Den richtigen Drehgeber für die Anwendung finden
Wie bei den meisten Sensoren, ist auch bei Encodern die Auflösung ein entscheidender Parameter bei der Auswahl. Dabei gilt: die Auflösung des Encoders muss deutlich besser sein, als die angestrebte Positionsauflösung. Beim Beurteilen der Eignung müssen aber zusätzliche Faktoren beachtet werden, beispielsweise ob der Encoder direkt oder über ein Getriebe am Motor sitzt und wie die Umgebungsbedingungen sind. Weitere wichtige Parameter sind die Signalübertragung und die erreichbare Regelgüte. In der Praxis haben sich sogenannte Dual-Loop-Regelungen bewährt, mit denen sich Lasten hochdynamisch positionieren lassen.
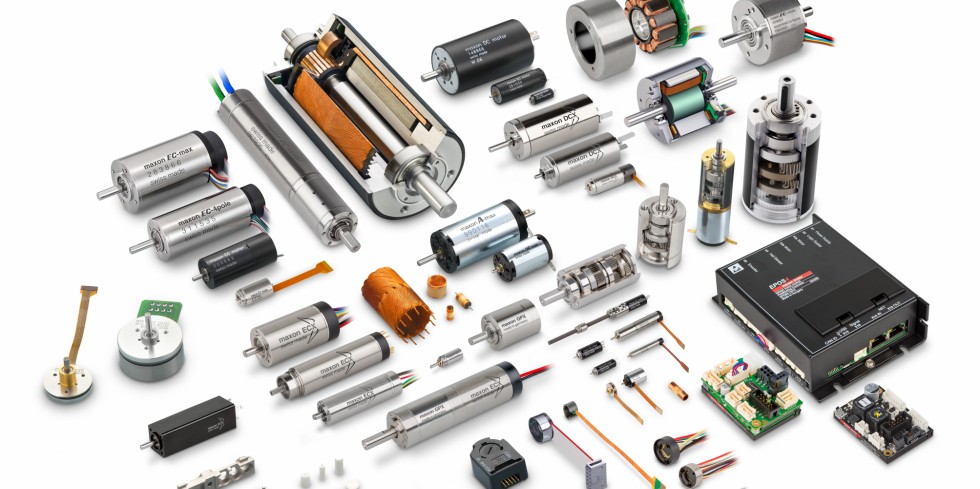
Bild 1 Die Anforderungen an Encoder sind vielfältig. Dementsprechend groß ist die Auswahl an verschiedenen Ausführungen.
Foto: maxon
Der charakteristische Parameter eines Encoders ist seine Auflösung, das heißt die Anzahl der Rechteckimpulsen pro Umdrehung auf jedem der beiden Signalkanäle. Die beiden Signale sind um ein Viertel der Signalperiode gegeneinander verschoben, was die Erkennung der Drehrichtung ermöglicht. Durch das Auswerten der Signalflanken kann eine viermal höhere Auflösung als die nominelle Anzahl der Impulse erreicht werden. Ein Encoder mit beispielsweise 500 Impulsen pro Umdrehung liefert 2000 Zustände, was einer Winkelauflösung von 0,18° entspricht. Das Nichtbeachten dieser Unterscheidung zwischen Impulszahl und Anzahl Zustände erzeugt immer mal wieder Missverständnisse. Bei Absolutgebern macht natürlich nur die Anzahl der unterscheidbaren Zustände Sinn.
Übliche Encodern haben Impulszahlen im Bereich von 128 bis 1024 pro Umdrehung; es gibt aber auch Encoder mit gerade mal 12 Impulsen oder solche mit mehreren Zehntausend Impulsen pro Umdrehung. Einige der Faktoren, welche die erreichbare Encoder-Auflösung beeinflussen, sind das zugrunde liegende physikalische Prinzip (optisch, magnetisch, induktiv …), der primäre Signaltyp (analog oder digital) und die Signalverarbeitung (zum Beispiel Interpolation). Die Genauigkeit, das heißt die Länge der Encoderimpulse, kann aufgrund mechanischer Toleranzen (beispielsweise Wellenschlag, Länge der Magnetpole) variieren. Infolgedessen weicht die gemessene Position über eine Motorumdrehung periodisch von der tatsächlichen Position ab.
