Wie ein innovativer Katalysator die Herstellung von E-Fuels revolutioniert
Verfahren zur Gewinnung von E-Fuels sind nicht neu, aber optimierbar. Das ist US-Ingenieuren jetzt durch eine innovative Beschichtung katalytisch aktiver Kupferoberflächen mit Polymeren gelungen.
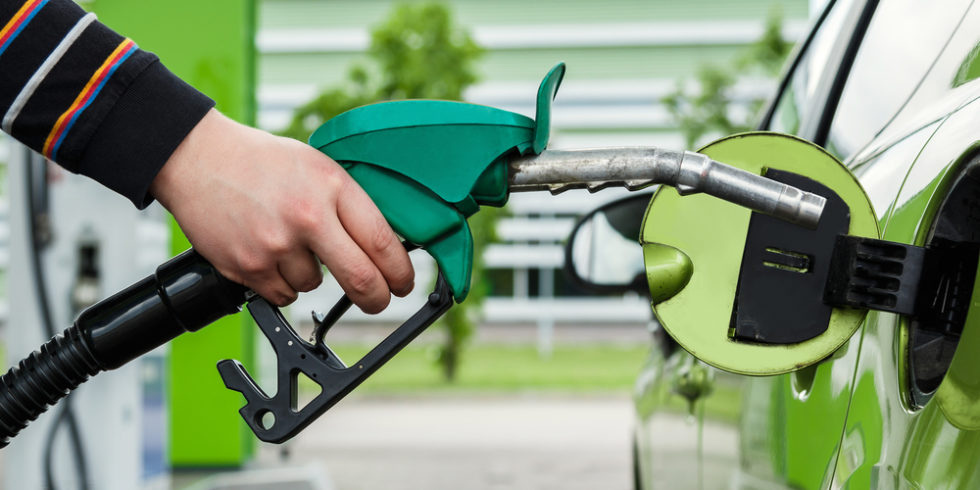
Ingenieurinnen und Ingenieure haben eine Möglichkeit entwickelt, E-Fuels effizienter herzustellen – bislang nur im Labor.
Foto: panthermedia.net/AY_PHOTO
Egal, ob beim Auto oder beim Flugzeug: Verbrennungsmotoren lasen sich nicht von heute auf morgen ersetzen. Auch so manche Heizung benötigt Energieträger auf Kohlenstoffbasis. Hier kommen E-Fuels ins Spiel: synthetische Kraftstoffe, die aus Wasser und Kohlenstoffdioxid hergestellt werden. Das Treibhausgas wird gebunden und in gleicher Menge bei der späteren Verbrennung wieder freigesetzt. Die notwendige Energie kommt aus Strom erneuerbaren Ursprungs. Alle Vorgänge lassen sich klimaneutral ausführen.
Zwar haben Ingenieurinnen und Ingenieure dafür in den letzten Jahren etliche Methoden entwickelt. Um wirtschaftlich rentabel zu sein, müssen solche Verfahren jedoch verbessert werden, um eine größere Menge an kohlenstoffreichen Produkten gewinnen zu können. Wichtig ist dabei, keine Stoffgemische zu erhalten, die im Anschluss an die Reaktion aufwendig getrennt werden müssten.
Forscherinnen und Forscher des Lawrence Berkeley National Laboratory in Berkeley, Kalifornien, ist es jetzt gelungen, die Selektivität der Kohlenstoff-Reduktion zu verbessern. Sie haben die Oberfläche eines Kupferkatalysators gezielt verändert.
Klimaneutralität: Deutsche Energie-Agentur veröffentlicht neue Leitstudie
E-Fuels: Niedrige Selektivität der katalytischen Vorgänge
„Wir wissen zwar, dass Kupfer der beste Katalysator für diese Reaktion ist, aber das Metall führt zu keiner hohen Selektivität für die gewünschten Produkte“, so Alexis Bell. Er ist leitender Wissenschaftler in der Abteilung Chemische Wissenschaften des Berkeley Lab und Professor für Chemieingenieurwesen an der UC Berkeley. „Unsere Gruppe hat herausgefunden, dass man verschiedene Tricks mit der lokalen Umgebung des Katalysators anwenden kann, um diese Selektivität zu optimieren.“
Zum Hintergrund: In früheren Studien hatten Forschende bereits genaue Reaktionsbedingungen für das Verfahren ermittelt. Ihr Ziel war, das beste elektrische und chemische Umfeld für die Herstellung kommerziell interessanter kohlenstoffreicher Produkte zu gewährleisten. Doch sie hatten ein Problem: Alle Bedingungen entsprachen nicht den Parametern typischer elektrochemischer Zellen, die ein leitendes Material auf Wasserbasis verwenden.
