Simulationsgestütztes Entwicklen wird immer wichtiger
Welche Trends werden den CAD-Markt im Jahr 2023 bestimmen? Eine Einschätzung von Brian Thompson, General Manager und Divisional Vice President CAD bei PTC.
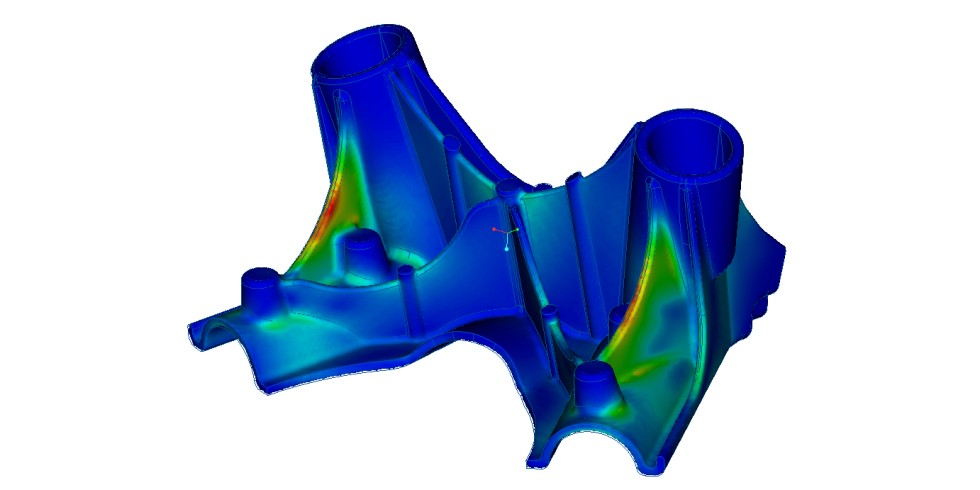
Strukturelle Spannungsanalyse eines Schneemobilteils unter Verwendung von Creo Simulation Live zur Echtzeit-Konstruktionsunterstützung.
Foto: PTC
Im Jahr 2023 wird der CAD-Markt weiterhin von den Bedürfnissen der Hersteller als Reaktion auf einzigartige makroökonomische Trends bestimmt. Interessanterweise wirken sich diese Trends, die sich, während der COVID-19-Pandemie beschleunigt haben, unterschiedlich auf große und kleine Unternehmen aus.
Wir befinden uns heute in einem stark inflationären Umfeld. Rohstoffe und Teile sind teurer denn je, und die gut dokumentierten Engpässe in der Lieferkette wirken sich weiterhin auf die Hersteller aus. Ein weiterer wichtiger Makrotrend ist die Stärke des Dollars im Vergleich zum Euro. Wenn der Euro schwächer wird, spüren Hersteller, die ihre Rohstoffe in Euro einkaufen, einen erheblichen Druck auf ihre Gewinnspannen, während Hersteller, die ihre Produkte in Europa verkaufen, ihre Geschäfte aber in der Regel in US-Dollar abwickeln, erhebliche Umsatzeinbußen hinnehmen müssen. Letztlich wirkt sich dies auf die Erträge aus, was zu Änderungen bei einer Reihe von Investitionsplänen führen kann, die die Hersteller für das Wachstum ihrer Unternehmen haben.
