Direkte Drehmomentmessung am Antrieb
In diesem Beitrag wird ein variables, hochgenaues Drehmomentmesssystem für die Antriebstechnik vorgestellt. Es ermöglicht einen direkten, raumsparenden Einbau und ist für Feldmessungen und für Zustandsbeobachtungen bestens geeignet.
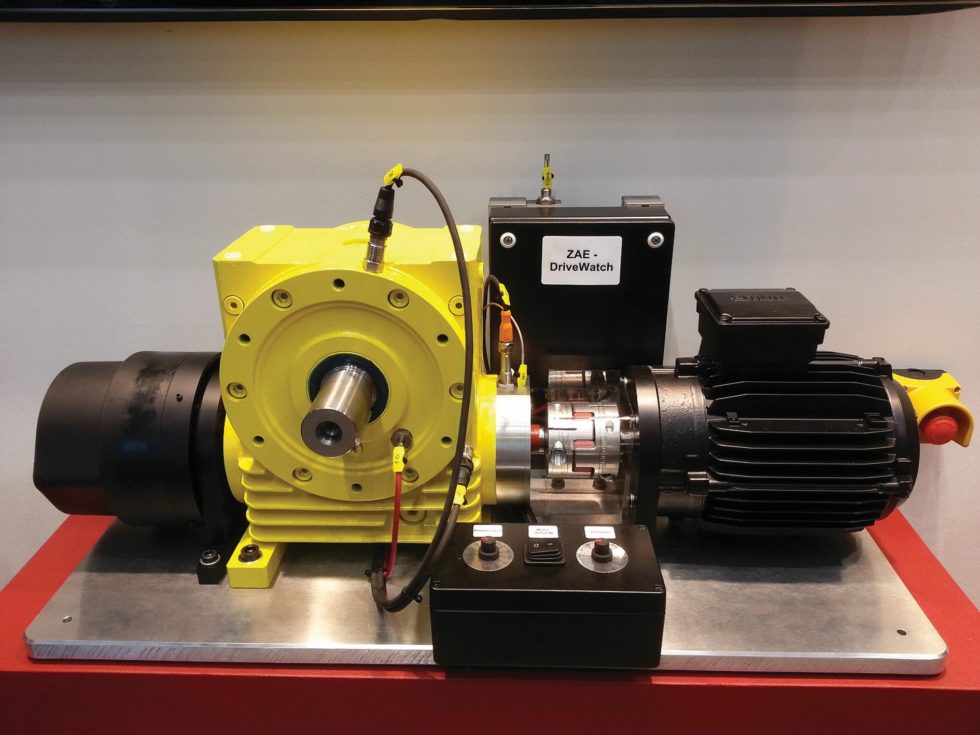
ZAE-DriveWatch-Demonstrator mit eingebauten Messsystemen und Messdatencontroller. Bild: ZAE
Die Anforderungen an die moderne Antriebstechnik steigen bezüglich Dimensionierung, Preis, Energie- verbrauch, Wartung und Lebensdauer immer weiter. Der Kunde erwartet zunehmend von seinen Lieferanten in allen Belangen eine nachhaltige Antriebslösung [1]. Die Antriebshersteller stellen sich diesen steigenden Anforderungen mit zahlreichen Aktivitäten und Maßnahmen. Es wird mehr Wert auf Innovation gelegt und entsprechende Forschung und Entwicklung betrieben. Im Bereich der virtuellen Produktentwicklung unterstützen leistungsfähige Berechnungsprogramme den Ingenieur. Auf modernen Prüfständen werden die Produkte weiter optimiert und validiert. Messungen im Feld unterstützen eine maßgeschneiderte Antriebslösung und ermöglichen zudem eine permanente Überwachung eines Antriebes unter den vorherrschenden Betriebsbedingungen.
