Eigene Steuerungssoftware erhöht Produktivität von FTS
Mit mobilen Robotern hat Schaeffler die Montage von E-Achsen automatisiert. Die Steuerungssoftware für die FTS hat das Unternehmen selbst entwickelt.
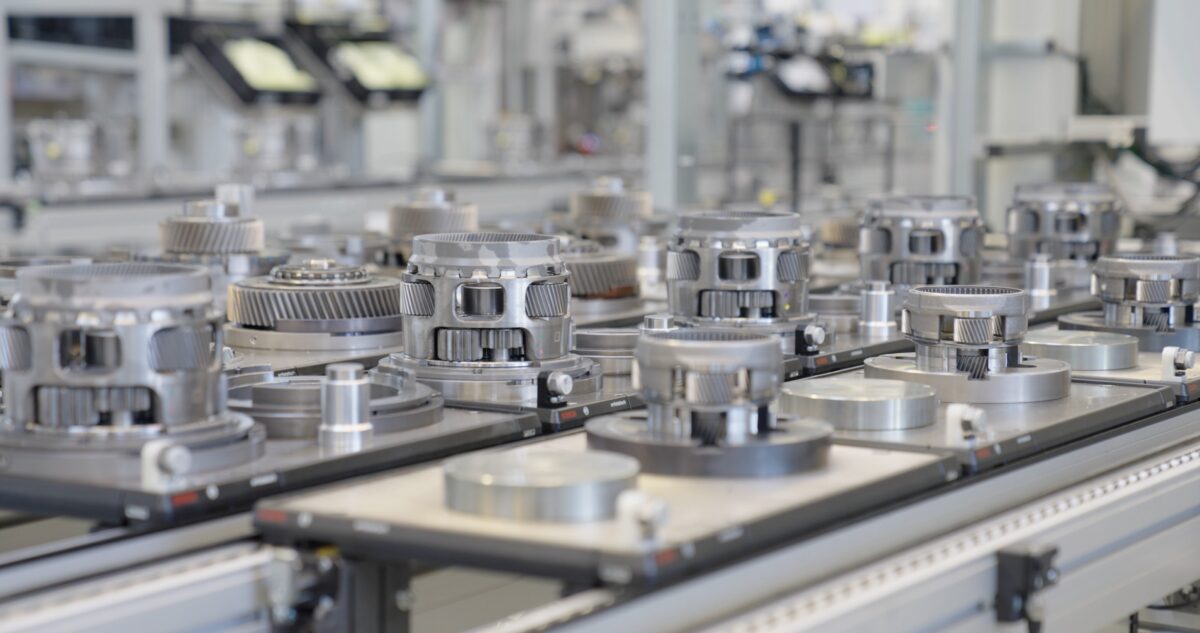
Jede Vormontagelinie fertigt zwei verschiedene Getriebebaugruppen, die in der Endmontage paarweise weiterverarbeitet werden.
Foto: Schaeffler
Seit mehr als 75 Jahren beliefert die Schaeffler-Gruppe weltweit Automobilhersteller und Industrieunternehmen mit zukunftsweisenden Erfindungen und Entwicklungen in den Bereichen Motion Technology. Das Unternehmen produziert Präzisionskomponenten und Systeme für Antriebsstrang und Fahrwerk sowie Wälz- und Gleitlagerlösungen für eine Vielzahl von Industrieanwendungen. Das Portfolio besteht aus einer Vielzahl an innovativen Techniken, darunter auch Produkte und Dienstleistungen in den Bereichen Elektromobilität und CO2-effiziente Antriebe. So produziert das Unternehmen im Feld Elektromobilität mehrere verschiedene elektrische Achsantriebe (E-Achsen). Montiert werden diese Achsen unter anderem am Unternehmenssitz in Herzogenaurach.
Mobile Roboter statt des Transports mit Handwagen
Eine E-Achse kombiniert die Komponenten Elektromotor, Getriebe und Leistungselektronik in einer Baugruppe. Die Fertigungsstraße der E-Achsen in Herzogenaurach besteht aus zwei typspezifischen Vormontagelinien, einem Puffer und einer typunabhängigen Endmontagelinie mit vollautomatischen Endprüfprozessen. Jede Vormontagelinie fertigt zwei verschiedene Getriebebaugruppen, die in der Endmontage paarweise weiterverarbeitet werden.
