Prozessgase aus der Stahlproduktion energetisch genutzt
Die bei der Stahlproduktion anfallenden Prozessgase sind wertvolle Energiequellen, die sich für eine effiziente Strom- und Wärmeerzeugung im Kraftwerk nutzen lassen. Für den Stahlhersteller, der häufig auch der Kraftwerksbetreiber ist, führt die Nutzung dieser Gase zu wirtschaftlichen Vorteilen, da er den Einsatz anderweitiger fossiler Energieträger verringern kann. Ein zusätzlicher Anreiz besteht darin, dass die energetische Nutzung der Prozessgase CO2-kostenneutral erfolgt, da die Stahlherstellung selbst bereits mit CO2-Kosten belastet wird. Der Beitrag schildert Betriebserfahrungen mit gichtgasbefeuerten Dampferzeugeranlagen, dargestellt am Beispiel der Vulkan Energiewirtschaft Oderbrücke GmbH (VEO) in Eisenhüttenstadt.
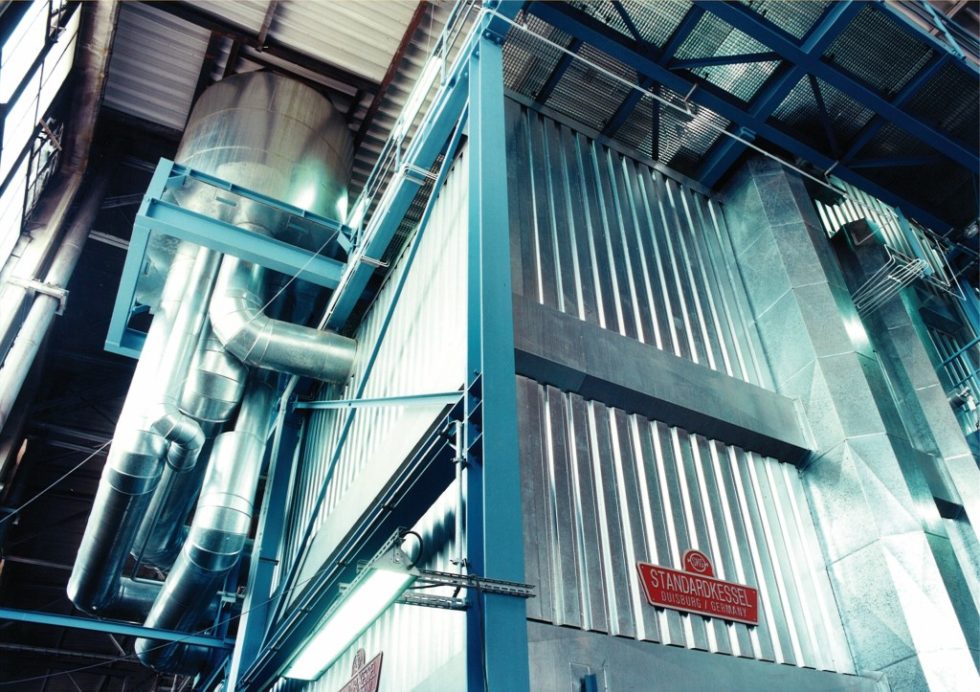
Kesselanlage der Vulkan Energiewirtschaft Oderbrücke GmbH (VEO) in Eisenhüttenstadt. Bild: Standardkessel
Bei der Stahlerzeugung fallen aufgrund der unterschiedlichen Verfahrensstufen zwei unterschiedliche Gassorten als Nebenprodukte an, die unter den Bezeichnungen Gichtgas und Konvertergas bekannt sind. Wird gleichzeitig noch eine Kokerei betrieben, fällt zusätzlich auch noch Koksgas an, das energetisch genutzt werden kann. Die Zusammensetzung dieser Prozessgase unterscheidet sich je nach Herkunft beträchtlich und damit auch die verbrennungstechnischen Eigenschaften wie Brennwert, Flammentemperatur, Wobbe-Index usw. Im Vergleich zum Erdgas haben die Gase eine schwankende Zusammensetzung, einen geringeren Heizwert und somit niedrige Flammentemperaturen. Verfahrenstechnisch problematischer sind jedoch die oft erheblichen Schwankungen bei Gasmenge und Zusammensetzung der einzelnen Gase in Abhängigkeit von der Produktion (Tabelle 1).
Darüber hinaus finden sich in den Gasen zahlreiche Verunreinigungen, vor allem in Form von H2S, NH3, HCN, Benzol BTX, Teer und Stäuben.
