Arbeitsplanung mit einer Low-Code-Plattform
Beim Erstellen von Arbeitsplänen gibt es zwei Entwicklungen, die Fertigungs- und Montageplaner vor Probleme stellt. Zum einen soll die Produktion möglichst agil aufgestellt sein, zum anderen steigt die Anzahl individueller Kundenwünsche. Unterstützung bietet eine Anwendung auf Basis einer Low-Code-Plattform. Aufgrund der grafischen Benutzeroberfläche der Low-Code-Plattform können Anwender direkt in die Entwicklung einbezogen werden. Ziel ist es, automatisiert aus dem 3D-CAD-Modell einer neuen Bauteilvariante, einen vollständigen Fertigungsarbeitsplan abzuleiten.
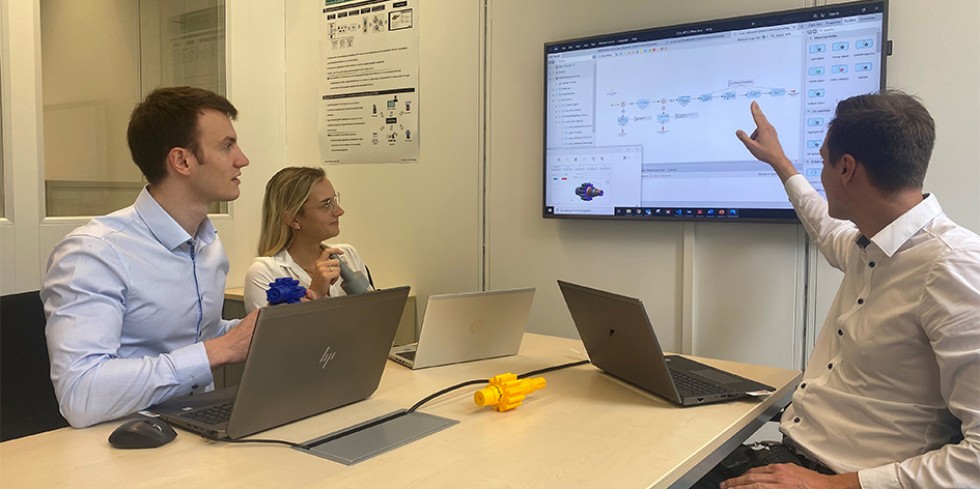
Das 3D-CAD-Modell als Ausgangsbasis für eine automatisierte Arbeitsplangenerierung.
Foto: Siemens
Die Umsetzung der steigenden Anzahl von individuellen Kundenwünschen bringt die Fertigungs- und Montageplaner an ihre Grenzen. Im Rahmen der agilen Produktion bedarf es einer Lösung, die es ermöglicht, die Produktionsplanung schnell und effizient zu unterstützen. Eine, in der Siemens Low-Code-Plattform Mendix aufgebaute, Anwendung bietet dabei eine automatisierte Lösung, die basierend auf einem Regelwerk optimierte und flexible Arbeitspläne generiert [1] [2]. Durch den modularen Ansatz lassen sich viele implementierte Funktionalitäten in weiteren Anwendungsfällen neu kombinieren, erweitern und wiederverwenden.
Aufgrund der stetig wachsenden Anforderungen, der zunehmenden Agilität der Produktentwicklung und der verstärkten Fokussierung auf individuelle Kundenwünsche sind die Fertigungsplanungsprozesse zunehmend schwerer zu gleichbleibenden Kosten zu bewerkstelligen [2].
Zum Umsetzen einer Konstruktionsanforderung legt ein Arbeitsvorbereiter einen Arbeitsplan im Produktionsplanungssystem an. Der Arbeitsplan dokumentiert die einzelnen Fertigungs- und Montageschritte des Bauteils oder des Erzeugnisses für die später folgende Produktion. Aus der Vielzahl an individuellen Konstruktionsvarianten folgt ein wiederkehrender Arbeitsaufwand, der manuell erfolgt und zu Fehlern führen kann. Hinzu kommt der Aspekt, dass das Wissen des Arbeitsplanerstellers auf individuellen Erfahrungen basiert und somit beschränkt ist. Dementsprechend werden in einem manuell erstellten Arbeitsplan in der Regel nicht alle möglichen alternativen Fertigungsschritte berücksichtigt oder angelegt. Die alternativen Fertigungsschritte bieten eine Durchlaufzeit-optimierte Eintaktung der einzelnen Bauteile durch die Fertigung und eine Echtzeit-Ausweichmöglichkeit auf alternative Arbeitseinrichtungen im Falle von Produktionsstörungen. [3]
Anwender in Entwicklung einbeziehen
Low-Code-Plattformen ermöglichen es, durch die grafisch gestaltete Benutzeroberfläche die späteren Anwender („citizen developer“), die ihre Anforderungen bestens kennen, direkt in den Software-Entwicklungsprozess einzubeziehen. Dabei wird die Anwendungslogik, zum Beispiel die Arbeitsplanungsfunktion, durch die Anwendung von vorgefertigten Elementen (Programmbausteine) visuell über Drag&Drop-Funktionen konfiguriert [5].
