Messen von Ankopplungskräften zur Beurteilung der Vibrationsübertragung auf die Hände
Die Ankopplungskräfte zwischen der menschlichen Hand und vibrierenden Werkzeuggriffen haben einen hohen Einfluss auf die Schwingungsübertragung und damit auf die Gefährdung. Der Stand der Technik zur Ermittlung der Ankopplungskräfte im Sinne der geltenden Normen benötigt derzeit eine Messtechnik im fünfstelligen Euro-Bereich. Zur weiteren Verbreitung der Anwendung untersucht das Institut für Arbeitsschutz der Deutschen Gesetzlichen Unfallversicherung (IFA) die Einsatzmöglichkeiten eines preiswerteren Systems zur Ankopplungskraftmessung.
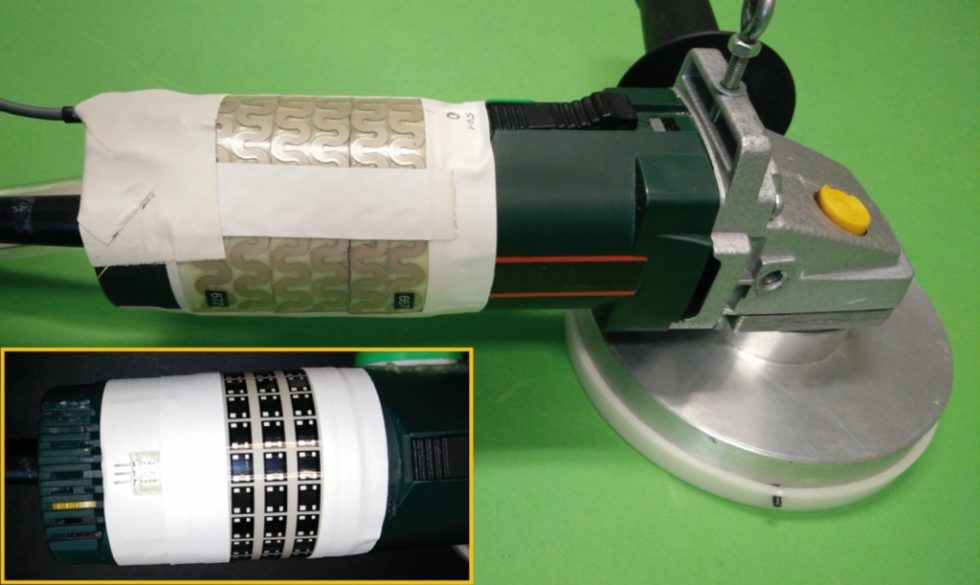
Quelle: DGUV
Vibrationsexpositionen bilden einen Belastungsbereich beim Einsatz von Maschinen. Die Exposition bei hohen Vibrationsintensitäten über mehrere Jahre kann zu Erkrankungen des Hand-Arm-Systems führen. Derartige Erkrankungen können auf neuronale und muskuloskeletale irreversible Schädigungen zurückzuführen sein. Unter bestimmten Voraussetzungen werden Berufserkrankungen von den Unfallversicherungsträgern in Deutschland entschädigt [1].
Die Ermittlung, Bewertung und Beurteilung der Vibrationskenngrößen wird im Wesentlichen durch Normen und Richtlinien festgelegt. Die Vorgehensweise zur Messung der Maschinenvibration schreibt eine Montage der Vibrationsaufnehmer unmittelbar in der Nähe der Mensch-Maschine-Schnittstelle (Handgriff) vor [2].
Aufgrund dieser Gegebenheit lässt sich jedoch keine Aussage darüber treffen, wie groß der Anteil der Vibrationsenergie ist, der tatsächlich in die Hand des Maschinenbedieners eingeleitet wird. Daher ist die Ankopplungskraft zwischen Hand und Maschinengriff ein wesentlicher Einflussfaktor auf die Vibrationseinleitung. Erhöhte Halte- und Führungskräfte führen zu einer besseren Ankopplung zwischen Hand und Maschinengriff und resultieren in einer höheren Vibrationsübertragung und umgekehrt. Ferner beeinflusst die Stärke der Ankopplung den vom Vibrationsaufnehmer gemessenen Vibrationskennwert [3].
Somit ist es im Interesse der Forschung, neben der gemessenen Vibrationskenngröße (ahv, Effektivwert der frequenzbewerteten Hand-Arm-Schwingungen) und der Expositionszeit auch die sog. Ankopplungskraft quantitativ zu ermitteln.
