Umweltfreundlich arbeiten mit Polyethylen – wie das funktioniert
Polyethylen gehört zu den am häufigsten industriell eingesetzten Kunststoffen. Forschende aus Konstanz zeigen, wie sich Polyethylen-Dispersionen in Wasser herstellen lassen – und wie das Recycling nachhaltiger wird.
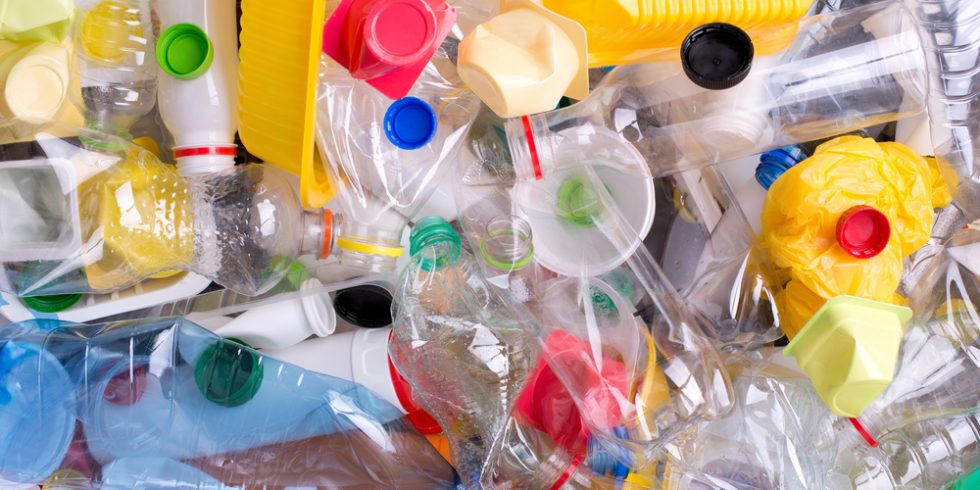
Kunststoffe wie Polyethylen lassen sich nachhaltiger herstellen und recyceln.
Foto: panthermedia.net/photkas
Kunststoffe wie Polyethylen werden auch in den nächsten Jahren und Jahrzehnten eine entscheidende Rolle bei unterschiedlichen Anwendungen spielen; sie lassen sich nicht von heute auf morgen ersetzen. Ingenieurinnen und Ingenieure versuchen deshalb, möglichst nachhaltige Verfahren zu entwickeln: sowohl bei Synthesen als auch beim Recycling. Ein Durchbruch ist jetzt Forschenden an der Universität Konstanz gelungen. Sie haben einen innovativen Katalysator entwickelt, um Polyethylen-Dispersionen direkt in Wasser herzustellen. Ziel des Projekts ist, umweltfreundliche Verfahren für lösungsmittelfreier Kunststoff-Beschichtungen zu entwickeln – und Abfälle zu vermeiden.
Nachhaltigkeit: Das Remanufacturing alter Fahrzeug-Bauteile optimieren – mit künstlicher Intelligenz
Ein neuer Katalysator für die Polyethylen-Chemie
Zum Hintergrund: Polymere wie Polyethylen entstehen aus Monomeren, den Ausgangsstoffen. Bei Polyethylenen ist das Ethylen, ein gasförmiger Kohlenwasserstoff. Um die chemische Reaktion durchzuführen, sind geeignete Katalysatoren erforderlich. Die Umsetzung selbst war bislang nur in organischen Lösungsmitteln möglich. Diese werden in einem aufwändigen, teuren Schritt dann durch Wasser ersetzt werden, um Dispersionen herzustellen. Gleichteig entstehen Gemische, die aufwändig zu entsorgen oder zu trennen sind. Solche Verfahren sind deshalb wenig attraktiv.
Chemikerinnen und Chemiker der Uni Konstanz haben deshalb eine neue Klasse von wasserlöslichen Katalysatoren entwickelt. Ihre Studie zeigt, dass es gelingt, Polyethylen direkt in Wasser als Lösungsmittel herzustellen. „Man benötigt dafür Katalysatoren, die zum einen in Wasser aktiv sind und zum anderen nicht durch das Wasser zerstört werden“, so Stefan Mecking, Professor für Chemische Materialwissenschaft an der Universität Konstanz. „Die meisten traditionellen Katalysatoren sind nicht stabil, wenn sie mit Wasser in Kontakt geraten.“
Einen solchen Katalysator haben die Forschenden jetzt erfolgreich entwickelt. Ihre Laboranalysen zeigen, dass bei der Reaktion in Wasser kleine Polyethylen-Partikel entstehen, und das bei hoher Ausbeute. Der Kunststoff bildet sich dabei als Dispersion; teure oder giftige Lösungsmittel sind nicht erforderlich. Der Werkstoff selbst hatte gute Eigenschaften. Das Molekulargewicht war hoch, und die Moleküle hatten eine hohe Linearität. Es handelte sich um sogenanntes High Density Polyethylen (HDPE), ein besonders hochwertiges Material. Bei der Verarbeitung und Aushärtung verdampft lediglich Wasser.
Die Forschungsergebnisse eröffnen laut Mecking etliche neue Perspektiven für umweltfreundliche Polymerisationsverfahren generell, aber auch speziell für lösungsmittel- und emissionsfreier Beschichtungen mit Polyethylen. In dem Verfahren stecken große Potenziale.
Fraunhofer-Entwicklung: Silizium-Recycling: Aus Altmodulen werden neue Solarzellen
Polyethylen nachhaltig recyceln: Diese Probleme gab es bislang
Doch Mecking hat noch weitere Ideen für ein anderes, recht bekanntes Problem. Aus dem Alltag sind Kunststoffe wie Polyethylen nicht wegzudenken. Nur sind die Recycling-Quoten immer noch recht niedrig; große Mengen werden thermisch verwertet. „Die Polymerketten von Polyethylenen sind sehr stabil und nicht so leicht wieder in kleine Moleküle zurückzuführen“, erläutert Mecking. So seien Temperaturen von über 600 Grad Celsius erforderlich, was das Verfahren energieaufwändig und teuer mache. Zugleich werde oft nur zehn Prozent des Ausgangsstoffes recycelt. Zwar gibt es neben diesem chemischen Verfahren auch Möglichkeiten der mechanischen Trennung; das scheitert jedoch oft an der fehlenden Sortenreinheit – oder führt zu minderwertigen Produkten.
Polyethylen bei niedriger Temperatur recyceln
Das wollen die Forschenden jetzt ändern. Ihr neues Recycling-Verfahren funktioniert schon bei niedrigen Verfahren, weil die Chemikerinnen und Chemiker molekulare „Sollbruchstellen“ nutzen. Das spart Energie. Außerdem sind die Rückgewinnungsquoten mit rund 96 Prozent des Ausgangsstoffes deutlich höher als bei industriellen Verfahren. Die kristalline Struktur und die Materialeigenschaften des Kunststoffs bleiben unverändert.
Im Labor zeigten die Wissenschaftlerinnen und Wissenschaftler, wie sich ein Polyethylen-artiger Kunststoff auf Pflanzenölbasis recyceln lässt. Dies war schon bei Temperaturen von rund 120 Grad möglich. Gemischen mit anderen Kunststoffen, wie sie in Abfallströmen vorkommen, konnten ebenfalls mit Erfolg bearbeitet werden. Mecking berichtet, die wiedergewonnen Materialien seien in ihren Eigenschaften dem Ausgangsmaterial ebenbürtig. Sie eignen sich beispielsweise für den 3D-Druck.
Mehr zum Thema Recycling: