Hochpräzise positionieren
Kommerziell verfügbare Antriebssysteme positionieren beispielsweise Wafer in der Halbleiterfertigung hochpräzise innerhalb einer Ebene. Nanometergenau anheben können sie Objekte aber oft nur dank kaskadierter Grob-Fein-Antriebsstrukturen. Für gesamte 150- oder 300-mm-Wafer liegen derzeit erzielte Messunsicherheiten meist nur im Bereich von ±0,5 bis ±1 Mikrometer. Das IMMS hat mit der SIOS Meßtechnik GmbH und der TU Ilmenau einen luftgeführten 6-DOF-Direktantrieb entwickelt, der Objekte in den drei Raumachsen und der jeweiligen Rotation um diese Achsen frei im Raum in einem Verfahrbereich von ø 100 mm in einem Hebe- bzw. Senkbereich von 10 mm nanometergenau und aktiv geregelt positioniert (Bild 1).
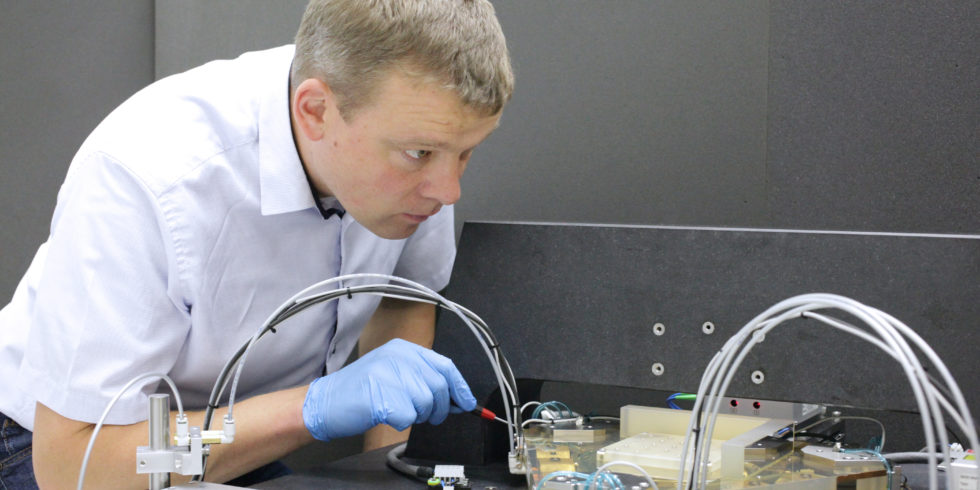
Bild 1 Arbeiten am 6D-Direktantrieb, der Objekte frei im Raum in einem Verfahrbereich von ø 100 mm in der Ebene und einem Hebe- bzw. Senkbereich von 10 mm aktiv geregelt mit Nanometer-Präzision bewegt. Bild: IMMS
Herausforderungen
Mess- und Strukturierungsanlagen verfügen in der Regel über einen Positioniertisch. Dessen Läufer bewegt Objekte hochpräzise innerhalb einer Ebene. Die Ebenheit einer Führungsfläche kann nicht beliebig genau gefertigt werden, was bereits Höhenschwankungen und Verkippungen des Läufers beim Gleiten über die Führungsfläche nach sich zieht. Zudem sind Höhen von Halterungen oder Rohlingen nicht immer identisch und Fertigungsprozesse können sich auf verschiedene Ebenen verteilen.
In der Fertigung Nutzlasten anzuheben, präzise und sicher zu positionieren ist bisher nur sehr schwer und mit Kompromissen zu lösen. Da sie sich gut steuern lassen, werden für Vertikalbewegungen elektro-dynamische Antriebselemente bevorzugt. Wenn diese jedoch den Läufer und das Objekt darauf tragen sollen, müssen enorme Kräfte aufgebracht werden. Diese ziehen sehr hohe Verlustleistungen nach sich, die Wärme erzeugen. Temperaturerhöhungen von nur 0,01 K verursachen aber durch Materialausdehnung einer Maske zur Waferbelichtung bereits einen Messfehler, der zum Ausfall der damit produzierten integrierten Schaltkreise führen würde.
Gesamtaufbau
Die Besonderheit des neuen Antriebskonzepts ist, dass die Kräfte für die Steuerung aller sechs Freiheitsgrade, das heißt der drei Translationsbewegungen in x-, y- und z-Richtung sowie der drei Rotationen um diese Achsen (rx-ry-rz), berührungslos und reibungsfrei auf nur ein zu bewegendes Läuferelement eingeleitet werden.
Die Positionsdaten werden wie bei vielen Präzisionsantrieben aus drei um den Läufer verteilten Laserinterferometern gewonnen. An den Spiegelflächen der mit dem Läufer bewegten Spiegelecke werden die Laserstrahlen reflektiert und zur Abstandsmessung genutzt. Das Objekt befindet sich innerhalb der Spiegelecke und alle virtuell verlängerten Messstrahlen der Koordinaten x, y und z der Interferometer treffen sich im Antast- bzw. Bearbeitungspunkt (Abbe-Punkt). Somit sind Spiegel-ecke sowie Objekt je nach Dicke und Oberflächenprofil anzuheben oder abzusenken, um den Antastpunkt auf der Objektoberfläche in den Abbe-Punkt zu bringen.
Alle Partner haben gemeinsam ein Gerätegrundkonzept erarbeitet, welches der Konfiguration nach Bild 2 entspricht.
Damit bleibt der Bauraum oberhalb des Läufers für ein Kundentool zur Messung und Fertigung frei. Systemarchitektur und Gesamtkonzept sowie konstruktive Integration, Aufbau, Inbetriebnahme und Charakterisierung wurden unter der Federführung von SIOS realisiert. Die TU Ilmenau war für die Entwicklung und Implementierung des hochpräzisen Mehrkanal-Interferometer-Systems verantwortlich. Das IMMS hat das Planar- motorsystem mit den Hub- und Antriebseinheiten sowie die Steuerung und Regelung erarbeitet.
Erweiterung von drei auf sechs Dimensionen
Den Ausgangspunkt für das Planar-motorkonzept bildeten zwei am IMMS entwickelte Lösungen – die integrierten planaren 3D-Direktantriebe sowie ein Vertikalantrieb. Von diesem wurden drei als Aktor- und Führungselemente in einen planaren 3D-Antrieb integriert, um Unebenheiten in der Führungsfläche auszugleichen und den Läufer in der richtigen Höhe zu positionieren, vgl. Bild 3.

