Entwicklung neuer Magnesiumbleche für die Automobilindustrie
Während in einer Vielzahl von Anwendungen in Form von Gussteilen das hohe Leichtbaupotenzial von Magnesium im Automobil hinreichend bewiesen ist, beschränken sich Blechbauteile auf sehr wenige Nischen. Zwei wesentliche Gründe für die zögerliche Nutzung des Leichtmetalls in Blechbauteilen sind zum einen der Preis für das Halbzeug, zum anderen aber auch limitierte werkstoffliche Eigenschaften bekannter Legierungen, die einen Herstellprozess automobiler Bauteile deutlich verkomplizieren. Während durch das Gießwalzverfahren wesentliche Fortschritte in der wirtschaftlichen Herstellung von Magnesium- Blechen in den vergangenen Jahren erreicht wurden, bleibt die Auswahl an verfügbaren Legierungen dünn. An letzterem Umstand setzt ein Konsortium zwischen der Volkswagen AG, dem Helmholtz-Zentrum Geesthacht und der Firma Posco an. Mithilfe von gezielter Legierungsentwicklung kann gezeigt werden, wie verbesserte Werkstoffeigenschaften zu einer vereinfachten Produktion automobiler Bauteile führen.
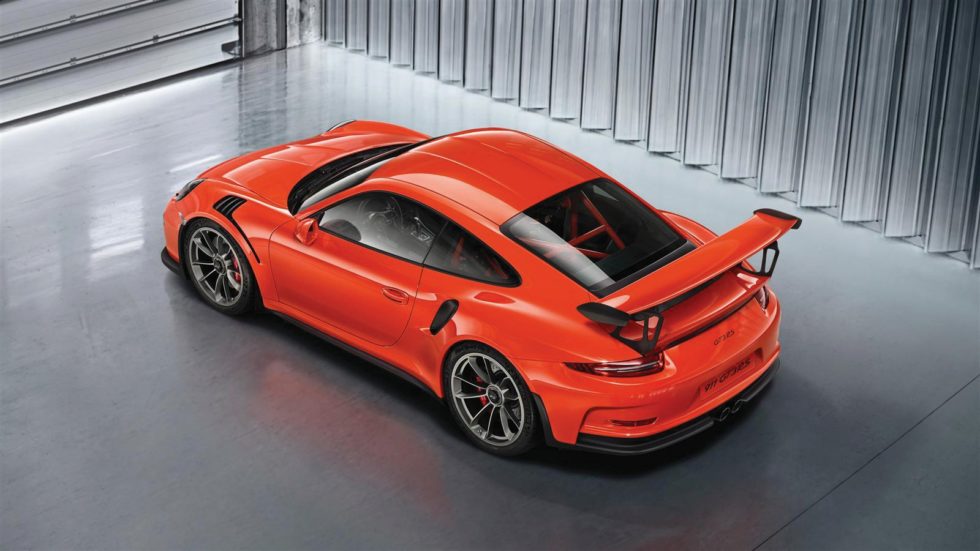
Die Nutzung von Magnesium für leichte Bauteile in der Automobilindustrie kennt in der Vergangenheit und in der Gegenwart viele Beispiele. So wurden schon der luftgekühlte Motorblock und die Getriebegehäuse des Volkswagen Käfers aus Magnesium gefertigt. Prominente Magnesiumanwendungen in heutigen Fahrzeugen sind Lenkradskelette, Getriebe- und Kupplungsgehäuse sowie in wenigen Fällen Klappeninnenteile (Bild 1). Bei diesen Anwendungen handelt es sich fast ausschließlich um Bauteile, die im Druckgussverfahren hergestellt werden. Serienanwendungen von Blechbauteilen beschränken sich jedoch nur auf wenige Nischen. So besteht zum Beispiel das Dach des aktuellen Porsche 911 GT3 RS aus Magnesium-Blech – die weltweit erste Anwendung von Magnesium in der Außenhaut (Bild 1). Einer der wesentlichen Gründe für die zögerliche Verwendung des Werkstoffs als Blech ist der Umstand, dass sowohl die Herstellung des Halbzeugs als auch der Bauteile nur mit hohem finanziellen Aufwand machbar sind.
