Ultrahochfeste Aluminiumlegierungen – eine Marktlücke im Fahrzeugbau
Der Automobilmarkt ist hart umkämpft. Während Ansprüche an Leistung, Design, Komfort und Sicherheit steigen, steht auch die Umweltverträglichkeit immer mehr im Fokus. In allen Bereichen wird versucht Gewicht einzusparen – so ist die Herausforderung Leichtbau auch lange schon zu einem Thema für die Materiallieferanten geworden. Insbesondere bei Fahrzeugteilen, von denen eine hohe Festigkeit erwartet wird, hatte Stahl bislang eine Vorreiter-Rolle inne. Durch innovative, ultrahochfeste Aluminiumlegierungen kann sich das nun ändern.
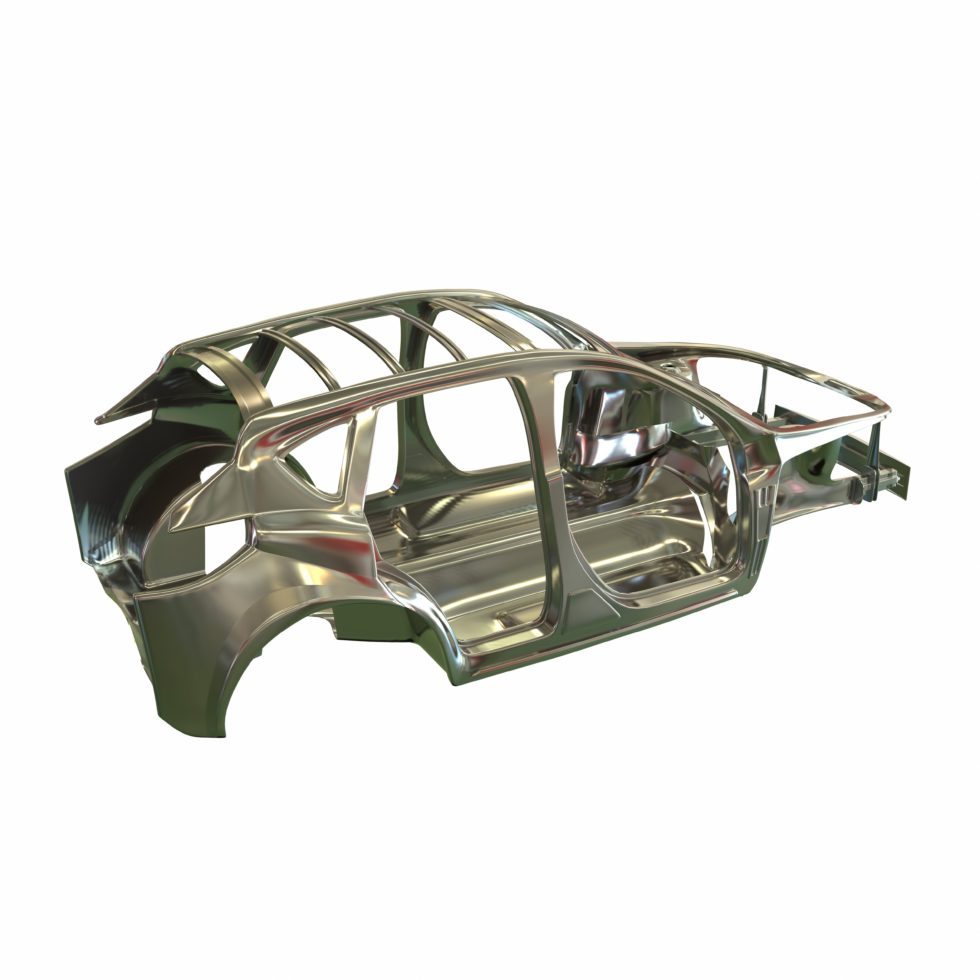
Bild 1 Sicherheitskäfig eines Autos. Bild: Verfasser
Aluminium: Werkstoff der Zukunft
In den letzten Jahren hat sich Stahl als Werkstoff weiterentwickelt. Mit festeren und leichteren Stählen hat die Branche Alternativen geschaffen, die genau die Bedürfnisse der Automobilindustrie treffen. Ultrahochfeste Stähle bieten Festigkeit und Kollisionssicherheit, während gleichzeitig gegenüber herkömmlichen Stählen Gewicht eingespart werden kann. Mit den Aluminiumlegierungen der 6000er-Familie für verschiedenste Einsatzzwecke und mit unterschiedlichen Eigenschaften lässt sich relativ einfach eine Festigkeit von bis zu 400 MPa erreichen. Um im Wettbewerb mit Stahl zu bestehen, hat die Aluminiumindustrie große Bemühungen in die Forschung und Entwicklung investiert – mit konkreten Ergebnissen: Ultrahochfeste Aluminium- legierungen mit einer Streckgrenze von mehr als 400 MPa bieten nun eine echte Alternative zu ultrahochfesten Stählen und ermöglichen dabei aufgrund der geringeren Dichte des Werkstoffes Aluminium gleichzeitig weitere Gewichtseinsparungen.
In enger Kooperation mit Automobilherstellern und Forschungseinrichtungen wie der Université de Toulouse in Frankreich und der University of Manchester in Großbritannien hat Constellium in den letzten Jahren an einer neuen Serie von Aluminiumlegierungen gearbeitet. Die Produktfamilie „Ultralex“ gehört zu den 7000er-Legierungen und besteht aus einer Aluminium-Zink-Magnesium-Kupfer-Legierung. Neben der möglichen Gewichtseinsparung haben ultrahochfeste Alumi- niumlegierungen noch einen