Mehr Prozessicherheit mit Hazop und PAAG
„Der Störfall im chemischen Betrieb“ lautete der Titel der ersten deutschsprachigen Broschüre zum PAAG-Verfahren, die im März 1980 von der Sektion Chemie der Internationalen Vereinigung für Soziale Sicherheit (IVSS) herausgegeben wurde. Sie war die wortgetreue Übersetzung der 1977 erschienenen HAZOP-Broschüre „A Guide to Hazard and Operability Studies“ der britischen Chemical Industries Association. Im Mai 1980 veranstaltete dann die Berufsgenossenschaft Chemie (heute BG RCI) die erste Schulungsveranstaltung zu der Methode. Broschüre und Seminar zum PAAG-Verfahren sind seit fast 40 Jahren fester Bestandteil des Bildungsprogramms der BG RCI, werden ständig an aktuelle Entwicklungen angepasst und dokumentieren so das etablierte Vorgehen zur systematischen Gefahrenanalyse in der chemischen Industrie. 2017 hat nun der Verband der Elektrotechnik Elektronik Informationstechnik (VDE) eine HAZOP-Methode in einer deutschsprachigen Übersetzung genormt, die mit dem-PAAG-Verfahren moderner Prägung so gut wie nichts gemeinsam hat. Der Beitrag gibt einen Rückblick auf die Erfolgsgeschichte des Verfahrens.
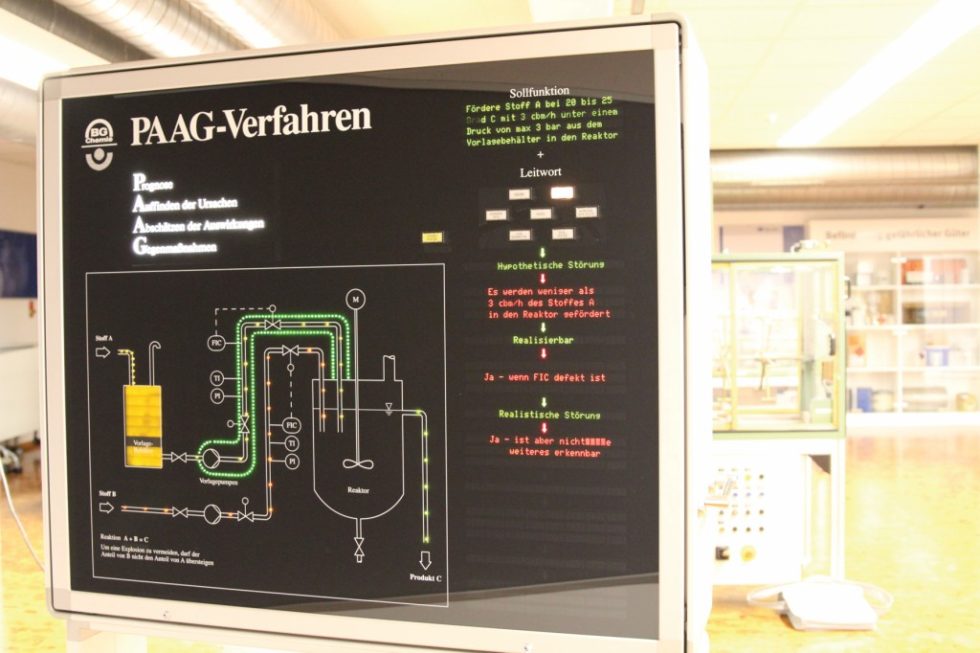
Quelle: BGRCI
Im Mai 1980 konnte Ellis Knowlton, langjähriger Mitarbeiter der ICI in Manchester und Autor der Broschüre „A Guide to Hazard and Operability Studies“ [1], zusammen mit Heinz Hoffmann, Klaus Hammer und Karl-Heinz Blohm von der BG Chemie 42 hochrangige Vertreter der deutschen chemischen Industrie im Ausbildungszentrum der Berufsgenossenschaft im hessischen Laubach begrüßen. Hoffmann hatte im Jahr zuvor an einem HAZOP-Seminar von Knowlton teilgenommen und verfolgte nun die Idee, die unterschiedlichen Ansätze für Sicherheitsanalysen in den Chemieunternehmen zu harmonisieren und zu optimieren. Der erste Tag des Seminars galt dem Erfahrungsaustausch, dann schlossen sich vier intensive Tage mit moderierten Gruppenarbeiten an. Das alles in englischer Sprache, doch am Ende war allen klar: dieses Seminar durfte keine Eintagsfliege bleiben, es sollte in das Bildungsprogramm der BG Chemie aufgenommen werden, die Unterlagen und alle Übungen auch in deutscher Sprache verfügbar sein, um eine möglichst weite Verbreitung zu ermöglichen (Bild).
