Hubmodule für die Präzisionsantriebstechnik
Das IMMS hat einen Antrieb entwickelt, der Objekte nanometergenau positioniert. Die Hubmodule wurden nun für Fertigung und Messtechnik optimiert.
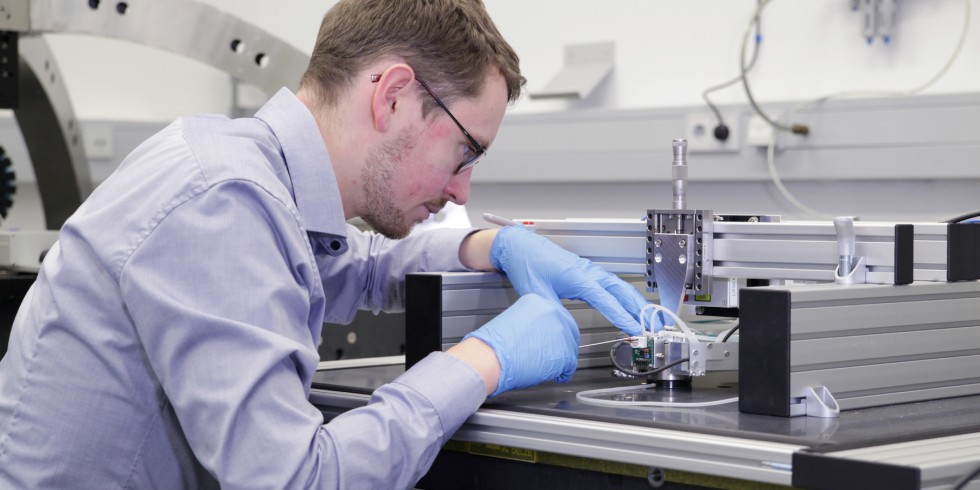
Bild 1 Die am IMMS entwickelten Hubmodule wurden für den Einsatz in der Fertigung und Messtechnik optimiert.
Foto: IMMS
Positioniersysteme in der Halbleiterfertigung und der hochgenauen Messtechnik müssen immer präziser bewegen, um die voranschreitende Miniaturisierung zu bewältigen. Für neue Fertigungsverfahren werden immer größere vertikale Stellbereiche gefordert. Dafür hat das IMMS bereits einen 6D-Direktantrieb entwickelt, der Objekte in einem Verfahrbereich von 100 mm Durchmesser in einem Hebe- beziehungsweise Senkbereich von 10 mm frei im Raum nanometergenau und aktiv geregelt positioniert. Die Hubmodule wurden nun weiterentwickelt, um das System aufgrund des 75 % geringeren Wärmeeintrags für den Einsatz in der Fertigung und Messtechnik zu optimieren. Der parallel erarbeitete Design-Flow für große Bewegungsbereiche ist die Basis für noch effizientere anwendungsspezifische Entwicklungen.
Gemeinsam mit seinen Partnern entwickelt und realisiert das IMMS Präzisionsantriebe für die nanometergenaue Positionierung in Verfahrbereichen von 100 mm und mehr. Durch die Integration eigens entwickelter Hubmodule wird dies nicht nur für eine planare Positionierung in der xy-Ebene sondern zusätzlich auch für die Bewegung in z-Richtung, beispielsweise über 10 mm möglich.
Neuer Prozess: Grundlage der Weiterentwicklung
Ein neu erarbeiteter Entwurfsprozess bildet die Grundlage für die passgenaue und optimierte Weiterentwicklung dieser hochintegrierten Hubmodule, womit auch für zukünftige Hub-Last-Kombinationen ein effizienter und schneller Entwurf möglich ist. Für den Neuentwurf der Hubmodule wurde zunächst das zugrundeliegende planare Antriebssystem (Bild 2) ganzheitlich betrachtet. Es basiert auf einem monolithischen Zentralkörper (Läufer), welcher auf drei Luftlagern reibungsfrei in der xy-Ebene bewegt werden kann.
