Akkupacks für mobile Industrieroboter
Lange Lebensdauer, hohe Energiedichte und Widerstandsfähigkeit gegen Stöße und Vibrationen sind gängige Anforderungen an fahrerlose Transportsysteme und andere Arten mobiler Roboter. Um diese Anforderungen zu erfüllen, müssen die Zellchemie und das Design des Akkupacks richtig gewählt werden. Gute Hersteller dieser Akkus beraten ausführlich.
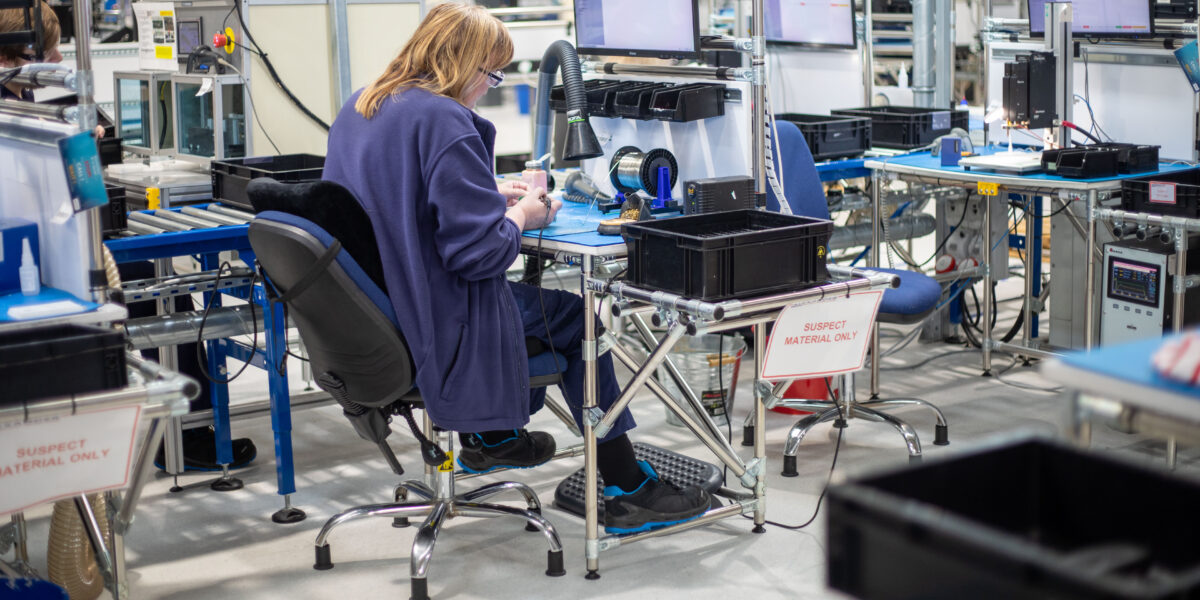
Eine Mitarbeiterin von Alexander Battery Technologies lötet sorgfältig Drähte an eine Leiterplattenbaugruppe. Ein wichtiger Schritt in der Herstellung von Akkupaketen.
Foto: Alexander Battery Technologies
Effizienz, Maximierung des Durchsatzes, Sicherheit und Senkung der Betriebskosten sind die Schlagworte der intelligenten, digitalisierten Fabriken und Lagerhäuser von heute. Um diese Ziele zu erreichen, automatisieren Industrieunternehmen immer mehr Prozesse und setzen dafür auch verschiedene mobile Roboter ein. Zu diesen gehören „Automated Guided Vehicles“ (AGV), also fahrerlose Transportsysteme für den Materialtransport und andere Anwendungen, „autonomous mobile robots (AMR), also automatisierte mobile Roboter für die Auslieferung auf der letzten Meile, als auch Rahmenkletterer in automatisierten Lagern.
Einer der Vorteile mobiler Roboter im Vergleich zu ihren menschlichen Kollegen ist die Fähigkeit, theoretisch, ohne Pausen einlegen zu müssen, 24 Stunden am Tag arbeiten zu können. Dies erfordert jedoch ein tragbares Batteriesystem, das eine kontinuierliche Leistung aufrechterhalten kann, ohne dass die Ladung zur Neige geht oder aufgrund einer Störung oder eines Ausfalls vorzeitig ausfällt.