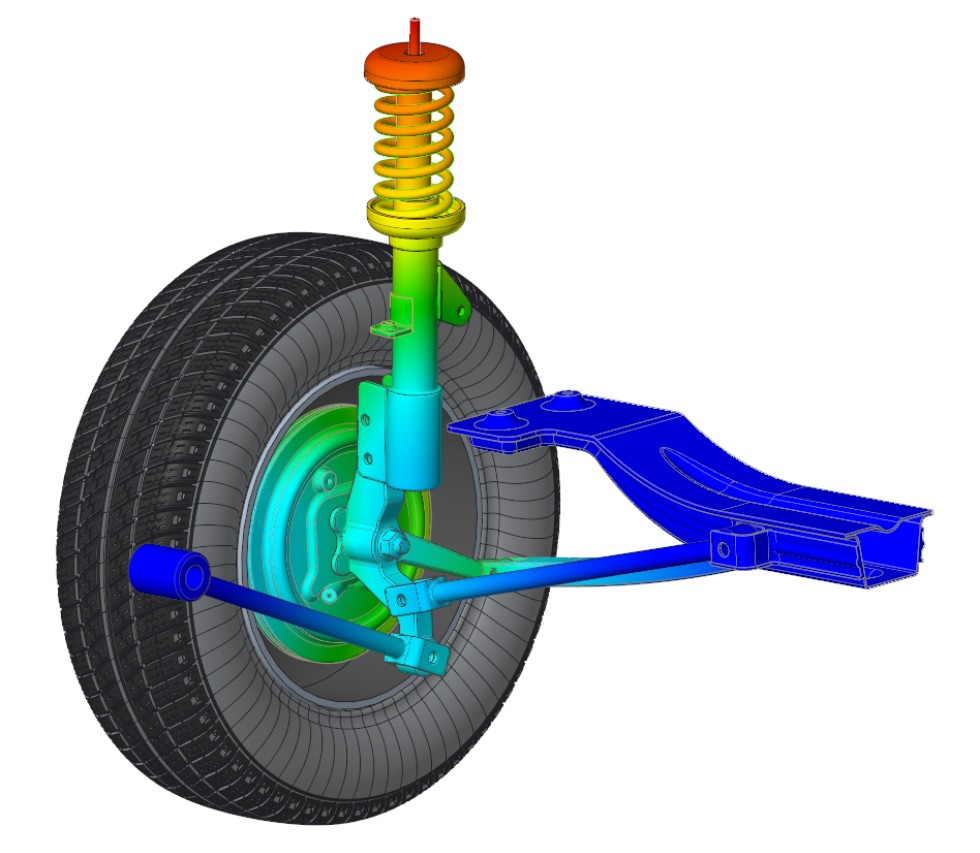
Echtzeit-Konstruktionsunterstützung mit Creo Simulation Live – Strukturspannungsanalyse eines Rades, einer Aufhängung und von Pleuelstangen.
Foto: PTC
In Verbindung mit anderen makropolitischen Herausforderungen führen diese beiden Trends zu Unsicherheit über die wirtschaftlichen Aussichten für 2023. Während diese Welle der Unsicherheit zwangsläufig den gesamten Markt beeinflussen wird, sind Unternehmen und mittelständische Betriebe besser mit den Ressourcen ausgestattet, um das Risiko aufzufangen. Diese Unternehmen wissen, dass sie während des Abschwungs weiter investieren müssen, wenn sie vom unvermeidlichen Aufschwung profitieren wollen. Tatsächlich haben die großen und mittleren Unternehmen ihre Ausgaben für die Produktentwicklung während der COVID-19-Pandemie weitgehend beibehalten oder sogar erhöht. Kleinere Unternehmen haben in der Regel geringere Gewinnspannen, ein geringeres finanzielles Polster und weniger Möglichkeiten, die vorgelagerten Kosten zu beeinflussen, so dass sie in dieser Zeit mit zusätzlichen Ausgaben sehr viel vorsichtiger waren. Sollten sich diese Makrotrends fortsetzen, würden wir erwarten, dass kleinere Unternehmen im Jahr 2023 weniger ausgeben werden.
Für das Jahr 2023 sehen wir fünf Haupttrends in der Produktentwicklung:
- Einführung von simulationsgestütztem Design
- Innovation mit aufstrebenden Techniken ermöglichen
- Den digitalen Faden durch den Designprozess ziehen
- Die Vorteile von Cloud Computing und SaaS nutzen
- In die Ausbildung investieren
Trend 1: Einführung von simulationsgestütztem Design
Im Jahr 2023 erwarten wir eine anhaltende Dynamik für simulationsgetriebenes Design (SDD) auf dem Markt. Anstatt die Simulationstechnik primär am Ende des Entwurfsprozesses einzusetzen, erwarten wir eine kontinuierliche Ausweitung durch Designer und Ingenieure während des gesamten Entwurfsprozesses. Diese „Linksverschiebung“ positioniert die Simulation strategisch an der frühesten praktischen Stelle des Produktentwicklungsprozesses. Auf diese Weise können Unternehmen qualitativ hochwertigere Entwürfe erstellen und die Kosten besser kontrollieren, da sie früher im Entwurfsprozess fundierte Entscheidungen treffen können. Darüber hinaus ermöglicht es mehr Innovation, da die Unternehmen mit Hilfe digitaler Tests viel mehr potenzielle Entwürfe untersuchen können. Es ist diese verlockende Kombination aus qualitativ hochwertigeren, innovativeren und kostengünstigeren Entwürfen in Verbindung mit neueren benutzerfreundlichen Technologien wie der Echtzeitsimulation, die die Einführung von SDD beschleunigt.