Mit Hilfe von vier Laserinterferometern, einem Autokollimator und in den Läufer integrierter Planspiegel ist es möglich, dessen Lage und Orientierung im Raum zu bestimmen. Gestellfeste Spulen erzeugen Kräfte auf NdFeB-Magneten auf der Unterseite des Läufers, wodurch dieser präzise in x- und y-Richtung bewegt werden kann. Zwischen den Luftlagern an den Ecken und dem Zentralkörper sollen nun zusätzliche Führungen und Aktoren eingebracht werden, um einen z-Hub des Läufers um 10 mm zu ermöglichen und die verbleibenden Fehler in den Kippwinkeln φx und φy eliminieren zu können. Mit dieser Anordnung muss der Läufer nur minimal modifiziert werden und es ist möglich, drei identische Module einzusetzen, auf welche sich die zu tragende Masse von circa 12 kg gleichmäßig verteilt.
Das Lastenheft für ein Präzisionssystem ist meist sehr ausführlich, weil Wechselwirkungen, die im klassischen Maschinenbau vernachlässigbar sind, im Präzisionsbereich einen erheblichen Einfluss auf die erzielbare Genauigkeit haben können. Um alle Anforderungen angemessen zu erfüllen, ist ein geeigneter konstruktiver Entwicklungsprozess unerlässlich. Dazu werden in diesem Fall die Konstruktionsprinzipien aus der Präzisionstechnik (Funktionstrennung) mit denen aus der Mechatronik (Funktionsintegration) in Einklang gebracht. Das betrifft insbesondere die zwei funktionalen Kernkomponenten: den Vertikalantrieb und die Vertikalführung.
Ein Aktor für die Gewichtskraft, einer für die Position
Das zu entwerfende Hubmodul soll in der Lage sein, 4 kg über 10 mm nanometergenau und stick-slip-frei zu heben, wofür ein Bauraum von lediglich circa Ø 50 mm × 60 mm zur Verfügung steht. Besonderes Augenmerk liegt auf der entstehenden Wärme im Betrieb: Diese soll minimal sein, weil jede Erwärmung thermische Ausdehnung und damit Präzisionsverlust zur Folge hat. Zusätzlich sollen Antrieb und Führung so gestaltet sein, dass sie sich gut für größere Lasten und Bewegungsbereiche skalieren lassen. Eine Analyse der in Frage kommenden Antriebsprinzipien (pneumatisch, piezoelektrisch, elektromagnetisch) hat gezeigt, dass keines allein in der Lage ist, alle Anforderungen hinreichend zu erfüllen. Eine sinnvolle Lösung bietet die Abwandlung des Grobtrieb-Feintrieb-Prinzips: Ein erster Aktor kompensiert maßgeblich die Gewichtskraft, wodurch ein zweiter Aktor nur noch sehr geringe Kräfte benötigt, um die Präzisionspositionierung zu ermöglichen. Als Gewichtskraftkompensation eignet sich besonders ein Pneumatikzylinder, da dieser über eine hohe Kraftdichte verfügt, lokal keine Wärme ins System einträgt und über den Druck an verschiedene Lasten anpassbar ist. Die verbleibenden niedrigen, aber hochdynamischen Präzisionskräfte sind dann durch einen optimal gestalteten elektromagnetischen Aktor realisierbar. Außerdem können beide Aktorprinzipien sehr gut an größere Hübe und Lasten angepasst werden.
Als reibungsfrei arbeitende Führung eignet sich insbesondere eine aerostatische Buchsenführung. Diese kann zusätzlich sehr gut in den Pneumatikzylinder integriert werden, ohne funktionale Abstriche zu machen.
Modellierung der Aktoren ist ein zentraler Schritt
Zentraler Entwicklungsschritt der Auslegung und Dimensionierung ist die Modellierung der Aktoren. Detaillierte pneumatische Modelle erlauben es, Rückschlüsse auf das statische und dynamische Verhalten sowie den Luftverbrauch des Pneumatikzylinders zu ziehen. So konnte die Kolben-Zylinder-Kombination mit einer reibungsfreien Dichtung ideal an die Anforderungen und die vorhandene Infrastruktur angepasst werden.