Nach den Technischen Regeln der Lärm-Vibrations-Arbeitsschutzverordnung [4; 5] ist die messtechnische Erfassung der Ankopplungskräfte bisher nicht erforderlich. Zur Verringerung der Belastung sind aber solche Arbeitsverfahren und Geräte vorzuziehen, die nur geringe Ankopplungskräfte erfordern. Informationen zur Prävention enthält das DGUV Fachbereichs-Informationsblatt Nr. 63 [6].
Um ein einheitliches Verständnis der an Maschinengriffen auftretenden Kräfte zu schaffen, wurde der Begriff der Ankopplungskraft erstmals mit der Norm DIN 45679 festgelegt [7]. Sie ist die betragsmäßige Summe der auf einen Griff wirkenden Andruck- und Greifkräfte, die sich terminologisch an der in den 1990er-Jahren zur Verfügung stehenden Messtechnik orientieren (siehe Bild 1).
Dabei entspricht die Andruckkraft einer von außen auf die Maschine wirkenden Kraft, die nicht innerhalb der Hand kompensiert wird. Die Greifkraft hingegen ist als zangenartig wirkende Kraft definiert, die beim Umschließen eines Griffs von entgegengesetzten Teilkräften kompensiert wird.
Zur Beurteilung, inwiefern sich die Höhe der Ankopplungskraft auf die Vibrationsbelastung auswirkt, bietet die DIN 45679 ein Verfahren, um die gemessene Vibrationskenngröße mit einem Ankopplungskoeffizienten zu gewichten. Somit kann eine ankopplungskraftabhängige Messgröße ermittelt werden, die sich in die bestehenden Mess- und Beurteilungsverfahren im Sinne der Norm DIN EN ISO 5349 eingliedert.
Ursprünglich konnten die Greif- und Andruckkräfte nur aufwendig mithilfe von instrumentierten Griffen und Messplattformen unter Laborbedingungen ermittelt werden. Innerhalb eines von der EU geförderten Projekts („Vibtool“) [8] wurde ein Messsystem entwickelt, das mit Sensormatrizen aus einzelnen kapazitiven Messzellen in der Lage ist, die Druckverteilung bei Ankopplungsvorgängen an realen Maschinengriffen zu ermitteln (Bild 2).
Aus der Druckverteilung am Griff können dann die Andruck- und Greifkräfte im Sinne der Normen berechnet werden. Seitdem wird dieses kapazitive Messsystem auch in betrieblichen Messungen zur Gefährdungsbeurteilung erfolgreich eingesetzt.
Aufgrund seines hohen Preises, der vergleichsweise empfindlichen Sensorik sowie der Komplexität im Umgang mit der Messdatenauswertung findet das Messsystem derzeit jedoch wenig Anwendung.
Piezoresistive Sensortechnologie
Im Gegensatz zu den kapazitiven Sensormatrizen sind piezoresistive Foliensensoren günstig, robust und können durch Kürzen der Sensorfolie flexibel an Maschinengriffe angepasst werden. In Bild 3 sind zwei Exemplare dargestellt, wobei der untere Sensor ein kundenindividuell angefertigtes Produkt ist, das in der Untersuchung verwendet wurde.

Bild 3 Piezoresistive Foliensensoren. Oben: herkömmlicher Sensor. Unten: kundenspezifische Anfertigung.
Foto: DGUV
An jedem Ort, an dem sich die obere und untere Elektrodengitterstruktur kreuzen, entsteht eine aktive Sensorfläche. Die Elektrodengitter werden durch eine elastische dielektrische Schicht voneinander getrennt. Wirkt eine Kraft auf den Sensor ein, reduziert sich dessen intrinsischer Widerstand aufgrund der Kompression der dielektrischen Schicht. Die Widerstandsänderung wird als Summensignal abgegriffen und von einfachen Verstärkerschaltungen in ein Gleichspannungssignal umgewandelt. Das Signal kann daraufhin in beliebige Messwerterfassungskarten eingespeist werden.
Die Einfachheit solcher preiswerten Sensoren hat den Nachteil, dass eine ortsaufgelöste Druckverteilung entlang der Sensoroberfläche aus dem Summensignal nicht errechnet werden kann. Dies setzt vor allem eine möglichst gleichmäßige Sensitivität entlang der Sensoroberfläche voraus.
Im Rahmen einer Voruntersuchung zeigten die piezoresistiven Sensoren eine geringe Messabweichung hinsichtlich Linearität (2 bis 4 %), Hysterese (< 4 %) und Wiederholpräzision (< 6 %). Damit liegt die Messabweichung in der Größenordnung von Ergebnissen vergleichbarer Untersuchungen [9; 10].
Werden die Sensoren jedoch an unterschiedlichen Orten entlang ihrer Sensoroberfläche mit der gleichen Kraft belastet, führt dies zu deutlich variierenden Signalantworten.