Eine zweite wichtige Eigenschaft betrifft die Signalübertragung. Moderne Encoder verwenden sogenannte Line Driver, welche aufgrund des Treibers, die Signalqualität auch über längere Distanzen (bis 30 m) sicherstellen und aufgrund differentieller Signalübertragung elektromagnetische Störsignale (etwa von Motorleitungen) eliminieren. Line Driver können entsprechend verschiedener elektrischer Standards ausgestaltet sein, beispielsweise RS 422, TTL, CMOS. Moderne Steuerungen sind für die Verwendung von Line Drivern ausgerüstet. Single-ended Encodersignale kommen praktisch nicht mehr zum Einsatz (Bild 2).
Hochgenaue Startposition mit drittem Kanal festlegen
Einige Inkrementalencoder weisen einen dritten Kanal auf. Dieser Indexkanal liefert einen schmalen Rechteckimpuls pro Umdrehung, welche eine einzelne Referenzposition pro Umdrehung liefert. Damit lässt sich eine hochgenaue Startposition bei Positionieraufgaben festlegen. Der Indexkanal kann auch zu Überwachungszwecken eingesetzt werden: Sind alle Zustände pro Umdrehung detektiert worden oder sind Zustände „verloren“ gegangen?
Man beachte weiter den Versorgungsspannungsbereich (Spannungsabfall bei langen Leitungen!) und die Stromaufnahme des Encoders, sowie die maximale Impulsfrequenz oder Drehzahl, bei denen er die Signale noch in genügender Qualität liefert.
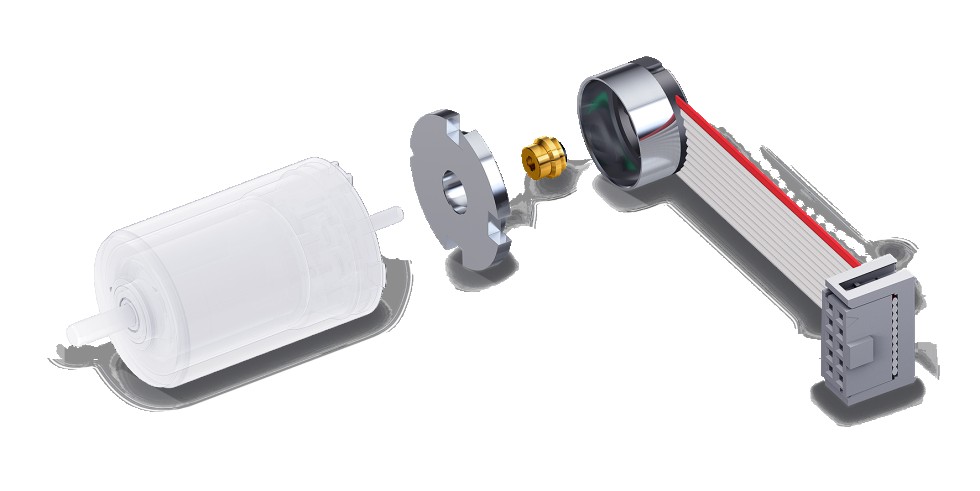
Bild 3 Robustes ENX 16 Easy Encoderdesign mit Target (auf Wellenende montiert). Das Encodergehäuse wird mit dem Montageflansch fest verschweißt. Das Flachbandkabel ist eingespritzt und damit zugentlastet. (
Foto: maxon)
Die Baugröße des Encoders kann bei Kleinstantrieben eine wesentliche Rolle spielen. Der Motor als Leistungsteil und nicht der Encoder hinten auf dem Motor soll das dominierende Bauteil sein. Die Hersteller von Kleinstmotoren entwickeln deshalb ihre eigenen kleinen Encoder, welche sie nach Möglichkeit in den Motor integrieren, um Baugröße zu sparen.
Je nach Anwendungsfall muss der Geber unempfindlich gegenüber Umwelteinflüssen sein. Dies kann hohe oder sehr tiefe Temperaturen betreffen, Vibrationen, Staub und Schmutz oder elektromagnetische Störfelder. Mechanische Robustheit ist ebenfalls ein Kriterium. Man denke beispielsweise an eine Zugentlastung der Encoderkabel.
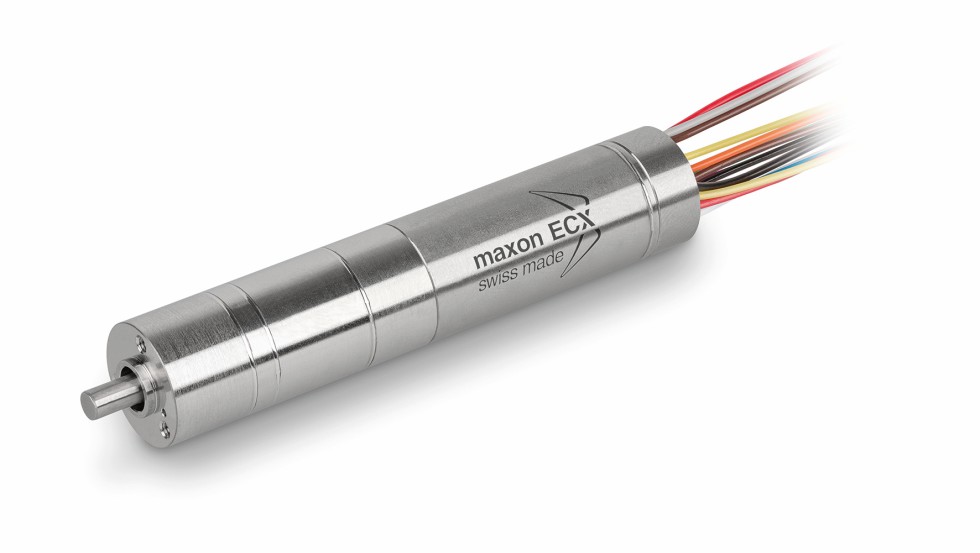
Bild 4 13 mm sterilisierbare Getriebe-Motor-Encoder-Kombination mit integriertem ENX 13 Easy INT. (
Foto: maxon)
Vorauszuschicken gilt es, dass die erreichbare Regelgüte nicht nur von der Auflösung und Genauigkeit der Feedbacksignale abhängt, sondern auch vom Regler selbst, seinen Regelparametern und dem zu regelnden mechanischen System (beispielsweise Reibung, Massenträgheiten, Elastizitäten, und so weiter).
Wir wollen uns an dieser Stelle aber auf den Einfluss der Encoderauflösung fokussieren. Auflösung soll im Folgenden als Anzahl unterscheidbarer Zustände verstanden sein, also nicht als Impulszahl pro Kanal.
Beim direkten Positionieren ohne mechanische Elemente wie Getriebe sind die Anforderungen an die Encoderauflösung einfach zu formulieren. Die zu erreichende Winkelauflösung ergibt direkt die minimale Encoderauflösung. Tatsächlich wird man aber nach Möglichkeit einen Encoder mit mindestens viermal, besser zehnmal, höherer Auflösung wählen: Das Messgerät soll genauer sein als die zu unterscheidenden Positionen. Der Positionsregler kann Abweichungen schneller detektieren und dynamischer reagieren, um die Position innerhalb des geforderten Bereichs zu halten.
Reduzierende Getriebe erhöhen die Auflösung
Encoder sitzen in der Regel auf dem Motor. Reduzierende Getriebe und mechanische Elemente, zum Beispiel Spindeln, erhöhen die Auflösung an der Last. Ein Getriebe mit Untersetzung 20:1 vergrößert die Winkelauflösung um einen Faktor zwanzig; 512 Zustände am Motor ergeben 10240 Zustände am Getriebeabgang oder eine theoretische Winkelauflösung von 0,035°. Die Mutter einer Spindel mit Steigung 5 mm wird sich gerade mal um 5 mm/512 ~ 0,01 mm vorwärts bewegen. Fazit: Für das Positionieren mit untersetzenden mechanischen Elementen reichen kleine Encoderauflösungen. Die Genauigkeit der Mechanik ist meist der limitierende Faktor bei präzisen Positionieraufgaben. Mechanisches Spiel und elastische Kupplungen erschweren eine präzise und steife Regelung.
Als mögliche Lösung bietet sich eine Dual-Loop-Regelung an, wie sie in den Maxon EPOS4-Kontrollern implementiert ist. Dabei liefert ein direkt an der Last angebrachter Encoder die Feedbacksignale für die primäre Positionsregelung; der Encoder auf dem Motor ist für den untergeordneten Regelkreis zuständig. Dual-Loop-Regelkreise sollten geeignete Filter und Dämpfung enthalten, um instabiles Verhalten aufgrund von Elastizitäten, mechanischem Spiel und der diskreten Encodersignale zu vermeiden.
Auflösung, Reglertakt und Drehzahl abstimmen
Encoder liefern Positionsinformationen. Für die Drehzahlregelung werden die Encodersignale integriert, indem die Anzahl der Zustandsänderungen pro Reglertakt – zum Beispiel pro Millisekunde – gezählt werden. Dies Diskretisierung führt dazu, dass Drehzahlen nur in festen Schritten gemessen werden. Die Auflösung beträgt 1 Encoderzustand pro Reglertakt. Bei einem Encoder mit 2000 Zuständen pro Umdrehung und einem Reglertakt von 1 ms ergibt sich eine Auflösung der Drehzahl von 30 Umdrehungen pro Minute (min−1). Schnellere Reglertakte vergrößern die Messschritte, höhere Encoderauflösungen verkleinern sie. Die effektive Drehzahl des Motors entspricht dem Mittelwert des Feedbacksignals, welches meist über einen Tiefpassfilter zur eigentlichen Drehzahlregelung herangezogen wird; die wenigsten Antriebe könnten den schnellen Variationen des Feedbacksignals wirklich folgen. In der Praxis geht es also darum, eine geeignete Encoderauflösung für den Reglertakt und die geforderten Drehzahlen zu finden.
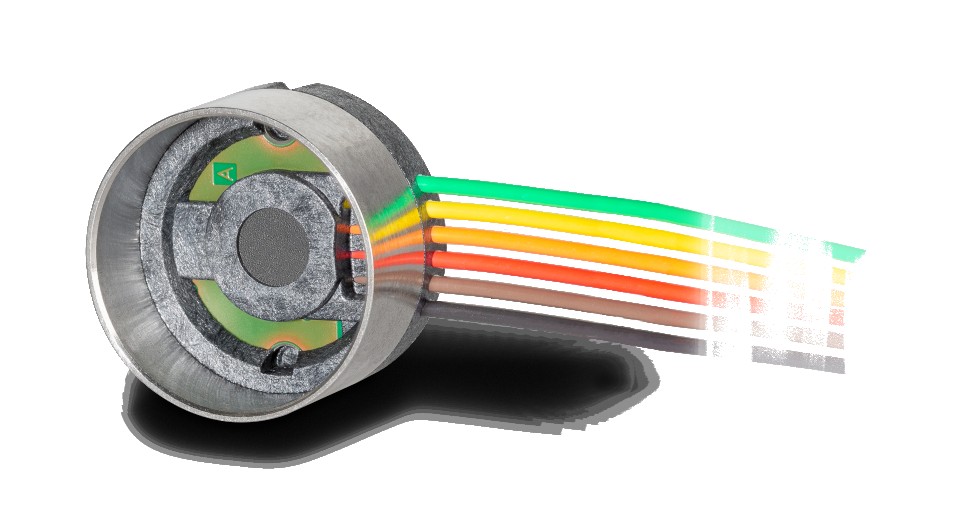
Bild 5 Blick in einen ENX 16 Easy Absolut-Encoder mit Kabel für einen erweiterten Temperaturbereich. (
Foto: maxon)