Unternehmen wollen schon seit Jahren SDD-Praktiken einführen, aber unzusammenhängende Werkzeuge und nicht funktionierende Prozesse haben diese Bemühungen zunichte gemacht. Die Ausweitung des Einsatzes von Simulationswerkzeugen ist immer noch eine Prozessänderung, die wie jede andere Änderung Arbeit und Engagement erfordert. Die Einführung von Simulationstechniken, die direkt in die CAD-Tools integriert sind, mit denen Konstrukteure und Ingenieure bereits arbeiten, beseitigt das größte Hindernis für die Einführung. Konstrukteure und Ingenieure können jetzt Simulationswerkzeuge sowohl mit dem nativen CAD-Modell als auch innerhalb ihrer aktuellen Konstruktionsprozesse verwenden. Es ist diese tiefe Integration, die den digitalen Faden ermöglicht. Durch diese Integration werden Änderungen und Aktualisierungen, die während des SDD vorgenommen werden, sofort in den Aufzeichnungen des digitalen Threads wiedergegeben. Dies ist besonders wichtig, da es die Autorität der „Single Source of Truth“ über die gesamte Wertschöpfungskette hinweg stärkt und so Konsistenz durch die Vermeidung von Fehlern und Effizienz durch die Reduzierung der Prozesszykluszeiten gewährleistet.
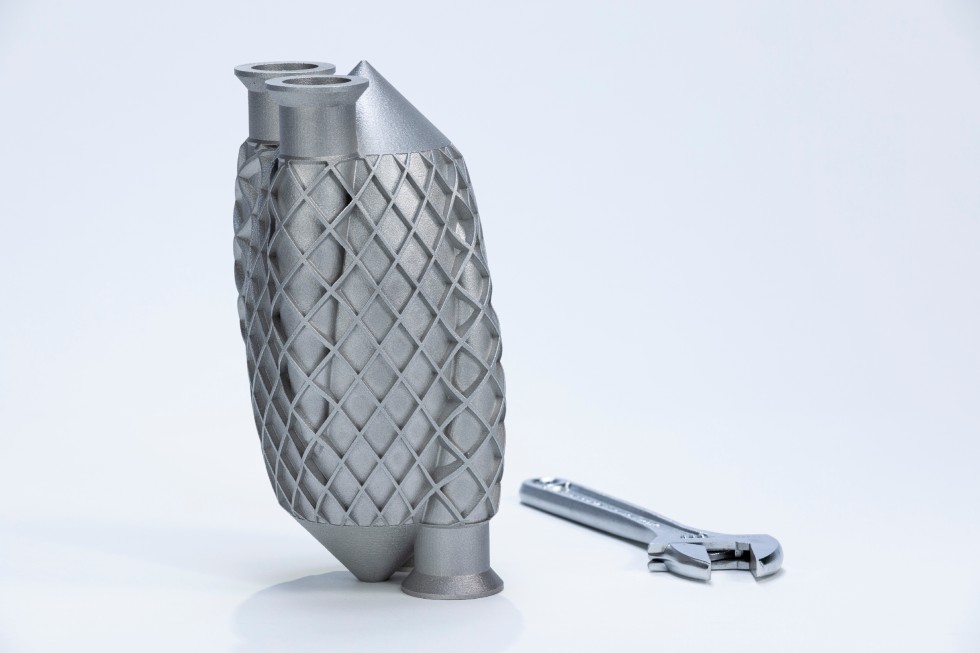
Ein Wärmeübertrager für die Luftfahrt, der mithilfe von additivem Metalldruck und selbsttragenden Gyroid-Gittern hergestellt wird. Das Design bietet eine höhere strukturelle Festigkeit, eine bessere Leistung und ein halb so großes Volumen wie das ursprüngliche Design.
Foto: PTC
Infolgedessen sehen wir einen kontinuierlichen Zuwachs an neuen Kunden, die diese Techniken erwerben, und, was noch wichtiger ist, eine breitere Akzeptanz und Expansion innerhalb bestehender Kunden bei großen und kleinen Unternehmen. Die Unternehmen profitieren von einer größeren Flexibilität, da sie ihre Entwürfe schnell validieren und weiterentwickeln, die Qualität verbessern, die Markteinführung beschleunigen und mit größerem Vertrauen entwerfen können. Außerdem erforschen die Kunden mit Hilfe der Simulationstechnik ein breiteres Spektrum an Designkonzepten als mit kostspieligen Prototypen, was die Wahrscheinlichkeit erhöht, dass sie optimalere Produkte liefern.