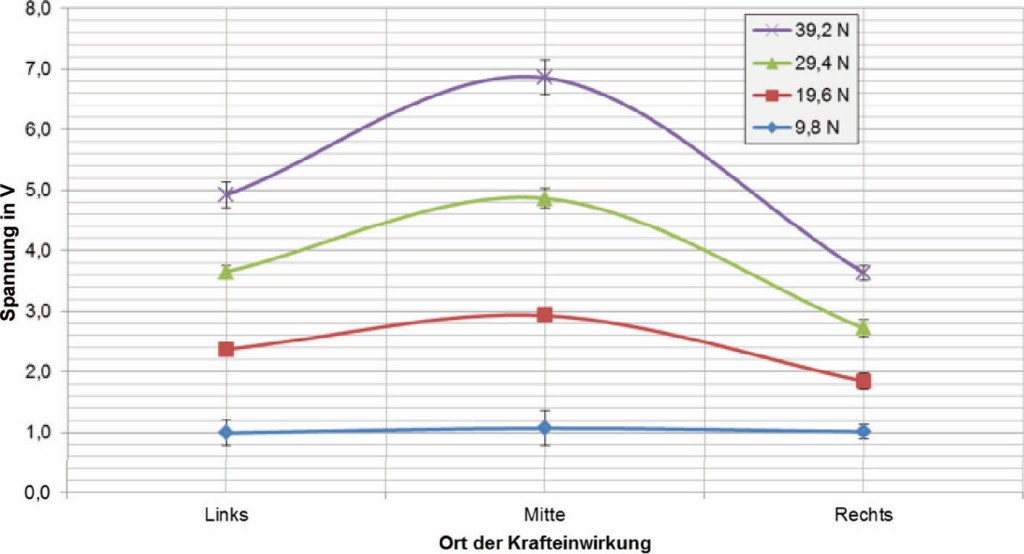
Bild 4 Sensorsignal in Abhängigkeit vom Ort der Krafteinwirkung auf der Sensoroberfläche.
Foto: DGUV
Bild 4 zeigt den Einfluss von vier Belastungsintensitäten an drei unterschiedlichen Positionen auf der Sensoroberfläche. Da die Sensoren nur ein Summensignal liefern, kann dieser Effekt nicht korrigiert werden und führt zu einer durchschnittlichen Messabweichung von 29 % ( 8 %; n = 7).
Anders als bei herkömmlichen Sensoren ist aufgrund der physikalischen Eigenschaften der piezoresistiven Sensortechnologie z. B. eine Werkskalibrierung aufgrund der fehlenden Langzeitstabilität nicht möglich. Somit muss der Zusammenhang zwischen einwirkender Kraft und Ausgangssignal beispielsweise über Regressionsanalysen hergestellt werden. Dabei ist der zu ermittelnde Faktor der Sensitivitätskoeffizient, der je nach Sensorexemplar und Anbringungsart am Maschinengriff deutlich variiert. Dies setzt voraus, dass eine Sensorkalibrierung erst nach der Montage am Maschinengriff erfolgen kann.
Innerhalb der Untersuchung wurde ein Verfahren entwickelt, um die Foliensensoren unmittelbar am Maschinengriff zu kalibrieren und in Betrieb zu nehmen. Dazu wurde der Sensor am Griff von einem Elastomer umschlungen und mit definierten Kräften belastet. Über eine Kalibrierapplikation kann daraufhin der Zusammenhang (Sensitivitätskoeffizienten) zwischen der einwirkenden Kraft am Griff und dem resultierenden Sensorsignal hergestellt werden.
Untersuchung der Messabweichung
Nachdem ein praktikabler Weg gefunden wurde, um Ankopplungskräfte mit den Foliensensoren an Maschinengriffen zu messen, wurde die Messgenauigkeit beider Sensortechnologien gegenübergestellt. Dazu wurden die kapazitiven- und piezoresistiven Sensoren an einem mit Präzisionskraftaufnehmern instrumentierten Referenzgriff (Bild 5) befestigt, um deren jeweilige Messabweichung im Vergleich zum Referenzgriff zu untersuchen.
