Hybrid-Autobahn: Beton für Brummis, Asphalt für Pkw
Auf einem Abschnitt der A61 bei Koblenz wurde in Fahrtrichtung Köln erstmals in Deutschland eine durchgehend bewehrte Betonfahrbahn in horizontaler Hybridbauweise hergestellt.
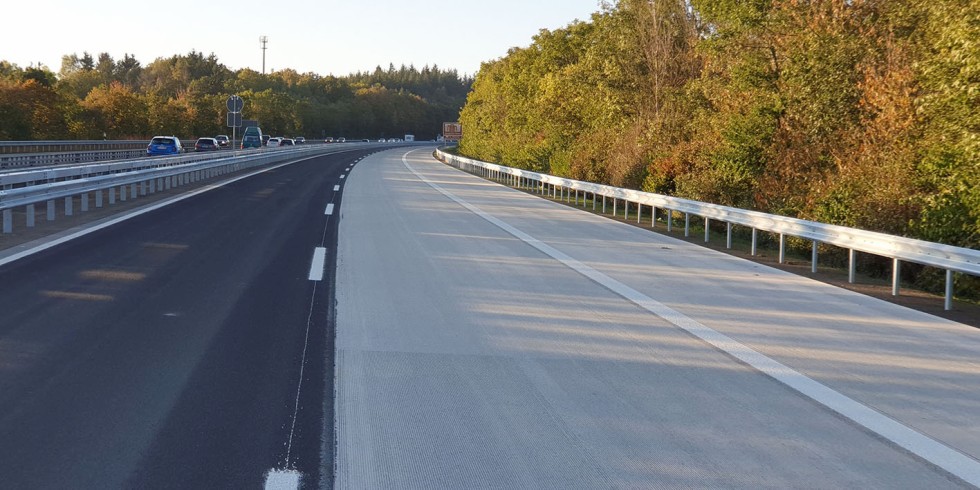
Links Asphalt, rechts Beton: Experten erhoffen sich eine Nutzungsdauer der Betonfahrbahn von bis zu 50 Jahren, obwohl hier vor allem schwere Lkws rollen.
Foto: Schnorpfeil
Wer auf deutschen Autobahnen unterwegs ist, kennt das Phänomen: Sobald die Fahrbahndecke aus Beton besteht, entstehen alle etwa fünf oder sechs Meter beim Überfahren der Fugen zwischen den Betonplatten leichte, aber regelmäßige Fahrgeräusche. Die Fugen sind notwendig, um eine unkontrollierte Rissbildung in der Betonfahrbahn zu vermeiden (siehe Kasten ganz unten).
Durchgehend bewehrte Fahrbahn hat Vorteile
Doch es geht noch besser: Eine durchgehende Bewehrung macht die in die Betonoberfläche eingeschnittenen Fugen überflüssig. Damit entfällt einerseits der durch sie verursachte Erhaltungs- und Pflegeaufwand, andererseits steigen Fahrkomfort und Lebensdauer der Fahrbahn. Dabei sorgt die durchgehenden Längsbewehrung für eine gleichmäßige Verteilung der Querrisse in Fahrbahnrichtung und führt zu einer Minimierung der Rissbreite.
Darüber hinaus können Fahrbahnen mit durchgehender Bewehrung in ihrer Einbauhöhe reduziert werden, was zu einer Schonung natürlicher Ressourcen beiträgt. Die Bauweise mit durchgehender Bewehrung ist jedoch aufgrund der Verwendung des Bewehrungsstahls teurer in der Herstellung, weswegen sie sich bisher in Deutschland nicht durchgesetzt hat.
Stattdessen findet man immer öfter in Hybridbauweise gebaute Autobahnen, die den richtigen Baustoff an die richtige Stelle bringt: Während die hauptsächlich von Pkw befahrene Überholspur konventionell aus Asphalt besteht, wird die durch Lkw stark beanspruchte rechte Fahrspur als Betonfahrbahn ausgeführt – allerdings in Deutschland bislang in der kostengünstigeren Plattenbauweise.
Neuartige Hybridbauweise mit durchgehender Bewehrung eingesetzt
Erstmals wurde nun in Deutschland eine horizontale Hybridbauweise eingesetzt, die Asphaltfahrbahnen und eine Betonfahrbahn für den Schwerlastverkehr mit durchgehender Bewehrung kombiniert. Zwischen den Spuren aus unterschiedlichem Material wird eine längs verlaufende Dehnungsfuge benötigt, unter der eine Drainage dafür sorgt, dass Wasser versickern kann, ohne die Tragschicht zu beschädigen.