Insbesondere Messungen im Feld werden im Kontext mit IoT beziehungsweise Industrie 4.0 und den damit verbundenen Entwicklungen im Bereich der IT immer besser realisierbar. Sehr viele Daten (Big Data) können auf leistungsfähigen Servern gesammelt und verarbeitet werden. Für die Internetgateways stehen bezahlbare Hardware und IoT-Protokolle zur Verfügung. Vor Ort können mittels echtzeitfähiger, modularer Controllersysteme Messdaten erfasst und vorverarbeitet werden, die von dort auf die Server gesendet werden. Die fortschreitende Entwicklung in der Messtechnik ermöglicht gut integrierbare, bezahlbare Sensoren für alle relevanten Messgrößen an einem Industrieantrieb. Ein internetbasiertes Predictive Maintenance-System kann darauf aufbauend ermöglicht werden. Immer wieder fragen Kunden nach Lösungen für die Aufgabenstellungen einer permanenten Antriebs- und Anlagenüberwachung aus der Ferne, die möglichst automatisiert Diagnosen und Alarme generiert. ZAE-AntriebsSysteme entwickelt derzeit mit gutem Fortschritt an einer eigenen Lösung auf diesem Gebiet, die den Namen „ZAE-DriveWatch“ trägt (Bild 1), [2].
Neues gut integrierbares und variabel einsetzbares Drehmomentmesssystem
Für qualifizierte Messungen am Getriebe werden vor allem Drehzahl, Drehmoment, Temperatur und Schwingungen als Messgrößen erfasst und ausgewertet. Für diese und andere Messgrößen wurden in der Vergangenheit zahlreiche Messprinzipien entwickelt und Anwendungen zugänglich gemacht [3 – 7]. Für Feldmessungen an Industrieantrieben werden einfach integrierbare und preiswerte Systeme benötigt, die über lange Zeit zuverlässig funktionieren. Zum Teil können Messwerte bereits von der Antriebselektronik geliefert werden, sehr oft sind aber auch separate Sensoren, Messverstärker und Controller erforderlich, um ein wirkungsvolles Predictive Maintenance aufzubauen. Die Suche nach geeigneten Sensoren gestaltet sich schwierig [8]. Gerne wird dabei in Richtung Massenprodukte, beispielsweise aus dem Automotive- oder Smartphone-Bereich geschaut. Aber sind diese Sensoren dann auch bezüglich Messbereich und Widerstandsfähigkeit geeignet, um in einer rauen Industrieumgebung lange problemlos ihren Dienst zu versehen?
Eine besondere Rolle für den Antrieb spielt stets das dynamische Drehmoment einerseits aufgrund seiner Aussagefähigkeit, andererseits aufgrund der Kompliziertheit seiner Erfassung [9]. Auf der Suche nach geeigneter Messtechnik für Feldmessungen und Predictive Maintenance stieß ZAE-AntriebsSysteme auf das „Q-Torque“- Messsystem der Firma Manner Sensortelemetrie [10, 11].
Im Gegensatz zu herkömmlichen Sensoren, die meistens einen größeren Umbauaufwand am Antrieb oder in der Maschine aufgrund von Adaption und Platzbedarf erfordern, lässt sich Q-Torque sehr platzsparend und nahezu ohne strukturelle Änderungen integrieren. Somit kann die Applikation bei Bedarf sogar innerhalb eines Getriebes erfolgen. Eigene Tests bei ZAE-Antriebssysteme zeigen, dass das System im Vergleich zu anderen Prinzipien, wie dem aktiven magnetoelastischen Messprinzip, sehr viel genauer und vor allem auch unabhängig vom Wellenmaterial funktioniert [12]. Das Q-Torque Messsystem basiert auf Dehnungsmessstreifen (DMS), welche bis heute trotz großer Anstrengungen bei der Entwicklung alternativer Messverfahren eine unverzichtbare Rolle einnehmen. Im Vergleich zu anderen Verfahren ist der DMS für die Drehmomentmessaufgabe in vielen Bereichen, aber insbesondere im Getriebe nach heutigem Kenntnisstand immer noch die erste Wahl, wenn es um Langzeitmessungen, Genauigkeit und Dynamik geht. Auch, wenn er auf den ersten Blick als aufwendige Lösung erscheinen mag.