Der Materialtransport zwischen den Linien wurde lange Zeit zwecks Flexibilität und Unabhängigkeit von starrer Transporttechnik von den Mitarbeitenden mit Handwagen durchgeführt. Allerdings waren bei dieser Methode pro Schicht zwei anderweitig benötigte Produktionsmitarbeitende unter anderem mit dem Teilehandling zwischen Vor- und Endmontage beschäftigt. Ein kontinuierlicher Materialfluss war so nicht sicher gewährleistet. Aus diesen Gründen beauftragte Schaeffler den firmeneigenen Maschinenbauer Schaeffler Special Machinery mit der Suche nach einer neuen Intralogistiklösung.
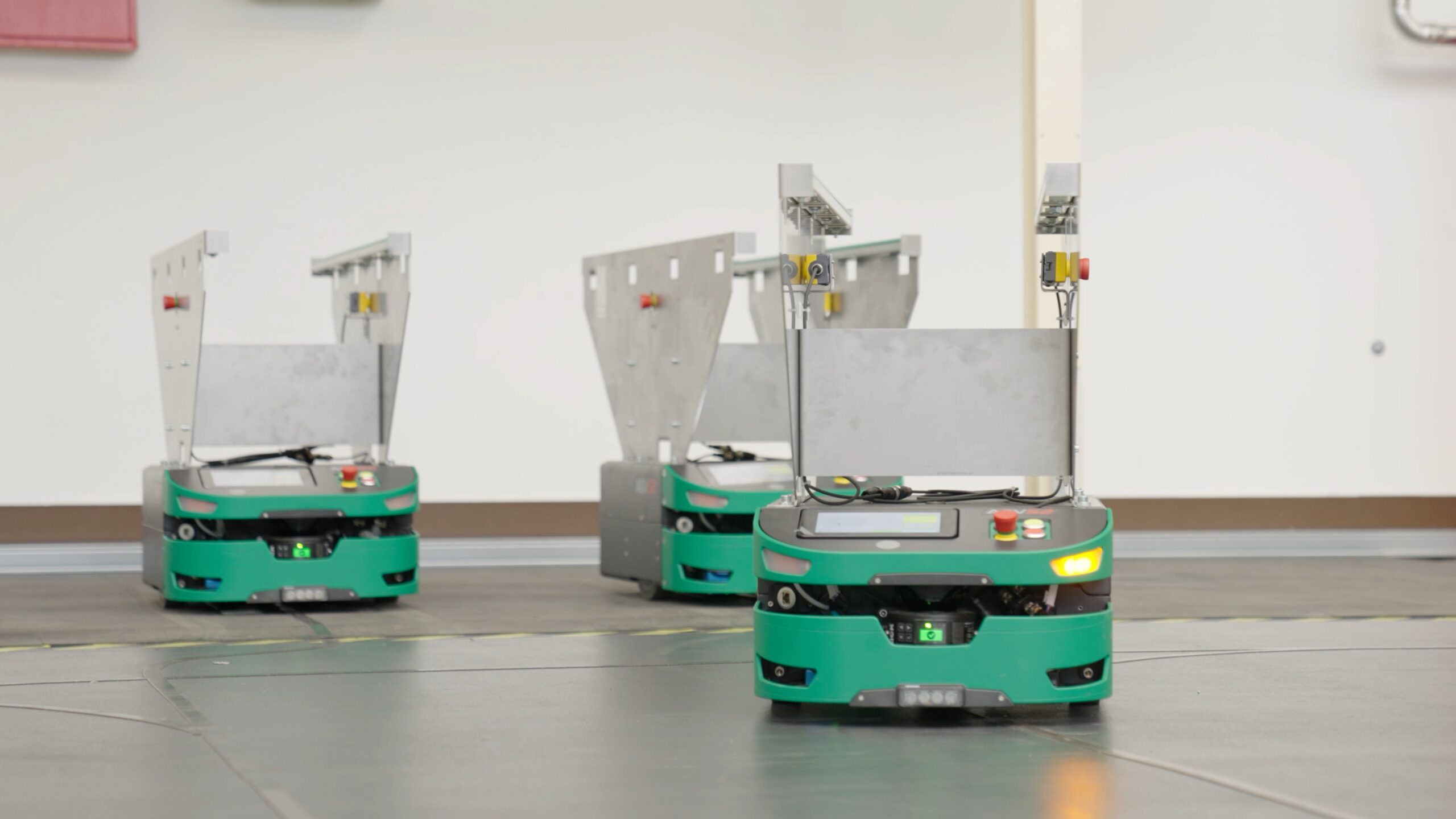
Die mobilen Roboter werden durch die eigens programmierte Software „Schaeffler AGV Middleware“ gesteuert.
