Verschleiß von Parkplatzoberflächen praxisgerecht prüfen
Die Verschleißbeständigkeit von befahrenen Oberflächenschutzsystemen für Parkbauten zu bewerten, ist mit den gegenwärtigen normativen Prüfverfahren schwierig bis unmöglich. Daher wurde ein praxisnahes Verfahren konzipiert. In einem Forschungsprojekt mit der Technischen Universität Kaiserslautern wird dieses weiterentwickelt.
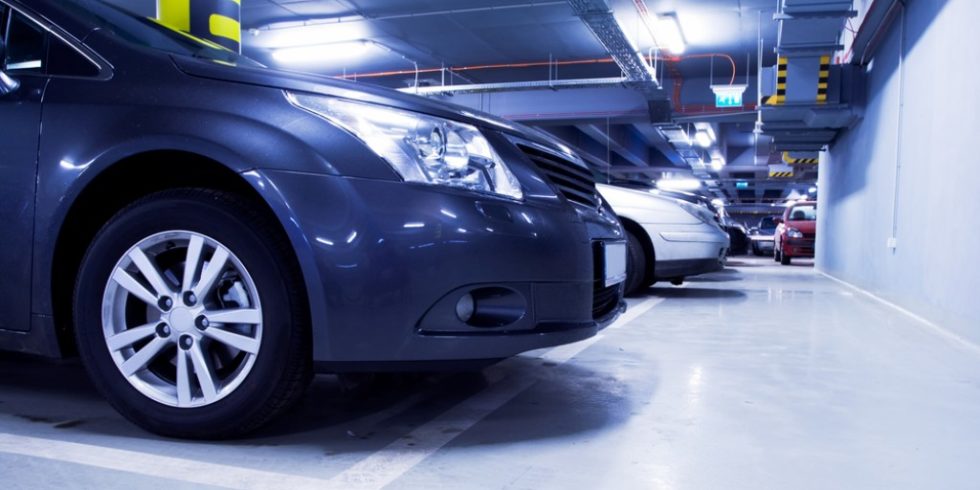
Ein praxisnahes Verfahren soll die Verschleißbeständigkeit von Oberflächenschutzssystemen prüfen.
Foto: panthermedia.net/blasbike
Die Dauerhaftigkeit von Stahlbetonkonstruktionen in Parkbauten kann durch die Verwendung von Oberflächenschutzsystemen sichergestellt werden. Diese verhindern, dass aggressive Substanzen, wie zum Beispiel chloridhaltiges Wasser, bis zur Bewehrung vordringt und diese schädigt. Doch die Oberflächenschutzsysteme sind durch das Befahren mit Pkw selbst mechanischen Verschleißbeanspruchungen ausgesetzt.
Realitätsnahe Beanspruchung entscheidend für den Praxistest
Um die sehr unterschiedliche Dauerhaftigkeit dieser Systeme zu beurteilen, stehen nach der Richtlinie für Schutz und Instandsetzung von Betonbauteilen des Deutschen Ausschuss für Stahlbeton e. V. (DAfStb) mehrere standardisierte Prüfverfahren zur Verfügung. Methoden, wie beispielsweise der Taber-Abraser-Test oder das BCA-Verfahren, sind dabei aus anderen Bereichen, wie zum Beispiel zur Prüfung von Zement- und Kunstharzestrichen, entliehen. Mit diesen Tests ist die realitätsnahe Verschleißbeanspruchung in einem Parkhaus jedoch nicht darstellbar. Das liegt daran, dass mit ihnen eine andere Belastungsart mit zu niedriger Auflast simuliert wird. Daraus resultierend bestehen die Oberflächenschutzsysteme diese Prüfungen und können hinsichtlich ihrer Verschleißbeständigkeit nicht unterschieden oder gar klassifiziert werden.

Im Prüfstand des Parking Abrasion Tests wird die mechanische Verschließbeanspruchung von Oberflächenschutzsystemen getestet.
Foto: Sika Deutschland GmbH
Prüfstand simuliert Reifenbelastung
Eine Quantifizierung der Dauerhaftigkeit bei mechanischer Beanspruchung ist mit neu entwickelten Prüfverfahren möglich. Diese sind derzeit jedoch nicht normativ geregelt. Das in Fachkreisen inzwischen bekannteste Verfahren ist der Parking Abrasion Test (PAT).
Der Prüfstand für den Parking Abrasion Test besteht aus einem im 90-Grad-Auslenkwinkel rotierenden Pkw-Reifen mit der Auflast eines Pkw-Rades von 450 Kilogramm. Nach einer Rotation (und auch Rückrotation) wird durch eine Pause verhindert, dass sich die Oberfläche durch die Reibung zu stark erhitzt und die Glasübergangstemperatur erreicht wird. Durch die Reifendrehung bilden sich Scherkräfte, wie sie beim Einparken und Rangieren in einer Parklücke entstehen können. Anfahr- und Bremskräfte, die üblicherweise in Kurven und an Rampen wirken, werden mit jeder neuen Rotation simuliert. In Summe ist eine Prüfdauer von bis zu 15 000 Zyklen vorgesehen. In zeitlichen Intervallen ist es möglich, den Verschleiß zu dokumentieren.
Neben der visuellen Begutachtung und der Dokumentation mit der Kamera ist eine zerstörungsfreie Aufzeichnung möglich. Hierfür stehen zwei Verfahren zur Verfügung: die magnetisch-induktive Schichtdickenmessung und das 2D-/3D-Laserscanning. Beide Verfahren liefern trotz der Oberflächenrauheit sehr genaue reproduzierbare Ergebnisse, wobei für die magnetisch-induktive Schichtdickenmessung die Probenvorbereitung aufwendiger ist und die Auswertung nur an einem „Messstreifen“ erfolgt. Das 2D-/3D-Laserscanning ermöglicht die Erfassung der kompletten Oberfläche, generiert gleichzeitig jedoch sehr viele Messdaten (ca. 500.000 Messwerte je Messung).
