Schmierfette mittels Radial-Wellendichtungen richtig abdichten
Die berührende Abdichtung von Schmierfetten wird oft als Randthema angesehen. Entsprechend gering ist die Anzahl von wissenschaftlichen Veröffentlichungen, die dem Anwender solcher Systeme verfügbar sind. Am Institut für Maschinenelemente der Universität Stuttgart wird seit einiger Zeit an diesem Thema geforscht. Der vorliegende Beitrag fasst die für den Konstrukteur wichtigsten Erkenntnisse in einer Übersicht zusammen.
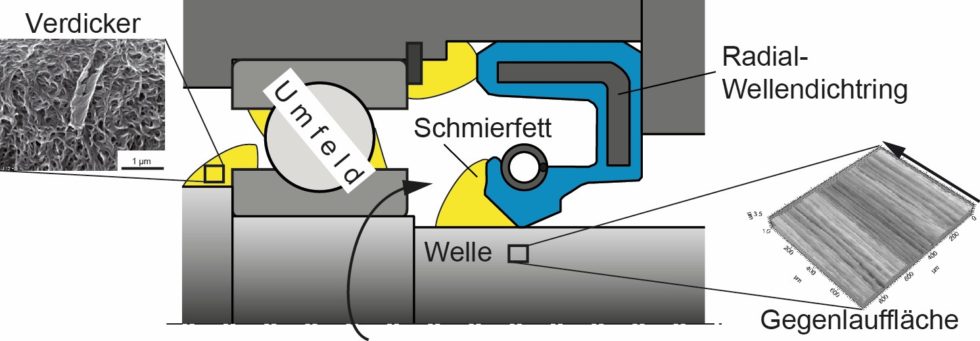
Bild 1: Fettabdichtende Radial-Wellendichtung. (Bild: IMA, Universität Stuttgart)
1 Einleitung
Die Schmierung mit Schmierfetten bietet gegenüber einer Ölschmierung wesentliche Vorteile. Der konstruktive Aufwand ist gering, es sind keine zusätzlichen Aggregate erforderlich, eine Lebensdauerschmierung ist erreichbar und das Schmierfett kann eine Barriere gegen Kontamination bilden. Die Vorteile, die Schmierfett für das Gesamtsystem bringt, sind jedoch mit großen Herausforderungen an die Radial-Wellendichtungen verbunden. Schmierfette fließen nicht wie Öle. Dies erschwert die zwingend erforderliche Schmierung des Dichtkontakts und führt im schlimmsten Fall zu Trockenlauf. Dieser mündet nach kurzer Zeit in der Zerstörung des Radial-Wellendichtrings.
2 Betriebsverhalten
Durch die geringe Fließfähigkeit von Schmierfetten findet keine nennenswerte Wärmeabfuhr vom Dichtkontakt über den Schmierstoff statt. Die maximal zulässige Umfangsgeschwindigkeit der Wellenoberfläche beträgt daher nur noch ca. 50 % des vom Dichtungshersteller für die Ölabdichtung angegebenen Grenzwerts [1].
Im Gegensatz zur Ölabdichtung steht der Radial-Wellendichtung meist auch nur eine begrenzte Schmierstoffmenge zur Verfügung. Bei der Abdichtung von Fließfetten ist ein geringer Austausch mit dem Umfeld noch gegeben [2]. Bei härteren Fetten muss die Schmierfettmenge, die sich bei der Inbetriebnahme des Systems im Bereich des Dichtkontakts befindet, diesen über die gesamte Lebensdauer schmieren. Die Verteilung des Schmierfettes in diesem Bereich ist von Einflussgrößen wie der Wellendrehzahl abhängig. Bei hohen Drehzahlen besteht die Gefahr, dass das Schmierfett von der Welle abgeschleudert wird [3].
