Stationäre thermodynamische Prozesssimulationen am Beispiel eines Industriekraftwerks
Um bauliche Veränderungen in bestehenden Kraftwerksprozessen auf ihre Wirkungsweise untersuchen und thermodynamisch beziehungsweise wirtschaftlich bewerten zu können, werden thermische Kraftwerksprozesse mit geeigneter Simulationssoftware abgebildet und in verschiedenen Detaillierungsstufen ausgelegt oder nachgerechnet. Im Folgenden wird ein Weg aufgezeigt, wie mit Hilfe einer stationären Simulationssoftware die Gesamtjahresbilanz eines Kraftwerks vorausberechnet werden kann. Mit Hilfe von Prozessdaten aus Vorjahren wird nachgewiesen, dass das Berechnungsmodell das bestehende Kraftwerk mit einer Abweichung von weniger als drei Prozent bezüglich erzeugter elektrischer Leistung und Brennstoffeinsatz und bei bekannter Dampfproduktion abbilden kann. Das so verifizierte Modell kann zur Untersuchung von Zubaumaßnahmen oder Veränderungen im Kraftwerksprozess eingesetzt werden.
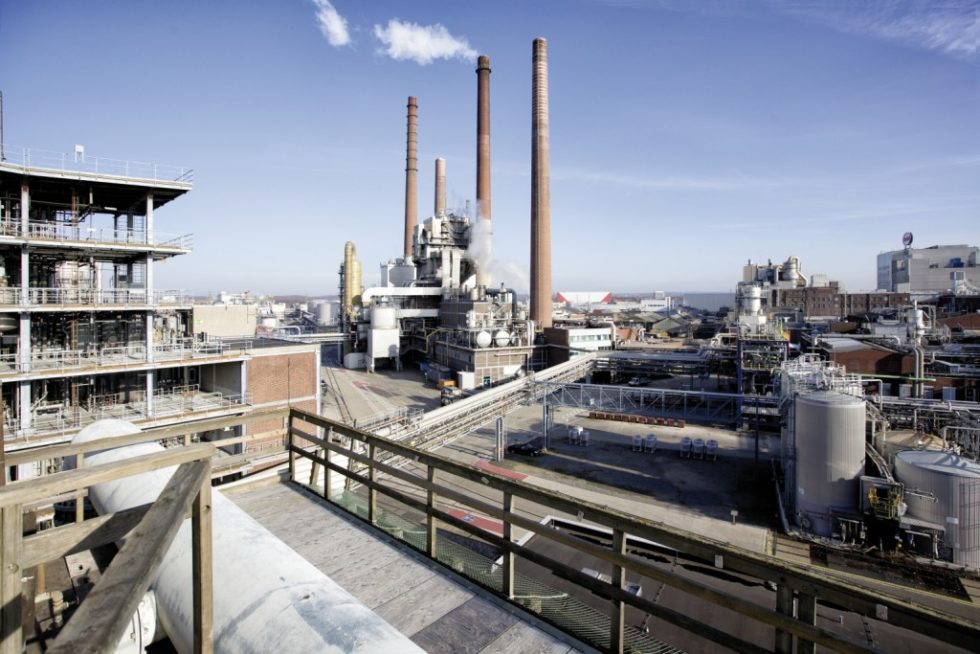
Bild: Henkel
Zur Bereitstellung von thermischer und elektrischer Energie für die Produktionsprozesse der Firma Henkel AG & Co. KGaA verfügt der Standort Düsseldorf Holthausen über ein werkseigenes Kraftwerk, das nach dem Prinzip der Kraft-Wärme-Kopplung arbeitet. Das Kraftwerk wird wärmegeführt betrieben und erzeugt je nach Bedarf im Industriepark Dampf in vier verschiedenen Druckstufen. Die dabei zusätzlich erzeugte elektrische Energie wird ebenfalls zur Deckung des Strombedarfs am Standort verwendet. Bild 1 zeigt eine schematische Darstellung des Kraftwerksprozesses.