Das System Q-Torque besteht aus wenigen Einzelkomponenten, die für nahezu beliebige Kundenapplikationen anpassbar und einsetzbar sind. Auf der Getriebewelle ist eine Rotorelektronik anzubringen, welche eine geringe Aufbauhöhe von weniger als 4 mm benötigt. Als „Klebestreifen“ kann die Rotorelektronik einfach auf der Welle befestigt werden. Die DMS, bestehend aus zwei Vollbrücken, sind hierbei bereits im Kit integriert.
Das gesamte Rotor-Kit ist sehr flach und schmal und ist auf Wellen unterschiedlichen Materials und im Durchmesserbereich 30 bis 4000 mm applizierbar. Mit Hilfe der umlaufenden Nut kann die Rotorelektronik in der Wellenoberfläche versenkt werden. Dadurch können spätere Lagerwechsel im Rahmen einer Reparatur ohne Zerstörungsgefahr stattfinden.
Auf der stationären Seite des Getriebes wird eine sehr einfache Induktionsschleife platziert. Das effiziente, induktiv arbeitende und wartungsfreie Energie- und Datenübertragungsverfahren ermöglicht eine Vielzahl von möglichen Statorantennen-Designs, wodurch die Integration in das Getriebe sehr einfach ist. ZAE hat sich für einen einfachen Kunststoffhalter, der auf jede Umgebung angepasst werden kann, entschieden.
Als letzte Komponente wird eine sehr kleine mit 24 V DC zu speisende Elektronikbox benötigt, welche das kalibrierte Ausgangssignal im Bereich 0 bis 10 V an die PLC oder den Messdatencontroller liefert, Bild 2.
Das induktive berührungslose Messsystem ist völlig wartungs- und verschleißfrei. Der Hersteller verspricht eine hohe Messgenauigkeit von 0,1 % v. E. und eine sehr hohe Abtastrate von 3,4 kHz.
Damit sind Drehschwingmessungen im Strang möglich, was zusätzliche Beschleunigungsaufnehmer und die zugehörige Messelektronik einsparen kann. Zudem kann das System um Drehzahl- und Temperaturmessungen erweitert werden, womit eine umfassende Antriebsbeobachtung ermöglicht wird. Bild 3 zeigt den schematischen Aufbau des Messsystems.
Das Q-Torque System ist mittels Remote Control (RMC-Software) und einer zugehörigen USB-Adapterbox über einen PC konfigurierbar.
Die RMC-Software ist recht einfach zu handhaben und ermöglicht neben der Prüfung der Installationsgüte auch beispielsweise die Einstellung des Messbereichs und des Offsets entsprechend einer Kalibrierung des Messaufnehmers.
Nach der Kalibrierung können die Werte fest gespeichert werden, um einen bestimmten Signalpegel am Ausgang zu erhalten (Bild 4).
Erste Anwendungen des Drehmomentmesssystems bei ZAE-AntriebsSysteme
ZAE-AntriebsSysteme hat sich dieses Messsystem angeschaut und verspricht sich vor allem für eine künftige Nutzung im Bereich der Feldmessungen für Produktentwicklungen und Predictive Maintenance einiges von dem Einsatz. So wurde ein Getriebe im Rahmen des laufenden Entwicklungsprojektes für ZAE-DriveWatch mit Q-Torque ausgerüstet und erfolgreich getestet. Die Testergebnisse sind sehr vielversprechend, sodass ZAE-AntriebsSysteme einen Demonstrator mit dem Messsystem ausgestattet hat, um es Kunden zu zeigen und anzubieten (Bild 5).