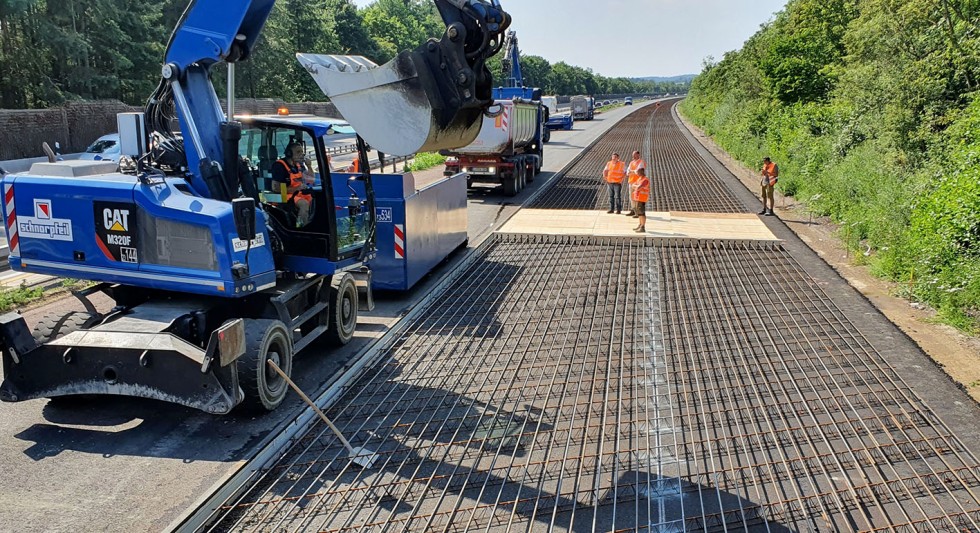
Bei der horizontalen Hybridbauweise wird nur die rechte Fahrbahn sowie der Standstreifen als durchgehend bewehrte Betonfahrbahn ausgeführt.
Foto: Schnorpfeil
Auf dem Weg zur Standardbauweise
In Belgien und den USA bestehen bereits umfangreiche, positive Erfahrungen mit durchgehend bewehrten Fahrbahndecken aus Beton. Auf der A61 wurde somit ein Verfahren umgesetzt, das gute Aussichten hat, in den nächsten Jahren zur Standardbauweise für hochbelastete Autobahnabschnitte zu werden. Bauherrin der vier Kilometer langen Pilotstrecke zwischen den Anschlussstellen Boppard Buchholz und Waldesch in Fahrtrichtung Köln ist die Niederlassung West der Autobahn GmbH.
Erkenntnisse zur Lärmminderung erwartet
Auch zum Thema Minderung von Lärmemissionen soll das Pilotprojekt auf der A61 neue Erkenntnisse liefern. Bei Fahrbahndecken aus Beton können Fahrgeräusche durch Texturierung (Strukturierung) der Betondecke reduziert werden; hier laufen aktuell Studien zur Dauerhaftigkeit der lärmreduzierenden Eigenschaft.
In diesem Zusammenhang wurden auch auf dem Autobahnabschnitt bei Koblenz verschiedene Texturvarianten mittels Einschleifen einer Struktur in die erhärtete Betondecke (Grinding) aufgebracht. Weil bei durchgehend bewehrten Betonfahrbahnen keine quer verlaufenden Dehnungsfugen vorhanden sind, lässt sich dieses Verfahren leichter als sonst anwenden.
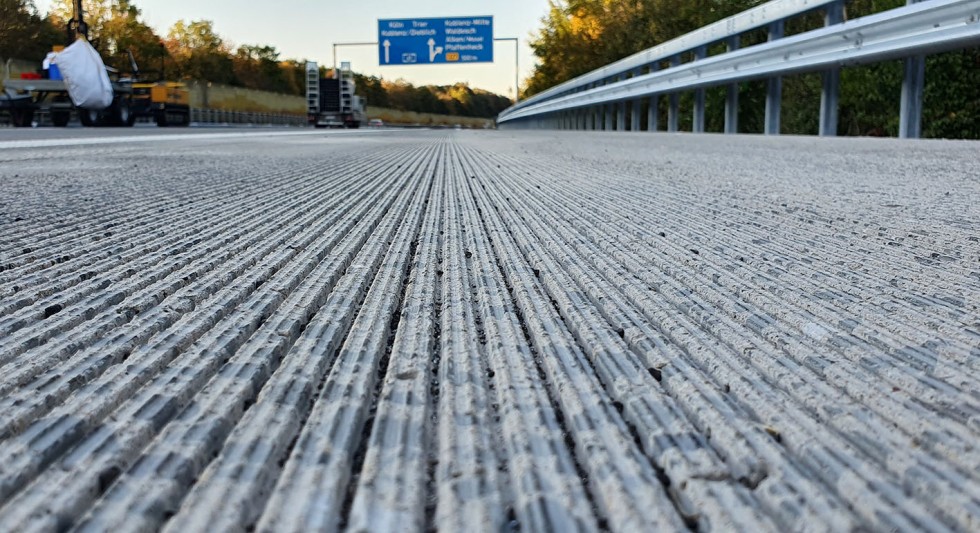
Auch die Verringerung der Lärmemissionen durch Texturierung der Betondecke wird auf der Pilotstrecke bei Koblenz getestet.