In einem Artikel mit der Überschrift „Mind full of Accidents“ berichtete das „ICI-Magazine“ schon im Juli 1980 über den erfolgreichen Wissenstransfer auf das kontinentale Europa.
Die Anfänge von HAZOP
Die Geschichte von HAZOP begann eigentlich mehr als bescheiden. Als man in den frühen 1960er-Jahren bei ICI plante, Anlagen für eine neue Generation von Pflanzenschutzmitteln zu bauen, stand man vor der Herausforderung, sehr giftige Zwischenprodukte und gefährliche Prozessschritte beherrschen zu müssen. Daher beschloss man, ein fundamental neues Verfahren für die Überprüfung des Anlagen- und Prozessdesigns zu entwickeln: die bei der Planung involvierten Abteilungen sollten nicht nur auf das von ihnen zu verantwortende Gewerk schauen, sondern gemeinsam einen Blick auf mögliche Abweichungen des bestimmungsgemäßen Prozesses werfen, die entsprechenden Ursachen hierfür finden und die potenziellen Auswirkungen beschreiben. „Critical Examination“ nannte man dieses Vorgehen, bei dem anhand von „Guide Words“ jeder einzelne Prozessparameter des Verfahrens hinterfragt wurde.
Zwei Erfahrungen wurden bei diesem Vorgehen gemacht: Erstens, dass mittels dieser Methodik eine ganze Reihe von Planungsfehlern aufgedeckt wurden, die mit der üblichen Routine nicht gefunden worden waren. Zweitens, dass dieses Vorgehen zwar erfolgreich, aber auch ausgesprochen aufwendig war und sich somit nicht grundsätzlich auf alle Neuplanungen anwenden ließ.
Eine Verbesserung der Methode gelang 1967 in der Petrochemischen Division der ICI. Die Anwendung der „Guide Words“, die bisher auf die rein verbale Prozessbeschreibung beschränkt geblieben war, erfolgte nun in Kombination mit den R&I1)-Schemata des Prozesses. Die Dokumentation beschränkte sich ausschließlich auf erforderliche Änderungen oder offene Fragen. Diese „Flowsheet Method“ beschleunigte das Vorgehen um etwa einen Faktor zehn und führte dazu, dass HAZOP-Studien nun routinemäßig bei den verschiedensten Anlagetypen zum Einsatz kamen.
1970 übernahm die Pharmazeutische Division der ICI das HAZOP-Verfahren. Eingeführt wurden der „study leader“, der die systematische Untersuchung managte, und die Unterstützung durch einen technischen Sekretär, der die gefundenen Ergebnisse tabellarisch protokollierte. Dies lenkte die Diskussion und förderte die Kreativität des Teams, sodass diese Rollenverteilung als eine maßgebliche Verbesserung empfunden wurde. Zugleich wurde das Verfahren auch erstmals auf Batch-Prozesse angewandt und manuelle Tätigkeiten des Bedienpersonals einbezogen.
Mit diesen organisatorischen Änderungen war der Durchbruch der Methodik gelungen und die Akzeptanz des Verfahrens erreicht. Auf der Basis der Modifikationen begann man 1975 bei ICI Schulungen durchzuführen, um alle bestehenden und neuen Anlagen mit der Methode sicherheitstechnisch überprüfen zu können. Der hierzu geschriebene ICI-interne Report über die „Hazard and Operability Studies“ wurde 1977 von der Chemical Industry Association veröffentlicht und dann, wie eingangs erwähnt, 1980 als PAAG-Verfahren im deutschsprachigen Raum übernommen. Parallel wurden auch Seminare angeboten, um die praktische Anwendung des Verfahrens zu trainieren. Chemetics International Company, der kanadische Ableger der Ingenieurabteilung von ICI, übersetzte die Broschüre in zahlreiche Sprachen und sorgte mit entsprechenden Schulungen für eine weltweite Verbreitung der Methode. Trevor Kletz und Ellis Knowlton hatten wegweisende Pionierarbeit geleistet, aus den hölzern wirkenden Anfängen einen international anerkannten Standard zu schaffen, auf dem die Sicherheit tausender Prozessanlagen in der ganzen Welt basiert – und den zehntausende Artikel in Fachzeitschriften und rund 1,3 Millionen Treffer bei Internet-Suchmaschinen rezensieren.