Bei nicht allzu kleinen Drehzahlen (einige hundert min−1 und höher) reichen in der Regel Encoder mit moderater Auflösung von unter 1000 Zuständen pro Umdrehung für eine vernünftige Regelung. Je größer die Drehzahl, umso kleiner kann die Encoderauflösung sein. Faustformel: (Drehzahl in min−1) × (Encoderauflösung in cpt) > 100.000 min−1 cpt ist für die meisten Anwendungen bei weitem ausreichend. Allerdings gilt auch: Je genauer die Regelung sein soll, umso höher die Impulszahl des Encoders. Bei sehr hohen Drehzahlen in Kombination mit hoher Impulszahl gilt es die Grenzfrequenz des Encoders und eventuell auch des Encodereingangs des Reglers zu beachten.
Regelung tiefer Drehzahlen ist große Herausforderung
Die großen Herausforderungen stellen sich aber bei der Regelung von sehr tiefen Drehzahlen, wenn nur noch wenige Inkremente pro Regeltakt eintreffen. Bei 60 min−1 dreht sich die Welle in 1 ms noch um 1 Tausendstel Umdrehung und ein Encoder mit 500 Zuständen liefert gerade mal jeden zweiten Regeltakt einen Impuls. Während die zustandszählende Art der Drehzahlauswertung bei hohen Drehzahlen zu einer guten Drehzahlregelung führt, reicht der Encoder mit 500 Zuständen nicht mehr aus, um eine stabile und gleichmäßig geregelte Drehzahl zu erreichen, zum Beispiel 60 min−1 mit einer Genauigkeit von 5 % oder 3 min−1. Für eine vernünftige Messgenauigkeit benötigt man eine höhere Encoderauflösung, aber auch einen schnellen Controller, um die absolut gesehen sehr kleinen aber relativ betrachtet großen Drehzahlschwankungen zu reduzieren. Ein schnellerer Regeltakt erhöht aber wiederum die Anforderungen and die Encoderauflösung. Beide Effekte wirken bei tiefen Drehzahlen zusammen und die benötigte Geberauflösung steigt umgekehrt proportional mit dem Quadrat der Drehzahl: Halbieren der Drehzahl erfordert eine 4-fach höhere Encoderauflösung.
Bei sehr niedrigen Drehzahlen erlauben einige Controller eine alternative Methode der Drehzahlauswertung. Dabei wird die Zeit gemessen, die zwischen zwei Zuständen verstreicht. Die Drehzahlrückführwerte werden homogener, die Phasenverschiebung aufgrund der Tiefpassfilterung entfällt, was eine steifere und dynamischere Regelung ermöglicht. Ergänzend oder alternativ können auch Drehzahlbeobachter verwendet werden. Diese schätzen zusätzlich laufend die Geschwindigkeit aufgrund der beobachteten Position und dem Systemverhalten ab. Die maxon EPOS4-Steuerung beispielsweise erlauben bei niedrigen Drehzahlen die Verwendung eines solchen Drehzahlbeobachters.
Die wichtigste Erkenntnis bleibt aber: Bei tiefen Drehzahlen sind Encoder mit sehr hohen Auflösungen nötig.
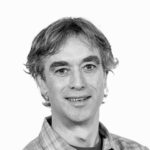
Text: Urs Kafader
Dr. Urs Kafader
ist Leiter der maxon academy, Sachseln/Schweiz.
Kontakt
maxon motor gmbh,
81825 München,
Tel. (0 89) 42 04 93 - 0,
www.maxongroup.de
Bild: maxon