Neben den Anwendungen für Feldmessungen kommt das Drehmomentmesssystem Q-Torque künftig auch in Beschichtungsanlagen der Firma Kroenert zum Einsatz. Hier soll aus Bauraum- und Kostengründen die platzsparende, integrierte Sensorik zum Einsatz kommen, um eine Drehmomentregelung für eine Bahnspannung aufzubauen. In diesem Zuge wurden die Kosten für das Messsystem bereits weiter optimiert und eine erste Anlage mit fünf Antrieben ausgestattet.
Bei ZAE-AntriebsSysteme wurde die Drehmomentmesstechnik mit Unterstützung durch Manner in die Getriebe verbaut und auf dem Prüfstand bei ZAE-AntriebsSysteme auf ihre Funktion überprüft und kalibriert, Bild 6.
Nachdem alle Überprüfungen unter dynamischen Testbedingungen abgeschlossen waren und die endgültige Konfiguration des Messsystems mittels der RMC-Software erfolgte, konnten die Kegel-Stirnradgetriebe mit dem eingebauten Messsystem an den Kunden ausgeliefert werden (Bild 7).
Der Einbau der Antriebe in der Anlage und die Inbetriebnahme folgten. Dort liefert das Messsystem analog ein Messsignal im Bereich 0 bis + 10 V. Bei 5 V beträgt das Drehmoment 0 Nm. Durch die gewählte Einstellung eines Drehmomentmessbereichs von + / – 500 Nm werden bei 0 V – 500 Nm und bei 10 V entsprechend + 500 Nm durch das analoge Interface ausgegeben.
Dieses Signal wird der PLC der Maschine zugeführt und in einem Servoregler der Firma Siemens für die sensible Regelung der somit indirekt gemessenen Bahnspannung genutzt. Früher kamen hier Kraftmesslager an den Walzen zum Einsatz, um die Bahnkraft direkt zu messen. Diese sind teuer und aufwendig zu montieren. Bild 7 (rechts) zeigt einen von fünf der Antriebe mit eingebautem Messsystem an der Anlage.
Besonders der platzsparende Einbau, die Linearität, Dynamik und Hysteresearmut des Messsignales sowie die Langzeitstabilität der Messkette haben zu dem Entschluss beigetragen, das Messsystem erstmals in einer Kroenert-Anlage einzusetzen. Mit dieser hochintegrierten Messtechnik in einem Antrieb hat ZAE-AntriebsSysteme maßgeblich zur Weiterentwicklung der Technologie bei Kroenert beigetragen, so Jonathan Dreifürst, Konstruktionsleiter bei Kroenert.
Ausblick
Das Q-Torque Messsystem der Firma Manner hebt sich deutlich positiv von allen anderen durch ZAE-Antriebssysteme untersuchten Lösungen zur Drehmomentmessung ab. Mit den jetzt genommenen Schritten und den ersten positiven Erfahrungen setzt ZAE-AntriebsSysteme künftig auf die Q-Torque-Drehmomentmesstechnik.
Sie bietet die Möglichkeit einer direkten Drehmomentmessung am Antrieb, ohne dass dieser oder die Umgebungskonstruktion wesentlich in ihrer Struktur verändert werden müssen. Der platzsparende Einbau und der vernachlässigbare Einfluss auf das Systemverhalten sind bestimmend. Dazu kommt die hohe Messgenauigkeit und die hohe Abtastrate im Kiloherzbereich, die für Schwingungsbeobachtungen und -analysen geeignet ist. Die im System bereits integrierte optionale Erweiterbarkeit um Drehzahl- und Temperaturmessung bietet zusätzliche Möglichkeiten der Nutzung, um am Antrieb direkt zu messen und Daten zu sammeln.