Bild 1 Schematische Darstellung des Kraftwerkes am Standort Düsseldorf-Holthausen. Bild: eigene Darstellung
Zur Untersuchung von Zubaumaßnahmen und Kapazitätsveränderungen wurde mit Hilfe der Software „Ebsilon Professional“ ein Modell des bestehenden Kraftwerks erstellt. Dieses bildet den Prozess im Hinblick auf dessen äußere Bilanzgrenze wirklichkeitsgetreu ab und liefert für die Stromerzeugung, den Brennstoffverbrauch und den elektrischen sowie thermischen Wirkungsgrad des Gesamtprozesses realitätsnahe Ergebnisse. Die gute Anpassung des Modells an den realen Prozess kann am Beispiel des Gasverbrauchs (Bild 2) nachvollzogen werden. Hier werden für zwei unterschiedliche Betriebspunkte für jeweils 48 Stunden die gemessenen und simulierten Stundenmittelwerte des Gasverbrauches gegenübergestellt.
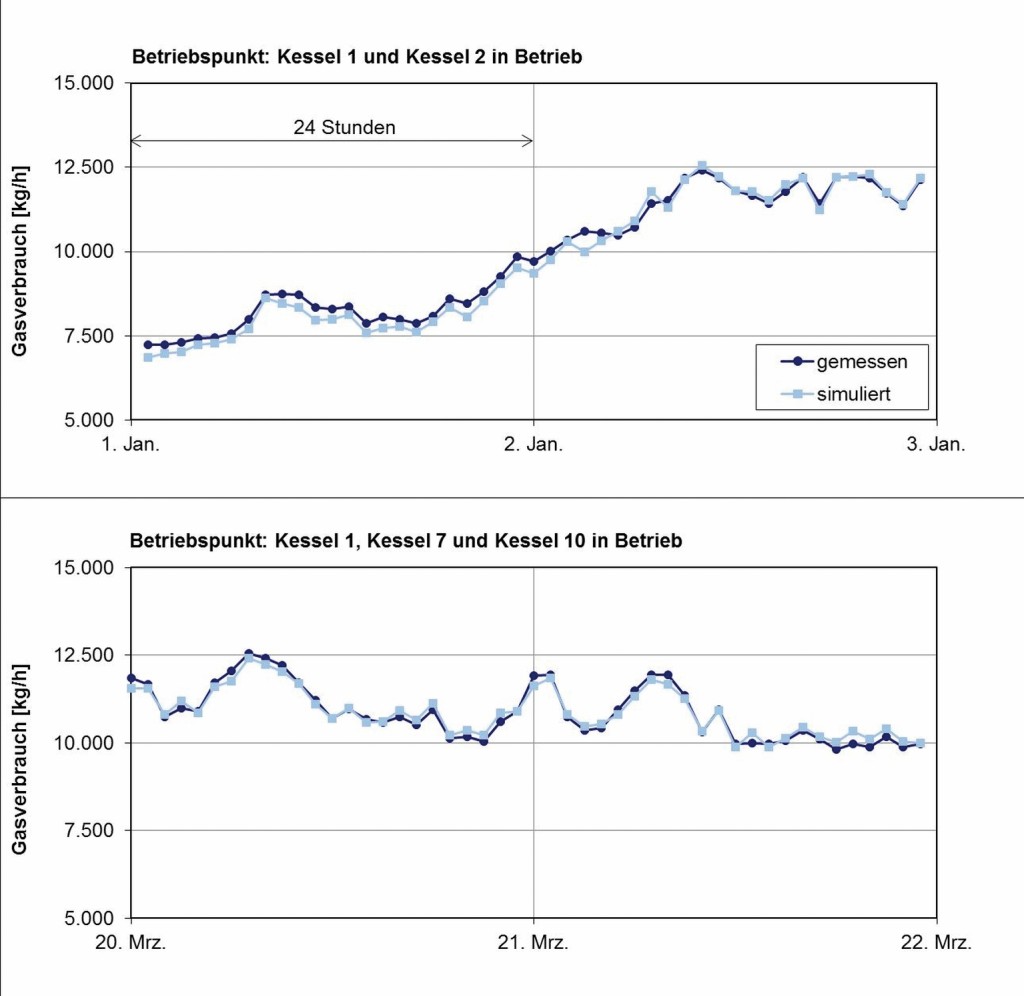
Bild 2 Beispiel für einen gemessenen und simulierten Tagesverlauf des Gesamt-Gasverbrauchs des Industriekraftwerks für zwei verschiedene Betriebspunkte. Bild: eigene Darstellung
Das Modell erlaubt es, Optimierungsmöglichkeiten des bestehenden Prozesses vor dem tatsächlichen Einbau von neuen Komponenten zu simulieren. Durch Betrachtung der Auswirkungen auf Strom- und Dampfproduktion sowie Brennstoffverbrauch können diese Prozessoptimierungen in energetischer und wirtschaftlicher Hinsicht bewertet werden. Bei einer bestehenden Kraftwerksanlage ist es dabei häufig wünschenswert, den tatsächlichen Betrieb der Anlage über längere Zeiträume abzubilden, um so einen Vergleich zwischen dem Ist-Zustand der bestehenden Anlage und dem Zustand einer erweiterten oder veränderten Anlage ziehen zu können. Obwohl das Kraftwerk selbst dynamisch und instationär betrieben wird, soll bei der Simulation der Anlage dennoch auf ein stationäres Berechnungsmodell zurückgegriffen werden. In der in Bild 2 gezeigten Darstellung der Gasverbräuche wurde zum Beispiel mit Stundenmittelwerten der erzeugten elektrischen Leistung beziehungsweise der erzeugten Dampfmassenströme gearbeitet, um – neben anderen Brennstoffmassenströmen – den Gasverbrauch der eingebauten Gasturbine zu berechnen. Es zeigt sich eine gute Übereinstimmung der berechneten Verbräuche mit den gemessenen beziehungsweise aus Validierungsrechnungen mit einer weiteren Software bekannten Ergebnissen. Für die Betrachtung eines ganzen Betriebsjahres ist es jedoch nicht praktikabel, dieses aufgrund des hohen Simulationsaufwandes mit 8 760 Stundenmittelwerten und damit ebenso vielen stationären Einzelrechnungen abzubilden.