Trend 2: Innovation mit neuen Techniken ermöglichen
Neue Designtechnologien wie generatives Design und additive Fertigung treiben die Innovation in der Produktentwicklung voran. Diese Technologien erweitern den potenziellen Lösungsraum für die Erreichung bestimmter Designziele erheblich. Kurz gesagt, der Bereich der Möglichkeiten ist breiter, die Kunst des Möglichen ist größer. Während viele größere Unternehmen experimentieren und diese neuen Technologien in ihre Arbeitsabläufe integrieren, sind es die kleineren, wendigeren Unternehmen, die den Weg vorgeben.
Generative Design-Algorithmen sind unvoreingenommen – unbelastet vom menschlichen Denkprozess. Die Benutzer definieren das Designproblem, und die Engine ermittelt eine Reihe optimaler Lösungen, oft viele, die kein Mensch finden würde. So kann in wenigen Stunden oder Tagen erreicht werden, wofür Designer Wochen oder Monate brauchen würden – vorausgesetzt, sie hätten überhaupt die Zeit und das Budget, so viele Optionen zu prüfen. Durch die Verlagerung des Schwerpunkts von der Geometrieerstellung auf eine bessere Definition des Problems ermöglicht die generative Technik den Ingenieuren, sich auf das zu konzentrieren, was sie am besten können – das Konstruieren. Durch die tiefe Integration dieser Technik in das CAD-Werkzeug und die Verwendung des nativen CAD-Modells können Ingenieure generativ entwickelte Entwürfe in ihre bestehenden Entwürfe einbauen. So entsteht ein agiler Prozess, der die Vorteile des parametrischen CAD voll ausschöpft. Dies macht generatives Design zu einem Motor für bedeutende Innovationen und nicht zu einer halbwegs nützlichen Punktlösung, die vom restlichen Prozess abgekoppelt ist.
Die additive Fertigung ermöglicht es Unternehmen, einzigartige Designs zu entwickeln, die mit anderen Fertigungstechniken nicht realisierbar sind. In den letzten zehn Jahren hat dieses Potenzial viele Unternehmen dazu gebracht, mit der additiven Fertigung zu experimentieren und erstaunliche Ergebnisse zu erzielen. Im Fall von Advanced Engineering Solutions hat das Unternehmen das Design für den Ersatzwärmetauscher eines Hubschraubers optimiert. Mithilfe von Gitterstrukturen, die nur mit Hilfe der Additivtechnologie hergestellt werden konnten, wurde der Wärmetauscher so konstruiert und gefertigt, dass er nur halb so groß wie das Original ist und gleichzeitig die vierfache Kühlleistung erbringt. Dieser Anwendungsfall ist die Art von Innovation, die immer mehr Kunden dazu veranlasst, Werkzeuge für das Design für die additive Fertigung direkt in ihren Designprozess zu integrieren. Ähnlich wie beim generativen Design unterbricht eine Punktlösung den digitalen Faden, was die Konstrukteure daran hindert, die Vorteile des nativen CAD-Modells zu nutzen, und einen erheblichen Mehraufwand verursacht.
Um wirklich innovativ zu sein, müssen die Benutzer im nativen CAD-Modell arbeiten, mit Techniken, die vollständig in ihre bestehenden Arbeitsabläufe integriert sind. Konstrukteure wollen die gleichen hochpräzisen Ergebnisse und ausgefeilten Beziehungen zwischen allen Aspekten ihres Entwurfs erhalten, unabhängig von der Herkunft der Geometrie oder der beabsichtigten Fertigungstechnik. Ohne Integration sind die Konstrukteure mit einer unterbrochenen Werkzeugkette konfrontiert und können die Vorteile und die Leistungsfähigkeit des parametrischen CAD nicht voll ausschöpfen. In der Integration liegt die Chance zur Innovation. Echte Innovation nutzt die Vorteile der besten Technik für die jeweilige Konstruktionsaufgabe, und zwar für alle Teile des Entwurfs, ohne die funktionelle Interaktion zwischen den verschiedenen Teilen zu beeinträchtigen.
Trend 3: Den digitalen Faden durch den Designprozess ziehen
Seit Jahren sind sich die Unternehmen des Wertes eines modellbasierten Unternehmens bewusst, indem sie die Verwendung von CAD-Modellen im gesamten Unternehmen ausweiten. Ziel ist es, die Effizienz zu steigern und Fehler zu vermeiden, indem ein digitaler Faden zwischen den Funktionen und im gesamten Unternehmen geschaffen wird.