Bohrkern dient der Verschleiß-Klassifizierung
Eine weitere Maßnahme für die Bestimmung der Abtragstiefe stellt der Feinschnitt eines Bohrkerns dar. Dies wird mit Beendigung des Versuchs an der optisch am stärksten verschlissenen Stelle entnommen . Für einen Vergleich ist es notwendig, einen weiteren Bohrkern von einer unbelasteten Stelle zu entnehmen. Mit Erreichen der 15.000 Zyklen (und bei Bedarf auch zwischendurch) kann der Probekörper in Abhängigkeit von der Verschleißstärke klassifiziert werden. Hierfür stehen fünf (bzw. sechs) Verschleißklassen zur Verfügung. Die Klassifizierung beruht im Wesentlichen auf der visuellen Begutachtung. Mit zunehmendem Verschleiß erfolgt die Eingruppierung in eine höhere Klasse.
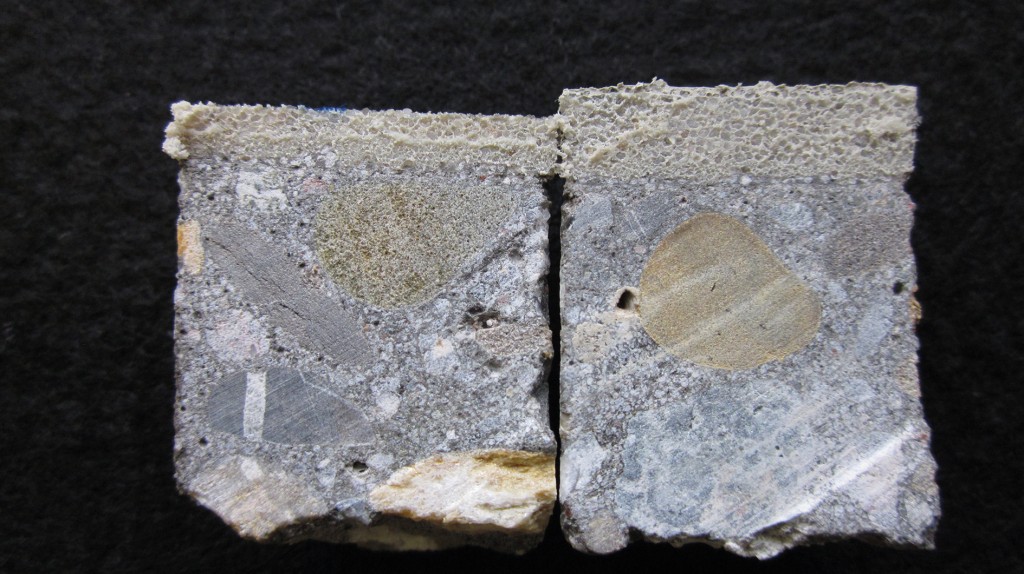
Die Verschleißbestimmung des Oberflächenschutzsystems findet am Bohrkern statt: Links die Probe der am stärksten verschlissenen Stelle, rechts die unbelastete Vergleichsfläche.
Foto: Sika Deutschland GmbH
Die Forschungsergebnisse haben gezeigt, dass die Oberflächenschutzsysteme ein unterschiedliches Verschleißverhalten aufweisen. In der Regel sind die starren Systeme (OS 8) verschleißärmer, während die rissüberbrückenden, elastischen Systeme zu einem höheren Verschleißvolumen neigen. Eine Differenzierung der im System geprüften Produkte in Verschleißklassen ist möglich. Ebenfalls stimmen die Verschleißbilder mit denen in der Praxis vorzufindenden Schadensbilder überein. Die Simulation weiterer zusätzlicher praxisnaher Beanspruchungen, wie zum Beispiel eine Wasserbeaufschlagung oder auch Splitt, ist bei Bedarf durchführbar.
Nicht möglich jedoch ist auf Basis der Prüfung mit dem Parking Abrasion Test eine direkte Berechnung der Lebensdauer von befahrenen Systemen. Zum einen ist die Beanspruchung beim Parking Abrasion Test punktuell höher als in der Realität, während zusätzliche Belastungen, wie eine Wasserbeaufschlagung in dem Grundtest, unberücksichtigt bleiben. Zum anderen sind auch nur wenige Daten aus der Praxis bezüglich der Befahrung einzelner Stellflächen oder Kurven und Rampen überliefert, was für eine Korrelation unabdingbar ist.
Antrag auf Zulassung als normatives Prüfverfahren
Unabhängig davon bildet der Parking Abrasion Test den Verschleiß realitätsnah ab. Die Sika Deutschland GmbH unterzieht bereits heute alle ihrer befahrenen Oberflächenschutzsysteme diesem Prüfverfahren. Das neue OS 11a-System von Sika auf Basis der i-Cure-Technologie war bei extrem klimatischen Bedingungen (8°C, 80% r. L.) auch nach 5.000 Testzyklen noch völlig intakt.

Beispiel für die Auswertung des Oberflächenverschleißes in der Profilmitte nach 5 000, 10 000 und 15 000 Prüfzyklen. Grafik: Sika Deutschland GmbH
Unter der Federführung der Technischen Universität Kaiserslautern erarbeitet derzeit ein Konsortium mit allen am Bau beteiligten Fachkreisen die Etablierung des Parking Abrasion Tests als normatives Prüfverfahren.