Schmierfette bestehen aus Flüssigkeit (Grundöl) und Festkörper (Verdicker). Daraus folgen andere Verhältnisse im Dichtkontakt als bei der Abdichtung von Ölen. Das Schmierfett wird mit hohen Scherraten belastet. Diese führen zur Zerstörung der Verdickerstruktur. Im Dichtkontakt befinden sich als Folge dessen Grundöl und Verdickerpartikel aus der zerstörten Struktur. Die Größe der Partikel liegt in der Größenordnung der Dichtspaltgeometrie. Daher beeinflussen sie Reibung, Verschleiß und Dichtwirkung nachhaltig [4].
Wie gut Schmierstoff aus dem Schmierfett nahe der Dichtkante in den Dichtkontakt dringt, hängt von der Konsistenz des Schmierfettes ab. Harte Schmierfette und niedrige Temperaturen bringen ein hohes Risiko von Mangelschmierung mit sich [4]. Ansätze, bei denen Schmierfettdepots im Dichtsystem einer Mangelschmierung vorbeugen und für geringere Reibung sorgen sollen, sind vorhanden [5].
Über die Höhe des Schmierfilms im Dichtkontakt fettabdichtender Radial-Wellendichtungen sind keine abgesicherten Kenntnisse vorhanden. Es existieren Modelle, die sich dieser Fragestellung auf rechnerischem Wege nähern [6, 7]. Eine Messung der Schmierfilmhöhe stellt bereits bei Ölschmierung eine große Herausforderung dar. Bei Fettschmierung wird dieses Problem durch den Verdicker weiter verschärft [8]. Eine aussagekräftige Messung ist nach aktuellem Stand nicht veröffentlicht. Aus Messungen bei Wälzkontakten ist bekannt, dass der Schmierfilm bei Fettschmierung während der Einlaufphase höher [9–11], anschließend jedoch dünner ist als bei Ölschmierung [12]. Es wird angenommen, dass der Schmierfilm bei der Abdichtung von Schmierfetten entsprechend vergleichbar oder dünner ist als bei der Abdichtung von Ölen, also weniger als 1 µm beträgt.
3 Gestaltung
Zur Abdichtung von Schmierfetten wurden am Institut für Maschinenelemente (IMA) der Universität Stuttgart Hinweise zur Wahl bzw. Gestaltung der Komponenten Welle, Dichtelement und Umfeld sowie zum Schmierfett selbst erarbeitet (Bild 1).
3.1 Welle
Bei fettabdichtenden Radial-Wellendichtungen muss die Wärmeabfuhr fast vollständig über die Welle erfolgen. Diese sollte daher als Vollwelle aus einem gut wärmeleitfähigen Werkstoff ausgeführt sein.
Wie auch bei der Ölabdichtung ist der Wellenoberfläche, der sogenannten Gegenlauffläche, besondere Sorgfalt zu widmen. Sie muss drallfrei sein. Mikrostrukturen auf der Gegenlauffläche bewirken ein axiales Umlenken der tangentialen Schleppströmung im Dichtkontakt. Dies führt bei Schmierfett zu einer vergleichbaren Förderwirkung wie bei Öl [13]. Diese Förderwirkung kann zu Leckage oder zu Mangelschmierung oder gar zu Trockenlauf führen.
Als gut geeignet haben sich im Einstich geschliffene Gegenlaufflächen aus Stahl erwiesen. Der in Achsrichtung gemessene Rauheitswert Rz der Gegenlauffläche sollte nach DIN 3760 [14] im Bereich von 1 µm bis 5 µm liegen. Versuche mit Gegenlauf-flächen dieser Spezifikation haben gezeigt, dass das Reibmoment und die Temperatur des Dichtkontakts mit steigender Rauheit abnehmen. Die Rauheitserhebungen begünstigen die Ausbildung eines hydrodynamischen Schmierfilms im Dichtkontakt. Da der Verschleiß mit steigender Rauheit aufgrund abrasiver Rauheitsspitzen jedoch zunimmt, sollte als Kompromiss ein Rz-Wert von 2,5 µm bis 3,0 µm angestrebt werden [1].