Ritterschlag für das PAAG-Verfahren
Die Teilnehmer des ersten PAAG- Seminars bei der BG Chemie kamen natürlich zum überwiegenden Teil von den bekannten Firmen der deutschen Großchemie und dem Anlagenbau – BASF, Bayer, Hoechst, DuPont, Lurgi – aber von Anfang an waren auch zahlreiche Behördenvertreter an einer Seminarteilnahme interessiert. Denn wenige Tage nach der Veranstaltung in Laubach wurde am 27. Juni 1980 von der Bundesregierung die 12. Verordnung zur Durchführung des Bundes-Immissionsschutzgesetzes verabschiedet – die Störfall-Verordnung [2] –, aus der zwei Jahre später auf europäischer Ebene die sog. Seveso-Richtlinie hervorging. Danach waren entsprechende Betriebe angehalten, im Rahmen einer Sicherheitsanalyse den Nachweis zu führen, dass „eine Gemeingefahr infolge einer Störung des bestimmungsgemäßen Betriebes“ ausgeschlossen werden konnte. Spätestens als am 27. April 1982 die Zweite Allgemeine Verwaltungsvorschrift zur Störfall-Verordnung (2. StörfallVwV) explizit das PAAG-Verfahren als eine der Methoden aufzählte, um die Forderung nach einer systematischen Vorgehensweise zu erfüllen [3], stieg die Nachfrage nach Seminarplätzen enorm an und erforderte das Ausweichen auf Hotels, da die Kapazitäten der BG-Bildungsstätten nicht mehr ausreichten.
Von Anfang an setzten die Verantwortlichen auf ein interaktives Lernen. Fünf Tutoren mit praktischer Erfahrung führten jeweils eine Kleingruppe mit maximal sechs Lernenden anhand eines realistischen Übungsbeispiels an die Methode heran und gaben dabei allen Teilnehmenden die Möglichkeit, als Moderator die Anleitung einer interdisziplinären Gruppe zu üben. Viele Ansätze aus der modernen Erwachsenenbildung wurden bei dem Seminar vorweggenommen. Die Schritte „Prognose von Abweichungen, Auffinden der Ursachen, Abschätzen der Auswirkungen und Gegenmaßnahmen“ sowie die Begriffe „Sollfunktion“ für die detaillierte Beschreibung des bestimmungsgemäßen Betriebs sowie „Leitworte“ für die Abweichungen „nein, mehr, weniger, sowohl als auch, teilweise, Umkehrung und anders als“ haben seit dieser Zeit rund 3 500 Seminarteilnehmende verinnerlicht und wenden diese zu einem großen Teil selbst in ihren Betrieben an. Gleichzeitig wurden weit über 30 000 PAAG-Broschüren mit der Erklärung der Vorgehensweise von der Sektion Chemie der IVSS vertrieben [4]. Wobei der Titel „Der Störfall im chemischen Betrieb“ selbstredend ab der zweiten Auflage verschwunden war.
Weiterentwicklung von HAZOP und PAAG in Prozessindustrie
Ab den 1990er-Jahren wurden die in den Betrieben der chemischen Industrie verwendeten Einrichtungen der Mess- und Regeltechnik zunehmend auch zur Beherrschung von Prozessabweichungen im Sinne der Anlagensicherung genutzt. Seitens der Normenarbeitsgemeinschaft für Meß- und Regeltechnik in der chemischen Industrie (NAMUR; seit 2005 Interessengemeinschaft Automatisierungstechnik der Prozessindustrie e. V.) wurde hierfür der Riskograph entwickelt, der die Klassifizierung der sog. Schutzeinrichtungen ermöglichte, deren Verfügbarkeit über die der Betriebs- und Überwachungseinrichtungen hinausging. Insbesondere in den angelsächsischen Ländern kam etwa zeitgleich der Ansatz der Risikomatrix auf, der ebenfalls eine Bewertung des von Prozessanlagen ausgehenden Gefahrenpotenzials ermöglichte.