weiteren Vorteil: Während immer mehr Fahrzeuge und gleichzeitig auch immer mehr Fahrzeugteile aus Aluminium gefertigt werden, erleichtert die Verwendung von Aluminium auch für besonders beanspruchte Komponenten wie B-Säulenverstärkung oder Fahrzeugdach die Verbindung einzelner Fahrzeugteile. So können Teile aus einer 7000er-Legierung deutlich einfacher in eine Aluminiumstruktur integriert werden, als das bei ultrahochfesten Stählen der Fall ist. Durch die durchgängige Verwendung von Aluminium im Fahrzeugbau wird außerdem das Sortieren von Schrotten und damit das Recycling erleichtert und so die Nachhaltigkeit des gesamten Produkts verbessert.
Ultrahochfeste Aluminium- legierungen: eine Herausforderung
Bei allen Vorteilen sind ultrahochfeste Aluminiumlegierungen eine Herausforderung für materialverarbeitende Unternehmen. So sind sie im Vergleich zu 6000er-Legierungen und ähnlich wie auch ultrahochfeste Stähle etwa schwerer formbar. Eine Möglichkeit, die auch im Stahl-Bereich genutzt wird, ist das Heißprägen und Presshärten. Hierbei wird das Aluminiumgemisch auf etwa 500 Grad erhitzt und anschließend in einem Formwerkzeug sehr rasch abgekühlt und dadurch gehärtet. So entstehen Aluminiumteile mit hoher Festigkeit und Belastbarkeit sowie guten mechanischen Eigenschaften, während gleichzeitig durch die Nutzung eines Formwerkzeugs im Härtevorgang verhindert wird, dass sich das Bauteil beim Abkühlen verzieht. Ein alternatives Verfahren, das mit Aluminiumlegierungen, nicht jedoch mit ultrahochfesten Stählen möglich ist, ist das sogenannte Lösungsglühen mit anschließender Warm-Umformung. Dabei wird das Aluminium abhängig von den enthaltenen Legierungen auf 500 bis 600 Grad erhitzt, sodass sich alle Elemente lösen und sich gleichmäßig im Aluminium verteilen. Man spricht hierbei auch vom Homogenisieren des Mate-rials. Nach dem raschen Abkühlen auf Raumtemperatur wird das Metall erneut auf 200 bis 250 Grad erhitzt und dann warmumgeformt. Dieses zweite Verfahren ist bei Aluminiumlegierungen möglich, bei Borstahl hingegen nicht. Somit wird Automobilherstellern eine Alternative geboten, je nach Komplexität des Bauteils unterschiedliche Möglichkeiten des Formens zu nutzen.
