Topologieoptimierte Faserverbundstrukturen
Leichtbau ist eine Schlüsseltechnologie, wenn es um Ressourcen- und Energieeffizienz geht. Mit zunehmender Verwendung in massentauglichen Anwendungen steigt der Bedarf nach kostengünstigen Produktionsmethoden. Der vorgestellte Ansatz kombiniert neue Möglichkeiten der additiven Fertigung mit der Produktion von faserverstärkten Sandwichbauteilen. Dadurch wird die Prozesskette verkürzt, der Materialaufwand für Halbzeuge und Werkzeuge reduziert und somit die Herstellung von Leichtbauteilen einen großen Schritt wettbewerbsfähiger.
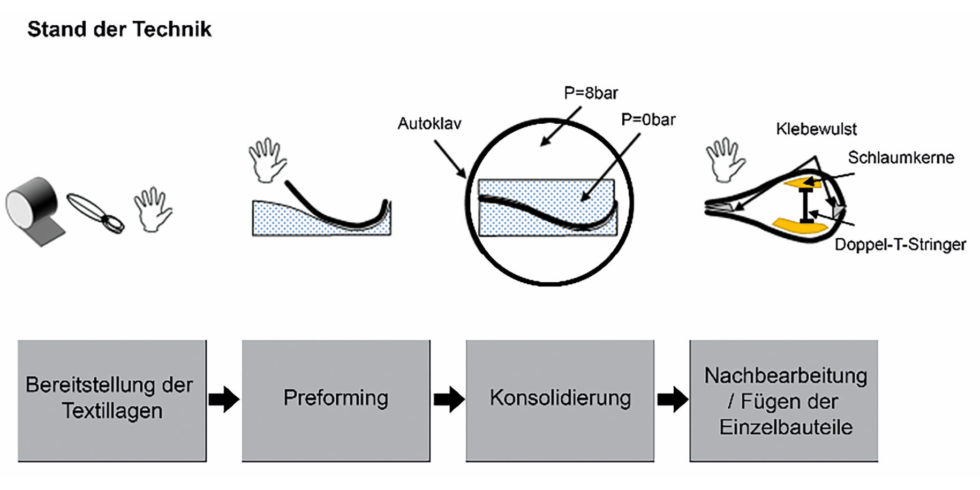
Bild 1a: Prozesskette herkömmliche Bauweise. Bild: RWTH Aachen
Aufgrund der hervorragenden gewichtsbe-zogenen mechanischen Eigenschaften werden faserverstärkte Kunststoffe (FVK) in einer Vielzahl von Anwendungen in unterschiedlichen Branchen (u. a. Luftfahrt und Automotive) eingesetzt. Die größten Herausforderungen für KMU sind hierbei das Einsetzen einer erschwinglichen, effektiven Fertigungsmethode bei maximaler Produktionsflexibilität, sowie die Herstellung komplexer lastpfadgerechter Geometrien. Für eine strukturelle Verstärkung und zur Übertragung von Kräften im Bereich der Luftsportgeräte werden Flügelholmstrukturen aus FVK eingesetzt. Diese weisen eine belastungsgerechte Geometrie auf und sind durch über die Länge variierende Querschnitte gekennzeichnet. Zur Versteifung der Flügelstruktur werden Schaum-/Sandwichkerne integriert (Integralbauweise).
Manuelle Herstellung stößt an Grenzen
Diese werden während der Herstellung der CFK-Schalen in separaten zeitintensiven Prozessschritten manuell appliziert. Die Herstellung dieser Strukturen ist aktuell aufgrund aufwendiger Handhabungsschritte fertigungstechnisch höchst komplex. In der Folge ergibt sich ein hoher Anteil an erforderlicher manueller Arbeit. Die manuelle Arbeit erschwert die Arbeitsplanung, da Fertigungsschritte zunächst angelernt und anschließend eingeübt werden müssen. Durch den Faktor Mensch sind daher Qualität und Zykluszeit abhängig von der ausführenden Person sowie deren Tagesform. Bei kleineren Personenkreisen haben Abwesenheiten wie Krankheit oder Urlaub einen direkten Einfluss auf die Produktionsleistung. Eine kosteneffizientere teil- oder vollautomatisierte Fertigung ist in Deutschland aufgrund der geringeren Flexibilität und hohen Investitionskosten kommerzieller Automatisierungslösungen vor allem für KMU nicht umsetzbar.
