Carbon Black aus Autoreifen zurückgewinnen – das funktioniert!
Industrieruß, auch Carbon Black genannt, gehört zu den wichtigsten großtechnisch genutzten Pigmenten Seine Herstellung erfordert viel Energie. Jetzt zeigen Fraunhofer-Ingenieure, dass sich der Farbstoff effizient recyceln lässt.
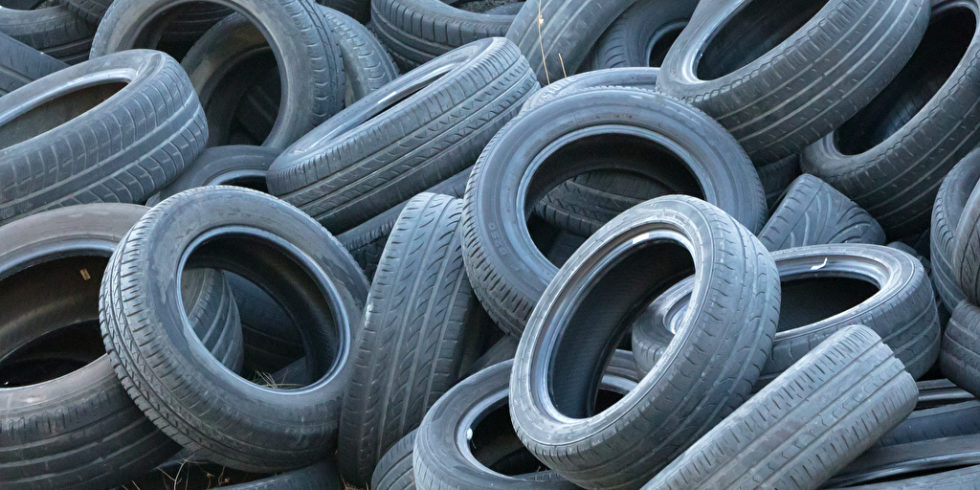
Alte Autoreifen sind ein wertvoller Rohstoff für Carbon Black. Fraunhofer-Ingenieure stellen ein neues Verfahren vor.
Foto: panthermedia.net/michaklootwijk (YAYMicro)
Im Jahr 2020 wurden rund 42,8 Millionen Consumer-Reifen verkauft. Für 2021 rechnen Experten mit rund 45,7 Millionen Reifen. Laut ADAC landen pro Jahr bundesweit etwa 600.000 Tonnen Altreifen in Abfallentsorgungsanlagen. Europaweit liegt das Müllaufkommen bei schätzungsweise 3,4 Millionen Tonnen. Etwa vier Milliarden Altreifen haben sich bereits auf Deponien angesammelt, jährlich kommen etwa 1,8 Milliarden Reifen neu dazu. Das sind beeindruckende Zahlen, die eine erhebliche Belastung für die Umwelt mit sich bringen.
Denn Reifen enthalten als Verbundabfall bis zu 200 unterschiedliche Stoffe. Mengenmäßig stehen Gummi, Stahl und Gewebe an erster Stelle. Bislang wurden 396.000 Tonnen stofflich aufgearbeitet und weitere 175.000 Tonnen der thermischen Verwertung zugeführt. Das in Reifen enthaltene Carbon Black wurde bislang kaum aufbereitet, weil es zu etwa 20% mineralische Bestandteile enthält. Das sich dieses Pigment gut recyclen lässt, zeigen Forschende am Fraunhofer-Instituts für Bauphysik IBP. Bei ihrem Verfahren entstehen neben dem Farbstoff selbst auch wertvolle anorganische Produkte.
Überraschende Spuren: Wo Reifenabrieb landet – und was Hersteller unternehmen sollten
Carbon Black: Hoher Energieaufwand bei der Herstellung
Zum Hintergrund: Jeder Autoreifen enthält etwa drei Kilogramm Industrieruß. Pro Tonne dieses schwarzen Pigments werden 1,5 Tonnen fossile Rohstoffe und große Mengen Wasser eingesetzt. Beim Prozess entstehen bis zu drei Tonnen Kohlenstoffdioxid.