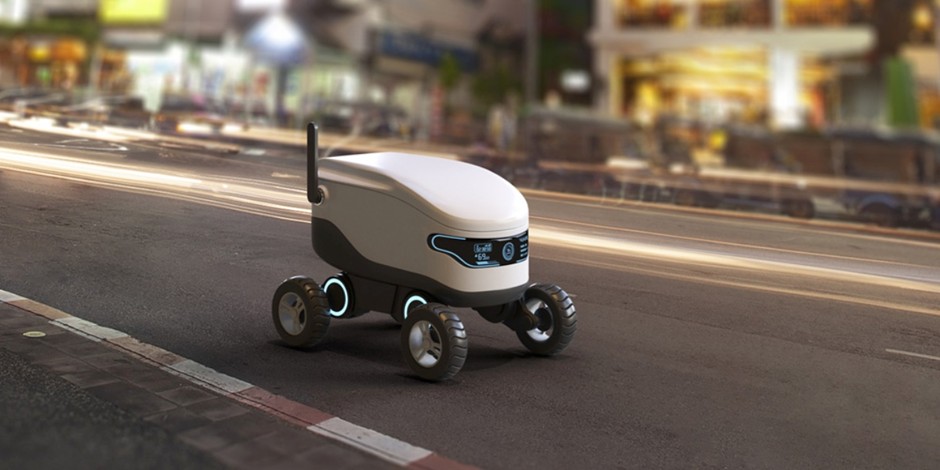
Autonome mobile Roboter (AMR) werden zunehmend eingesetzt, um menschliche Fahrerinnen und Fahrer bei der Zustellung von Paketen zu Haushalten und Büros zu ersetzen.
Foto: Infineon
Dies zeigt, wie wichtig die Qualität der Akkupakete mobiler Roboter ist. In fast allen Fällen benötigt ein solcher Roboter einen kundenspezifischen Akkupack, um die Anforderungen der Anwendung in Bezug auf Kapazität, Größe, Haltbarkeit und Robustheit, Spitzenleistung, Zykluslebensdauer, Temperaturtoleranz und andere Faktoren zu erfüllen. Dies bedeutet, die Wahl des richtigen Herstellers von kundenspezifischen Akkus ist eine wichtige Entscheidung.
Akkus auf Lithiumbasis sind heute die am häufigsten verwendeten für neue Industriebatterien. Sie haben eine hohe Energiedichte und Kapazität und erlauben eine viel längere Betriebszeit zwischen Ladevorgängen als jede andere Batteriechemie. In der Tat können viele Arten von Lithiumchemien in Batteriezellen verwendet werden, und die Technik und Produktion von Batteriezellen und -paketen wird ständig weiterentwickelt.
Was sind also die aktuellen Best Practices für die Spezifikation von Akkupacks, und was sind die wichtigsten Überlegungen, die Originalgerätehersteller, kurz OEM (Original Equipment Manufacturer), von mobilen Robotern heute bei der Spezifikation des Zellentyps, des Packdesigns und der Qualitätskriterien berücksichtigen sollten?
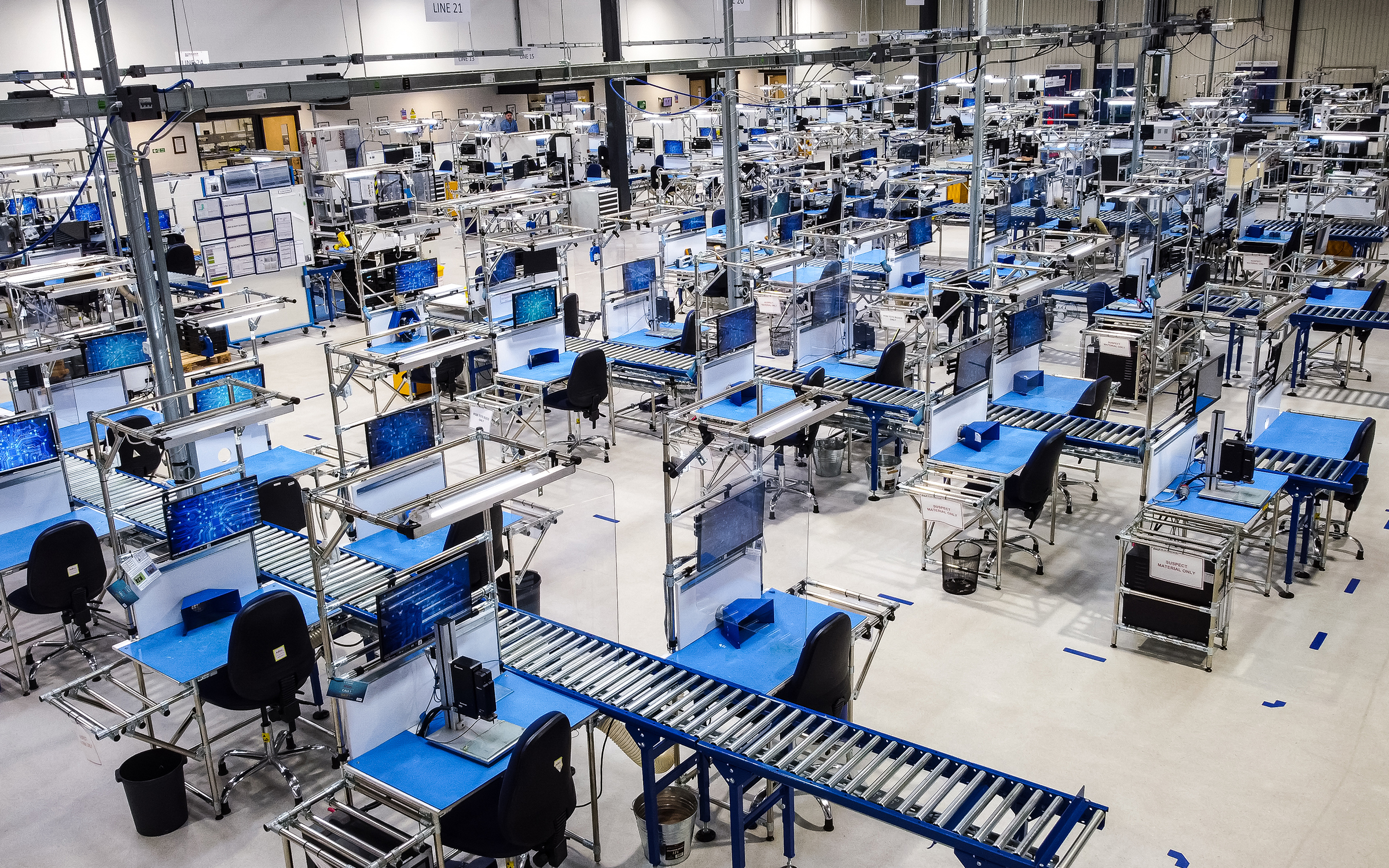