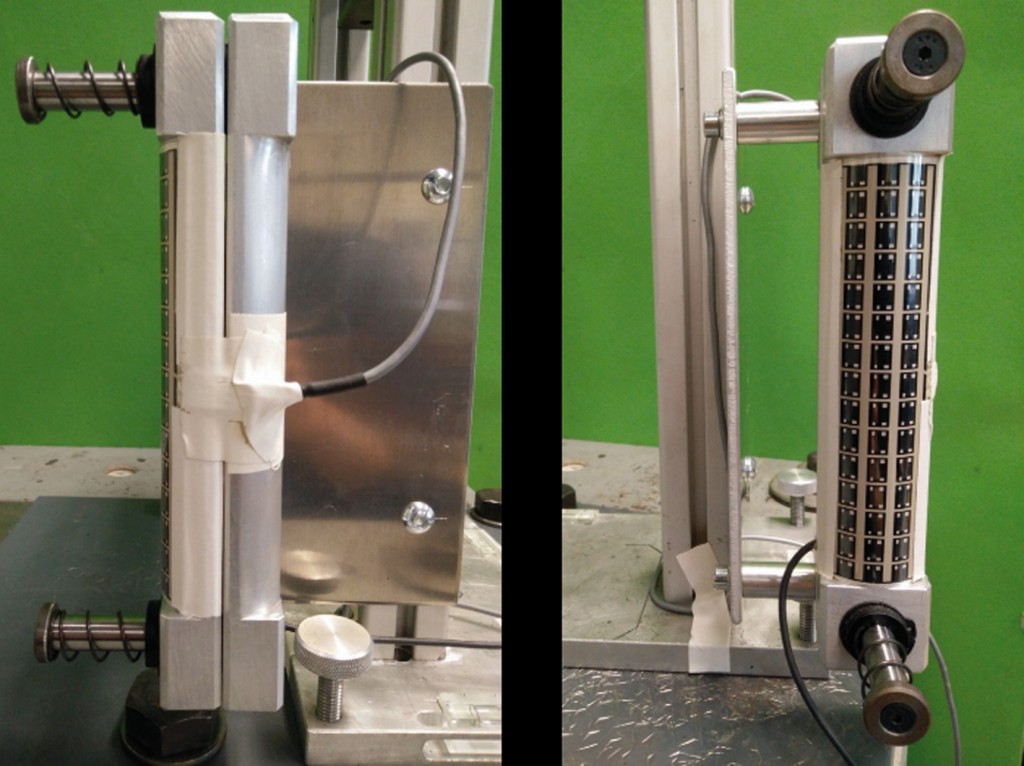
Bild 5 Seitenansicht und Draufsicht des instrumentierten Referenzgriffs zum Vergleich beider Messsysteme.
Foto: DGUV
Der Aufbau orientiert sich an der Vorlage der DIN 10819 [11] zur Gestaltung eines instrumentieren Griffs mit Messeinrichtungen für Andruck- und Greifkräfte. Mithilfe von sechs Versuchspersonen wurden unterschiedliche Ankopplungsvorgänge am instrumentierten Griff simuliert. Die Signalantworten des jeweils zu prüfenden Systems (kapazitiv und piezoresistiv) wurden mit den Messwerten des Referenzgriffs hinsichtlich ihrer Abweichungen untersucht. Einen beispielhaften Signalverlauf zeigt Bild 6.

Bild 6 Vergleich der Signalverläufe vom Foliensensor und Referenzgriff. Die Markierungen zeigen Nichtlinearitäten.
Foto: DGUV
Bild 7 zeigt die durchschnittliche Messabweichung beider Sensortechnologien im Vergleich zum Referenzgriff.
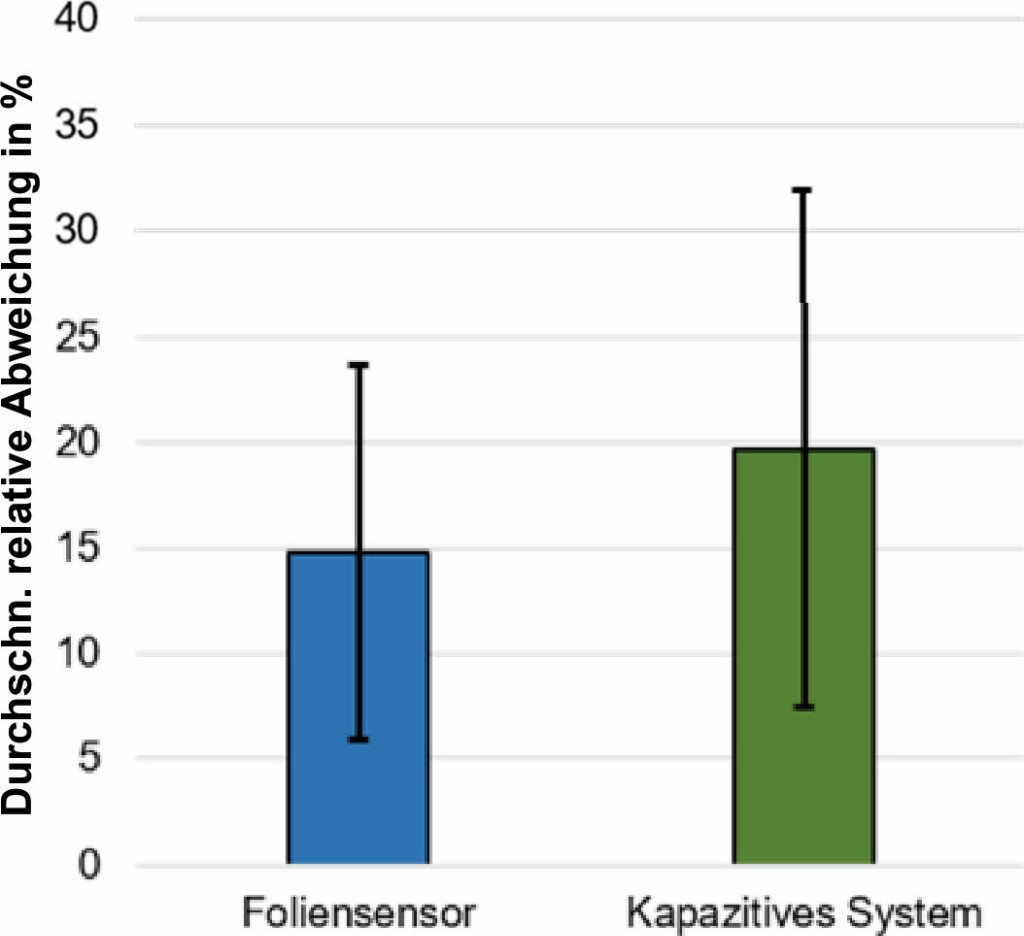
Bild 7 Durchschnittliche relative Messabweichung der Foliensensoren und des kapazitiven Systems am instrumentierten Griff.
Foto: DGUV
Die günstigen Foliensensoren zeigten eine um etwa 5 % geringere durchschnittliche Messabweichung im Vergleich zum kapazitiven Messsystem. Beide Systeme liegen hinsichtlich ihrer durchschnittlichen Abweichung beim Messen von Ankopplungskräften innerhalb der normativen Empfehlung (kombinierte Messabweichung < 28 % für die Ankopplungskraft nach DIN 45679 und ISO 15230).
Ferner stieg die Messabweichung für sehr hohe Ankopplungskräfte (> 300 N) aufgrund von Übersteuerungseffekten. Zudem nimmt die relative Messabweichung für Ankopplungskräfte < 30 N zu, da Drifteffekte der Offsetspannung der Sensoren bei geringen Belastungen stärker ins Gewicht fallen.
