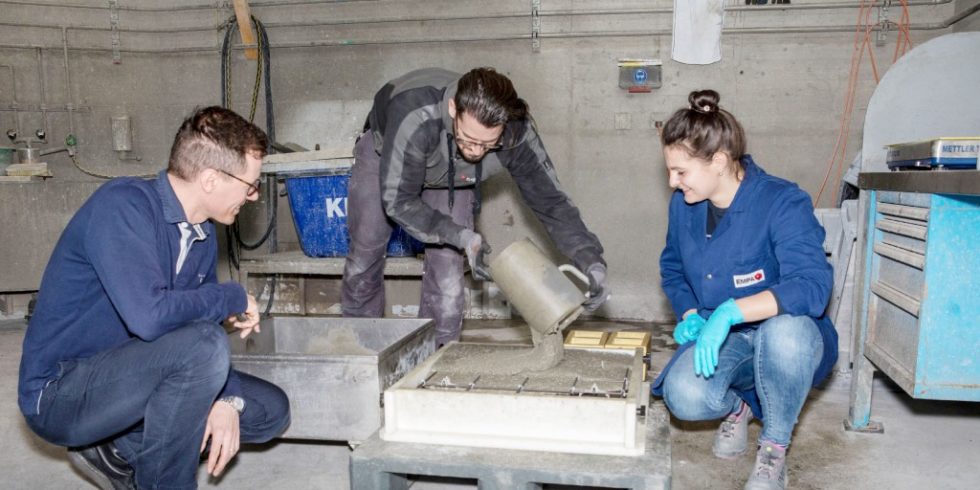
Die Empa-Forschenden Mateusz Wyrzykowski und Volha Semianiuk untersuchen mithilfe von Labortechniker Sebastiano Valvo neue Möglichkeiten für selbstvorgespannte CFK-Betonelemente.
Foto: Empa
Zehn Milliarden Tonnen Beton werden jährlich weltweit hergestellt und verbaut. Diese riesige Menge hat großen Einfluss auf die weltweite Umweltbelastung, obwohl die verursachten Emissionen und die benötigte Energie bei der Herstellung einer Tonne Beton nicht so hoch sind, wie bei anderen Baumaterialen. Das Bindemittel im Beton, der Zement, ist der Hauptverantwortliche für die hohen Energiewerte. Drei Prozent der weltweiten Primärenergie werden für die jährlich benötigten vier Milliarden Tonnen Zement aufgebracht. Bis zu acht Prozent der weltweiten CO2-Emissionen gehen auf die Zementproduktion zurück. Doch ein Ende für den Beton und ein Ersatz sind nicht in Sicht, denn Beton hat als Baustoff zu viele Vorteile. Daher ist ein nachhaltiger Umgang mit Beton unumgänglich. Dieser kann bei der Produktion beginnen, beim sparsamen Materialeinsatz weitergehen und den Abbruch und das Recycling von Beton beinhalten.
Stabilität von Betonelementen die hohe Lasten aufnehmen
Um den Materialverbrauch von Beton zu senken, entwickeln die Forscher an der Empa Methoden für schlankere Beton-Elemente, die trotzdem langlebig und stabil sind. Ein europäisches und ein US-amerikanisches Patent wurde erst kürzlich an eine Forschergruppe um Giovanni Terrasi, Pietro Lura und Mateusz Wyrzykowski vergeben. Das Patent beinhaltet eine selbst-vorspannende Betontechnologie. Wenn ein Betonelement sehr große Lasten aufnehmen muss, wie es bei Brücken oder auskragenden Bauteilen der Fall ist, dann kommen meist Vorspannungen zum Einsatz. Die Spannglieder, die in der Regel aus Stahl sind, werden in einer Spannbettvorrichtung vor auf beiden Seiten des Elements verankert und unter Zug gesetzt. Dann wird der Beton eingebracht. Nachdem der Beton ausgehärtet ist, wird die Spannung wieder gelöst. Daraufhin beginnen die Kräfte in den Spanngliedern zu wirken. Sie setzen den Beton unter Druckspannung. Hier entsteht die Stabilität, denn durch die vorgespannte Bewehrung wird das Element von beiden Seiten zusammengezogen. Damit die Stabilität bestehen bleibt, muss der rostanfällige Stahl durch den Beton geschützt werden. Dies geschieht durch eine bestimmte Mindestdicke des Betons.
Carbonfasern statt Stahl um dem Rost zu entgehen
Anstelle von Stahl als Bewehrung kommt seit den 1990er-Jahren auch carbonfaserverstärkter Kunststoff (CFK) zum Einsatz. CFK hat den Vorteil, dass er nicht korrodiert. Das ermöglicht schlankere Betonbauteile, da die schützende Schicht geringer ausfallen darf. Somit findet auch weniger Materialeinsatz statt. „Will man diese CFK-Armierungen ebenfalls vorspannen, um damit noch dünner und stabiler bauen zu können, stößt man aber an Grenzen“, sagt Wyrzykowski. Die benötigten Spannbettvorrichtungen sind sehr teuer und CFK-Stäben sind bei der Verankerung komplizierter als Spannstahl.
Betonrezeptur ermöglicht mehr Stabilität
Genau mit dieser Stelle, die Verankerung der Elemente, hat sich das Empa-Team beschäftigt. Sie haben es geschafft, dass sie auf die Verankerung auf beiden Seiten des Beton-Elements verzichten können. Bei ihnen macht der Beton die Arbeit selbst. Hierzu haben sie eine Betonrezeptur entwickelt, bei der sich der Beton beim Aushärten ausdehnt. Die CFK-Stäbe im Beton werden durch seine Expansion unter Zug gesetzt. Dadurch werden sie automatisch vorgespannt. Die Forscher zeigen mit ihren Laborversuchen, dass die selbstvorgespannten CFK-Betonelemente rund dreimal mehr Lasten tragen können, als ein nicht vorgespanntes CFK-Betonelement. Damit stehen neue Wege im Leichtbau offen. „Wir können nicht nur stabiler bauen, sondern brauchen dafür auch weniger Material“, sagt Wyrzykowski und beschreibt neue Anwendungsfelder: „Wir können gleichzeitig in mehrere Richtungen vorspannen, etwa für dünne Betondecken oder filigrane gekrümmte Betonschalen“. Damit die Anwendungsmöglichkeiten weiterentwickelt werden, bekommen die Forscher jetzt Unterstützung von BASF als Industriepartner.