Paradigmenwechsel
Bei der Herstellung von Magnesium-Blechen hat in den vergangenen zehn Jahren ein Paradigmenwechsel stattgefunden. Das aufwendige Brammenwalzverfahren, das bei Magnesium aufgrund der Notwendigkeit des Warmwalzens bis zum letzten Stich kostenintensiv ist, ist durch das Gießwalzverfahren ergänzt worden. Im Gießwalzverfahren kann durch das Injizieren der Metallschmelze in den Walzspalt direkt ein coilbares Band von etwa 5 mm Dicke hergestellt werden, sodass die Prozesskette deutlich verkürzt werden kann. Die Kostenersparnis liegt bei etwa 60 %, sodass der Werkstoff nun in einem besseren Kostenverhältnis zu Aluminium zu bewerten ist. Ein in diesem Kontext für die Automobilindustrie wichtiger Schritt war die Skalierung des Verfahrens auf bis zu 2000 mm Blechbreite durch die Firma Posco im Jahr 2012, sodass auch große automobile Bauteile nun darstellbar sind.
Ein zwingend notwendiger weiterer Schritt in Richtung wirtschaftlicher Magnesium-Blechbauteile ist die Vereinfachung der Prozesskette der Weiterverarbeitung des Blechs in der Automobilfabrik. Es ist klar, dass dieser Schritt nur über eine konsequente Weiterentwicklung und Verbesserung der werkstofflichen Eigenschaften zu erreichen ist. Um dieses Ziel zu erfüllen, hat sich Volkswagen mit dem Helmholtz-Zentrum Geesthacht und Posco zusammengeschlossen. Vorteil dieses Konsortiums ist, dass ein Bogen von der Erforschung der werkstofflichen Grundlagen über die großskalige, industrielle Herstellung des Blechs mittels Gießwalzens hin zum Aufbau automobiler Prototypen gespannt werden kann.
Textur-Design
Der anfängliche Fokus der Legierungsentwicklungsarbeit lag auf der Verbesserung der Umformbarkeit von Magnesium-Blechen. Konventionelle Bleche, wie zum Beispiel die gängige Mg-Al-Zn-Legierung AZ31, zeigen nur bei Temperaturen oberhalb von 220 °C ein gutes Umformvermögen. Die mit der Warmumformung verbundene Werkzeugbeheizung sowie die Limitation in verfügbaren Hochtemperaturschmierstoffen als auch die Komplexität der Temperaturführung in einem Serienumformprozess führen zu zusätzlichen Kosten, die es zu reduzieren gilt. Bei der Legierungsentwicklungsstrategie ist es wichtig zu bemerken, dass die limitierte Umformbarkeit der konventionellen Legierung AZ31 nicht nur aus der hexagonalen Kristallstruktur herrührt, sondern auch durch eine starke basale Textur beschränkt wird, das heißt der bevorzugten Ausrichtung der Körner mit der basalen Ebene parallel zur Blechebene. Eine starke basale Textur führt zu dem Umstand, dass Dehnung in Blechdickenrichtung nur vermindert aufgenommen werden kann, wodurch die Herstellung komplexer Bauteilgeometrien deutlich eingeschränkt ist. Im Umkehrschluss gilt, dass durch ein Aufbrechen der starken basalen Textur, das heißt mittels „Textur-Design“, die Umformbarkeit von Magnesium-Blechen gesteigert werden kann. Genau an diesem Punkt setzt die innerhalb des Konsortiums entwickelte neue Legierung aus Magnesium, Zink und Kalzium auf Basis des Gießwalzverfahrens an. Durch die Zugabe von geringen Mengen an Kalzium in einer Magnesium-Zink-Legierung konnte nachgewiesen werden, dass die Orientierung der einzelnen Körner weitaus regelloser erfolgt als in der Vergleichslegierung AZ31 (Bild 2). Dies bedeutet, dass mehr Körner mit der basalen Ebene außerhalb der Blechebene liegen, sodass eine Aufnahme der Dehnung in Blechdicke einfacher erfolgen kann. Dieser Effekt wird insbesondere in der Streckziehbarkeit bei Raumtemperatur, gemessen mithilfe der Erichsen Tiefung, deutlich. Bild 3 zeigt den Vergleich der Streckziehbarkeit unterschiedlicher Blechwerkstoffe. Anhand des sogenannten Erichsen-Index weist die neue Magnesium-Zink-Kalzium-Legierung gegenüber AZ31 mehr als eine Verdopplung des Umformvermögens auf, sodass sie sich nun zwischen den 6000er und 7000er Aluminium-Legierungen einordnet.