In dieser Werkshalle in Peterlee werden Batteriepacks effizient und skalierbar hergestellt.
Foto: Alexander Battery Technologies
Akkus: technische Kompromisse abwägen
Die zunehmende Verbreitung von Lithiumchemien und Komponenten wie Batterieladekontroll-ICs, die Lithium-Batteriepacks unterstützen, bedeutet, dass ein Roboter-OEM mit einer Reihe komplexer Kompromisse konfrontiert werden kann, die er berücksichtigen muss. Zellchemien wie Lithium-Nickel-Mangan-Kobalt-Oxid (NMC), Lithium-Eisenphosphat (LFP), Lithium-Titanat (LTO), Lithium-Mangan-Oxid (LMO) und Lithium-Kobalt-Oxid (LCO) unterscheiden sich in einer Reihe von Parametern.
Ein Parameter ist die Energiedichte, die sich auf die Größe und das Gewicht des Batteriesatzes auswirkt, und die maximale Spitzenleistung. Andere wichtige Parameter sind die sichere Betriebstemperatur, eine mögliche Anfälligkeit für thermisches Durchgehen, die Zykluslebensdauer sowie die nominale Ausgangsspannung und die maximale Ladegeschwindigkeit.
Energiedichte versus Ladezyklen
Die Entscheidung über das beste Paket muss für jede einzelne Anwendung getroffen werden. Bei einem kleinen AGV oder AMR, das leichte Lasten transportiert, macht das Batteriepaket in der Regel einen großen Teil des Gesamtgewichts des Roboters aus und nimmt im Verhältnis zum Robotergehäuse viel Platz in Anspruch: Hier ist eine hohe Energiedichte eine wichtige Anforderung, um eine möglichst kleine und leichte Batterie herzustellen, eine Anforderung, die im Allgemeinen den Einsatz von NMC-Zellen erfordert.