In Eisenhüttenstadt fällt Gichtgas und Konvertergas an und wird gegebenenfalls mit Erdgas aufgefettet. Auch das Konvertergas steht nicht permanent zur Verfügung. Zusammenfassend wird das Gemisch der eingangs genannten Gase als „Hüttengas“ bezeichnet.
Hüttengaskessel VEO Eisenhüttenstadt
Kesselkonzept
Am Standort Eisenhüttenstadt wurde im Jahre 1997 im Auftrag der VEO ein Dampferzeuger (Kessel 4) zur energetischen Nutzung der Prozessgase des benachbarten Stahlwerkes errichtet. Als Brennstoff steht Hüttengas als Mischung aus Gichtgas mit maximal 10 % Konvertergas aus dem Stahlwerk zur Verfügung. Alternativ kann die Anlage auch mit Erdgas betrieben werden.
Der Dampferzeuger wurde in stehender Vertikalbauweise als Dreizugkessel konzipiert und im Naturumlauf geschaltet (Bild 1).
Die Überhitzerheizflächen sind in drei Stufen aufgeteilt mit zwei dazwischen liegenden Einspritzkühlern zur Heißdampftemperaturregelung. Die Speisewasservorwärmung erfolgt in einem nachgeschalteten Rippenrohrvorwärmer. Die Kesselkonstruktion war dabei auf die im Kesselhaus vorhandenen Platzverhältnisse anzupassen. Dies beinhaltete auch die Einbindung des Rauchgaskanals in einen der vorhandenen Schornsteine, um das äußere Erscheinungsbild des Kraftwerkgebäudes nicht zu verändern. Die Kesselanlage wurde für die in Tabelle 2 abgebildeten technischen Daten konzipiert.
Der Dampferzeuger ist mit einer kombinierten Hüttengas-/Erdgasfeuerungsanlage ausgerüstet. Die vier Brenner sind als Drallbrenner ausgeführt, die im Kesselboden angeordnet sind.
Zur Überwachung der Flamme sind je Brenner zwei Flammenwächter vorgesehen, die bei Erlöschen der Flamme die Schnellschlussorgane vor dem Brenner schließen und sofort die Brennstoffzufuhr unterbrechen.
Die Regelung der Feuerung erfolgt mittels Brennstoff-/Luftverhältnisregelung gemeinsam für alle Brenner, ebenso die Zuführung von rezirkuliertem Rauchgas im Erdgasbetrieb (Bild 2).
Aufgrund des niedrigen Gasvordrucks an der Liefergrenze war die Installation eines drehzahlgeregelten Hüttengasverdichters erforderlich, um einen ausreichend hohen und konstanten Förderdruck des Hüttengases gewährleisten zu können. Trotz dieser Maßnahme war der Regelbereich der Brenner auf 1 : 3 zu begrenzen, da ein größerer Regelbereich zwangsläufig einen höheren gasseitigen Druckverlust im Brenner bedingt, was wiederum den Eigenbedarf des Hüttengasverdichters in die Höhe treiben würde.
Betrieb mit Stützgas
Zur Stabilisierung der Brennerflamme wird permanent eine definierte Menge an Stützgas zugefeuert. Hierzu wird Erdgas verwendet.
Verbrennungsluft
Der Kessel ist für einen rauchgasseitigen Überdruckbetrieb ausgelegt. Somit liefert das drallgeregelte Frischluftgebläse die Gesamtpressung zur Überwindung sämtlicher luft- und rauchgasseitiger Widerstände.
Rauchgasrezirkulation
Zur Reduzierung der NOX-Emissionen und zur Anhebung der Frischdampftemperatur bei Teillast wird im Erdgasbetrieb Rauchgas hinter Eco entnommen und den Brennern zugeführt.
Betriebserfahrungen
Kesselkonstruktion
Die Ausführung der Kesselanlage als von unten unterstützter Kessel mit Bodenfeuerung hat sich sehr gut bewährt. Die Bodenfeuerung führt zu einer sehr gleichmäßigen Heizflächenbelastung im Feuerraum, da sich die Flammen parallel zu den Umfassungswänden ausbilden. Punktuelle Wandbelastungen, die zu einem erhöhten Materialverschleiß führen könnten, werden sicher vermieden. Konvektionsheizflächen sind erst im zweiten Kesselzug, also außerhalb des Einstrahlungsbereiches der Feuerung, angeordnet. Diese Maßnahme führt zu einer geringeren Materialbelastung der Überhitzerheizflächen beim Anfahren, aber auch im Dauerbetrieb.