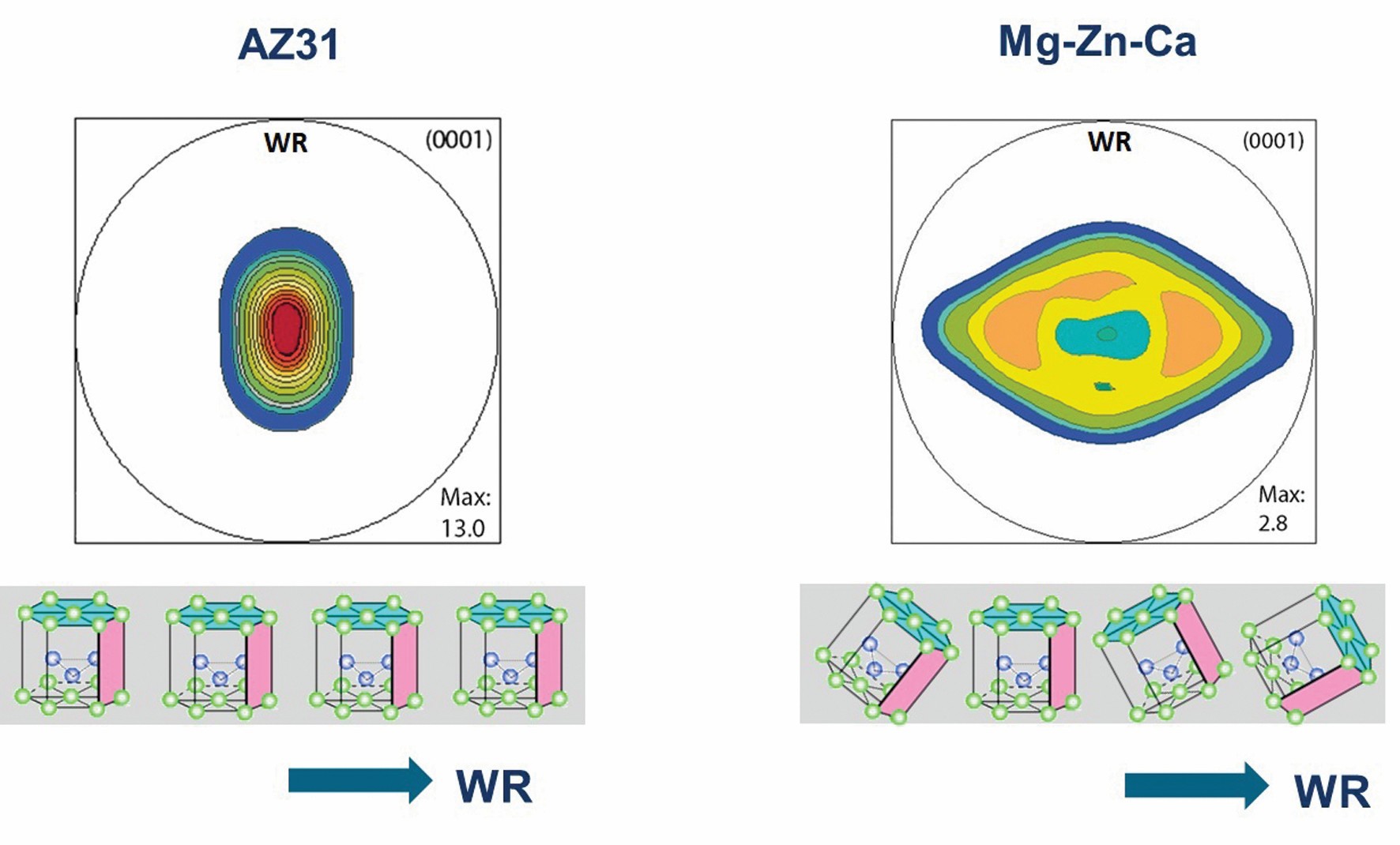
Bild 2: Texturvergleich der konventionellen Legierung AZ31 (links) mit der neuen Mg-Zn-Ca-Legierung (rechts). Die Texturabschwächung führt bei der Mg-Zn-Ca-Legierung zu einem Drehen der basalen Ebenen (türkis) aus der Blechebene (WR: Walzrichtung). Dies steigert das Umformvermögen. Bild: Volkswagen AG

Bild 3: Vergleich der Streckziehbarkeit unterschiedlicher Blechwerkstoffe anhand der Erichsen-Tiefung. Die neue Legierung Mg-Zn-Ca besitzt eine mehr als verdoppelte Streckziehbarkeit im Vergleich zur konventionellen AZ31. Bild: Volkswagen AG
Erprobung der neuen Legierung
Die Herstellung der neuen Legierung auf Grundlage der Gießwalztechnik wurde in mehreren Schritten sukzessive erprobt und optimiert. Hierzu wurden unterschiedliche Anlagen sowohl in den Laboratorien des Helmholtz-Zentrums Geesthacht als auch in der industriellen Fertigung bei Posco verwendet. Im Ergebnis konnte nachgewiesen werden, dass die Legierung prozesssicher in Mengen über 10 t und auf Breiten bis zu 2000 mm industriell herstellbar ist. Ein wesentlicher Vorteil der Legierung beruht auf der Tatsache, dass die Tendenz der Ausbildung von Seigerungen aufgrund einer sehr geringen Zusammensetzung, das heißt Legierungselementzugaben jeweils unter 1,5 Gew.-%, stark vermindert wird, sodass die Herstellung von homogenem Material deutlich einfacher erfolgen kann.