Zusammenfassend kann festgehalten werden, dass durch den aktuell erforder-lichen hohen manuellen Arbeitsanteil lange Zykluszeiten, hohe Ausschussraten und dadurch ein erhöhter Kostenaufwand entstehen. Des Weiteren ist fraglich, ob mit einer vorwiegend manuellen Herstellungsweise die steigende Nachfrage (4,7 % Markwachstum p. a.) im Luftfahrtbereich gedeckt werden kann.

Bild 2 Links: Druckversuche bionisch geformter Kerne, rechts: Druckversuche auf Carbontextil. Fotos: ConsiderIT
Komplexe topologieoptimierte Faserverbundstrukturen erzeugen
Ziel des vorgestellten Projektes ist die Entwicklung eines neuen Verfahrens zur Herstellung komplexer topologieoptimierter Faserverbundstrukturen in Integralbauweise. Hierzu werden nach der Auslegung bionische Verstärkungskerne auf vorimprägnierte Halbzeuge (sogenannte Prepregs) additiv gefertigt. Durch den Einsatz additiver Fertigungsverfahren wird es möglich, neuartige bionische Designs von Bauteilen zu fertigen. Die Adaption bionischer Prinzipien für den Leichtbau führt zur Reduktion des Bauteilgewichts und zur Steigerung der mechanischen Eigenschaften. Additiv gefertigte bionische Strukturen können auf den vorliegenden Lastfall ausgelegt werden. Das Bauteilgewicht soll so im Vergleich zum Stand der Technik um mindestens 20 Prozent reduziert werden.
Bionische Strukturen erzeugen
In Versuchen konnte bereits die generelle Bedruckbarkeit von Halbzeugen aus Carbonfasern sowie die Umsetzung von bionischen Strukturen mit Hilfe des 3-D-Druck-Verfahrens nachgewiesen werden. Zur Bauteilfertigung wird eine Prozesskette zur Fertigung von Demon-stratoren entwickelt und umgesetzt. Eine zentrale Bestrebung besteht in der Entwicklung einer kostengünstigen Lösung, die auch für KMU finanzierbar ist. Neben einem geringen Marktpreis steht zudem vor allem die für KMU besonders wichtige Flexibilität im Fokus. Daher soll ein 3-D-Druck-Portal so ausgelegt werden, dass die Versteifungsstrukturen über ein Schienensystem abschnittsweise aufgedruckt werden können.
Mit dem Gesamtsystem sollen Bauteile mit einer Abmessung von bis zu 1 m Breite und 4 m Länge gefertigt werden können. Im Zuge des Projektes wird der Druck von bionischen Kernen für eine Flügelstruktur sowie einen Roboterarm-ausleger verfolgt. Eine Applikation der Schaumstoffkerne sowie weiterer Elemente, wie z. B. Doppel-T-Stringer und das manuelle, fehleranfällige Fügen mit der CFK-Schale via Kleben sind mit dem neuen Verfahren nicht mehr erforderlich.
Danksagung: Das ZIM-Vorhaben ZF4558949PO9 wird im Rahmen des Zentralen Innovationsprogramms Mittelstand vom Bundesministerium für Wirtschaft und Energie aufgrund eines Beschlusses des Deutschen Bundestages gefördert. Wir danken den genannten Institutionen für die Bereitstellung der finanziellen Mittel.

Dr.-Ing. Till Quadflieg, Head of Composite Production
Max Schmidt, Waldemar Biche, Thomas Gries
alle: Institut für Textiltechnik (ITA), RWTH Aachen University, Otto-Blumenthal-Str. 1, 52074 Aachen, Tel.: 02 41 / 80 234 83,
E-Mail: till.quadflieg@ita.rwth-aachen.de, www.ita.rwth-aachen.de
Gianluca Brandino, consider it GmbH, E-Mail: brandino@consider-carbon.com, www.consider-it.de