Beim Umschließen des Griffs kann es zu einer Änderung der Druckverteilung der Handinnenfläche kommen, sodass die Belastung an sensitiveren oder insensitiveren Sensorbereichen erfolgt. Aufgrund der beschriebenen Sensitivitätsunterschiede entlang der Oberfläche der Foliensensoren führt dies zu einem nichtlinearen Signalverlauf (gelbe Rechtecke in Bild 6).
Man kann annehmen, dass dieser Effekt den größten Teil zur Messabweichung beim Messen mit den Foliensensoren beiträgt. Der Effekt kann an realen Maschinengriffen aufgrund variierender Greifwinkel und Positionen einen größeren Einfluss auf die Messabweichung nehmen.
Erprobung an handgeführten schwingenden Geräten
Um eine Aussage über die Praxistauglichkeit der günstigen Foliensensoren zu treffen, wurden diese an Griffen von handgeführten Geräten untersucht. Für eine Einschätzung der Messgenauigkeit der Foliensensoren müssen beide Messsysteme simultan an der gleichen Krafteinleitungsstelle messen.
Exemplarisch wurden ein Winkelschleifer (Bild 8) und ein Stampfer (Bild 9) untersucht.

Bild 8 Sensormontage am Winkelschleifer. Der Foliensensor liegt unter dem kapazitiven System.
Foto: DGUV
Beide Geräte besitzen sehr unterschiedliche charakteristische Vibrationsverhalten, die stellvertretend für ihre Maschinengruppe sind.
Ein Winkelschleifer wurde gewählt, da er in vielen Wirtschaftszweigen Verwendung findet. Der Stampfer wird fast ausschließlich in Gießereien verwendet, wurde aber aufgrund seines Arbeitsverhaltens mit hohen Amplituden, niedriger Frequenz und Impulshaltigkeit ausgewählt. Diese Eigenschaften erschweren den Messsystemen die Messaufgabe deutlich. Daher ist es von Interesse, die Anwendbarkeit der Foliensensoren bei einer solchen Maschine zu untersuchen.