Bei einer großen mobilen Hebebühne beispielsweise, die Lasten von bis zu 1 000 kg bewegen kann, trägt die Batterie hingegen nur unwesentlich zur Gesamtgröße und zum Gewicht bei. Hier ist die Energiedichte von geringer Bedeutung, sodass der Plattform-OEM stattdessen LFP-Zellen wählen könnte: Ihre Energiedichte ist mindestens ein Drittel geringer als die von NMC, aber die Zyklenlebensdauer ist viel länger – mehr als 2 000 Zyklen, verglichen mit nur 500 bis 600 Zyklen in einigen NMC-Implementierungen. LFP-Zellen können auch bei viel höheren Temperaturen als NMC sicher betrieben werden, was die Anforderungen an die Wärmeableitung, die Wärmeüberwachung und die Sicherheitsschaltungen erleichtert.
Zyklusdauer und Ladezeit sind hingegen entscheidende Parameter für viele mobile Roboter: Fahrerlose Transportsysteme in einem intelligenten Lagerhaus zum Beispiel können das ganze Jahr über rund um die Uhr arbeiten. Eine typische Konfiguration verwendet einen austauschbaren Akkupack, der es dem FTS ermöglicht, zu einer Ladestation zurückzukehren, um einen entladenen Akkupack zu entfernen und durch einen neu geladenen Akkupack zu ersetzen.
In diesem Fall durchlaufen die Akkus kontinuierlich den Lade-/Entladevorgang und die Zellen im Akkupack müssen vielen Ladezyklen und einer schnellen Aufladung standhalten, damit sie nach der Entnahme aus einem FTS im entladenen Zustand schnell wieder einsatzbereit sind.
Ein seriöser Hersteller von Akkupacks wird detaillierte Hinweise zu diesen und allen anderen Leistungsmerkmalen jeder Lithiumchemie geben können und die beste Wahl für die mobile Roboteranwendung des OEMs empfehlen.
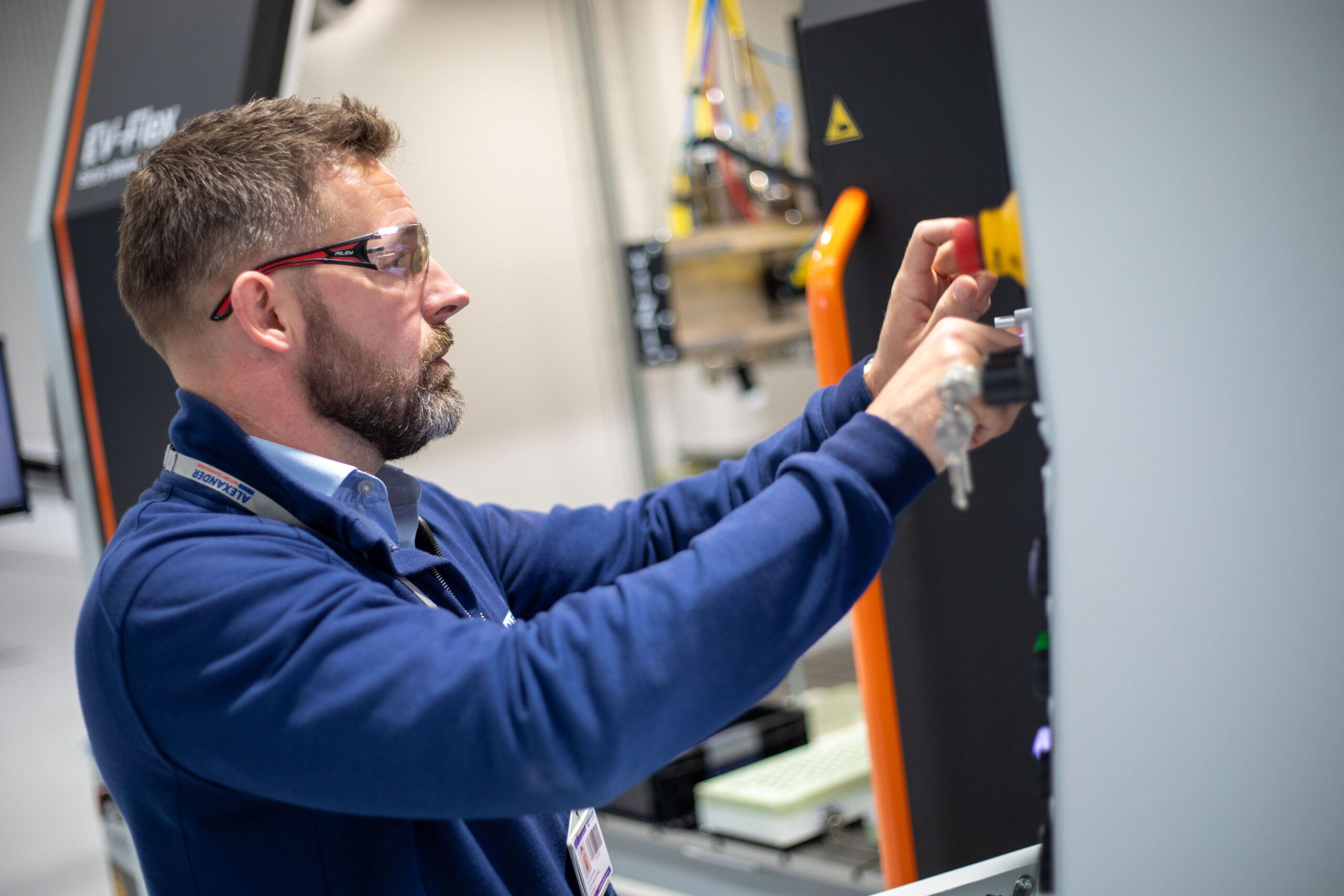
Der Produktionsleiter Brett Ramshaw bedient ein Laserschweißgerät für präzises und zuverlässiges Schweißen des Batteriepacks.
Foto: Alexander Battery Technologies
Spezifikation des Akkupacks