Die neuen Werkzeuge zur Klassifizierung war die Stunde der Kritiker von PAAG/HAZOP, die nun der Methodik neben ihrem erheblichen personellen und zeitlichen Aufwand eine weitere Schwachstelle vorwarfen: die mangelnde Risikobewertung, die mit anderen Methoden viel besser zu bewerkstelligen sei. Eine Kritik, die eigentlich ungerechtfertigt war, denn der Ansatz von PAAG/HAZOP war nie die Risikobewertung gewesen, sondern zuvorderst die Identifikation der potenziellen Gefahren, die von der betrachteten Anlage ausgehen können. Als entsprechendes „Werkzeug“ nutzen die „verbesserten“ Methoden in der Regel definierte Szenarien oder erfahrungsbasierte Checklisten. Der Clou des PAAG/HAZOP, nämlich die Suche nach den nicht offensichtlichen Schwachstellen eines neuartigen Prozesses, wird hierbei völlig ausgeblendet, was in manchen Fällen zum Übersehen der eigentlichen Knackpunkte führen kann.
Gleichwohl entwickelten sich HAZOP und PAAG in diese Richtung weiter. Neues aufnehmen und Ballast abwerfen war die Devise. Neben HAZOP entstand die Methode HAZID zur vorgelagerten Gefahrenidentifizierung (Hazard Identification), um eine Abschätzung zu ermöglichen, in welchem Umfang überhaupt Risiken zu erwarten sind und entsprechend die Tiefe des HAZOP anzupassen, sowie das Werkzeug HAZAN zur Gefahrenbewertung (Hazard Analysis), um Anforderungen an das Schutzkonzept anzupassen. Eine entsprechende Broschüre von Trevor Kletz erläutert das Vorgehen [5]. Ähnliche Instrumente wurden in Deutschland in Ergänzung zum PAAG entwickelt, wobei firmenspezifische Lösungen die Regel waren. Praktische Erfahrungen mit der HAZOP- Methodik trugen Industriekollegen in einer Schrift des Europäischen Prozesssicherheitszentrums EPSC (European Process Safety Centre) zusammen, die aufzeigt, dass einige der ursprünglichen Ideen, wie beispielsweise das Anwenden aller Leitworte auf alle Elemente der Sollfunktion, keine Verbesserung der Qualität, dagegen eine aufgeblähte Diskussion und Dokumentation bedeuteten [6].
Bei der Nutzung des PAAG-Verfahrens hat sich ebenfalls viel getan und die Kombination von PAAG als Methode der Gefahrenidentifikation mit den bewertenden Instrumenten Risikomatrix, Risikograph, FMEA (Fehlermöglichkeiten- und Einfluss-Analyse) oder LOPA (Layers of Protection Analysis) sind heute gang und gäbe.
Neues Seminarkonzept der BG RCI
Auch die Seminare und die Broschüre zum PAAG-Verfahren übernahmen die fachlichen Erweiterungen und folgten in ihren theoretischen Schwerpunkten dem Zeitgeist. Zum einen wurden die Darstellungen der verwendeten Übungsbeispiele modernen Prozessanlagen angepasst, zum anderen die organisatorisch-soziologischen Anforderungen, die eine Einführung und Nutzung der Methodik in Betrieben mit sich bringen, auf der Basis der Erfahrungen der Teilnehmenden abgebildet. Die wandelnde Unternehmenskultur von hierarchisch geprägtem Umgang hin zu flachen Organisationsstrukturen, die kollegiale Teamarbeit und die Nutzung digitaler Medien sind inzwischen so selbstverständlich geworden, dass eine ausufernde Darstellung dieses zur damaligen Zeit geradezu als revolutionär geltenden Vorgehens nicht mehr erforderlich war.
Weil längst nicht alle Seminarteilnehmende in ihrem Betrieb die Rolle des Moderators übernehmen und das Erlernen der Grundtechniken nicht einer ganzen Woche bedarf, wird es ab 2018 bei der BG RCI zwei neue Typen von PAAG-Seminaren geben: ein Halbwochenseminar für Einsteiger, das als Basisseminar den Teilnehmenden die Prinzipien des PAAG-Verfahrens beispielhaft erläutert, und ein Halbwochenseminar als Aufbauseminar für Praktiker, bei dem sowohl die Moderation eines interdisziplinären Teams als auch die Modifikation der Methodik hinsichtlich Gefahrenidentifikation und Gefahrenbewertung im Vordergrund stehen2). Intensiviert werden soll in den Seminaren auch wieder der Austausch mit den Genehmigungsbehörden, um dem mit der Neufassung der Störfallverordnung 2017 gestiegenen Informationsbedürfnis Rechnung zu tragen.