Bild 3 Bereits Unebenheiten der Führungsfläche rufen bei herkömmlichen 3D-Antrieben (links) Höhenschwankungen und Verkippungen des Läufers beim Gleiten über die Führungsfläche hervor. Mit Vertikalaktoren in einem 6D-Antrieb (rechts) kann der Höhenunterschied ausgeglichen und der Läufer in der richtigen Höhe positioniert werden. (Bild: IMMS)
Ziel war es, damit ein echtes 6D-Direktantriebssystem mit den oben genannten Eigenschaften aufzubauen, eine 6D-Regelung dafür zu entwerfen und erste Untersuchungen zur Leistungsfähigkeit des konzeptionell neuartigen Ansatzes durchzuführen.
Integrierte planare 3-DOF-Direktantriebe als erster Ausgangspunkt
Der grundlegende Ansatz beruht auf den hervorragenden Positioniereigenschaften eines integrierten planaren elektrodynamischen Direktantriebsprinzips, vgl. Bild 4.

Bild 4 Schema eines planaren Antriebssystems mit 3 Spulenpaaren (links). Für den 6D-Antrieb wurden anstelle der drei sonst verwendeten Luftlager drei Vertikalantriebe (rechts) als Aktor-Führungs-elemente (AFE) integriert. (Bild: IMMS)
Bislang hatte das IMMS solche aerostatischen Direktantriebe für drei Freiheitsgrade entwickelt: Ein planarer luftgeführter Läufer, welcher an seiner Unterseite Magnetbrücken trägt, konnte über statorfixe Spulenpaare in den beiden horizontalen Achsen x und y sowie um seine Drehachse rz bewegt werden. Die sehr steif ausgeführten Läuferelemente können mit hoher Geschwindigkeit und sehr hoher Genauigkeit eine Sollbahn abfahren. Ein weiterer wesentlicher Vorteil ist, dass der Läufer passiv ist, d. h. vollkommen ohne störende Schleppkabel für Aktorik und Sensorik auskommt. Schäd-liche Wärmequellen können so sehr gut vom zu bewegenden Objekt ferngehalten werden. Diese am IMMS entwickelten Antriebe sind bereits gut am Markt etabliert.1
Vertikalantrieb als Aktor- und Führungselemente als zweiter Ausgangspunkt
Das IMMS hatte mit der AeroLas GmbH bereits eine Lösung für einen Vertikalaktor entwickelt, vgl. Bild 4. Dieser nimmt nun im neuen 6D-Direktantrieb als Aktor- und Führungselement jeweils anstelle der drei Luftlager die Gewichtskraft des Läufers mit einer sehr feinfühlig geregelten pneumatischen Druckkammer auf. Die verbleibende und mittels Tauchspulantrieb gelöste feinfühlige vertikale Positionierung des Läufers benötigt dann nur noch wenige Millinewton. Folglich generiert der Antrieb nahezu vernachlässigbare parasitäre Wärmeströme innerhalb der Maschine. Das ermöglicht ein quasi leistungsloses Anheben des Läufers einschließlich des zu vermessenden Objektes und gestattet gleichzeitig eine Positionsauflösung im Nanometerbereich.
Entwicklung des 6-DOF-Planarmotorsystems
Das IMMS hat für die o. g. Grundanordnung die Kernkomponenten für den planaren Antrieb und die Führung dimensioniert. Im Fokus stand dabei das Schwingungsverhalten des mechanischen Systems. Mittels FEM-Simulationen wurden die Antriebe und die Mechanik-Bauteile so gestaltet, dass die bewegte Masse möglichst gering gehalten, gleichzeitig jedoch eine hohe Struktursteifigkeit erzielt wird und die Eigenfrequenzen somit ausreichend hoch sind, um die hohen Anforderungen an die Positionierdynamik zu erreichen. Bild 5 zeigt das Ergebnis einer FEM-Modalanalyse des finalen Läuferentwurfs mit einer ersten Eigenfrequenz von 291 Hz.