Aus Gründen der Praktikabilität wurden Ersatzarbeitsverfahren eingesetzt, damit die Messungen im Labor durchgeführt werden konnten. Fünf Versuchspersonen absolvieren eine Trainingsphase an den Geräten. Die zugrunde liegenden Ersatzarbeitsverfahren richten sich nach den in DIN EN ISO 28927 [12] vorgeschlagenen Vibrationsemissionsmessungen für handgehaltene motorbetriebene Maschinen. Die Bilder 8 und 9 zeigen die Montage der Sensoren an den Geräten. Die gemessenen Ankopplungskräfte während des Maschinenbetriebs sind für alle Versuchspersonen und für beide Messsysteme in den Bildern 10 und 11 gegenübergestellt.
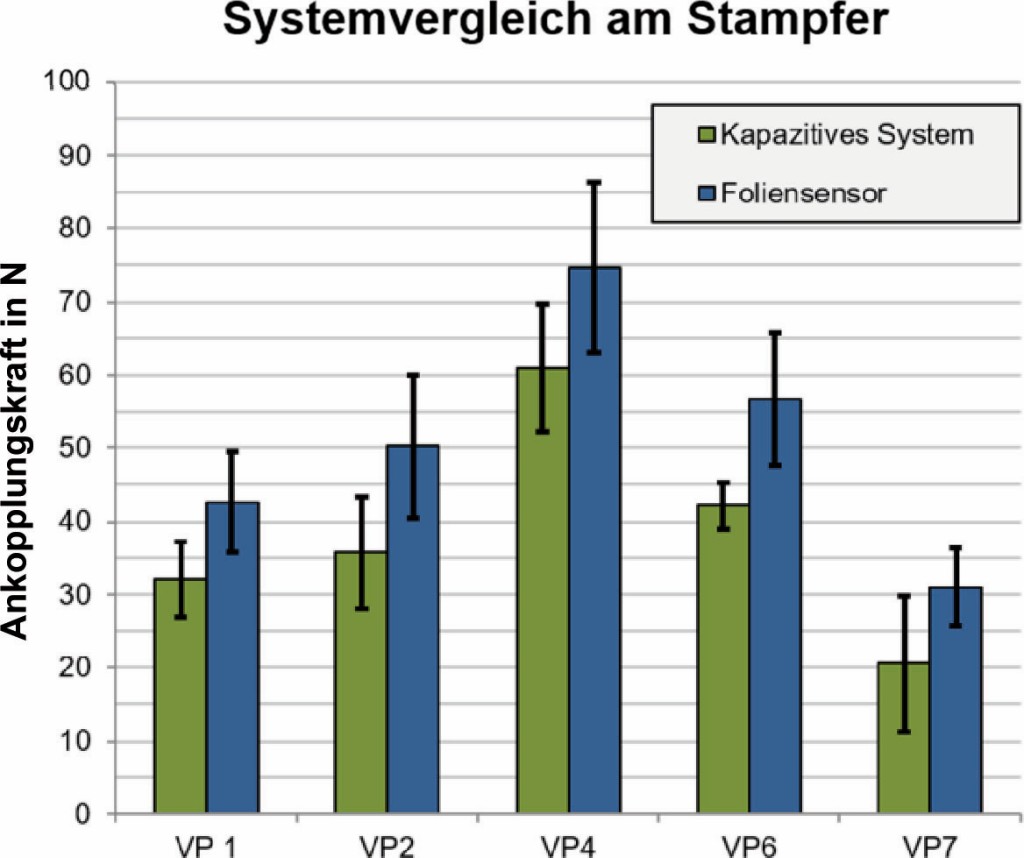
Bild 10 Ermittelte Ankopplungskräfte der Versuchspersonen (VP) beider Systeme am Stampfer.