Neue Idee fürs Reichweitenproblem: ein Hybrid aus Elektro- und Erdgasmotor
Mit Ionomeren zum Erfolg
Um ein molekulares Design zu finden, das in der wässrigen Umgebung von Brennstoffzellen eingesetzt werden kann, hatten Bell und sein Team eine Idee. Sie experimentierten mit dünnen Schichten von Ionomeren. Das sind thermoplastische Kunststoffe mit besonderen Eigenschaften. Ionomere zeichnen sich durch eine hohe Zähigkeit und Festigkeit, aber auch durch eine hohe Durchlässigkeit für bestimmte Ionen aus. Bei der Herstellung lässt sich steuern, welche geladenen Teilchen den Kunststoff passieren und welche nicht. Aufgrund ihrer hochselektiven Eigenschaften sind Ionomere in einzigartiger Weise geeignet, die Mikroumgebung in der Reaktionszelle stark zu beeinflussen.
Forschende aus Bells Gruppe schlugen vor, die Oberfläche des Kupferkatalysators mit zwei bekannten Ionomeren, Nafion und Sustainion, zu beschichten. Auf diese Weise, so ihre Hypothese, sollte sich die Umgebung – einschließlich des pH-Werts – in der unmittelbaren Umgebung des Katalysators so verändern, dass die Reaktion besser gesteuert werden kann.
Erste Tests im Labor
Im Experiment wurden eine dünne Schicht eines jedes Ionomers sowie eine Doppelschicht aus beiden Ionomeren auf Kupferfilmen aufgetragen. Tests in elektrochemische Zellen folgten. Während Forschende CO2 in die Zelle einleiteten und eine Spannung anlegten, erfassten sie den Gesamtstrom, der durch die Zelle floss. Sie bestimmten auch Gase und Flüssigkeiten, die sich während der Reaktion in den angrenzenden Reservoirs sammelten. Bei der zweischichtigen Zelle stellten sie fest, dass 80% der bei der Reaktion verbrauchten Energie in kohlenstoffreichen Produkten zu finden war, verglichen mit 60% bei der nicht beschichteten Variante.
Wissenschaftlerinnen und Wissenschaftler folgerten daraus, dass die verbesserte Reaktion eine Folge der hohen CO2-Konzentration war, die sich aufgrund von Beschichtungen unmittelbar über dem Kupfer aufbaute. Außerdem sorgten negativ geladene Moleküle, die sich in der Region zwischen den beiden Ionomeren ansammelten, für einen geringen lokalen Säuregehalt. Diese Kombination wirkte dem Konzentrationsgefälle entgegen, das in Abwesenheit der Ionomerfilme tendenziell auftritt.
Auf dem Weg zur Kommerzialisierung der neuen Technologie für E-Fuels
Um die Effizienz noch weiter zu steigern, griffen die Forscher auf eine Technik zurück, die bereits zuvor ohne Ionomer-Filme als weitere Möglichkeit zur Erhöhung von CO2 und pH-Wert demonstriert worden war. Durch die Verwendung gepulster Spannung mit der zweischichtigen Ionomer-Beschichtung erzielten sie einen Anstieg der kohlenstoffreichen Produkte um 250 % im Vergleich zu unbeschichtetem Kupfer und einer konstanten Spannung.
Im nächsten Schritt geht es jetzt um die Hochskalierung der Technologie. Ziel ist, Verfahren zu entwickeln, mit denen sich E-Fuels in größerer Menge herstellen lassen.
Mehr zum Thema Energie
- So könnte das europäische Energiesystem im Jahr 2050 aussehen
- Klimapfade 2.0: Wirtschafts- und Umweltfachleute legen Machbarkeitsstudie vor
- Klimaziele: Es reicht nicht, neue Verbrenner zu verbieten