Die Wahl der Chemie ist nur der Anfang des Prozesses der Beschaffung des richtigen Akkupacks für einen mobilen Roboter. Die Bewertung eines Herstellers von kundenspezifischen Akkupacks wird sich normalerweise auf die Fragen der Funktionen und der Qualität konzentrieren.
Der Akkupack-Hersteller sollte die Anwendung des Roboter-OEMs mit den entsprechenden Fähigkeiten und Merkmalen unterstützen. Dazu könnten gehören:
- Thermomanagement-Merkmale: Beim Entladen der Batterien entsteht Abwärme, die abgeführt werden muss, um die Betriebstemperatur des Akkus auf einem sicheren Niveau zu halten. Ausgeklügelte Konstruktionen verwenden innovative Zellanordnungen, um die Wärme effizient abzuführen, wodurch der Bedarf an Kühlkörpern reduziert oder ganz vermieden werden kann. Das spart Platz, Gewicht und Kosten. Ebenso müssen mobile Roboter, die in einer kalten Umgebung wie in einem Kühllager arbeiten, die Temperatur der Batterie berücksichtigen: Eine Lithiumzelle kann normalerweise nicht geladen werden, wenn sie kälter als 0 °C ist. Dies kann den Einsatz einer aktiven In-Pack-Heiztechnologie erfordern, um die Zellentemperatur zur Vorbereitung des Ladevorgangs über 0 °C anzuheben. Bei vielen Anwendungen ist die aktive Heizung eine bessere Lösung als das Abstellen des Akkus in einem Raum mit Raumtemperatur und das Warten darauf, dass er Wärme aus der Umgebungsluft aufnimmt.
- Telematik: Ein Fabrikbetreiber kann eine Flotte von AGVs oder anderen mobilen Robotern effektiver steuern, wenn er Zugang zu Daten über den Lade- und Gesundheitszustand der einzelnen Akkus hat. Fortschrittliche kundenspezifische Akkupacks können drahtlose Konnektivität beinhalten wie ein Bluetooth-Low-Energy-Funkgerät, das so konfiguriert ist, dass es Echtzeitdaten über den Ladezustand, die Batterietemperatur und andere wichtige Parameter liefert.