Foto: DGUV
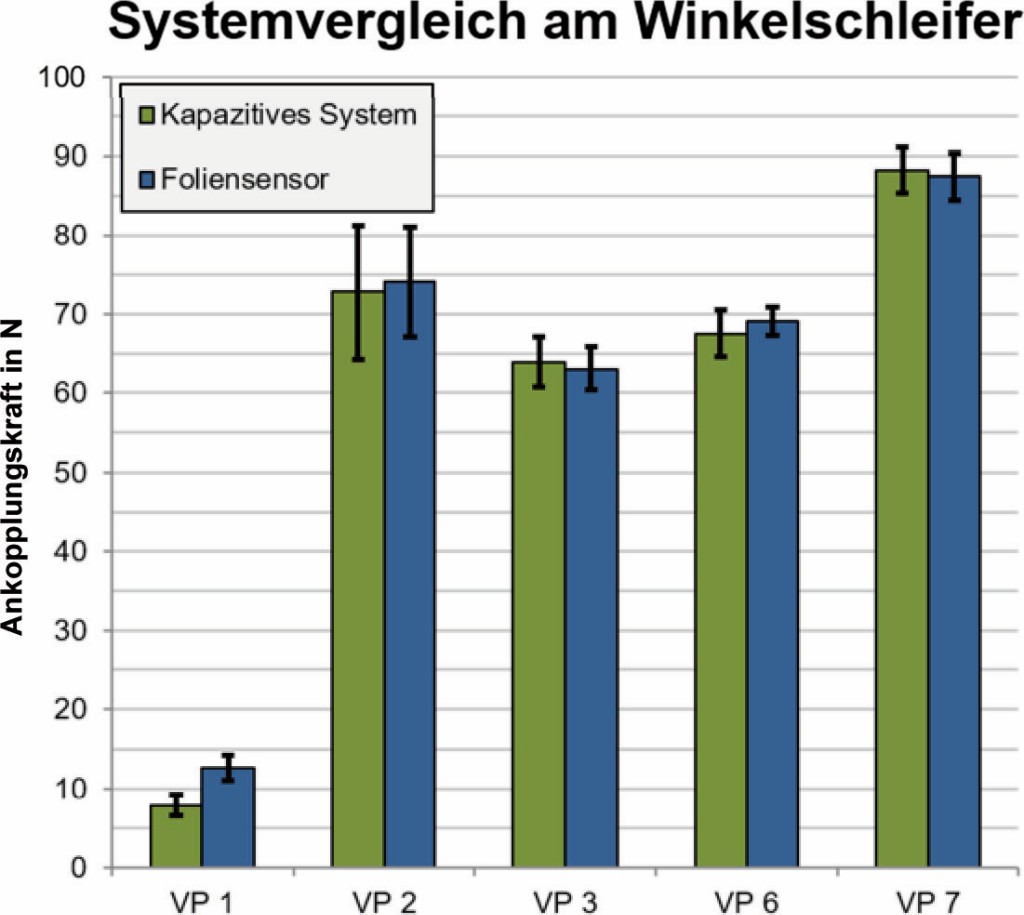
Bild 11 Ermittelte Ankopplungskräfte der Versuchspersonen (VP) beider Systeme am Winkelschleifer .
Foto: DGUV
Grüne Balken repräsentieren die gemessene Ankopplungskraft des kapazitiven Messsystems, blaue entsprechen denen der piezoresistiven Foliensensoren.
Die durchschnittliche Abweichung beider Systeme am Winkelschleifer fällt mit 10,5 % und einer Streuung von 12,2 % gering aus. Ein Grund für die gute Übereinstimmung sind die konstanten Bedingungen des Ersatzarbeitsverfahrens. Außerdem begünstigt die geringe Krümmung der Sensoren aufgrund des großen Griffdurchmessers des Winkelschleifers die Übereinstimmung der Messwerte.
Die durchschnittliche Abweichung beider Systeme am Stampfer fällt mit 25,7 % und einer Streuung von 7,6 % mehr als doppelt so hoch aus. Dies ist auf verschiedene Ursachen zurückzuführen. Zum einen führt der geringe Durchmesser des Nebengriffs dazu, dass die Sensoren stark gekrümmt werden. Dies kann vor allem beim kapazitiven Messsystem zur Vergrößerung der Messabweichung führen [8]. Ein anderer Grund liegt im vergleichsweise impulshaltigen Betrieb des Stampfers, der die Versuchspersonen zu kontinuierlichen Änderungen des Handgelenkwinkels zwingt. Dies kann sich wiederum nachteilig auf die Foliensensoren auswirken (ortsabhängige Sensitivitätsunterschiede).
Ein weiterer Grund für die höhere Abweichung liegt in der geänderten Anordnung der Sensoren zueinander. Im Gegensatz zur Untersuchung am Winkelschleifer war hier eine Anordnung des Foliensensors über den kapazitiven Sensor notwendig (Bild 9). Liegt der Foliensensor auf einer elastischen Oberfläche wie der des kapazitiven Systems, kann sich dieser beim Greifen in zwei Achsen verformen bzw. krümmen. Der Hersteller der Sensoren empfiehlt jedoch ausdrücklich von einer Krümmung in mehr als einer Raumrichtung abzusehen [13]. Dieser Effekt führt zur Überbeanspruchung des Sensors, was auch die systematisch höher gemessenen Ankopplungskräfte des Foliensensors erklären könnte. Hier empfiehlt es sich, eine Verformung aufgrund einer zu elastischen Griffoberfläche möglichst zu vermeiden.