Alternativ sind hartgedrehte Gegenlaufflächen mit einem ebenso gemessenen Rz-Wert von ca. 2,5 µm einsetzbar. Die Temperatur im Dichtkontakt und der Verschleiß sind mit einstich-geschliffenen Gegenlaufflächen vergleichbar [1, 15]. Es ist jedoch zu beachten, dass aufgrund des Drehpasses drehrichtungsabhängig Leckage auftreten kann [1], was bei der Ölabdichtung so nicht der Fall ist. Bei hartgedrehten Wellen besteht zudem die Gefahr, dass sich abrasiv wirkende Ablagerungen auf der Welle im Bereich des Dichtkontakts bilden. Diese resultieren aus einer lokalen Mangelschmierung des Dichtkontakts nahe der Luftseite [2].
Kugelgestrahlte Gegenlaufflächen begünstigen aufgrund ihrer taschenförmigen Topographie eine ausreichende Schmierung des Dichtkontakts und führen daher zu sehr geringen Reibmomenten und Temperaturen. Ihr Einsatz ist allerdings aufgrund der vergleichsweise scharfen und folglich abrasiv wirkenden Taschenränder nur unter Vorsicht ratsam [2].
Die ideale Gegenlauffläche zeichnet sich durch tiefe Senken und eine geringe Höhe von Rauheitsspitzen aus [2]. Die tiefen Senken begünstigen die Ausbildung eines Schmierfilms, was zu geringer Reibung führt. Fehlen ausgeprägte Rauheitsspitzen, wirkt die Gegenlauffläche kaum abrasiv auf die Dichtkante. Anhand von 3D- Rauheitskennwerte nach DIN EN ISO 25178-2 [16] ausgedrückt, bedeutet dies eine große Fünf-Punkt-Senkenhöhe S5v (S5v > 3 µm, Pruning = 6 % Sz) bei gleichzeitig geringer reduzierter Spitzenhöhe Spk (Spk < 1 µm). Die Messfläche sollte bei der Ermittlung der Kennwerte mindestens fünf Oberflächenstrukturen (Erhebungen und Vertiefungen) beinhalten. Mit einer Messfläche von 1 x 1 mm wurden am IMA gute Erfahrungen gemacht.
3.2 Dichtelement
Radial-Wellendichtringe nach DIN 3761 [17] sind zur Abdichtung von Schmierfetten geeignet. Das Schmierfett sollte dabei auf der Stirnseite anstehen, siehe Bild 1, und der abzudichtende Raum entlüftet sein. Fett nur auf der Bodenseite kann zu Mangelschmierung führen [1]. Von hydrodynamischen Dichthilfen („Drall“) bzw. einer ondulierten Dichtkante ist abzusehen. Diese unterstützen die Dichtwirkung bei der Ölabdichtung, indem sie Leckage axial umlenken und zurückführen. Die mikroskopische Förderwirkung der Dichtkante [18] ist bei solchen Elementen aufgrund fehlender Notwendigkeit daher oft schwächer ausgeprägt. Bei Schmierfetten tritt bei Dichtelementen mit derartigen Dichthilfen jedoch Leckage auf [1, 13]. Es wird ein Anhaften des ausgetretenen Schmierfetts an der Luftseite vermutet, welches eine Rückförderung zumindest teilweise unterbindet. Die in diesem Fall erforderliche Dichtwirkung der Dichtkante ist zu gering.
Aufgrund der starken Wärmeentwicklung im Dichtkontakt und der geringen Wärmeabfuhr bei der Fettabdichtung ist eine geringe Linienpressung der Dichtrings anzustreben (Richtwert: 0,1 N/mm im Neuzustand) um die Wärmentwicklung zu verringern [1]. Als Dichtringwerkstoffe sind NBR und FPM geeignet. NBR verschleißt weniger und erzeugt ein geringeres Reibmoment als FPM [13, 15], ist allerdings weniger temperaturbeständig. Tritt im Bereich der Bodenseite lokale Mangelschmierung auf, wirkt sich Fett zwischen Dichtkante und einer knapp nicht berührenden Schutzlippe positiv auf die Schmierung des Dichtkontakts aus, da Schmierstoff auch von der Luftseite aus in den Dichtkontakt dringt [2]. Dieser Bereich sollte zu ca. 30 % mit Fett gefüllt werden.