Nicht nur die Fertigungsprozesse unterscheiden sich von Werk zu Werk, sondern auch die Anwenderanforderungen an solch eine automatisierte Funktion. Den Siemens-Experten ist aufgefallen, dass sich trotz unterschiedlichste Wünsche, die Anwenderanforderungen auf abgekapselte Sub-Funktionsbausteine herunterbrechen lassen. Diese sogenannten Sub-Module einer Low-Code-Programmierung können wiederverwendet werden. Die Sub-Module lassen sich je nach Anwenderbedarf zu neuartigen Funktionsmodulen kombinieren, die dann eine individuelle Nutzeranwendung ergeben. Auf diese Weise wird die Code-Wiederverwendung auf Basis von funktionalen Sub-Modulen aus Bibliotheken erhöht. Ein Beispiel für die Sub-Modulfunktionalität stellt die Scanner-Funktionalität dar, die das Einlesen und die Verarbeitung einer, in einem Barcode hinterlegten, Codierung darstellt. Durch die sukzessive Erweiterung dieser Sub-Modul-Bibliothek lassen sich künftig neuartige Anwendungen (APPs) noch schneller zusammenstellen. Bild 1 zeigt schematisch den Aufbau einer Low-Code-Applikation bestehend aus funktionalen Modulen aus einer Sub-Modul-Bibliothek.
Das Ziel ist es, automatisiert für eine neue Bauteilvariante (aus dessen Bauteildefinition in Form eines 3D-CAD-Modells), nach einem vordefinierten Regelwerk, einen vollständigen Fertigungsarbeitsplan abzuleiten. Der Arbeitsplan beinhaltet alle notwendigen Arbeitsvorgänge, um das Fertigteil zu erzeugen. Zusätzlich wird zu jedem Arbeitsvorgang ein optimaler Arbeitsplatz zugeordnet, sowie alle in Frage kommenden Alternativarbeitsplätze festgelegt. Der Fertigungsdurchlauf wird aufgrund der zugewiesenen Alternativarbeitsplätze flexibilisiert und ermöglicht somit eine optimale Kapazitätsauslastung. [4] Durch diese Vorgehensweise kann die Fertigungskapazität bei sonst gleichbleibenden Bedingungen um 22 % erhöht werden. Bild 2 zeigt schematisch die einzelnen Arbeitsfolgen zur Fertigung eines Einzelteils mit den möglichen Alternativen, beispielsweise für den Dreh- und Schleifprozess.

Bild 2: Durch Ausweicharbeitsplätze (Arbeitsplatz AP) für die einzelnen Arbeitsvorgänge wird die Produktions-Kapazitätsauslastung erhöht. Grafik: Adam Myszkowski
Haupteingangsgrößen aus 3D-CAD-Modell
Für das automatisierte Erstellen eines Arbeitsplans sind die strukturierten geometrischen Informationen des zu fertigenden Bauteils in Form eines 3D-CAD-Modells, aus einem Produktdatenmanagement-System (PDM-System), die Haupteingangsgröße. Zusätzlich werden auch Informationen aus dem Enterprise Resource Planning (ERP)-System für die Maschinenzuweisung ausgeleitet. Das hinterlegte Mendix-Regelwerk wird auf das 3D-CAD-Modell des Bauteils aus dem PDM-System angewendet. Über subtraktive Bearbeitungsverfahren wird die Zielgeometrie, ausgehend von dem zuvor zugewiesenen Rohteil, erreicht. Die dafür notwendigen Arbeitsvorgänge werden sukzessive, regelbasiert, dem Arbeitsplan hinzugefügt. Die Arbeitsvorgänge werden jeweils um Fertigungsstationen (zum Beispiel die Werkzeugmaschinen) ergänzt, die nach festgelegten Kriterien, wie beispielsweise der Fertigungstechnologie, im Stande sind, den notwendigen Arbeitsvorgang umzusetzen. In Bild 3 wird schematisch dargestellt wie aus den Definitionsinformationen in Form des 3D-CAD-Modells mit PMI und dem Regelwerk in der Low-Code-Plattform Mendix automatisiert der Arbeitsplan entwickelt wird.