Bild 5 Eine der FEM-Simulationen des Schwingungsverhaltens des Läufers mit einer exemplarischen hinreichenden Eigenfrequenz von 291 Hz. (Bild: IMMS)
In gleicher Weise hat das IMMS auch die gestellfesten Antriebskomponenten, d.h. die Flachspulen mit Halterung bzw. Gehäuse modelliert, um die Antriebskraft und die damit verbundene thermische Belastung des Systems per Simulation abzuschätzen und damit die Spulengeometrie zu optimieren. Darüber hinaus wurden Lösungen für die Ankopplung der Ma-gnetbrücken an den Quarzläufer und für eine Temperiereinhausung der Planar-spulen erarbeitet.
Das IMMS hat die drei Vertikalantriebe mechanisch und pneumatisch in das Planarmotorsystem integriert und passgenaue Lösungen für die Einbindung in die elektronische Steuerungsarchitektur des Systems entwickelt. Schläuche und Kabel sitzen direkt am Läufer und bieten einen flexiblen Übergang vom Läufer zum Stator, um Bewegungen im Arbeitsbereich zu ermöglichen und lediglich geringe und gleichzeitig möglichst symmetrische Stör-kräfte bei der Bewegung des Läufers hervorzurufen.
Regelung des Systems in sechs Freiheitsgraden

Bild 6 Realisiertes 6D-Positioniersystem (links) mit integrierten Vertikalaktoren (rechts). (Bild: IMMS)
Das in Bild 6 dargestellte Antriebssystem wurde schrittweise in Betrieb genommen und dabei die simulationsbasiert entworfene 6D-Positionsregelung schrittweise erprobt und anhand der ermittelten Streckeneigenparameter weiter optimiert und verfeinert. Das IMMS hat die dazu benötigten physikalischen Parameter wie Motorkonstanten, Massenverhältnisse, Übertragungseigenschaften der verschiedenen Teilsysteme innerhalb der Regelstrecke sowie Eigenfrequenzen zunächst modellbasiert ermittelt und durch experimentelle Untersuchungen am Antrieb verifiziert und zum Teil nachgeführt. Der Fokus lag dabei auf frequenzabhängigen Übertragungseigenschaften. So wurde eine Feinabstimmung zwischen der geringdynamischen pneumatischen Gewichtsentlastung im Vertikalantrieb und der hochdynamischen Aktorik des Läufers vorgenommen, um bestmögliche Positionierergebnisse zu erzielen. Das IMMS hat die komplexen 6D-Regelungsalgorithmen entwickelt, in Matlab/Simulink programmiert und auf der dSpace-Hardware im Steuerungsrack für alle Teilsysteme implementiert.
Ergebnisse und Ausblick
Im Ergebnis wurden die angestrebten Regelabweichungen im Nanometerbereich erzielt. Bild 7 verdeutlicht die erreichte Regelgüte anhand der Zeitsignale für den geregelten Betrieb in allen sechs Freiheitsgraden bei einer Flughöhe von 1 mm.

Bild 7 Zeitsignale der sechs Koordinaten im geregelten Betrieb (oben); RMS-Regelabweichung in Abhängigkeit von der Flughöhe zset (unten). (Bild: IMMS)
In x, y und z werden Regelab-weichungen (RMS) von weniger als einem Nanometer erreicht. Systematisch wurde weiterhin die höhenabhängige Veränderung der Regelabweichungen untersucht und so der Nachweis erbracht, dass das 6D-Positioniersystem über den vollen z-Hub von 10 mm eine nanometergenaue Positionierung des Läufers ermöglicht. Das Antriebskonzept stellt einen vollkommen neuartigen Ansatz für ein sechsdimensionales Direktantriebssystem dar, der so bisher in keinem bekannten System umgesetzt wurde. Eine Skalierbarkeit des Konzepts für andere Anwendungen wurde bis zu einem Arbeitsbereich von 200 mm Durchmesser untersucht. Die Ergebnisse bilden die Basis für künftig zu entwerfende kundenspezifische 6D-Antriebssysteme im Hochpräzisionsbereich.
Förderung: Das Projekt INPOS wurde unter dem Kennzeichen ZF408707LT7 gefördert durch das Bundesministerium für Wirtschaft und Energie aufgrund eines Beschlusses des Deutschen Bundestages.

Dr.-Ing. Christoph Schäffel, Leiter Mechatronik IMMS Institut für Mikroelektronik- und Mechatronik-Systeme gemeinnützige GmbH (IMMS GmbH), Ehrenbergstraße 27, 98693 Ilmenau, Tel.: 0 36 77 / 8 74 93-60, E-Mail: christoph.schaeffel@imms.de, https://www.imms.de