Um die Vorteile der Legierung auf Bauteilebene in der Automobilindustrie auszuloben, wurde ein Heckdeckel auf Basis des aktuellen Passat B8 magnesiumgerecht konstruiert. Für die Berechnung wurde eine theoretische Vollkonstruktion aus Magnesium angenommen, einschließlich Außen-, Innen- und aller Verstärkungsteile (Bild 4).

Bild 4: Vergleich der Gewichte einer Heckklappe des Passat B8 durch Materialsubstitution. Eine Konstruktion aus Magnesium-Blech mit den rechts dargestellten Blechdicken liefert eine Gewichtsersparnis von 6,3 kg (52 %) im Vergleich zur Stahl-Serie. Bild: Volkswagen AG
Die Auslegung beweist das Leichtbaupotenzial von Magnesium: Im Vergleich zur Serienvariante aus Stahl liegt die Gewichtsersparnis bei 6,3 kg (-52 %) und im Fall einer äquivalenten Konstruktion aus Aluminium bei 1,8 kg (-24 %) (Bild 4). Um die Anforderungen hinsichtlich Steifigkeit zu erfüllen, sind für das Außen- und das Innenteil Blechdicken von 1,2 mm und 1,4 mm notwendig. Weitere Änderungen umfassten ausgehend von der Stahl-Seriengeometrie die Entschärfungen von wenigen Radien, um eine Herstellbarkeit in Magnesium zu gewährleisten.
Unter Verwendung der bei Posco hergestellten Bleche wurden am Beispiel des Innenblechs Umformversuche durchgeführt. Das Ergebnis ist in Bild 5 dargestellt.

Bild 5: Umgeformtes Mg-Innenblech der Passat B8 Heckklappe. Durch Legierungsentwicklung konnte die Umformtemperatur auf 160 °C reduziert werden. Bild: Volkswagen AG
Es konnte gezeigt werden, dass mit der neuen Magnesium-Zink-Kalzium-Legierung die Umformtemperaturen von über 220 °C für konventionelles Magnesium-Blech AZ31 auf 160 °C reduziert werden konnten. Als Konsequenz bedeutet dies, dass neben der Einsparung von Energie eine größere Bandbreite von Schmiermitteln zur Verfügung steht und in einem Serienumformprozess die Temperaturführung deutlich vereinfacht wird. Diese Schritte liefern die Grundlage, die Kosten einer Serienfertigung von Magnesium-Bauteilen zu senken und begründen damit die Motivation, den Werkstoff in seinen Eigenschaften substantiell weiterzuentwickeln. Nur mithilfe dieses Entwicklungsprozesses, der analog zu der hier beschriebenen Arbeit weitergeführt werden sollte, wird es möglich sein, einen zu Aluminium-Blechen konkurrenzfähigen Leichtbauwerkstoff zu entwickeln.
Ausblick
Neben der Verbesserung der Umformbarkeit, die in dem hier beschriebenen Legierungsentwicklungsprojekt erzielt wurde, existiert Bedarf, den Werkstoff Magnesium-Blech auch in anderen Aspekten weiterzuentwickeln. Im direkten Vergleich zu Aluminium sind hier in erster Linie die Korrosionsresistenz und die mögliche Aushärtbarkeit zu betrachten. Erste fundamentale Studien der Volkswagen AG, des Helmholtz-Zentrums Geesthacht und der Firma Posco zeigen, dass auch in diesen Bereichen weitreichende Verbesserungen gegenüber der konventionellen Magnesium-Blechlegierung AZ31 erzielt werden können. Dies begründet einen fundierten Optimismus, den Leichtbauwerkstoff Magnesium neben Gussteilen auch für Blechbauteile in Zukunft etablieren zu können.
Dr. David Klaumünzer, Werkstoffingenieur, Konzernforschung, Volkswagen
Dr. Sangbong Yi, Wissenschaftler, MagIC, Helmholtz-Zentrum Geesthacht
Dr. Dietmar Letzig, Wissenschaftler, MagIC, Helmholtz-Zentrum Geesthacht
Sang-hyun Kim Posco, Korea
Dr. Jae Joong Kim Posco, Korea
Kontakt: Volkswagen AG, Berliner Ring 2, 38440 Wolfsburg www.volkswagen.de