Der elektromagnetische Aktor hat einen deutlich höheren Design-Freiheitsgrad und ist damit der Schlüssel für darauf aufbauende anwendungsspezifische Entwürfe: Verschiedenste Magnetanordnungen können mit unterschiedlich gestalteten Eisenrückschlüssen und Spulen kombiniert werden. Um den idealen Antrieb für die gegebenen Randbedingungen zu finden, wurden 13 Topologien anhand eines universellen Performance-Parameters detailliert untersucht. Für Präzisionsantriebe eignet sich vor allem das Kraft-Leistungsverhältnis, weil so die Antriebsstrukturen unabhängig von der verwendeten Endstufe und der erwarteten Bahnkurve bewertet werden können.
Die elektromagnetischen Feldsimulationen sind in eine numerische Optimierung eingebettet, wodurch für jede Topologie die ideale Geometrie gefunden werden kann. Der dabei ermittelte Magnetantrieb verfügt über ein Kraft-Leistungsverhältnis von über 60 N²/W in einem Bauraum von circa Ø 50 mm × 40 mm. Der zugehörige Optimierungsdurchlauf sowie die Magnetfeldverteilung sind in Bild 3 a/b dargestellt.
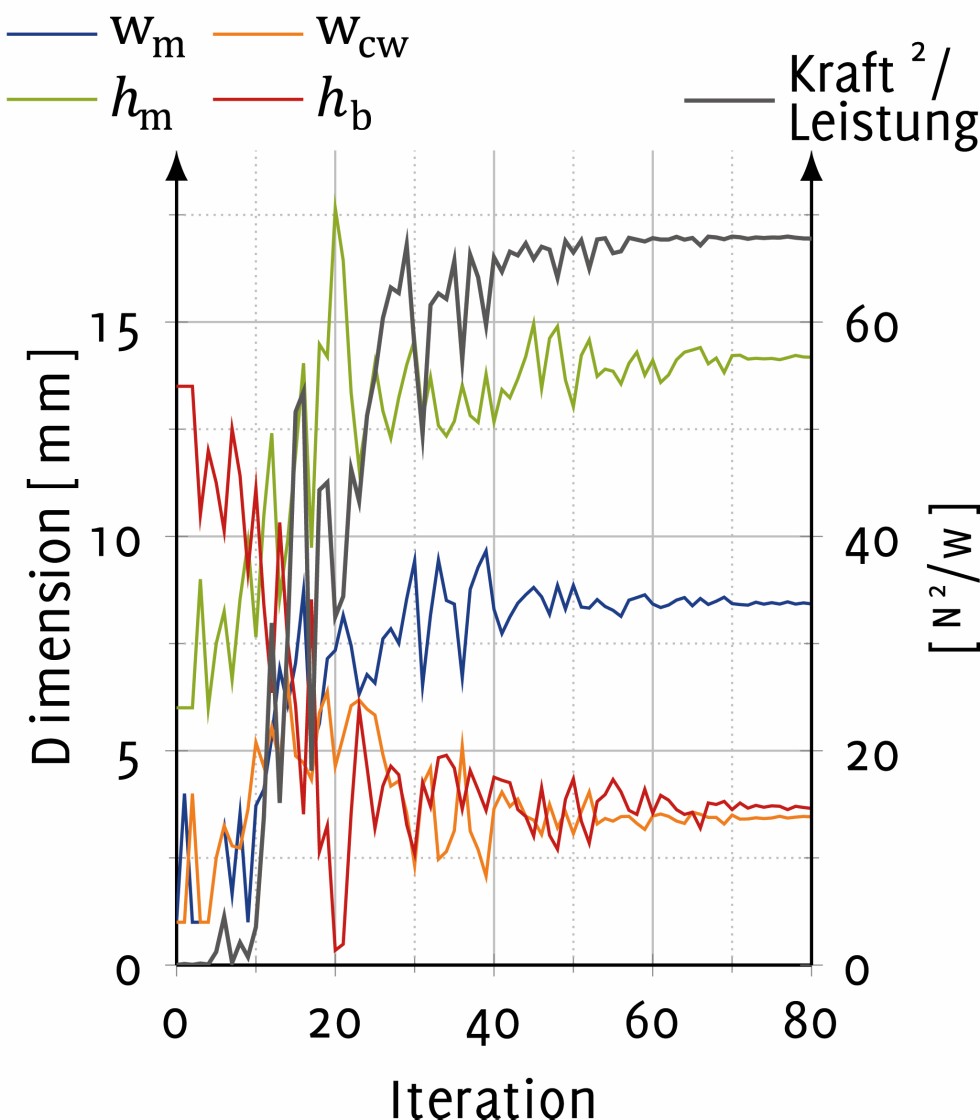
Bild 3a Optimierung der Aktorgeometrie für die final gewählte Antriebstopologie, per automatisiertem Optimierungsalgorithmus werden die Abmessungen von Magnet und Spule (wm, wcw, hm, hb) festgelegt. (Grafik: IMMS)
Deutliche Reduzierung der entstehenden Wärme
Das Optimierungsergebnis besteht in den gefundenen Abmessungen für Magnet und Spule des elektrodynamischen Aktors, welche sich über ein möglichst hohes Kraft-Leistungsverhältnis hinaus insbesondere durch eine homogene Flußdichteverteilung im Bewegungsbereich der Spule und somit eine konstante Krafterzeugungscharakteristik auszeichnen, siehe Bild 3 b.
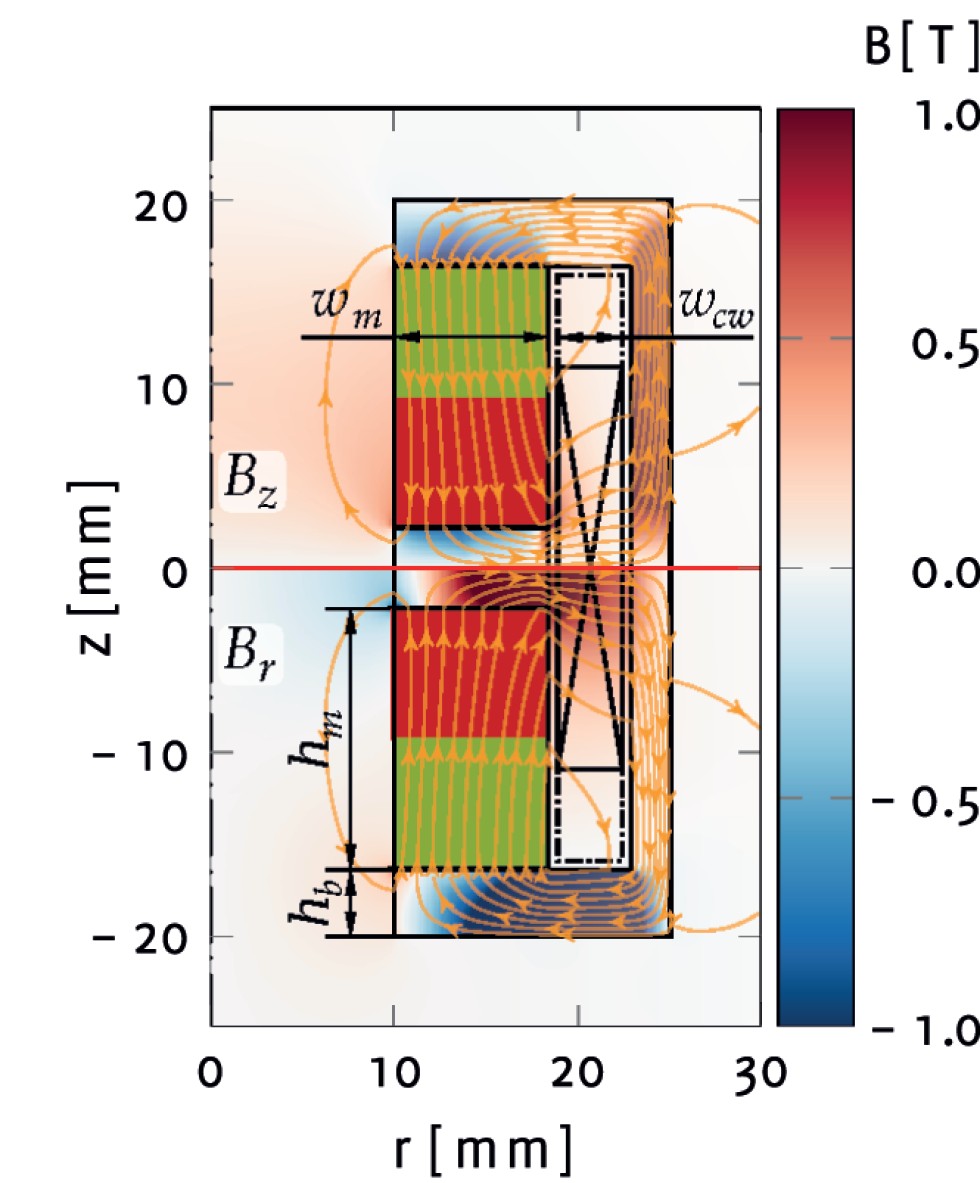
Bild 3b 2D-Querschnitt der gefundenen optimalen Antriebsgeometrie und FEM-basierte Analyse der zugehörigen Flussdichteverteilung. (Grafik: IMMS)
Aus einer anschließenden Parameterstudie kann dann die Spule ausgewählt werden, welche am besten zur Leistungsendstufe passt. Insgesamt konnte die entstehende Wärme gegenüber dem vorhergehenden Hubmodul um circa 75 % reduziert werden. Die geringe verbleibende Verlustleistung kann bei Bedarf zusätzlich durch ein integriertes Temperiersystem aus dem Messraum transportiert werden.
Neben dem konkreten Entwurfsergebnis steht nun zusätzlich eine erprobte Methodik zur Verfügung, um zukünftig auch für andere Hub/Last-Kombinationen und zugehörige Bauraumvorgaben schnell und effizient zu einem optimierten Entwurf des Hubmoduls zu kommen.
Bild 4 zeigt das entwickelte Hubmodul. Der Magnetantrieb schließt dabei die meisten Komponenten in seinem Inneren ein, wodurch alle Antriebskräfte exakt auf der Führungsachse liegen und somit keine parasitären Kipplasten entstehen. Die Störkräfte durch geschleppte Leitungen konnten maßgeblich reduziert werden, indem die Komponenten, welche eine Zuleitung benötigen, in die läuferfeste Baugruppe integriert wurden. Die ersten Messergebnisse aus einem einachsigen Messstand in Bild 5 bestätigen den Entwurf. Im ersten Schritt wurde das Hubmodul druck- und stromlos auf dem massiven Granitstator abgestellt.