Jahressimulation durch Clusterung von Betriebszuständen
Soll nun eine Optimierungsmöglichkeit des bestehenden Kraftwerks vor der Umsetzung mittels Simulation untersucht und mit dem Ist-Zustand verglichen werden, so genügt es in der Regel nicht, einzelne Betriebszustände zu simulieren und miteinander zu vergleichen. Interessant bei solchen Betrachtungen ist dabei vor allem der Betrieb der Anlage über den Zeitraum eines ganzen Jahres. Eine vollständige, stundenweise Jahressimulation würde jedoch eine zu umfangreiche Rechenzeit in Anspruch nehmen, zum anderen wäre die Wahrscheinlichkeit, dass einige stark instationäre Betriebspunkte nicht fehlerlos simuliert werden können, sehr hoch. Dies ist damit begründet, dass das bestehende Simulationsmodell nur darauf ausgelegt ist, die üblichen Betriebspunkte simulieren zu können. So ist es unter anderem nicht möglich, dynamische Betriebszustände wie An- und Abfahrvorgänge durchzurechnen.
Ziel ist es daher, eine begrenzte, repräsentative Anzahl an Betriebspunkten auszuwählen, die den am häufigsten im Jahr gefahrenen Betriebszuständen entsprechen und den Jahresbetrieb des Kraftwerks mit hinreichender Genauigkeit abbilden. Das bestehende und das erweiterte Kraftwerksmodell sollen für diese diskreten Betriebspunkte simuliert werden. Als Input-Daten müssen alle innerhalb der Bilanzgrenze relevanten Massenströme, Drücke und Temperaturen bekannt sein und vorgegeben werden. Dabei handelt es sich beispielsweise um die Massenströme der Dampfabgabe an die Betriebe oder der Dampfproduktion der Kessel.
Die Simulationsergebnisse sollen daraufhin nach Gewichtung mit der entsprechenden Betriebsstundenanzahl und Hochrechnung auf das komplette Betriebsjahr realitätsnahe Ergebnisse für ausschlaggebende Größen wie Gesamtdampfproduktion, Gasverbrauch, Kohleverbrauch und Stromproduktion liefern. Maßgebliche Input-Daten sind dabei die geforderte Dampfabgabemenge an die Produktionsanlagen sowie die Betriebsparameter der Kessel und Turbinen, mit Ausnahme der Massenströme des Regelkessels und der Regelturbine.
Auswahl repräsentativer Betriebspunkte
Die Auswahl der diskreten Betriebspunkte wurde vornehmlich nach der Menge der Gesamtdampferzeugung vorgenommen, da sich die Dampferzeugung im Kraftwerk nach dem Bedarf am Industriestandort richtet. Die Betriebspunkte sollen dabei den gesamten Lastbereich des Kraftwerks (120 bis 380 t/h) abdecken können. Zunächst wurden alle Betriebszustände des Jahres 2012 hinsichtlich der Gesamtdampferzeugung auf Basis von Stundenmittelwerten ausgewertet und in Lastbereiche von 20 t/h eingeteilt. Dabei fiel auf, dass sich die Anzahl der jährlichen Betriebszustände sehr ungleich auf die einzelnen Lastbereiche verteilt. Aus diesem Grund wurden als zweites Kriterium zur Auswahl der diskreten Betriebspunkte die in den Lastbereichen gefahrenen Kesselkombinationen herangezogen. Das Kraftwerk verfügt über fünf Dampfkessel, die nicht zeitgleich betrieben werden. Vielmehr werden bestimmte Dampfkessel und Kesselkombinationen bevorzugt betrieben. Die generelle Betriebsstrategie des Kraftwerks ist ebenso wie der Dampfbedarf am Standort ein wesentlicher Faktor, der den Jahresbetrieb des Kraftwerks ausmacht, und muss daher bei der Auswahl der Betriebspunkte unbedingt berücksichtigt werden.
Bild 3 zeigt die Betriebsstundenanzahl der einzelnen Kesselkombinationen in den einzelnen Lastbereichen.
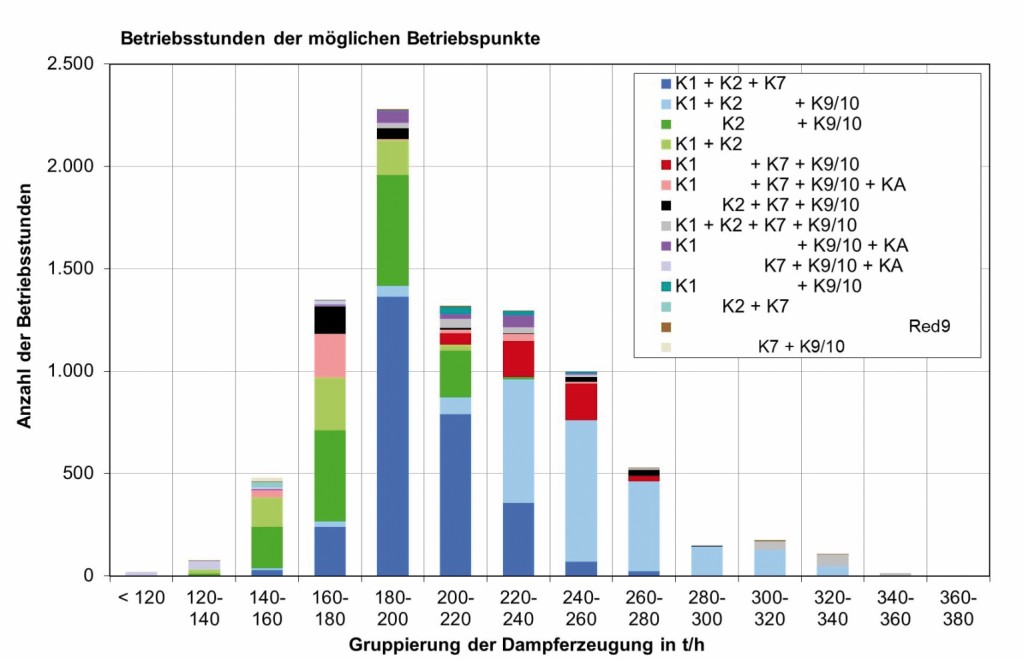
Bild 3 Betriebsstundenanzahl der einzelnen Kesselkombinationen in den verschiedenen Lastbereichen. Bild: eigene Darstellung
Die Abbildung macht deutlich, dass je nach Größe des Dampfdurchsatzes bestimmte Kesselkombinationen dominieren. Um dies entsprechend zu berücksichtigen, erfolgt die Auswahl der repräsentativen Betriebspunkte auf Grundlage der gezeigten Abbildung. Insgesamt ergeben sich nach der Einteilung in Lastbereiche und Kesselkombinationen für das betrachtete Jahr 87 verschiedene Betriebszustände. Aus diesen wurden jedoch nur diejenigen ausgewählt, die eine Betriebsstundenanzahl von mehr als 20 Stunden aufweisen und gleichzeitig übliche Kesselfahrweisen abbilden, damit untypische und nicht repräsentative Betriebszustände wie An- und Abfahren von Kesseln nicht ins Gewicht fallen. Durch diese Einschränkung kann die Anzahl der repräsentativen Betriebspunkte auf 45 reduziert werden.
Jahresbilanz mit ausgewählten Betriebspunkten
Für jeden der 45 festgelegten Betriebspunkte wurde ein dafür repräsentativer und stabiler Zustand aus der zuvor erstellten Jahresstundenauflistung des Jahres 2012 ausgewählt und mit Hilfe des thermodynamischen Modells simuliert. Die Simulationsergebnisse der 45 Betriebspunkte für Gesamtdampferzeugung, Gas- und Kohleverbrauch und Stromerzeugung wurden entsprechend der zuvor festgelegten Betriebsstundenanzahl der einzelnen Betriebspunkte hochgerechnet und summiert. So ergeben sich die Jahresergebnisse für die betrachteten Größen, die daraufhin mit den gemessenen Jahresergebnissen verglichen werden können. Die Zusammenfassung der Ergebnisse in der Tabelle macht deutlich, dass mit der Simulation von 45 Betriebspunkten die gemessenen Jahresbilanzen mit einer Abweichung von maximal 3 % und besser bestimmt werden können.

Tabelle Vergleich der gemessenen und simulierten Jahressummen für Produktion und Verbrauch.
Zur weiteren Überprüfung der Simulationsergebnisse wurden zu den dargestellten Größen Jahresdauerlinien erstellt. Bild 4 zeigt den Jahresverlauf des Gasverbrauches auf Basis der gemessenen und simulierten Werte.

Bild 4 Jahresdauerlinie des Gasverbrauchs auf Basis der gemessenen und simulierten Werte. Bild: eigene Darstellung
Auch hier zeigt sich, dass sich die Simulationsergebnisse sehr gut an die realen Werte annähern und die ausgewählten Betriebspunkte die Realität gut widerspiegeln.
Da gemäß der Tabelle der Kohleverbrauch die größte Abweichung aufweist, wird in Bild 5 die Jahresdauerlinie des Kohleverbrauches auf Basis der gemessenen und simulierten Werte ebenfalls aufgetragen.

Bild 5 Jahresdauerlinie des Kohleverbrauchs auf Basis der gemessenen und simulierten Werte. Bild: eigene Darstellung
Im Gegensatz zu Bild 4 weichen die simulierten und gemessenen Werte des Kohleverbrauches deutlich voneinander ab. Dies kann damit zusammenhängen, dass es sich bei dem hier dargestellten gemessenen Kohleverbrauch nicht um direkte Messwerte, sondern bereits um eine Berechnung aus mehreren Messwerten handelt, die jeweils mit Ungenauigkeiten behaftet sind.
Im Gegensatz zu einer Simulation mit Stundenmittelwerten konnte damit die reine Rechenzeit für die Bestimmung der Jahresbilanz von rund 80 Stunden auf etwa 25 Minuten reduziert werden. Dabei erfolgt das Einlesen der Daten aus den Betriebspunkten automatisiert über die Schnittstelle EbsScript zwischen Ebsilon Professional und MS Excel. In jedem Fall ist zusätzlich jedoch manuelle Voraufbereitung der Rohdaten notwendig, um zu stark instationäre Betriebspunkte oder fehlende Messdaten auszusortieren.
Fazit
Durch die Auswahl einer begrenzten, repräsentativen Anzahl an diskreten Betriebspunkten wurde eine Möglichkeit geschaffen, einen instationären Prozess mit einem stationären Simulationstool für die Erstellung von Gesamtjahresbilanzen mit hoher Genauigkeit abzubilden. Das mit Hilfe von Messdaten aus dem Jahr 2012 verifizierte Modell wurde anschließend verwendet, um den Zubau einer weiteren Gasturbinenanlage im Kraft-Wärme-Kopplungsbetrieb zu simulieren und hinsichtlich Wirkungsgradsteigerung, Stromausbeute und Auswirkung auf Brennstoffverbrauch zu untersuchen. Die Ergebnisse bildeten die Grundlage für eine Wirtschaftlichkeitsbetrachtung zur geplanten Investitionsmaßnahme.
M.Sc. Nina Wolter, Jahrgang 1991, Bachelor-Studium Prozess-, Energie- und Umwelttechnik und Master-Studium Simulations- und Experimentaltechnik an der Hochschule Düsseldorf. Seit 2015 Ingenieurin in der Abteilung HSU – Energy Efficiency & Customer Service der Firma Henkel AG & Co. KGaA, Düsseldorf.
Dr.-Ing. Thomas Zekorn, Jahrgang 1954, Studium des Maschinenbaus an der RWTH Aachen, Promotion am Forschungszentrum Jülich. Seit 1997 Leiter des Industriekraftwerkes am Hauptsitz der Firma Henkel AG & Co. KGaA in Düsseldorf.