Durch entsprechende Ausbildung wird Mitarbeitern von ZAE-AntriebsSysteme vermittelt, wie die Rotorelektronik korrekt verbaut wird und wie die einfache Kunststoffantenne herzustellen ist. Damit ist für jedes zu installierende Messsystem lediglich die Rotorelektronik (Klebestreifen) und die Messverstärkerbox zu beschaffen und am Antrieb einzubauen und zu kalibrieren.
Der Firma Manner sollte es in der nächsten Zeit gelingen, das System weiter kostenmäßig zu optimieren und ZAE-AntriebsSysteme ein Standardpaket an die Hand zu geben. Dieses Standardpaket kann dann selber verbaut und in Betrieb genommen werden. Idealerweise sollte die Rotorelektronik so beschaffen sein, dass sie für unterschiedliche Wellendurchmesser und Werkstoffe verwendet werden kann und über einfache Parametrierung darauf einstellbar ist. Eine individuelle Kalibrierung eines Messsystems mittels RMC-Software bei entsprechenden Torsionsmomenten als abschließender Schritt wird aber weiterhin notwendig sein.
Durch die Robustheit und Kompaktheit der beschriebenen Lösung kann diese an fast allen beliebigen Antrieben zuverlässig für die Drehmomenterfassung eingesetzt werden. Die Messsignale können künftig für Messungen am Antrieb zur Dimensionierung, für Zustandsbeobachtungen oder auch für regelungstechnische Aufgabenstellungen genutzt werden.
Literatur
[1] VDMA Blue Competence, unter: http://www.bluecompetence.net/about (abgerufen: 9.1.2019)
[2] Sellschopp, K.: Digitale DetektiveÜber die Zukunft der Zustandsdiagnose in der Antriebstechnik. In: Antriebstechnik 3/2017
[3] Schanz, G. W.: Sensoren. In: Sensortechnik für Praktiker, Hüthig Verlag, 2004
[4] Laible, M.; Müller, R. K.; Bill, B.; Gehrke, K.: Mechanische Größen, elektrisch gemessen. Expert Verlag, 2006
[5] Gevatter, H.-J.; Freyer, U.: Handbuch der Mess- und Automatisierungstechnik. Springer Verlag, 2006
[6] Schmusch, W.: Elektronische Messtechnik. Vogel Verlag, 2005
[7] Felderhoff, R.; Freyer, U.: Elektrische und elektronische Messtechnik. Hanser Verlag, 2007
[8] Bülau, A.: FVA-Vorhaben 752 I Sensoren – Anwendung Antriebssysteme. Projektbericht Forschungsvereinigung Antriebstechnik e.V., 2016
[9] Schicker, R.; Wegener, G.: Drehmomente richtig messen. Hottinger Baldwin Messtechnik, 2002
[10] Manner: Eine Sensor-Erfindung von besonderer Bedeutung, unter: https://www.elektronikpraxis.vogel.de/eine-sensor-erfindung-von-besonderer-bedeutung-a-545137/index4.html (abgerufen: 9.1.2019)
[11] Deckers J.: Zustandsüberwachung von Industriegetrieben auf Basis von Drehmoment- und Schwingungsdiagnosen. Dresdener Maschinenbau Kolloquium, 2009
[12] Ruser, H; Tröltzsch, U.; Horn, M.; Tränkler, H.-R.: Magnetische Drehmomentmessung mit Low-cost Sensor. Universität der Bundeswehr München
Kaj Sellschopp
Leiter Entwicklung und Konstruktion ZAE-AntriebsSysteme GmbH & Co KG, Schützenstraße 105, 22761 Hamburg
Tel.: 0 40 / 8 53 93-03 E-Mail: info@zae.de www.zae.de
Dr. rer. nat. Julia Manner
Geschäftsführung Manner Sensortelemetrie GmbH, Eschenwasen 20, 78549 Spaichingen
Tel.: 0 74 24 / 9 32 90 E-Mail: info@sensortelemetrie.de www.sensortelemetrie.de