Normung des HAZOP-Verfahrens
Anfang 2017 erschien nun – gut 40 Jahre nach Erscheinen der HAZOP-Broschüre und 37 Jahre nach der ersten Übersetzung der Methodik unter dem Namen PAAG ins Deutsche – eine vom Verband der Elektrotechnik Elektronik Informationstechnik (VDE) initiierte Norm, die als VDE 0050-8 [7] unter dem Titel „HAZOP-Verfahren (HAZOP-Studien) – Anwendungsleitfaden“ die Übersetzung der 15 Jahre alten IEC 61882 [8] darstellt3), Dabei wurden seitens des VDE einerseits völlig neue Begriffe eingeführt, statt auf die bewährten und in der verfahrenstechnischen Industrie längst etablierten Vokabeln zurückzugreifen (z. B. „Entwurfsziel“ statt „Sollfunktion“, „Vorhandene Lenkung“ statt „Gegenmaßnahmen“), andererseits auch in die Mottenkiste archaischer Formulierungen zurückgegriffen und weitgehend unverständliche Formulierungen übersetzt (z. B. „Die Studie wird unter der Anleitung eines geübten und erfahrenen Studienleiters durchgeführt, der eine umfassende Abdeckung des zu untersuchenden Systems durch logisch-analytisches Denken sicherzustellen hat.“ „Der Gebrauch eines Computers bietet eine größere Flexibilität im Layout.“ „Eine HAZOP-Studie erzeugt Besprechungsberichte oder Software, die die Abweichungen, ihre Ursachen, Folgen und empfohlenen Aktionen zusammen mit hervorgehoben gekennzeichneten Konstruktionszeichnungen, Dokumenten oder anderen Darstellungen des Systems festhalten, die die dazugehörigen Protokollnummer und, wo möglich, die empfohlene Maßnahme angeben.“).
Dem Anspruch, einen Anwendungsleitfaden darzustellen, wird die Norm aus Sicht des Autors in keinster Weise gerecht. Insbesondere die im Abschnitt B zitierten Anwendungsbeispiele an einer Prozessanlage aus dem Jahre 1998 sind alles andere als einer Schrift aus dem Jahr 2017 würdig, insbesondere vor dem Hintergrund, dass nun Fachfremde im Rahmen von Audits auf die Einhaltung dieser Norm mit ihren Begriffen und Darstellungen pochen und somit über 35 Jahre Erfahrung und praktische Anwendung des Verfahrens in der chemischen Industrie ignorieren könnten. TS 625
1) R&I: Rohrleitungs- und Instrumentierungsfließbilder
2) Die Seminarinhalte können auf der Homepage der BG RCI unter http://seminare.bgrci.de/shop/ anlagensicherheit eingesehen werden.
3) Bei der Revision dieser Norm 2016 wurden nur marginale redaktionelle Änderungen eingebracht.
Literaturverzeichnis
[1] Knowlton, E.: A Guide to Hazard and Operability Studies. Chemical Industries Association. London 1977.
[2] Zwölfte Verordnung zur Durchführung des Bundes-Immissionsschutzgesetzes (Störfall-Verordnung). BGBl. I (1980), S. 772 ff.
[3] Zweite Allgemeine Verwaltungsvorschrift zur Störfall-Verordnung. GMBl. (1982), S. 203 ff.
[4] Das PAAG-Verfahren – Methodik, Anwendung, Beispiele. Hrsg.: IVSS Sektion Chemie. 4. Aufl. Heidelberg: 2008. http://medienshop.bgrci.de/shop/ivss
[5] Kletz, T.: Hazop and Hazan. 4. Aufl. Boca Raton: CRC Press 1999.
[6] Tyler, B. J.; Crawley, F.; Preston, M. L.: HAZOP: Guide to Best Practice. Hrsg.: The Institution of Chemical Engineers. 2. Aufl. London 2008.
[7] DIN EN 61882 (VDE 0050-8): HAZOP-Verfahren (HAZOP-Studien) – Anwendungsleitfaden. Berlin: Beuth Verlag 2017.
[8] IEC 61882: Hazard and operability studies (HAZOP studies) – Application guide. Genf: International Electrotechnical Commission 2002.
Dr. Joachim Sommer, Referat Anlagen- und Verfahrenssicherheit der Berufsgenossenschaft Rohstoffe und chemische Industrie (BG RCI), Heidelberg.