Foto: Schaeffler
Schaeffler Special Machinery designt individuelle Produktionslösungen und setzt diese für seine Kunden um. Auch für das Intralogistikprojekt in Herzogenaurach erarbeitete der Special Machinery eine maßgeschneiderte Lösung. Nach der Betrachtung unterschiedlicher Automatisierungsmöglichkeiten entschieden sich die Maschinenbau-Experten für den Einsatz mobiler Roboter. Die Besonderheit: Special Machinery übernahm einen Großteil der Implementierung inklusive der Entwicklung einer eigenen Steuerungssoftware. Bei einer externen Marktanalyse überzeugte die Safelog GmbH aus Markt Schwaben.
Transportstecke ist als Kreislauf angelegt: keine Fahrt ohne Ladung
Schaeffler Special Machinery entwickelte verschiedene Lösungskonzepte für die Montageanlage in Herzogenaurach. In enger Abstimmung mit den Experten von Safelog fiel schließlich die Entscheidung für die Integration von vier Safelog AGV S2 und vollautomatischen Übergabestationen an jeder der drei Linien. Die Implementierung der einzelnen Komponenten einschließlich der eigenen Steuerungssoftware führte Schaeffler mit Unterstützung von Safelog durch.
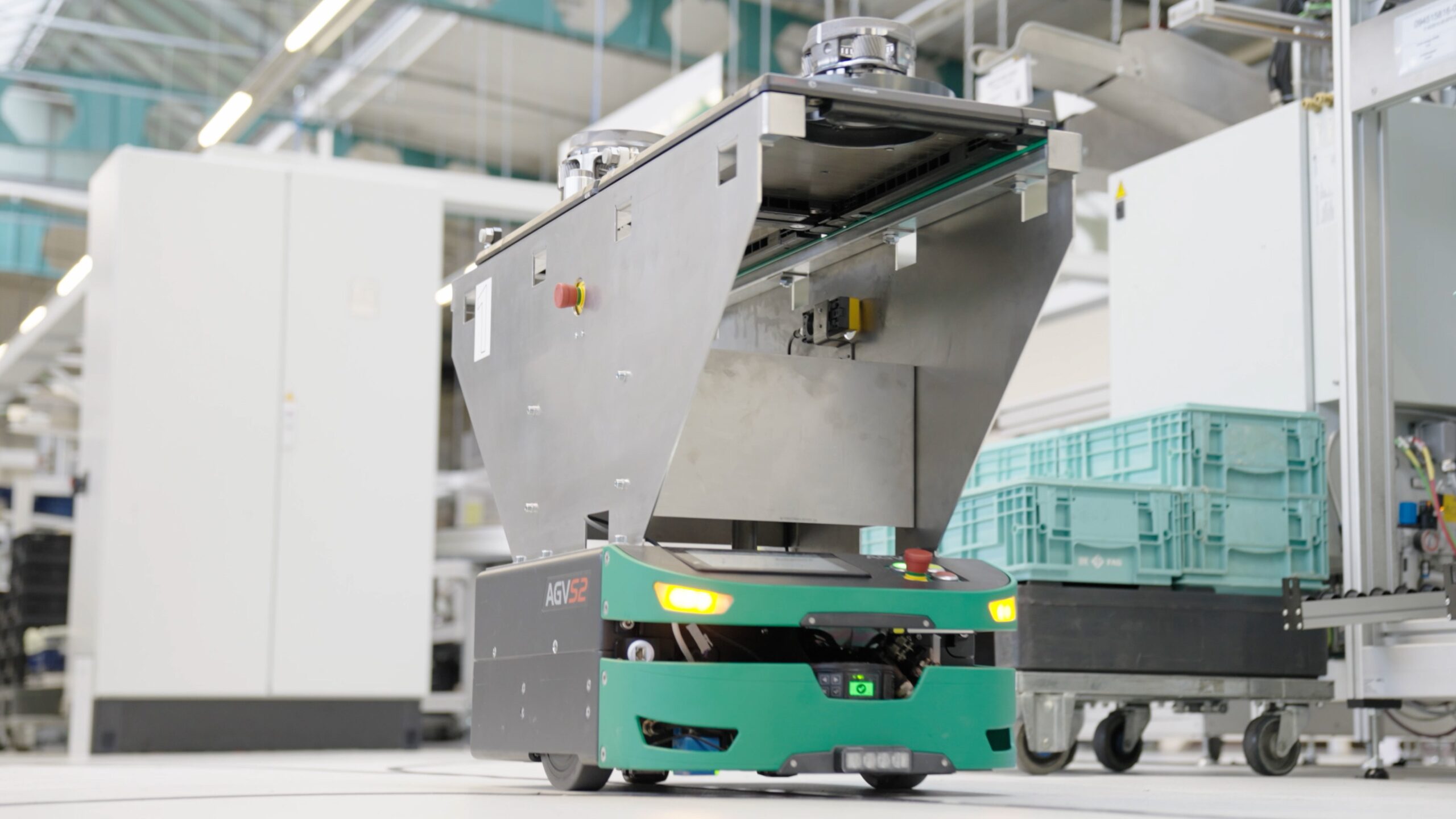
Für die Aufnahme der Werkzeugträger verfügen die AGV S2 über einen speziellen 400 mm hohen Aufbau, der Platz für zwei Werkzeugträger bietet.