Der Kessel wird 8 500 bis 8 600 Betriebsstunden pro Jahr mit häufig variierender Last gefahren. Der Kesselkonvektionszug wird routinemäßig einmal jährlich rauchgasseitig gereinigt. Dabei werden die Heizflächen mit Hochdruckwasser abgespritzt. Der Feuerraum wird nicht gereinigt. Die Verschmutzungsneigung der Heizflächen ist als gering einzuschätzen, ein nennenswerter Anstieg der Abgastemperatur liegt nicht vor.
Feuerung/Brennstoffsystem
Aufgrund des relativ niedrigen Heizwertes von Hüttengas und dem daraus resultierenden großen Volumenstrom in Verbindung mit dem üblicherweise niedrigen Vordruck des Gases benötigen Hüttengasbrenner deutlich größere Querschnitte als etwa Erdgasbrenner. Dies bedeutet, dass Hüttengasbrenner einer größeren Einstrahlung aus dem Feuerraum ausgesetzt sind, was zu einer höheren thermischen Belastung der dem Feuerraum zugewandten Teile führt. Im vorliegenden Fall führte dieser Effekt anfänglich zu Verzunderungsproblemen an Brennereinbauten, da diese zu heiß wurden. Durch Einsatz höherwertigerer Materialien sowie eine modifizierte Verbrennungsluftaufgabe, die eine verbesserte Kühlung der Brennereinbauten bewirkte, ließen sich die Probleme dauerhaft lösen.
Aufgrund des generell niedrigen Heizwertes von Hüttengas, der prozessbedingt deutliche Schwankungen nach oben und unten aufweist, war von Anfang an die Installation einer permanenten Stützfeuerung mit Erdgas vorgesehen. Es zeigte sich, dass die zunächst getroffene Annahme zum Stützgasverbrauch in Höhe von unter 1 % der Feuerungswärmeleistung zu optimistisch gewesen war. Um eine stabile Flamme auch bei sehr niedrigen Heizwerten sicherzustellen, hat sich eine Stützfeuerungsleistung von rund 3,8 % der Feuerungswärmeleistung als erforderlich herausgestellt.
Die Rauchgasemissionen der Kesselanlage ließen sich jederzeit problemlos beherrschen. Sowohl der NOX– als auch der CO-Grenzwert liegen immer, in der Regel sehr deutlich, unter den zulässigen Grenzwerten. Dies gilt auch für den Betrieb mit Erdgas, wobei dann jedoch die Frischluftvorwärmung zur Einhaltung der NOX-Emissionen außer Betrieb genommen werden muss.
Eine dauernde Herausforderung in hüttengasgefeuerten Kesselanlagen stellt der Feuchtegehalt im Brenngas dar. Durch die Abkühlung des wasserdampfgesättigten Hüttengases kondensiert ein Teil der Feuchtigkeit in den Rohrleitungen des Transportweges. Es ist daher sehr wichtig, ein geeignetes Entwässerungskonzept vorzusehen, das nicht nur anfallendes Kondensat permanent abführt, sondern auch dafür sorgt, dass kein Wasser in die Feuerung eingetragen wird.
Verfügbarkeit
Mit den bereits beschriebenen Maßnahmen konnte ein Anlagenbetrieb mit sehr hoher Verfügbarkeit realisiert werden, die im Durchschnitt Werte von 99 % erreichte. Hierzu hat auch das erfahrene Betriebspersonal durch kontinuierliche Beobachtung und Pflege der Anlage wesentlich beigetragen.
Neuer Gichtgaskessel
Durch die Vulkan Energiewirtschaft Oderbrücke GmbH wurde das Industriekraftwerk am Standort Eisenhüttenstadt in den Jahren 2011 und 2012 weiter modernisiert.
In diesem Rahmen wurde auch ein neuer mit Hüttengas gefeuerter Kessel als Ersatz für die bestehenden Dampferzeuger 1 bis 3 errichtet. Der neue Gichtgaskessel (K7) wurde für die gleichen Dampfparameter wie Kessel 4 ausgelegt, erzeugt mit 180 t/h jedoch 50 % mehr Dampf (Tabelle 3).
Um den Wirkungsgrad des Kraft-Wärmeprozesses zu verbessern und um den Stützgasverbrauch der Kesselfeuerung zu reduzieren, wurden jedoch zusätzliche Maßnahmen vorgesehen. So wurde zusätzlich zur Verbrennungsluft auch für das Gichtgas ein dampfbeheizter Vorwärmer installiert Beide Vorwärmer werden unter anderem mit Entnahmedampf aus der ebenfalls neuen Dampfturbine beheizt.