- Gesetzliche Vorschriften und Genehmigungen einhalten: Der rechtliche Rahmen, in dem ein Batteriedesign entwickelt wird, hängt von den Ländern oder Regionen ab, in denen das Akkupack verwendet werden soll. Die Regulierung ist ein sich schnell veränderndes Feld, zu dem der Hersteller des Akkupacks in der Lage sein sollte, aktuelle Ratschläge zu geben. So wurden beispielsweise durch Änderungen der US-Vorschriften die Anforderungen an Zellen und Batteriepacks in mobilen Robotern wie FTS verschärft und an die Vorschriften für batteriebetriebene Elektroautos angeglichen. Das Design eines Herstellers von kundenspezifischen Akkupacks sollte einen reibungslosen Weg durch die Prüfung, Zulassung und Zertifizierung für jeden Teil der Welt bieten, in dem der Roboter-OEM seine Produkte vermarkten möchte.
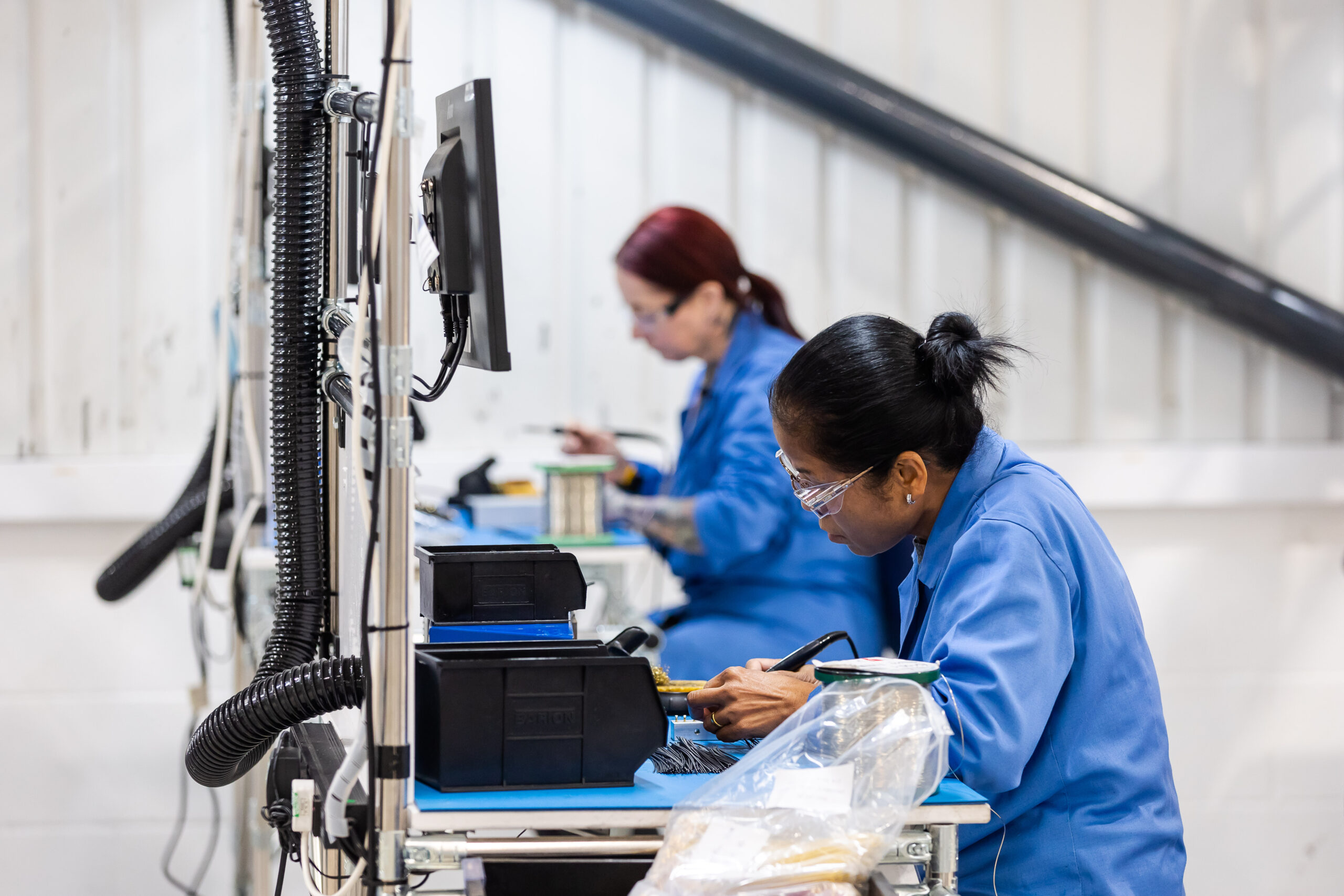
Mitarbeiterinnnen bereiten Kabelbäume für die Montage von Batteriepaketen vor.
Foto: Alexander Battery Technologies
Zuverlässige Akkupacks
Nach der Festlegung der Zellchemie und der richtigen Merkmale erstellt der Hersteller des Akkupacks ein Design für das Produkt. Wenn die Tests und die Genehmigung der endgültigen Prototypen abgeschlossen sind, geht das Akkupack in Produktion. Zu diesem Zeitpunkt ist der Erstausrüster dem Hersteller des Akkupacks ausgeliefert – es gibt keine zweite Quelle für ein kundenspezifisches Akkupack.
Bei der Herstellung von Akkus ist Qualität jedoch kein aufgeschraubtes Merkmal oder ein Kontrollverfahren, das am Ende der Produktionslinie angewandt wird: Wenn die Qualität nicht von Anfang an in den gesamten Prozess integriert ist, werden die Produktionseinheiten, die das Band verlassen, mangelhaft sein.
Die drei größten Hersteller der Welt von Li-Ionen-Zellen – als da sind Samsung und LG aus Südkorea sowie E-One Moli Energy aus Taiwan – testen alle Zellen auf die Einhaltung aller relevanten Sicherheits- und Compliance-Anforderungen. Für die Qualität und Sicherheit der besten Zellen ist ein Aufschlag auf die Stückkosten im Vergleich zu Zellen von Nicht-Markenherstellern zu zahlen, aber diese Vorlaufkosten werden durch die längere Lebensdauer und die überlegene Sicherheitsgarantie der teureren Zellen mehr als wettgemacht.
Gesicherte Qualität aus England
Der britische Batteriehersteller Alexander Battery Technologies aus Peterlee in England südlich von Newcastle hat beispielsweise sichere Liefervereinbarungen mit diesen drei führenden Zellenherstellern und verwendet in seinen Akkus nur Zellen dieser Hersteller. Die Anwendung von Qualitätsgrundsätzen sollte auch während des gesamten Produktionsprozesses erkennbar sein. Bei der Montage achten die Hersteller hochwertiger Akkus besonders auf die störanfälligsten Elemente der Struktur wie Schweißnähte: Fortschrittliche optische Inspektionstechniken sollten gewährleisten, dass die Schweißnähte hohe Mindestanforderungen an Größe und Unversehrtheit übertreffen, um sicherzustellen, dass die elektrischen Verbindungen des Akkus auch bei extremen Stößen oder Vibrationen, wie sie in der Anwendung auftreten, einwandfrei bleiben.