Pilotprojekt bei einem Getriebehersteller
Gemeinsam mit einem namhaften Getriebehersteller wurde ein Pilot-Projekt zur automatisierten Arbeitsplanableitung exemplarisch für Stirnräder unter Verwendung der Siemens Low-Code Plattform Mendix aufgebaut. Ein Fertigungsexperte des Getriebeherstellers erklärt die Vorgehensweise: „Die geometrischen Informationen des zu produzierenden Bauteils aus einer Geometriedatenbank werden durch ein, in Mendix aufgebautes Regelwerk analysiert. Dabei wird zu den abgeleiteten Arbeitsvorgängen jeweils ein Vorzugsarbeitsplatz festgelegt, der ein Optimum für die Wertschöpfung darstellt. Es werden aber auch Ausweichmöglichkeiten in Form von Alternativarbeitsplätzen definiert. Die alternativen Arbeitsplätze sind von ihren prozessualen Fähigkeiten her in der Lage, ebenfalls den Arbeitsvorgang umzusetzen“.
Nach den Erfahrungen bei Siemens, stellen diese alternativen Arbeitsplätze in der operativen Fertigungssteuerung eine Ausweichmöglichkeiten dar, die bei Kapazitätsengpässen (zum Beispiel Störungen) relevant sind. Die Umsetzung des Regelwerks mit der Low-Code Plattform Mendix gewährleistet die nachträgliche Anpassbarkeit bei Anforderungsänderungen durch die Nutzung von neuen Sub-Modulen aus der Funktionsbibliothek – ganz ohne Programmierkenntnisse.
Als logischen nächsten Schritt werden künftig die Experten bei Siemens und dem Getriebehersteller das 3D-CAD-Modell in Form des Functional Information Model (FIM) als Eingangsgröße für die automatisierte Arbeitsplanung verwenden. Das FIM beinhaltet zusätzlich zu der 3D-Geometrie auch weitere fertigungsrelevante Informationen in Form von Product- and Manufacturing Information (PMI). Damit wird im FIM beispielsweise eine Toleranzangabe oder auch die geforderte Oberflächenrauheit definiert. Die fertigungsrelevanten Informationen werden in den PMIs beschrieben und stellen in Kombination mit der 3D-Geometrie die erforderlichen Informationen vollständig zu dem zu fertigenden Bauteil zur Verfügung. Des Weiteren soll auch der baukastenbasierte Ansatz der APP-Entwicklung weiterverfolgt werden. Damit verbunden wird die Bibliothek um weitere Sub-Module erweitert, die den App-Entwicklungsprozess weiter beschleunigen. Dadurch kann der Anwendernutzen in sehr kurzer Zeit verbessert werden. Eine kontinuierliche Erweiterung der Funktions-Bibliothek ist entscheidend, um die Wiederverwendung der Sub-Module weiter zu beschleunigen, so die Expertenmeinung.
Literatur
- [1] R. Sanchis, O. Garcia-Perales, F. Fraile und P. Poler, „Low-Code as Enabler of Digital Transformation in Manufacturing Industry,“ Appl. Sci., 2020.
- [2] R. Waszkowski, „Low-code platform for automating business processes in manufacturing,“ IFAC-PapersOnLine, pp. 376–381, 2019.
- [3] M. Eigner und R. Stelzer, Product Lifecycle Management, Berlin, Heidelberg: Springer, 2009.
- [4] C. Saygin und S. Kilic, „Integrating Flexible Process Plans with Scheduling in Flexible Manufacturing Systems,“ Int J Adv Manuf Technol 15, pp. 269–280, 1999.
- [5] A. Benjamin, S. Hinrichsen und A. Nikolenko, „App Development via Low-Code Programming as Part of Modern Industrial Engineering Education,“ Advances in Intelligent Systems and Computing, 01 July 2020.

Adam Myszkowski
ist Research Scientist bei der Siemens AG (Bereich T AMM DMT-DE)
(Foto: Siemens
Pierre Brionne
und Alexander Nowitschkow, sind dort Research Scientist bei der Siemens AG (Bereich T AMM DMT-DE).
Kontakt
Dr.-Ing.Peter Robl Siemens AG – T AMM DMT-DE, 81739 München
peter.robl@siemens.com