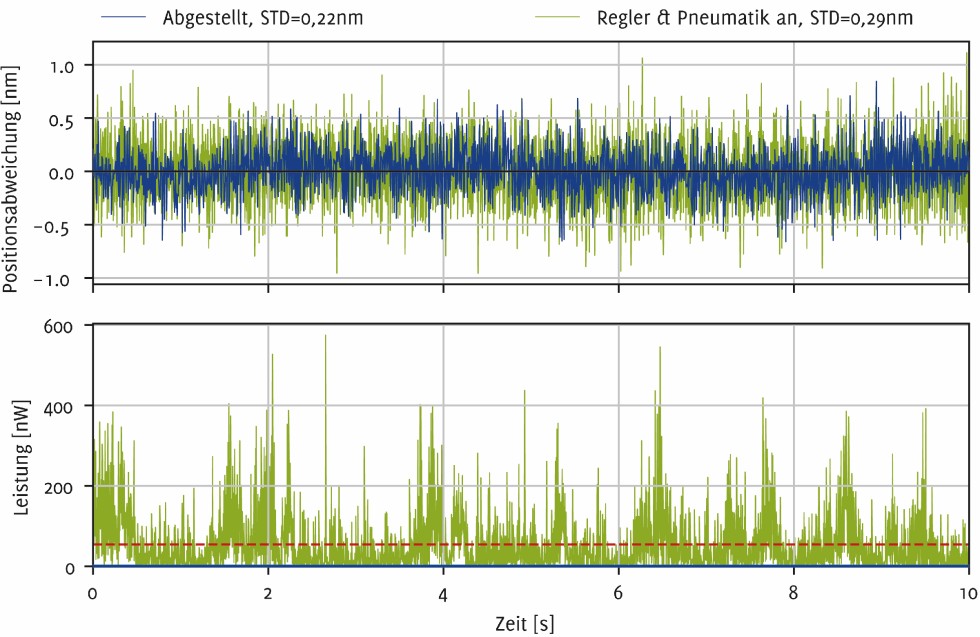
Bild 5 (Oben/blau) Positionsmessung, während das Modul druck- und stromlos auf der Unterlage ruht, (Oben/grün) Positionsabweichung vom Sollwert im closed-loop Betrieb (mit aktiver pneumatischer Gewichtskraftkompensation und Positionsregelung durch den Magnetantrieb); (Unten/grün) zugehörige abfallende elektrische Leistung im Magnetantrieb; (Unten/rot) Durchschnittswert von 54 nW der zum Positionierprozess benötigten elektrischen Leistung. (Grafik: IMMS)
Das Positionsrauschen weist dabei eine Standardabweichung von 0,22 nm auf, was somit das theoretische Limit darstellt. Im Closed-loop-Betrieb (Luftführung, pneumatische Gewichtskraftkompensation, Magnetantrieb und Regler aktiv) wurde ein nur minimal größerer Fehler von 0,29 nm bei einer elektrischen Leistungsabgabe von durchschnittlichen nur etwa 54 nW erreicht.
Hochgenaues Positionieren schwerer Lasten
Die neu entwickelten Hubmodule konnten beweisen, dass mehrere Kilogramm in einen makroskopischen Bewegungsbereich Nanometer-genau positioniert werden können, während nur eine Verlustleistung im niedrigen Nanowattbereich in den Messraum emittiert wird. Sie sind somit ein wichtiger Meilenstein für die industrielle Verwendung in 6D-Mess- und Nanofabrikationsystemen, die Objekte auf komplexen räumlichen Wegstrecken nano- und subnanometergenau positionieren sollen. Darüber hinaus bewährt sich der erarbeitete Konstruktionsleitfaden aktuell bei dem Entwurf weiterer Module für einen Hub von 25 mm und einer Last von 13 kg.
Die Arbeiten wurden im Rahmen des Graduiertenkollegs „Tip and laser-based 3D-Nanofabrication in extended macroscopic working areas“ (GRK 2182), gefördert durch die Deutsche Forschungsgemeinschaft (DFG), durchgeführt. Der Text basiert auf den Ergebnissen der Dissertation „A lifting and actuating unit for a planar nanoprecision drive system“ von Stephan Gorges (https://www.db-thueringen.de/receive/dbt_mods_00047399).
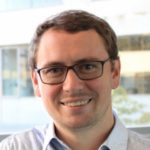
Dr.-Ing. Stephan Gorges
ist Entwicklungsingenieur für Präzisionsantriebssystem bei der IMMS Institut für Mikroelektronik- und Mechatronik-Systeme gemeinnützige GmbH
98693 Ilmenau
stephan.gorges@imms.de
www.imms.de
Foto: IMMS