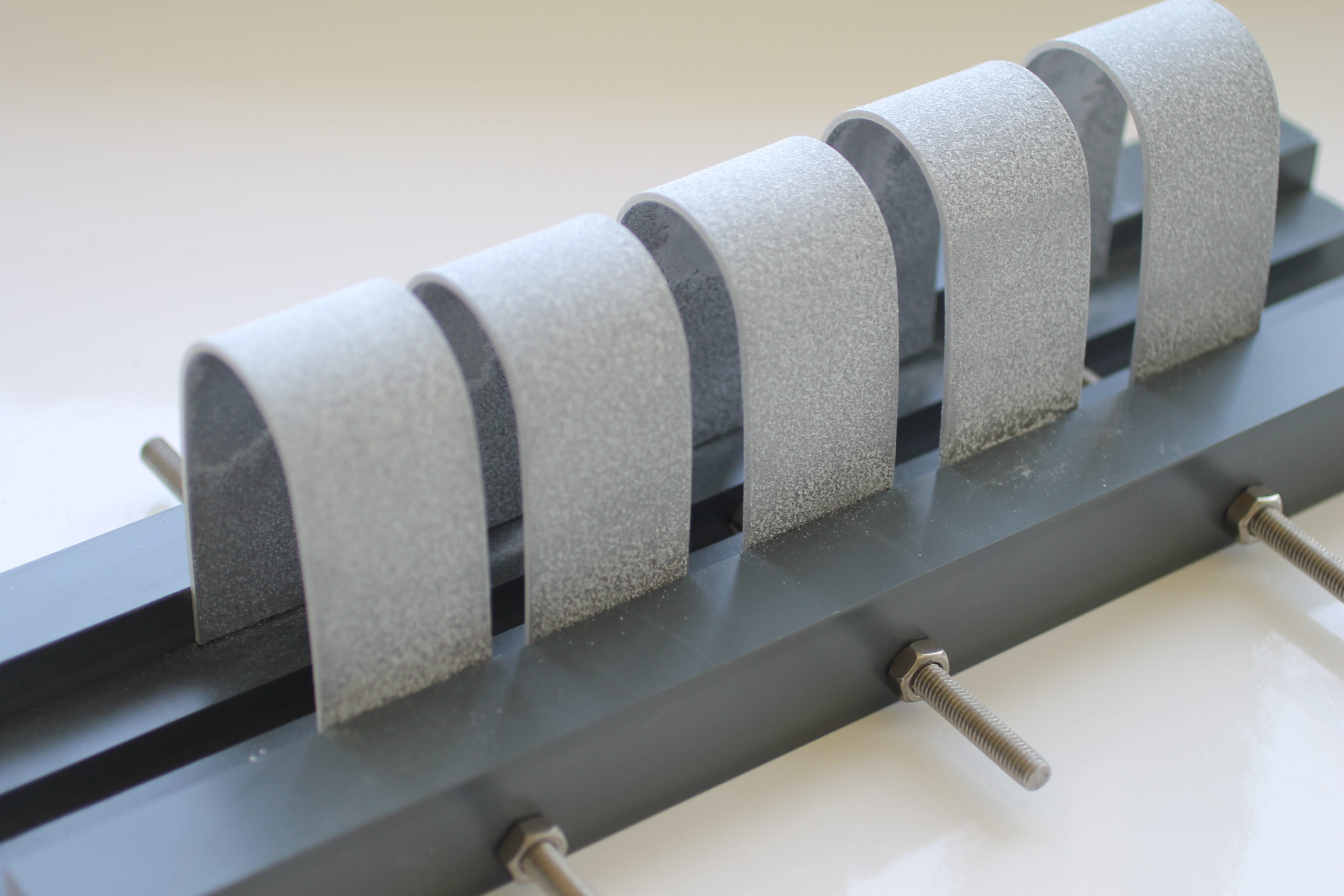
Bild 2 Korrosionstest bei einer 7000er-Legierung
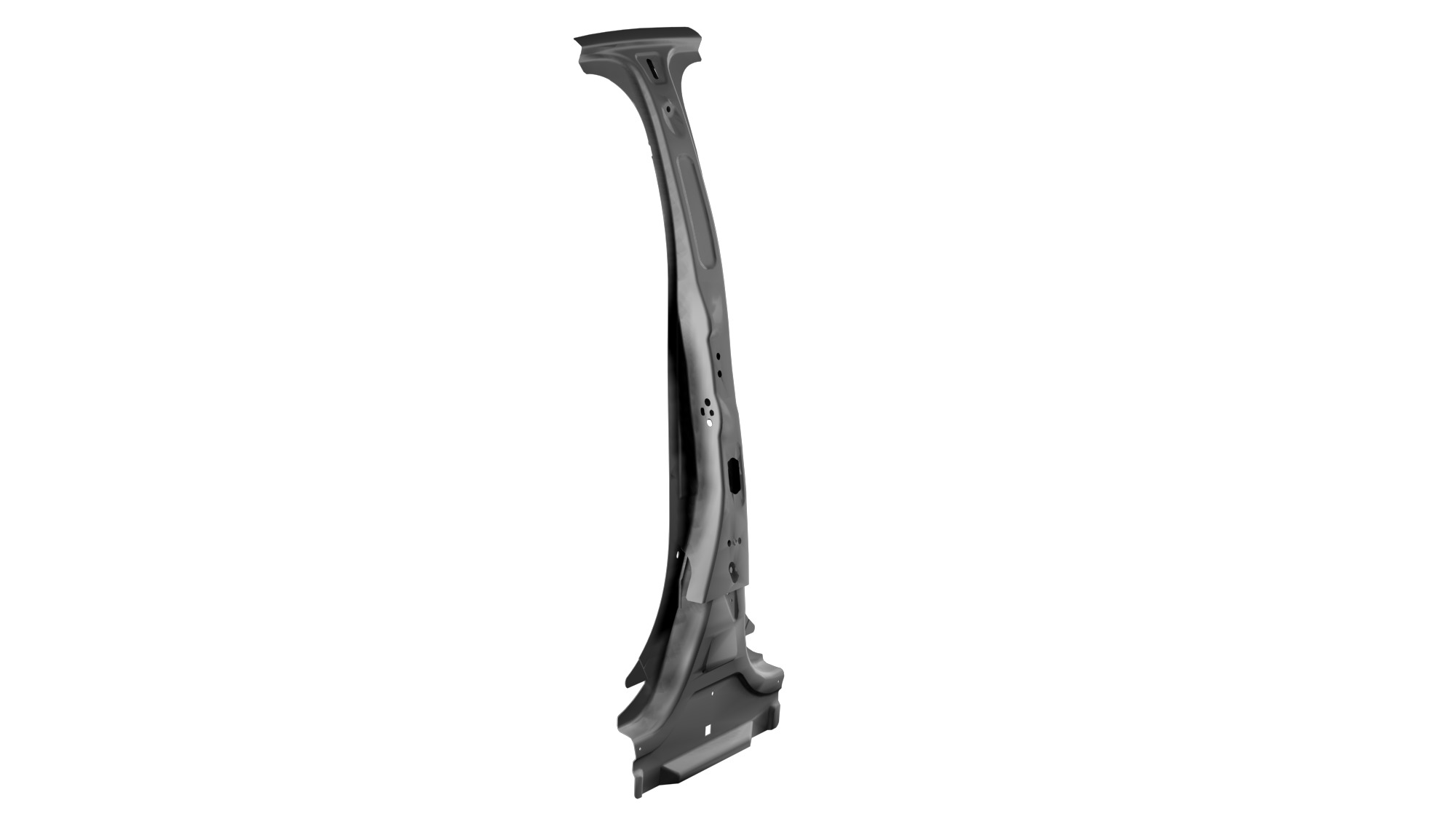
Bild 3 B-Säulenverstärkung aus Ultralex
Mit der Steigerung der Festigkeit einer Aluminiumlegierung geht ebenso wie bei ultrahochfesten Stählen oft ein Verlust der Korrosionsbeständigkeit einher. Während 6000er-Legierungen mit Magnesium- und Siliziumanteil eine sehr gute Resistenz gegen unterschiedlichste Arten der Korrosion aufweisen, benötigen 7000er-Legierungen mit hohem Kupfer-, Zink- und Magne- siumgehalt eine besondere Bearbeitung. Die größte Herausforderung sind dabei Spannungskorrosionsrisse, die an Stellen mit erhöhter korrosions-chemischer Empfindlichkeit und unter Belastung durch Spannung entstehen. Aufgabe der Materiallieferanten ist es in dieser Situation, sicherzugehen, dass die gelieferten Materialien und Komponenten immun gegen Spannungskorrosionsrisse sind und gleichzeitig nur auf eine Art und Weise eingesetzt werden, in der dies garantiert