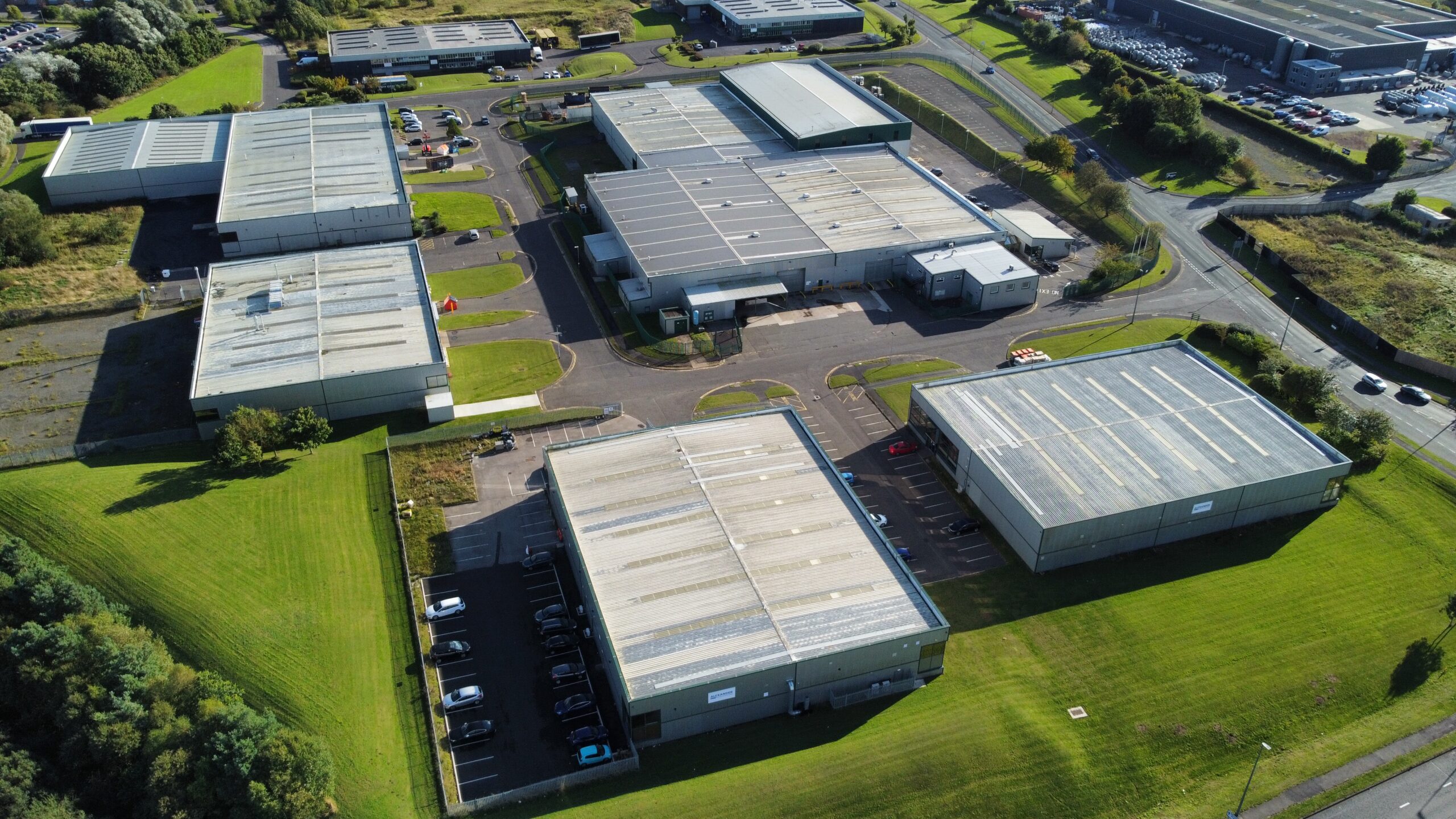
Das Werksgelände von Alexander Battery Technologies in Peterlee, Großbritannien, aus der Vogelpersektive. Zu sehen sind die Einheiten 1, 2 und 4.
Foto: Alexander Battery Technologies
Einige Hersteller folgen der von Alexander Battery Technologies eingeführten Praxis, ihre Kunden einzuladen, ihre Produktionsanlagen im Detail zu inspizieren. Moderne Softwaresysteme für das Enterprise Resource Planning (ERP), können auch eingesetzt werden, um Kunden die Möglichkeit zu geben, die Produktionsleistung seiner Akkus Stück für Stück zu überwachen und zu prüfen.
Qualitativ hochwertiges Design und Produktion unterstützen zudem eine schnelle und vor allem richtige Validierung und Zertifizierung von Batteriepacks nach den hohen Standards, die in Branchen wie der Automobilindustrie gelten.
Der Vormarsch digitalisierter und intelligenter Fertigungs- und Lagerpraktiken führt zu einem raschen Anstieg der Anzahl und Vielfalt mobiler Roboter in der Industrie. Die Betreiber verlassen sich darauf, dass diese Roboter rund um die Uhr ununterbrochen in Betrieb sind; unvorhergesehene Ausfallzeiten beeinträchtigen den Durchsatz und die Effizienz erheblich.
Die Batteriestromversorgung kann so zuverlässig sein wie jede andere Komponente eines mobilen Roboters: Die obige Anleitung zeigt, wie durch sorgfältige Beachtung der Zell- und Batteriespezifikation, des Designs und der Produktion sowie durch die Wahl eines zuverlässigen Pack-Herstellers eine zuverlässige und vorhersehbare Leistung über die gesamte Lebensdauer des Roboters gewährleistet werden kann.
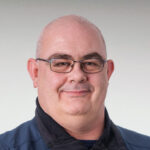
Owen McNally ist leitender Entwicklungsingenieur bei Alexander Battery Technologies
sales@alexenergy.co.uk