Fazit und weiterführende Optimierungsvorschläge
Um Ankopplungskräfte an handgehaltenen, schwingenden Geräten zu messen, wurde eine Methode entwickelt, mit der günstige Foliensensoren zuverlässig an Griffen in Betrieb genommen werden können.
Die Untersuchung zeigt, dass die piezoresistiven Foliensensoren im Vergleich zu kapazitiven Sensormatrizen eine günstige Alternative zum Messen von Ankopplungskräften darstellen. Obwohl die Sensoren für qualitative Kraftmessungen konzipiert wurden, sind quantitative Messungen entgegen ihrer ursprünglichen Applikation realisierbar. Für den künftigen Einsatz bieten folgende Punkte Verbesserungspotenzial:
- Messverstärker für die Foliensensoren sollten eine Kompensationsschaltung erhalten, um einen Drift des Spannungsoffsets zu vermeiden.
- Der Herstellungsprozess der Sensoren sollte hinsichtlich der Variation im Übertragungsverhalten entlang der Sensoroberfläche optimiert werden.
- Eine Optimierung der Flexibilität des Sensordesigns wäre sinnvoll, um diese künftig noch besser an ergonomisch geformte Griffe anbringen zu können.
Innerhalb der Normungsarbeit sollten Empfehlungen für neue Sensortechnologien ausgesprochen werden. Die Ergebnisse der Untersuchung zeigen, dass die piezoresistive Sensortechnologie das Potenzial bietet, Ankopplungsmessungen im Sinne der Normen gerecht zu werden. TS 569
Literaturverzeichnis
[1] Berufskrankheiten-Verordnung vom 31. Oktober 1997. BGBl. I, S. 2623, zul. geänd. durch Art. 1 der Verordnung vom 22. Dezember 2014. BGBl. I, S. 2397.
[2] DIN EN ISO 5349-2: Mechanische Schwingungen – Messung und Bewertung der Einwirkung von Schwingungen auf das Hand-Arm-System des Menschen – Teil 2: Praxisgerechte Anleitung zur Messung am Arbeitsplatz. Berlin: Beuth Verlag 2015.
[3] CEN/TR 16391: Mechanical vibration and shock – Hand transmitted vibration – Influence of the coupling forces at the hand-machine interface on exposure evaluation. Brüssel: CEN 2013.
[4] Technische Regel zur Lärm- und Vibrations-Arbeitsschutzverordnung – TRLV Vibrationen. GMBl. Nr. 25/26 vom 24. Juni 2015, S. 482.
[5] Lärm- und Vibrations-Arbeitsschutzverordnung vom 6. März 2007. BGBl. I, S. 261, zul. geänd. durch Art. 2 der Verordnung vom 15. November 2016. BGBl. I, S. 2531.
[6] Fachbereichsinformationsblatt Nr. 63: Hand-Arm-Vibration – Informationen zur Berücksichtigung der Ankopplungskräfte. Hrsg.: Fachbereich Holz und Metall der DGUV. Mainz 2012.
[7] DIN 45679: Mechanische Schwingungen – Messung und Bewertung der Ankopplungskräfte zur Beurteilung der Schwingungsbelastung des Hand-Arm-Systems. Berlin: Beuth Verlag 2013.
[8] VIBTOOL – Grip Force Mapping for Characterisation of Hand-Held Vibrating Tools. Final Technical Report. Ancona 2018.
[9] Marcotte, P.; Adewusi, S.; Rakheja, S.: Development of a low-cost system to evaluate coupling forces on real power tool handles. Can. Acoustics 39 (2011) Nr. 2, S. 36-37.
[10] Kalra, M. et al.: Feasibility analysis of low-cost flexible resistive sensors for measurements of driving point mechanical impedance of the hand-arm system. Int. J. Ind. Ergon. 49 (2015), S. 44-52.
[11] DIN EN ISO 10819: Mechanische Schwingungen und Stöße – Hand-Arm-Schwingungen – Messung und Bewertung der Schwingungsübertragung von Handschuhen in der Handfläche. Berlin: Beuth Verlag 2013.
[12] DIN EN ISO 28927: Handgehaltene motorbetriebene Maschinen – Messverfahren zur Ermittlung der Schwingungsemission. Berlin: Beuth Verlag 2011.
[13] How does the level of accuracy change as curvature of surfaces increases? Hrsg.: Tekscan Inc. South Boston 2016. www.tekscan.com/support/faqs/how-does-level-accuracy-change- curvature-surfaces-increases
Oliver Steffen, M. Sc., Dipl.-Ing. Uwe Kaulbars, Institut für Arbeitsschutz der Deutschen Gesetzlichen Unfallversicherung (DGUV), Sankt Augustin.