Das liegt am technischen Prozess selbst. Carbon Black wird zu 95% über das Furnaceruß-Verfahren hergestellt. Das Pigment entsteht dabei durch unvollständige Verbrennung von schweren Fraktionen der Erdöldestillation. Im ersten Schritt verbrennt man Erdgas oder Öl. In dieses Heißgas von 1200 bis 1800 Grad Celsius spritzt man Öle ein. Durch unvollständige Verbrennung der organischen Komponente entsteht Ruß. Nach einer bestimmten Verweilzeit wird das Reaktionsgemisch rasch mit Wasser abgekühlt. Anschließend arbeitet man den Ruß weiter auf. Allein für Autoreifen gibt es nahezu 40 verschiedene Industrierußtypen, je nach Verwendungszweck.
Kunststoffe länger verwenden – mit einem biologischen Trick
Von der Pyrolyse zum reinen Carbon Black
Forscherinnen und Forscher des Fraunhofer IBP lösen jetzt ein zentrales Problem. Führt man Altreifen nämlich der Pyrolyse zu, entstehen Öle als Energieträger. Der Rückstand enthält Recovered Carbon Black, ein Rohprodukt mit hohem mineralischem Anteil. Darunter sind vor allem Zinksalze und Silicate.
Zur Aufarbeitung entwickelten die Forschenden einen nasschemischen Prozess. Dazu brachten sie das rohe Gemisch aus Asche und Carbon Black in einen Reaktor. Ein Additiv und ein Fluid kamen mit hinzu. Dieses Gemisch behandelten sie bei unterschiedlichen Temperaturen und Druckwerten. Unter den Bedingungen gelang es, aus dem Gemisch selektiv einzelne Stoffe herauszulösen. In der Praxis erwies sich dieser Schritt als recht anspruchsvoll. Alle Parameter des Extraktionsschritts mussten passend gewählt werden. Auf zu große Mengen an Chemikalien, um das Verfahren wirtschaftlich und möglichst umweltfreundlich zu gestalten. Einen Teil der Additive konnten die Fraunhofer-Ingenieure wieder zurückgewinnen.
Über dieses Verfahren gelang es, rohen Ruß zu entmineralisieren. Dabei entsteht Carbon Black mit hohem Reinheitsgrad. „Das so behandelte Recoverd Carbon Black ist nahezu frei von mineralischen Reststoffen, es lässt sich beispielsweise zu 100% für die Seitenteile von Reifen einsetzen – also ohne Beimischung von primärem Carbon Black“, sagt Severin Seifert vom Fraunhofer IBP. Das Pigment könne somit Industriematerialien komplett ersetzen. Zum Vergleich: Ohne die Entmineralisierung sind gerade einmal 10% als Zusatz möglich.
Erste industrielle Anlage für aufbereitetes Carbon Black in Bau
Ziel der Fraunhofer-Arbeitsgruppe ist aber, ihr Wissen von der Forschung in die Anwendung zu bringen. Sie haben bereits eine Pilotanlage aufgebaut, die 200 Liter Volumen aufnehmen kann. Der Prozess ist auch schon patentiert worden – mit der RCB Nanotechnologies GmbH als Lizenznehmer.
Derzeit entsteht eine Anlage, deren Reaktor pro Produktionsstrang 4.000 Liter fasst. Umgerechnet bedeutet das: Jeder Produktionsstrang reinigt pro Stunde 400 Kilogramm Carbon Black. Das sind etwa 2.500 Tonnen pro Jahr. Perspektivisch sollen es sogar knapp 30.000 Tonnen werden.
Doch damit ist das Spektrum an Innovationen noch lange nicht ausgeschöpft. Firmen erforschen momentan, ob sich Lignin aus Holzabfällen eignet, um Carbon Black zu ersetzen. Lignin ist neben Zellulose das zweithäufigste Biopolymer weltweit. Holz besteht zu ungefähr 30% aus Lignin.
Mehr zum Thema Kunststoffe:
- Aus Plastikmüll wird Treibstoff – in nur einer Stunde!
- Lebensmittel haltbar verpackt – Ganz ohne Plastikmüll
- Wie Eiweiße künftig Erdöl-Produkte ersetzen könnten