Zugfederlose Elastomerdichtringe mit Spiralförderrille (z. B. F-Less-Dichtung) sind eine Alternative zum Radial-Wellendichtring nach DIN 3761 [1]. PTFE-Dichtelemente sind aufgrund des fehlenden Rückförderverhaltens nicht geeignet um Fett leckagefrei abzudichten [1, 15]. VR-Dichtringe führen zwar zu vergleichsweise geringen Temperaturen im Bereich des Dichtkontakts, allerding ist bei ihrem Einsatz ebenfalls mit Leckage zu rechnen [1].
3.3 Umfeld
Insbesondere bei Fließfetten wirkt sich die Gestaltung des Dichtungsumfelds erheblich auf das Dichtsystem aus. Eine mitrotierende Scheibe auf der Welle (Außendurchmesser ca. 60 mm bei einem Wellendurchmesser von 50 mm) nahe des Dichtrings hält das Schmierfett in Bewegung und trägt somit zu einem Abtransport der Reibwärme bei. Die Temperatur im Bereich der Dichtkante lässt sich dadurch um mehrere Kelvin senken [1, 15]. Eine vermeintliche Verbesserung des Schmierfettangebots durch Versorgungsbohrungen [15] bzw. ein Halten des Schmierfetts im Bereich der Dichtung durch Stauscheiben haben keinen positiven Einfluss [1, 15].
Das Dichtsystem sollte sich nach Möglichkeit nicht unmittelbar neben Komponenten befinden, die Wärme erzeugen und in die Welle einleiten. Dies führt zu einer höheren thermischen Belastung des Dichtelements und verkürzt die Lebensdauer. Eine horizontale Lage der Welle ist einer vertikalen stets vorzuziehen. Sollte eine vertikale Lage erforderlich sein, ist insbesondere das obere Dichtsystem einem hohen Mangelschmierungsrisiko bis hin zu Trockenlauf ausgesetzt. In Versuchen wurden bei am tiefsten Punkt eingebauten Dichtsystemen im Vergleich zu horizontaler Wellenlage deutlich erhöhte Temperaturen im Bereich des Dichtkontakts gemessen [15]. Der bei horizontaler Wellenlage bei Fließfetten stattfindende Schmierfettaustausch wird durch die vertikale Lage unterbunden.
Das System sollte entlüftet sein, um eine zusätzliche Anpressung der Dichtkante durch Überdruck zu vermeiden. Eine zusätzliche Anpressung hat einen erhöhten Wärmeeintrag zur Folge.
3.4 Schmierfett
Das Schmierfett ist die Systemkomponente mit dem größten Einfluss auf das Betriebsverhalten von Radial-Wellendichtungen. Eine für das Dichtsystem günstige Schmierstoffwahl ist jedoch oft nur eingeschränkt bis gar nicht möglich. Meist stehen die Anforderungen anderer Tribosysteme, wie Verzahnungen und Lager, im Vordergrund.
Prinzipiell sind Schmierfette mit geringer Konsistenz besser zur Abdichtung geeignet. Diese versorgen den Dichtkontakt besser mit Schmierstoff und beugen somit Mangelschmierung vor. Ferner ist zu beachten, dass die Schmierfettkonsistenz temperaturabhängig ist und das Risiko einer Mangelschmierung beim Kaltstart erhöht ist [4]. Schmierfette mit geringer Konsistenz sind fließfähiger und führen daher zu einer geringeren Temperatur im Bereich des Dichtkontakts, da sie ein gewisses Maß an Reibwärme abführen können [15].