werden kann. Ebenso verhindert werden müssen Formen von kosmetischer Korro- sion wie z. B. die Fadenkorrosion. Während bereits Möglichkeiten entwickelt wurden, um die hohe Qualität von Produkten aus ultrahochfesten Legierungen sicherzustellen, wird kontinuierlich an robusten und erschwinglichen Lösungen gearbeitet, um die Korro- sionsresistenz des Materials und dadurch die Beständigkeit des betreffenden Bauteils noch weiter zu steigern.
Leichtbau: der große Vorteil
Die Streckgrenze als Werkstoffkennwert beschreibt die maximale Belastung, die auf einen Werkstoff ausgeübt werden kann, bevor eine irreversible Verformung eintritt. Während eine Streckgrenze von 500 MPa für eine Aluminiumlegierung bereits einen außerordentlich hohen Wert darstellt, sind ultrahochfeste Stähle mit einer Streckgrenze von 1100 MPa bei gleicher Produktdicke dennoch fester. Werden 7000er-Legierungen wie Ultralex jedoch in einer höheren Produktdicke verwendet, kann ohne Probleme die gleiche Festigkeit wie bei ultrahoch- festen Stählen erreicht werden. Dabei ist aufgrund der deutlich geringeren Dichte von Aluminium gegenüber Stahl zusätzlich eine signifikante Gewichtseinsparung von etwa 17 Prozent möglich, wie in Tabelle 1 zu sehen ist.
Fahrzeugteile beider Materialien bieten ähnliche Eigenschaften für den Fall einer Kollision, also in Bezug auf Festigkeit und Energieabsorption. Alumi- niumlegierungen verursachen dabei jedoch weniger Gewicht. Experten gehen davon aus, dass pro 100 Kilogramm eingespartes Fahrzeuggewicht der CO2-Ausstoß pro Kilometer um rund 10 Gramm gesenkt werden kann. Eine Gewichtseinsparung von 17 Prozent kann hierbei einen entscheidenden Vorteil, nicht nur für Automobilhersteller, sondern ebenso auch für ihre Kunden bringen.
AutorAndreas Afseth, Ph.D. Leiter Forschung und Entwicklung Automotive, ConstelliumKontakt: Constellium Technology Center Parc Economique Centr’Alp 38341 Voreppe Cedex, France Tel.: +33 627 625 418 E-Mail: andreas.afseth@constellium.com www.constellium.com