Was ist der digitale Faden? Ein digitaler Faden schafft einen geschlossenen Kreislauf zwischen der digitalen und der physischen Welt, um Produkte, Menschen, Prozesse und Orte zu optimieren. Es ist eine Möglichkeit, universellen Zugang zu Daten zu schaffen – eine einzige Quelle der Wahrheit. Wenn er in einer gesamten Wertschöpfungskette implementiert wird, kann er Konsistenz schaffen und die Zusammenarbeit fördern, indem verschiedene Funktionen auf einen robusten Datensatz ausgerichtet werden. Der Datensatz wird durch eine Echtzeit-Datensynchronisation ermöglicht, so dass vor- und nachgelagerte Informationen für alle Benutzer verfügbar sind.
Heutzutage verwenden die meisten Unternehmen nach wie vor mehrere, nicht miteinander verbundene Werkzeuge für den Entwurfsprozess. Dadurch wird die digitale Werkzeugkette unterbrochen, was die Flexibilität und Effizienz beeinträchtigt und gleichzeitig eine Vielzahl von Fehlermöglichkeiten mit sich bringt. Angesichts des zunehmenden Wettbewerbs und der anhaltenden Lieferschwierigkeiten müssen Unternehmen Wege finden, um bessere Produkte schneller und zu geringeren Kosten auf den Markt zu bringen. Sie erkennen die Vorteile, die sich ergeben, wenn sie einen digitalen Faden durch den Produktentwicklungsprozess ziehen, um den vollen Wert des 3D-CAD-Modells zu nutzen. Indem sie den digitalen Faden durch den Produktentwicklungsprozess ziehen, eliminieren die Kunden effektiv die Datenübergabe zwischen unterschiedlichen Tools. Datenübertragungen kosten Zeit und Energie und bergen Fehlerquellen. Wenn ein Benutzer einmal das System wechselt, muss er es wieder tun. Und wenn er dies tut, ist der digitale Faden unterbrochen, was manuelle, unzusammenhängende Nacharbeiten erforderlich macht. Mehr denn je sehen wir Kunden, die vollständig assoziative Ergebnisse erstellen, die sowohl wiederverwendbar als auch leicht zu aktualisieren sind, wenn sich das Design weiterentwickelt.
Ein Hauptbeispiel für diesen wachsenden Trend ist die Auslagerung von Fertigungsergebnissen aus dem CAD-System, wodurch Punktlösungen für Elemente wie z. B. Bearbeitungswerkzeugpfade eliminiert werden. Wie bei den Herausforderungen, die sich aus der Trennung von Werkzeugen in der Konstruktion ergeben, führt diese Trennung zu unnötigen Reibungsverlusten, insbesondere wenn sich die Konstruktionen weiterentwickeln. Indem die Unternehmen diese Daten aus dem CAD-Tool beziehen, beseitigen sie einen Reibungspunkt, erhalten assoziative Verknüpfungen und vermeiden unnötige Datenübertragungen. Auf diese Weise wird zum Beispiel die Zeit verkürzt, die benötigt wird, um Teile für die Bearbeitung in der Fabrik bereitzustellen, und gleichzeitig werden Fehlerquellen eliminiert.
Trend 4: Die Vorteile von Cloud Computing und SaaS nutzen
Im Jahr 2023 werden schätzungsweise 50 % aller Ausgaben für Unternehmensanwendungen auf SaaS-Anwendungen entfallen. Da Unternehmen weiterhin in SaaS und die Cloud investieren, erwarten sie, dass die Softwareanbieter auch in Funktionen investieren, die die Vorteile von SaaS und der Cloud nutzen. Design-Software ist keine Ausnahme von diesem Trend, und der erste Bereich, in dem Änderungen zu erwarten sind, ist die Lizenzierung und Bereitstellung. Stellen Sie sich vor, Sie könnten alle Benutzerrechte verwalten und die Software für das gesamte Unternehmen unabhängig vom Standort bequem von Ihrem Schreibtisch aus über ein einfaches Webportal bereitstellen. Für große Unternehmen bedeutet dies eine erhebliche Zeitersparnis und eine Verringerung der Komplexität bei gleichzeitig größerer Kontrolle.
Ein weiterer Bereich, in dem wir erhebliche Verbesserungen erwarten, ist die Zusammenarbeit. Indem wir die Leistungsfähigkeit der Cloud in die Konstruktionssoftware einbeziehen, können mehrere Benutzer gleichzeitig in einer gemeinsamen Umgebung an demselben Entwurf arbeiten. Dadurch wird es auch viel einfacher, das Team für die Zusammenarbeit auf Personen außerhalb des Unternehmens (Lieferanten, Partner usw.) auszudehnen und IP zu kontrollieren.