Ziel dieser Maßnahmen ist es, den Kessel ohne Stützgaseinsatz zu fahren. Solange der Heizwert des Hüttengases über einem definierten Wert liegt, ist kein Stützgas erforderlich. Erst bei erwartetem Absinken unter den Grenzwert wird die Stützfeuerung zugeschaltet. Hierzu wird Erdgas eingesetzt. Das Signal zur Zuschaltung der Stützfeuerung erfolgt aus einer bauseits vorhandenen Wobbezahlmessung.
Erste Betriebserfahrungen
Nach rund zehnmonatiger Betriebszeit liegen die ersten Betriebserfahrungen mit dem neuen Kessel K7 vor. Erwartungsgemäß wurden die geplante Dampfleistung und die vorgesehenen Dampfparameter sofort erreicht. Die im April 2013 durchgeführten Abnahmemessungen zeigten, dass auch die zugesagten Kesselwirkungsgrade in allen Lastpunkten sicher erreicht werden (Tabelle 4).
Die Messung der Abgasemissionen zeigte ein differenziertes Ergebnis auf. Entsprechend den Vorgaben der 13. BimSchV waren die Werte in Tabelle 5 für das Hüttengas bzw. den Erdgasbetrieb einzuhalten.
Die Messungen ergaben CO-Werte, die weit unterhalb der zulässigen Grenzwerte lagen. Dies betraf alle Volllast- sowie Teillastfälle und beide Brennstoffe. Die NOX-Werte stellten sich ebenfalls deutlich unterhalb der zulässigen Werte ein. Lediglich im Erdgasbetrieb mit Luftvorwärmung auf 150 °C ergab sich ein NOX-Wert, der mit 118 mg/m3 oberhalb des Grenzwertes lag. Weitere Versuche zeigten jedoch, dass der Grenzwert mit abgesenkter Lufttemperatur sicher unterschritten werden konnte.
Übergangsverhalten
Eine wichtige Anforderung an Anlagen, die für mehrere Brennstoffe konzipiert sind, besteht im Übergangsverhalten der Anlage beim Brennstoffwechsel. Dies gilt insbesondere, wenn diese Brennstoffe sich im Brennverhalten und im Heizwert so stark unterscheiden, wie Hüttengas und Erdgas. Während der heißen Inbetriebsetzung der Kesselanlage wurde ein erheblicher Zeitaufwand eingesetzt, dieses Übergangsverhalten zu optimieren. Die Bilder 3 bis 5 zeigen, wie nach schrittweiser Veränderung der Brennereinstellungen schließlich eine Betriebsweise gefunden werden konnte, die ein flüssiges und unterbrechungsfreies Umschalten ermöglicht.
Bild 3 zeigt einen Brennstoffwechselvorgang von reinem Hüttengasbetrieb auf reinen Erdgasbetrieb und wieder zurück in etwa 30 Minuten. Die Messungen zeigen, dass die Heißdampftemperatur in einem engen Schwankungsbereich zwischen 528 und 536 °C gehalten werden kann. Der Dampfdruck bleibt während des gesamten Wechselvorgangs konstant auf seinem Solldruck (Bild 4). Die Heißdampfmenge bewegt sich – von 146 t/h ausgehend – zwischen 136 und 160 t/h, was für das nachgelagerte Wasser-Dampfsystem und die Dampfturbine als unproblematisch anzusehen ist (Bild 5).
Die eingesetzte Anlagentechnik erwies sich in den ersten Betriebsmonaten als zuverlässig. Probleme gab es lediglich mit der Dichtigkeit des Gasvorwärmers. Dieser ist so konzipiert, dass die Wärmeaustauscherheizfläche während eines Anlagenstillstandes ausgebaut und durch eine Reserveheizfläche ersetzt werden kann. Dieser Austauschvorgang ist in acht Stunden zu vollziehen. Es zeigte sich, dass die hierfür erforderlichen Flanschdichtungen nur begrenzt haltbar sind und nach zwei bis drei Monaten ersetzt werden müssen. Eine dauerhafte konstruktive Lösung ist in Vorbereitung und wird beim nächsten geplanten Anlagenstillstand installiert.
Mit einer sehr hohen Verfügbarkeit bereits in den ersten zehn Betriebsmonaten hat die Anlage die an die Versorgungssicherheit gestellten Anforderungen bisher im vollen Umfang erfüllt.
Dipl.-Ing. Wolfgang Zihla, Jahrgang 1951, Studium Allgemeiner Maschinenbau an der Ruhr-Universität Bochum. Projektleiter bei der Standardkessel GmbH, Duisburg.