Geringe Reibungsverluste können durch eine geringe Grundölviskosität erreicht werden [1]. Diese führen zu geringeren Scherverlusten im Dichtkontakt. Der Verdickeranteil hat, wenn die Dichtkante gut geschmiert ist, so gut wie keinen Einfluss. Die Zusammensetzung des Schmierstoffs im Dichtkontakt aus Grundöl und einzelnen Verdickerpartikeln wird vom Verdickeranteil im abzudichtenden Fett offensichtlich kaum beeinflusst. Die Verdickerart hat hingegen einen großen Einfluss auf die Höhe der Reibung (Bild 2). Im Mischreibungsgebiet wirken die Verdickerpartikel im Dicht-kontakt schmierend und reibungsmindernd. Besonders ausgeprägt ist dies bei kleinen Verdickerpartikeln wie Kieselsäure und Aluminiumseifen. Bei voll hydrodynamischer Reibung führen diese Schmierfette hingegen zu hoher Reibung. Die kleinen Partikel gelangen leicht in den Dichtkontakt und wirken viskositätserhöhend. In diesem Fall führen z.B. Lithiumseifen zu geringerer Reibung. Die Grundölart hat viel weniger Einfluss als die Verdickerart [4].
Schmierfette mit Kieselsäureverdicker wirken abrasiv auf die Gegenlauffläche. Diese kleinen, harten Partikel lagern sich in der weichen Dichtkante ein und führen zum Einlauf in die Welle. Ein besonders geringer Verschleiß wurde bei Schmierfetten mit Aluminiumseifen gemessen. Aufgrund der kugelförmigen Verdickerpartikel wird ein Abwälzen der Rauheitserhebungen auf diesen vermutet [4].
4 Alternative Abdichtbedingungen
Bei der Abdichtung von Wälzlagern können oftmals geringe Fettleckagen toleriert werden und überschüssiges Schmierfett muss beim Nachschmieren das System verlassen können. Die Hauptaufgabe des Dichtsystems liegt dann darin, das Eindringen von Verunreinigungen (abrasive Partikel, Wasser, Schmieröl, …) ausreichend zu behindern. Um dies zu erreichen werden oft „umgekehrt“ eingebaute, bodenseitig befettete Radial-Wellendichtungen verwendet (Bild 3). Eine Alternative hierzu sind (ins Lager integrierte) Dichtscheiben mit sehr geringer Linienpressung die wesentlich reibungsärmer und daher weniger thermisch belastend sind. Somit sind höhere Umfangsgeschwindigkeiten erreichbar. Ebenso können bei geforderten hohen Umfangsgeschwindigkeiten Deckscheiben verwendet werden. Diese bilden nach einer Einlaufphase einen engen Spalt aus und dichten berührungsfrei ab. Ein Schutz gegen das Eindringen von Flüssigkeit ist dann allerdings nicht mehr gegeben. Solche Systeme werden u. a. am Institut für Maschinenkonstruktion und Tribologie (IMKT) der Universität Hannover untersucht [19].
5 Zusammenfassung und Ausblick
Schmierfette stellen aufgrund ihrer Besonderheiten hohe Anforderungen an berührende Wellendichtungen. Nur eine gezielte Auslegung der Dichtstellen ermöglicht ein betriebssicheres Abdichten. Die vier Komponenten Dichtelement, Welle, Umfeld und Schmierfett sollten nach Möglichkeit folgenden Anforderungen entsprechen:
Dichtelement: Radial-Wellendichtring mit geringer Linienpressung (ca. 0,1 N/mm).
Welle: Einstichgeschliffene Gegenlauf-fläche, Rz ≈ 2,5 µm.
Umfeld: Horizontale Wellenlage, mitrotierende Scheibe.
Schmierfett: Fließfett (weiches Fett) mit geringer Grundölviskosität.
Inwiefern Mangelschmierung durch optimales Gestalten des Dichtsystems gemindert werden kann, ist Gegenstand aktueller Arbeiten. Für eine Bewertung der Schmierfett- bzw. Additivverträglichkeit fettabdichtender Dichtsysteme fehlen grundlegende Untersuchungen noch völlig. Dies ist auch bei der Abdichtung von Ölen eine nicht ausreichend beantwortete Fragestellung [20, 21]. Die Simulation des Betriebsverhaltens fettabdichtender Radial-Wellendichtungen ist ein weiteres, nach aktuellem Stand ungelöstes Problem.
