Batteriefertigung flexibel an den Markt anpassen
Die Produktion von Lithium-Ionen-Batteriezellen läuft bislang meist über starre Transferstraßen, bei denen sämtliche Prozessschritte, von der Herstellung der Elektrodenpasten bis hin zur Formierung der Zellen, in einer fest vorgegebenen Reihenfolge und Taktzeit ablaufen. Das erlaubt zwar eine effiziente und kostengünstige Massenproduktion, schränkt aber gleichzeitig die Flexibilität erheblich ein. Das Karlsruher Institut für Technologie (KIT) hat nun die erste automatisierte, agile Batteriezellenfertigung in Betrieb genommen, die sich flexibel den Erfordernissen des Marktes anpassen kann.
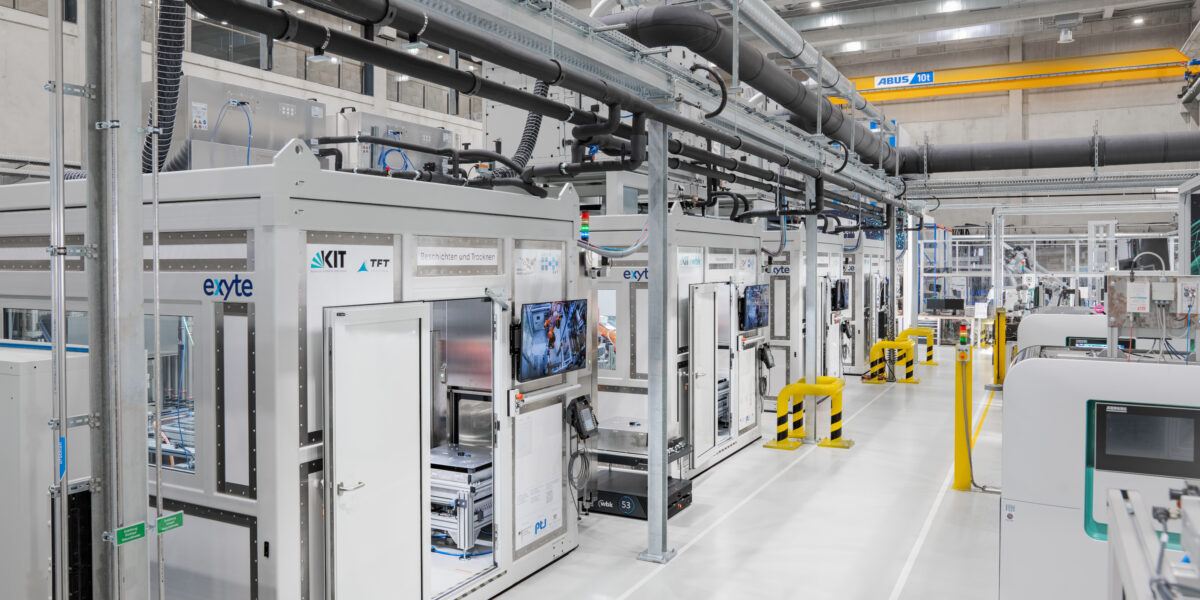
Pilotlinie einer agilen und modular aufgebauten Batteriezellfertigung in der Karlsruher Forschungsfabrik.
Foto: Amadeus Bramsiepe/KIT
Vor allem angesichts der immer kürzeren Lebenszyklen von Produkten, die mit Batteriezellen betrieben werden, wird die Starrheit bisheriger Fertigungsstraßen für Batteriezellen zunehmend zum Problem. Insbesondere im Bereich der Unterhaltungs- und Kommunikationselektronik, wo alle sechs bis zwölf Monate neue Generationen auf den Markt kommen, ändern sich die Anforderungen an die Batteriezellen ständig. Neue Bauräume und Zellformate sowie verbesserte Materialeigenschaften stellen die Produktion vor große Herausforderungen. Diese schnellen Innovationszyklen erfordern flexible Produktionssysteme, die sich leicht an neue Anforderungen anpassen lassen. Gleichzeitig ist es wichtig, ein tiefgehendes Verständnis der zugrunde liegenden Produktionsprozesse zu haben, um diese Anpassungen effizient und mit hoher Qualität umsetzen zu können.
Ein weiteres Problem, das durch die starren Systeme entsteht, ist die sogenannte Anlaufproblematik. Neue Produktgenerationen erfordern häufig eine Anpassung der Produktionssysteme, die mit unerwarteten Herausforderungen verbunden ist. Das liegt vor allem daran, dass sich Ergebnisse aus Labortests oft nicht direkt auf Großanlagen übertragen lassen. Die Korrelationen zwischen Materialien und Maschinen verhalten sich auf unterschiedlichen Fertigungsgrößen oft nicht linear, was zu Problemen bei der Hochskalierung führen kann. So kann es vorkommen, dass Werkzeuge zur Herstellung neuer Zellformate nicht in die bestehenden Anlagen passen. In solchen Fällen müssen ganze Produktionslinien ausgetauscht werden, was mit hohen Kosten und langen Ausfallzeiten verbunden ist.
Skalierungen in der Batteriefertigung leicht umsetzbar
Am KIT wurde seit 2020 an einer Fertigungsstraße gebaut, die die Flexibilität in der Produktion gewährleisten soll und gleichzeitig demonstrieren soll, dass agile Systeme in industriellem Umfeld wirtschaftlich betrieben werden können. Ermöglicht wurde das durch eine Förderung des Bundesministeriums für Bildung und Forschung (BMBF) in Höhe von knapp 14,5 Mio. € und des Ministeriums für Wissenschaft, Forschung und Kunst Baden-Württemberg (MWK) in Höhe von 4,5 Mio. €. Über 30 Wissenschaftlerinnen und Wissenschaftler sind an diesem Projekt beteiligt.
Das Projekt „AgiloBat2“ entwickelt ein neues, flexibles Produktionskonzept für Lithium-Ionen-Batteriezellen. Das Ziel besteht darin, durch agile Anlagenproduktion Zellen für unterschiedliche Branchen in unterschiedlichen Stückzahlen und Formaten fertigen zu können. Dieses Konzept bietet eine hohe Anpassungsfähigkeit an unterschiedliche Anforderungen und ermöglicht es, Produktionsprozesse effizient und kostengünstig umzurüsten. Dies wird durch ein modulares System erreicht, bei dem die Produktionsmodule schnell und einfach gewechselt werden können.
ZF und Infineon optimieren mit KI die Fahrdynamik
Ein wichtiger Meilenstein in diesem Projekt ist der Aufbau einer agilen Batteriezellfertigung in der Karlsruher Forschungsfabrik. Hier wurde eine innovative Produktionsumgebung geschaffen, die aus modularen, kranbaren Einheiten besteht. Diese sogenannten Microenvironments sind 3 x 3 x 2,5 m groß und mit dezentraler Klimatechnik ausgestattet, die es ermöglicht, Taupunkttemperaturen von bis zu – 50 °C einzustellen. Dies ist besonders wichtig für die Verarbeitung von feuchtigkeitsempfindlichen Materialien, die in modernen Batteriezellen häufig verwendet werden. Die Produktionsmodule können leicht ausgetauscht und rekonstruiert werden, da die Dächer der Microenvironments abgenommen und die Module per Kran ein- und ausgebracht werden können. Diese Flexibilität ermöglicht es, schnell auf technologische Änderungen zu reagieren und die Produktionsprozesse entsprechend anzupassen.
Flexible Module für fast alle Batterieformate
Die Produktionsmodule sind so konzipiert, dass sie eine breite Palette von Zellformaten abdecken können – etwa 80 % der am Markt verfügbaren Pouch-Zellen können nach Angaben des KIT mit diesen Modulen gefertigt werden. Die Module selbst sind über standardisierte Schnittstellen miteinander verbunden, was den Wechsel und die Anpassung erleichtert. Zudem sind die Produktionsprozesse weitgehend automatisiert, sodass menschliches Eingreifen nur bei Umrüstvorgängen erforderlich ist. Ein fahrerloses Transportsystem (FTS) übernimmt den Materialfluss zwischen den einzelnen Roboterzellen. Das FTS transportiert die Halbzeuge in diffusionsdichten Transportboxen und übergibt diese automatisch an die Materialschleusen der Microenvironments.
Akkupacks für mobile Industrieroboter
Zusätzlich zum physischen Aufbau der Anlage wurde auch ein digitaler Zwilling entwickelt, der die gesamte Produktionslinie in einer Simulationssoftware abbildet. Dieser digitale Zwilling ermöglicht es, die Produktionsprozesse virtuell zu optimieren und Skaleneffekte durch das Hinzufügen oder Entfernen von Modulen zu simulieren. Bottlenecks können so frühzeitig erkannt und behoben werden. Das Modell dient nicht nur der Planung, sondern wird auch während des Betriebs genutzt, um die Produktion effizient zu steuern. Die Produktionsplanung erfolgt dabei in Kombination mit einer zentralen Datenbank, die alle relevanten Prozessparameter speichert. So können Prozesszeiten abgeschätzt und Aufträge optimal verwaltet werden.
Nach dem Projektabschluss im Oktober 2024 nimmt die Forschungsfabrik nun ihre Produktion auf.