Foto: Schaeffler
Die mobilen Roboter übernehmen den Transport der Werkstückträger mit den vormontierten Baugruppen zur Endmontage sowie die Rückführung der leeren Träger zur Vormontage. Die Route ist dabei als Kreislauf angelegt. Die beiden Vormontagelinien sind wie eine liegende Acht aufgebaut. Jeder Kreis produziert eine vormontierte Baugruppe auf dafür vorgesehene Werkstückträger. An der Schnittstelle in der Mitte ist eine Übergabestation in Form eines Tunnels installiert, die die verschiedenen Baugruppen paarweise an ein AGV übergibt. Bei der Einfahrt in den Tunnel werden die leeren Werkstückträger durch ein absenkbares Schwertband vom Aufbau des mobilen Roboters gezogen. Anschließend bewegt sich das Band wieder in eine senkrechte Position und transportiert die Träger in ein Zwischenlager. Beim Verlassen wird das AGV dann durch den genau umgekehrten Prozess mit den entsprechenden Trägern bestückt. Für die Aufnahme der Werkstückträger verfügen die AGV S2 über einen speziellen 400 mm hohen Aufbau, der Platz für zwei Werkstückträger bietet.
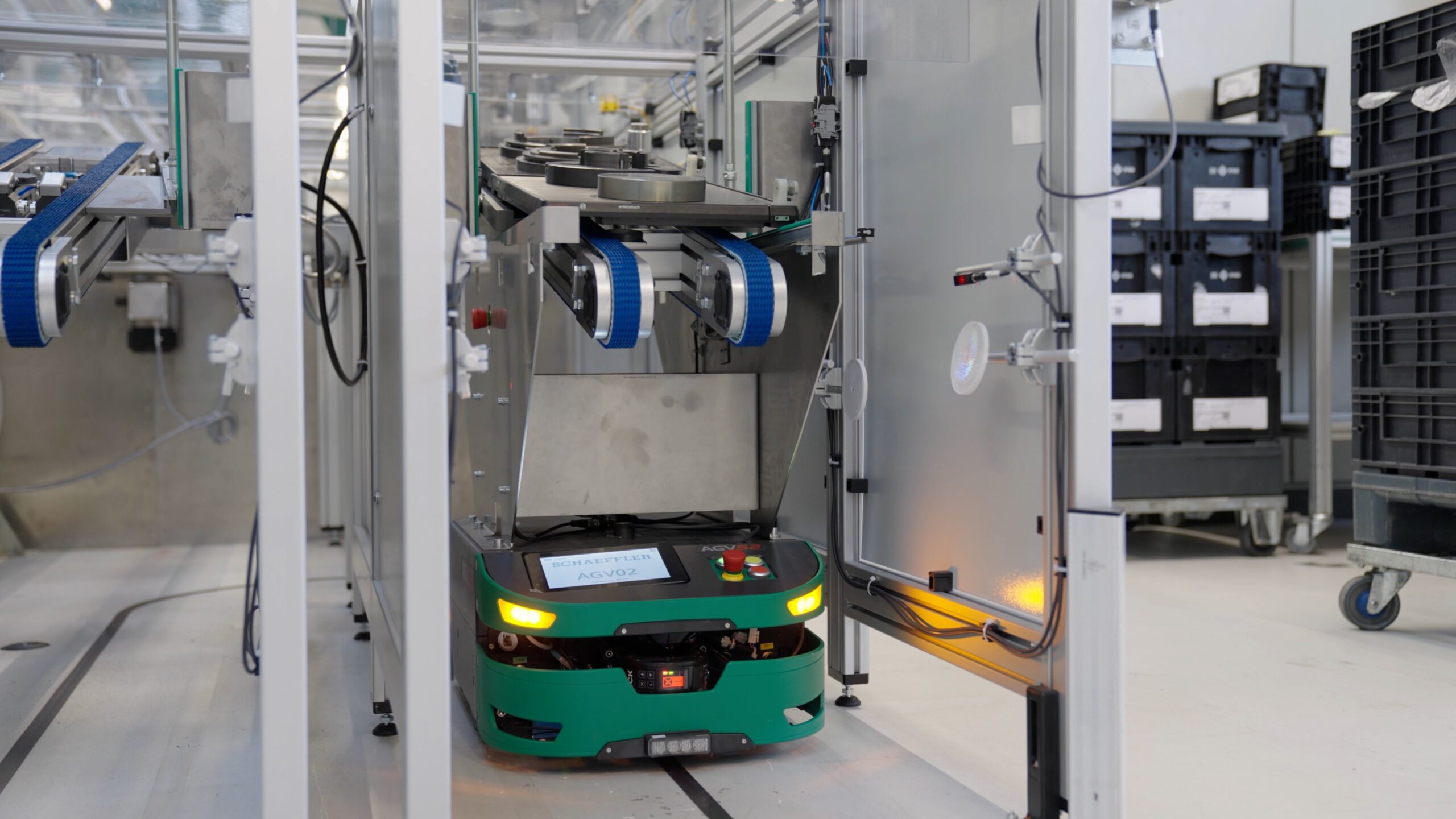
Beim Verlassen der Übergabestation wird der mobile Transportroboter mit je 2 Trägerplatten bestückt.
Foto: Schaeffler