Der Zugang zu elastischen Rechenressourcen wird auch für Konstruktionswerkzeuge ein großer Vorteil sein. Cloud Computing wird dazu genutzt werden, die Leistungsfähigkeit von Technologien wie dem generativen Design drastisch zu erhöhen. Wir beobachten bereits, dass Unternehmen die Vorteile des Elastic Computing nutzen, um den Entwurfsraum mit generativer Technologie zu erweitern und Hunderte potenzieller Lösungen in der Zeit zu untersuchen, die normalerweise für die Untersuchung einer einzigen Lösung benötigt wird. Und schließlich erhalten Kunden, die auf SaaS umsteigen, automatisch und regelmäßig Zugang zu neuen Funktionen und müssen sich nie wieder Gedanken über die Planung eines Versions-Upgrades machen.
Trend 5: Investitionen in die Ausbildung
Der letzte Trend, den wir für das Jahr 2023 sehen, besteht schon seit langem: die Weiterbildung. Wir beobachten ein Wiederaufleben der Ausbildung, da sich mehr Unternehmen darauf konzentrieren, den digitalen Faden durch die Wertschöpfungskette zu ziehen. Die Notwendigkeit, qualitativ hochwertige, direkt herstellbare 3D-Modelle zu produzieren, zwingt die Unternehmen dazu, sich auf gute Modellierungsverfahren zu konzentrieren.
Durch die Einführung und Nutzung bewährter Praktiken in den Teams durch effektive Schulungen werden auch die Wiederverwendung von Entwürfen und die Zusammenarbeit effizienter. Konstrukteure wollen bestehende Entwürfe wiederverwenden, da sie dadurch Zeit und Energie sparen. Wenn jedoch die Modellierungsverfahren, die zur Erstellung dieser Entwürfe verwendet wurden, fehlerhaft oder für den nächsten Konstrukteur unverständlich sind, dann ist ihre Wiederverwendung deutlich weniger wertvoll.
Eine weitere Herausforderung, die immer mehr Unternehmen dazu veranlasst, in die Ausbildung zu investieren, ist der zunehmende Mangel an technischen Fachkräften. Es gibt sogar Prognosen, dass bis 2030 weltweit Millionen von Ingenieuren fehlen werden. Unternehmen, unabhängig von ihrer Größe, spüren den Mangel bereits und haben erkannt, dass sie ihre Konstrukteure so effektiv wie möglich machen müssen. Der Wettbewerb um Ingenieurtalente stellt die Unternehmen auch vor die Herausforderung, Mitarbeiter zu halten. Konstrukteure, die ihre Marktfähigkeit verbessern wollen, wechseln den Arbeitsplatz, um Zugang zu Schulungen und Zertifizierungen zu erhalten. Umgekehrt schreiben einige Unternehmen den Abschluss von Zertifizierungen vor, um ihre Glaubwürdigkeit zu gewährleisten und ihre Zuverlässigkeit gegenüber den Kunden zu demonstrieren.
Schlussfolgerung
Aufgrund dieser Faktoren wird die Ausbildung im Jahr 2023 doppelt so wichtig sein. Gut ausgebildete Konstrukteure, die gemeinsame Prozesse nutzen, werden Verwirrung beseitigen, Konstruktionswiederholungen beschleunigen, die Qualität verbessern und ein höheres Maß an Zusammenarbeit und Innovation fördern. Letztendlich wollen Unternehmen effizientere, produktivere Ingenieure, die qualitativ hochwertige, direkt herstellbare Entwürfe erstellen, die in der gesamten Wertschöpfungskette wiederverwendbar und assoziativ sind. Sie wollen, dass diese Entwürfe während des gesamten Produktentwicklungsprozesses mit integrierter Simulationstechnologie digital getestet werden. Natürlich sollen diese Entwürfe die neuesten additiven Fertigungs- und generativen Techniken nutzen, wo dies sinnvoll ist. Selbst wenn diese fortschrittlichen Technologien tief in die CAD-Umgebung integriert sind, ist eine grundlegende Schulung zu ihrer Anwendung der bei weitem effizienteste Weg zu voller Produktivität. So erhalten Ingenieure und Designer das Wissen und die Ressourcen, die sie brauchen, um den digitalen Faden nicht zu verlieren.
Auch interessant: