Bei den Türmen fällt das Höhenlimit
Mit einer neuen Produktionstechnik für die Türme von Windkraftanlagen lassen sich die stetigeren und stärkeren Höhenwinde für die Stromproduktion nutzen.
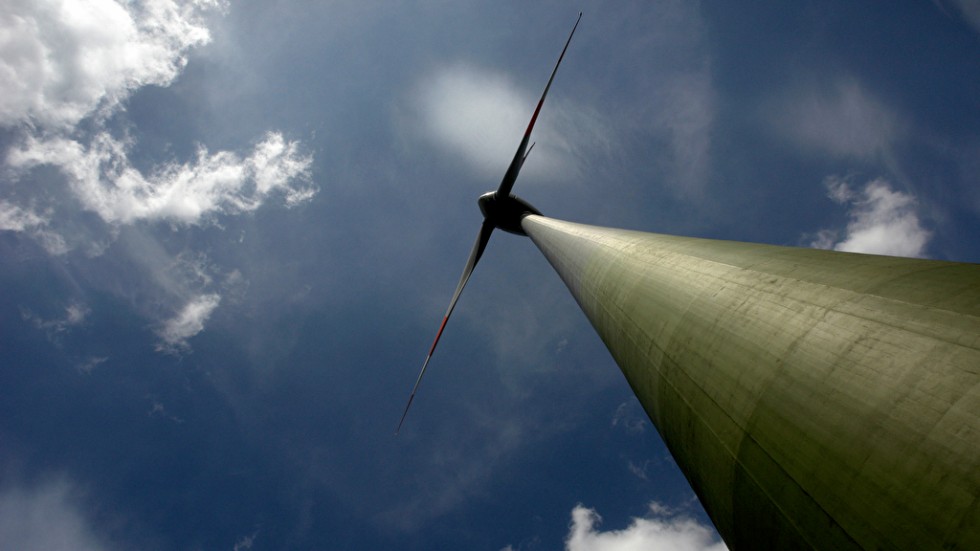
Höhere Windräder bringen eine höhere Stromausbeute, doch wurden sie bisher ab einer bestimmten Höhe unwirtschaftlich. Ein neues Produktionsverfahren könnte dies ändern.
Foto: PantherMedia/Brechtel
Bei den Windgeneratoren geht es immer höher hinaus. 150 m hohe Türme sind keine Seltenheit mehr. Der dänische Hersteller Vestas denkt schon an 199 m für sein größtes Exemplar, das eine Leistung von 15 MW hat und derzeit im Testzentrum in Østerild getestet wird. Je höher die Nabe montiert ist, desto größer ist die Stromausbeute. Hoch oben weht es kräftiger und beständiger, sodass seltener fossile Kraftwerke einspringen müssen, um schwächelnde Winde auszugleichen.
In großen Höhen droht Unwirtschaftlichkeit
Ab einer bestimmten Höhe wird es allerdings unwirtschaftlich, insbesondere bei Onshore-Anlagen. Vor allem der Transport der Turmsegmente vom Hersteller zum Zielort wird umso teurer, je höher der Turm werden soll. Für derartige Schwertransporte müssen schon mal Straßen erweitert oder große Umwege in Kauf genommen werden. Überproportional steigt auch der Aufwand für die Fundamentierung.
Spiralschweißen könnte die Lösung sein
Keystone Tower Systems in Denver im US-Bundesstaat Colorado, 2011 von einer Absolventin und einem Absolventen des Massachusetts Institute of Technology (MIT) in Cambridge bei Boston gegründet, will das ändern und kostengünstige Türme in schwindelerregenden Größenordnungen bauen. Sie bestehen aus breiten Stahlbahnen, die spiralförmig zu Rundtürmen gewickelt werden, die nach oben schlanker werden. Die ebenfalls spiralförmigen Nähte zwischen den Stahlbahnen werden mit einem Verfahren miteinander verbunden, das aus dem Pipelinebau bekannt ist, dem Spiralaschweißen. Diese Technik setzt beispielsweise das schwedische Unternehmen Alvenius in Eskilstuna ein.
Turmfabrik vor Ort
Keystone Tower Systems baut, wenn Türme errichtet werden sollen, an deren späterem Standort eine Fabrik auf, die vor allem zwei Aufgaben hat: Die Stahlbänder, die in Rollenform – sogenannten Coils – angeliefert werden, zu biegen und die Scheißnähte zu setzen bei gleichzeitiger Kontrolle der Naht. Der Transport von mächtigen Beton- oder Stahlpfeiler-Segmenten, die zentral hergestellt werden, entfällt. Zudem, was noch wichtiger ist, die Kosten steigen mit wachsender Höhe nicht überproportional an.
180 Meter und mehr sind möglich
Mit dem Verfahren des Unternehmens ließen sich Türme mit einem Durchmesser von 7 m und einer Höhe von 180 m und mehr so günstig herstellen, dass die Vorteile der Höhenwinde vollständig genutzt werden könnten, ohne die Investitionskosten in unzumutbare Höhen zu treiben, sagt Eric Smith, der CEO des Unternehmens. Der größte Generator der Welt rotiert heute auf einem 150 m hohen Turm. Smith hat am MIT Maschinenbau und Elektrotechnik studiert. Er hat das Unternehmen gemeinsam mit Rosalind Takata gegründet, die heute Chief Technical Officer (CTO) ist und ebenfalls ein Maschinenbaustudium am MIT absolviert hat.
Anteil der Turmkosten steigt überproportional
Etwa die Hälfte der Stromgestehungskosten einer durchschnittlichen kommerziellen Windenergieanlage stammt laut dem National Renewable Energy Laboratory (NREL) in Denver aus den Herstellungskosten der Windturbinen selbst. Davon entfällt fast die Hälfte auf die Gondel an der Spitze. Der Rest verteilt sich auf die Rotoren mit einem Anteil von rund 13,7 % und den Turm selbst mit rund 10,3 %. Aber wenn die Türme höher werden, steigt deren Anteil an den Investitionen überproportional an. Ein 110-Meter-Turm kommt bereits auf 20, ein 150-Meter-Turm schon auf 29 %.
Zunächst hat Keystone eine stationäre Produktionsstätte am Unternehmensstandort errichtet, um die Technik zu demonstrieren. Der erste dort hergestellte Turm ist allerdings nur bescheidene 89 m hoch. Er trägt eine Turbine von GE (General Electric) in Boston mit einer Leistung von 2,8 MW. Die erste kommerzielle Nutzung des Verfahrens mit wirklich großen Türmen ist für 2025 geplant.