Der Roboter bringt die vormontierten Baugruppen zur Endmontage. Dort befindet sich eine ähnliche Übergabestation wie an den Vormontagelinien, allerdings ist der Tunnel u-förmig angelegt. Beim Einfahren nimmt ein abgesenktes Schwertband die beladenen Werkstückträger auf, fährt in die Ausgangsposition und transportiert die Baugruppen über die Fördertechnik in einen Puffer. Dort können bis zu acht Baugruppen jeder Art lagern – also insgesamt 32 volle Werkstückträger. Auf diese Weise wird die kontinuierliche Materialversorgung der Endmontagelinie sichergestellt. Beim Verlassen der Übergabestation wird der mobile Transportroboter wieder mit leeren Trägern bestückt, die es zurück zur jeweiligen Vormontage transportiert. Durch diese Systematik gibt es keine Leerfahrten. Die Ladestation wird aufgesucht, bevor die Roboterbatterie vollständig entleert ist oder wenn die Auslastung der Anlage das Laden einzelner Fahrzeuge zulässt.
Selbstentwickelte Software sorgt für den vollautomatischen Transport
Mit dem Einsatz der mobilen Roboter lassen sich alle Transportaufträge automatisch durch die eigens programmierte Software „Schaeffler AGV Middleware“ steuern. Das System steuert die Geräte vollständig über das VDA5050-Protokoll mit einem eigenen Leitstand.