Literatur:
[1] Dürnegger, W.; Haas W.: Fette mittels Radial-Wellendichtung zuverlässig abdichten, FKM-Forschungsheft 302, Frankfurt/Main, 2009
[2] Narten, M.: Abdichtung von fließfettgeschmierten Getrieben mit Radialwellendichtungen – Reibungsminderung durch Makrostrukturierung der Dichtungsgegenlauffläche, Dissertation, Universität Stuttgart, 2014
[3] Baart, P.: Grease lubrication mechanisms in bearing seals, Dissertation, Luleå University of Technology, 2011
[4] Sommer, M.: Einfluss des Schmierfetts auf das tribologische System Radial-Wellendichtung – Betriebsverhalten und Funktionsmodell, Dissertation, Universität Stuttgart, 2015
[5] Zhou, X.; Barbera, S.: WO 2011110360 A1, Low-friction seal, 2011.
[6] Wangenheim, M.; Kozma, M. ; Mate, L.: Friction behavior of grease lubricated seals, 15th ISC, 2008
[7] Baart, P.; van Zoelen, M. ; Lugt, P.: Film thickness model for grease-lubricated bearing seals with an axial contacting lip. Tribology Transactions, 56 (1), S. 109–114, 2013
[8] Wangenheim, M.: Untersuchungen zu Reibmechanismen an Pneumatikdichtungen, Dissertation, Universität Hannover, 2012
[9] Cann, P.: Thin-film grease lubrication. Proceedings of the Institution of Mechanical Engineers, Part J: Journal of Engineering Tribology, 213 (5), S. 405–416, 1999
[10] Wilson, A.: The relative thickness of grease and oil films in rolling bearings. Proceedings of the Institution of Mechanical Engineers, 193 (1), S. 185–192, 1979
[11] Cousseau, T. et al.: Film thickness in a ball-on-disc contact lubricated with greases, bleed oils and base oils. Tribology International, 53, S. 53–60, 2012
[12] Cann, P.: Grease degradation in a bearing simulation device. Tribology International, 39 (12), S. 1698–1706, 2006
[13] Sommer, M.; Haas, W.: Fette mittels Radialwellendichtung zuverlässig abdichten II, FKM-Forschungsheft 314, Frankfurt/Main, 2012
[14] DIN 3760: Radial-Wellendichtringe, Beuth, Berlin, 1996
[15] Narten, M.; Haas, W.: Abdichtung von Fließfetten, IGF-Nr. 15703, FVA-Heft Nr. 1016, Frankfurt/Main, 2012
[16] DIN EN ISO 25178–2: Geometrische Produktspezifikation (GPS) – Oberflächenbeschaffenheit: Flächenhaft – Teil 2: Begriffe und Oberflächen-Kenngrößen, Beuth, Berlin, 2008
[17] DIN 3761–1: Radial-Wellendichtringe für Kraftfahrzeuge, Beuth, Berlin, 1984
[18] Kammüller, M.: Zur Abdichtwirkung von Radial-Wellendichtringen, Dissertation, Universität Stuttgart, 1986
[19] Ottink, K. ; Poll, G.: Schutzdichtungen für Wälzlager II, FVA-Heft Nr. 1053, Frankfurt a. M., 2013
[20] Klaiber, M.: Einfluss verschiedener Additive auf Elastomere und die tribologischen Eigenschaften im System Radial-Wellendichtung, FKM-Forschungsheft 318, Frankfurt/Main, 2012
[21] Flórez A. ; Hentschke, C.: Verträglichkeit von Schmierstoffen und Elastomeren, FVA-Heft Nr. 1128, 2015
LiteraturAutorenDr.-Ing. Max Sommer Prof. Dr.-Ing. habil. Werner Haasbeide: Institut für Maschinenelemente (IMA) Universität Stuttgart Pfaffenwaldring 9 70569 Stuttgart Tel.: 07 11/6 85-6 61 70 E-Mail: werner.haas@ima.uni-stuttgart.de www.ima.uni-stuttgart.de