Foto: Schnorpfeil
Höhere Nachhaltigkeit durch erhöhte Nutzungsdauer
Experten erhoffen sich von bewehrten Betonfahrbahnen eine Nutzungsdauer von bis zu 50 Jahren. Bei Betonfahrbahnen in Plattenbauweise geht man von einer Nutzungsdauer von etwa 30 Jahren aus. Zur Überprüfung aller Bewegungen werden Sensoren in die Fahrbahn eingebaut. So kann die das Projekt eng begleitende BASt (Bundesanstalt für Straßenwesen) die gesammelten Werte zusammen mit denen einer Vergleichsstrecke über mehrere Jahre auswerten.
Ausführung mit nachhaltigerem Zement
Mit der Ausführung wurde das Bauunternehmen Schnorpfeil aus Treis-Karden beauftragt. In der von Schnorpfeil eigens auf der Baustelle errichteten mobilen Mischanlage wurde ein Dyckerhoff HOZ Doppel (CEM III/A 42,5 N) aus dem Werk Neuwied eingesetzt, also ein Hochofenzement, wie er auch bei ähnlichen Projekten in Belgien zum Einsatz kam. Gegenüber Portlandzement (CEM I) weist er einen geringeren CO2-Fußabdruck auf.
Auch die Frostschutzverfestigung wurde mit Dyckerhoff-Zement hergestellt. Zur Anwendung kam hier ein TrZ Doppel (CEM II/B-P 42,5 N), ebenfalls aus dem Werk Neuwied.
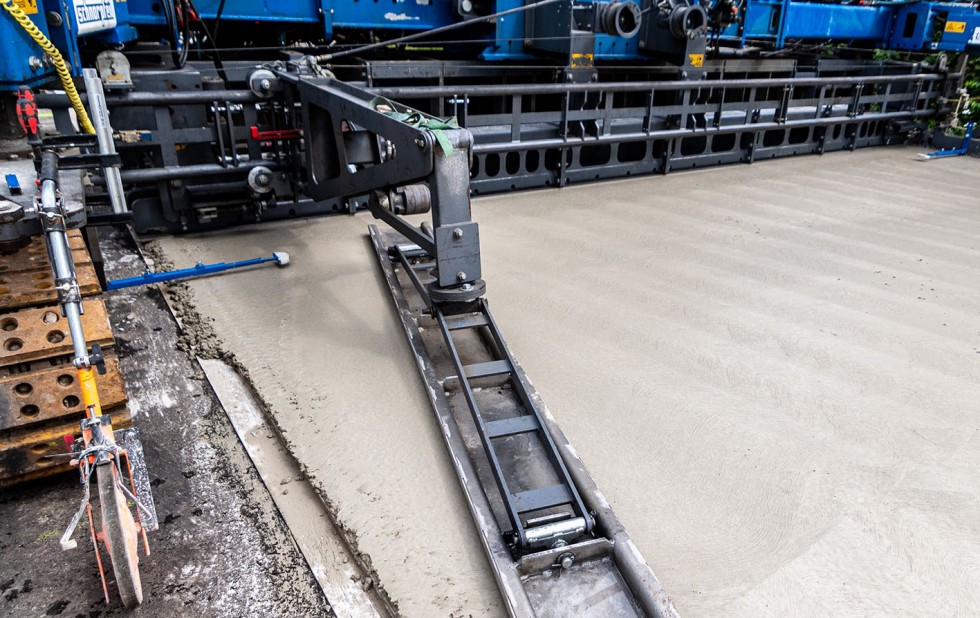
Für die Fahrbahndecke kam ein Hochofenzement zum Einsatz, der nachhaltiger ist als Portlandzement.
Foto: MPA Stuttgart
Beton im Straßenbau
Generell kommt im Straßenbau Beton dann zum Einsatz, wenn hohe Tragfähigkeit und Tragreserven, dauerhafte Oberflächeneigenschaften und lange und gute Befahrbarkeit gefordert sind. Dieses Gebrauchsverhalten entsteht durch eine wirksame Lastverteilung auf die Unterlage bei im Laufe der Jahre zunehmender Betonfestigkeit. Die Verformungsstabilität (sehr gute Längsebenheit und gleichbleibende Querebenheit) des Baustoffs führt zu einer dauerhaften Oberflächengeometrie mit zuverlässigem Oberflächenwasserabfluss.
Für die Umwelt positiv wirkt sich aus, dass Beton keine Gefahr für Boden und Grundwasser darstellt und vollständig wiederverwendet werden kann. Lange Instandsetzungsintervalle reduzieren die Anzahl benötigter Baustellen und damit das Risiko für Staus sowie Unfälle.
Das könnte Sie auch interessieren:
Weitere Beiträge aus zum Infrastrukturbau
Robot – Straßenbau 4.0: Praxis-Demo zum autonomer Asphalteinbau auf der B 189