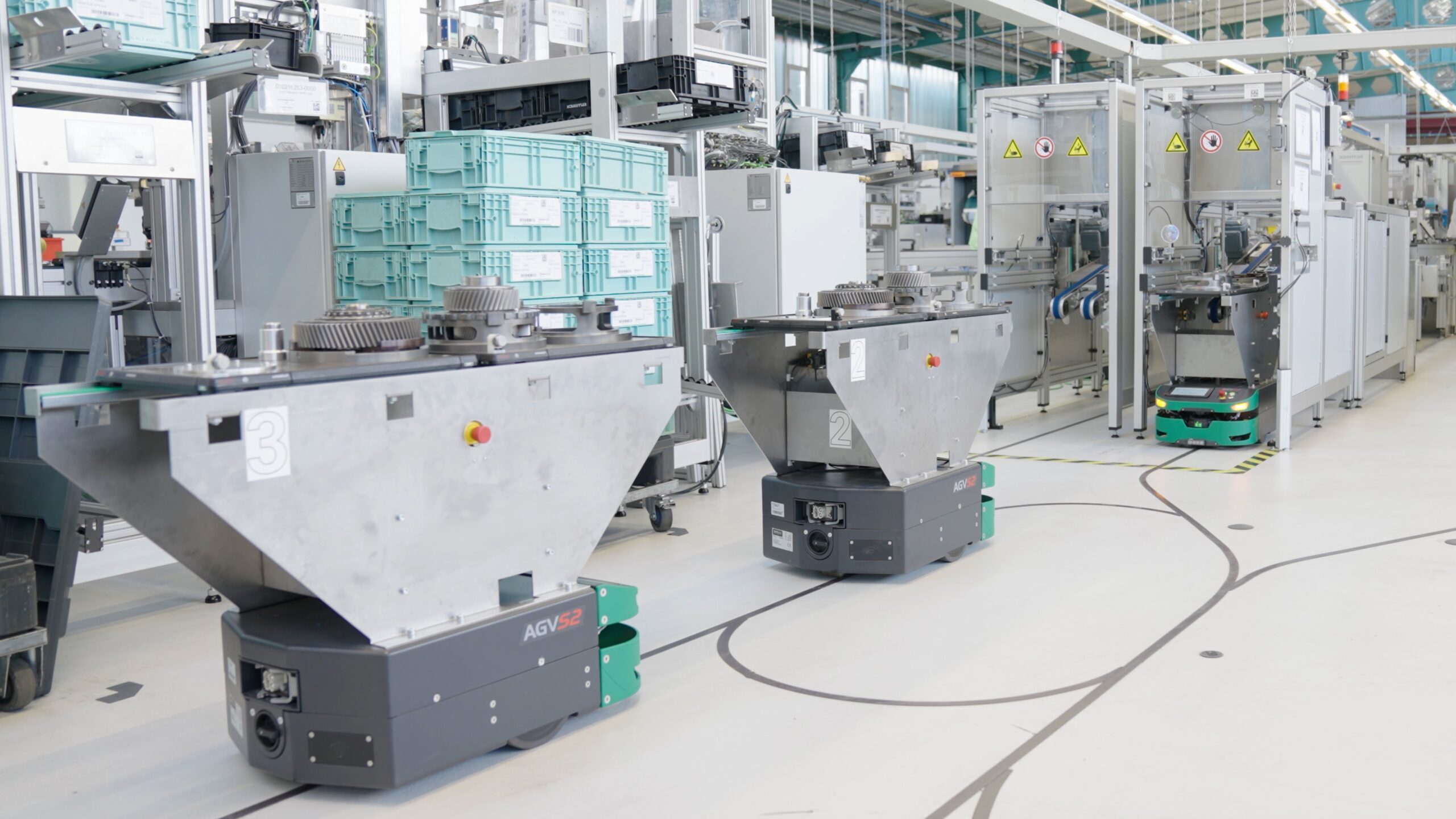
In den Bereichen der Übergabestationen navigieren die mobilen Transportroboter mit Hilfe aufgeklebter Magnetspuren – ansonsten via LLS (LiDAR LOC Service).
Foto: Schaeffler
Schaeffler Special Machinery konnte die Implementierung der AGV mit allen betriebsbedingten Anpassungen innerhalb von vier Wochen nach Anlieferung realisieren. Möglich machte das vor allem die Softwarestruktur von Safelog. „Unsere Steuerungssoftware hat offene Schnittstellen zu allen gängigen Systemen“, erklärt Max Kalk, Head of Sales bei Safelog. „Das ermöglicht eine problemlose Integration auch in bereits bestehende Systeme mit eigener Softwarearchitektur“.
Pilotprojekt erhöht Ausbringleistung
Aufgrund der Integration der AGV konnte Schaeffler die Bindung von Mitarbeiterkapazitäten beim Transport zwischen den Montagelinien minimieren und durch den kontinuierlichen Materialfluss zeitgleich die Ausbringleistung erhöhen. Das Technologieunternehmen rechnet mit einem Return on Investment (ROI) innerhalb von zwei Jahren. Für die Zukunft plant die Schaeffler Gruppe bereits weitere Projekte in Zusammenarbeit mit Safelog.