Wirtschaftlich Photovoltaik-Wafer in Deutschland klonen
In Sachsen-Anhalt will ein baden-württembergisches Unternehmen bald preisgünstig Siliziumwafer herstellen und so die Energiewende in Deutschland vorantreiben. Der Trick des Unternehmens: Es kann Grundbausteine der Sonnenenergienutzung „klonen“. Ein Gastbeitrag von Frank Siebke.
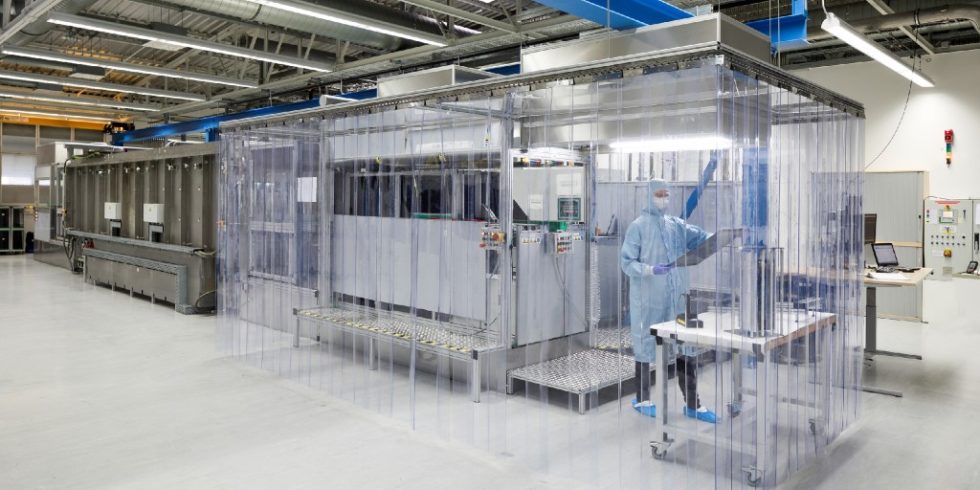
In dieser Anlage stellt das Start-up NexWafe in Freiburg i Br. kontinuierlich Wafer her.
Foto: NexWafe
Eine gute Idee umzusetzen, braucht oft Ausdauer. Das gilt auch für jene, die einige Experten am Fraunhofer-Institut für Solare Energiesysteme (ISE) in Freiburg hatte: „In dem wir Wafer klonen, wollen wir die Waferherstellung revolutionieren“, erklärt von ihnen, der Physiker Stefan Reber, das bahnbrechende Verfahren. 2015 gründeten sie die Firma NexWafe in Freiburg im Breisgau, um die Technologie zu kommerzialisieren.
Klassisch: Fast 50 % Verlust
Reber & Co. setzen an der teuersten Komponente eines Solarmoduls an: am Siliziumwafer. Auf die Herstellung der Wafer entfallen bis zu 40 % der Kosten eines Moduls. Ein paar Details: Konventionell werden Wafer aus Polysilizium hergestellt. Erst wird dazu das Silizium in einem Hochtemperaturprozess abgeschieden, dann in Stücke zerbrochen und wieder eingeschmolzen. Aus dieser Schmelze werden anschließend Einkristalle gezogen. Diese „Ingots“ werden in fast quaderförmige Blöcke geteilt, auf Drahtsägen gespannt und in einzelne Wafer zersägt. Dabei geht fast die Hälfte des verwendeten Siliziums verloren.
Neu: Wafer fast verlustfrei herstellen
Der Clou: Auf nur einem Wafer – dem „Saatwafer“ – wachsen alle anderen Wafer gleich in der richtigen Größe. Die einzelnen Schritte: Auf der Oberfläche des Saatwafers, der konventionell hergestellt wird, wird eine mikrometerdünne Trennschicht geätzt. Auf dieser dünnen Schicht wiederum wird aus Chlorsilanen und Wasserstoff in einem als Epitaxie bekannten Hochtemperaturprozess Silizium abgeschieden: Atom für Atom entsteht ein neuer Wafer. Die fertigen Wafer werden mechanisch von dem Saatwafer getrennt und gehen in die Solarzellenfertigung. Und: Der Saatwafer kann wiederverwendet werden.
Wafer kontinuierlich statt diskontinuierlich herstellen
Das Revolutionäre an dem Verfahren ist, dass alle Prozesse kontinuierlich ablaufen. Dies erhöht den Durchsatz im Vergleich zu den aus der Halbleiterindustrie bekannten Anlagen deutlich, die diskontinuierlich arbeiten. Das Ergebnis überzeugt: Das Freiburger Unternehmen kann die Siliziumverluste in der Waferherstellung um mehr als 90 % senken und den Energieverbrauch und damit die CO2-Emissionen um die Hälfte.
Günstiger herstellen als in China
Mit diesem kontinuierlichen Prozess lassen sich auch in Deutschland Siliziumwafer zu Kosten herstellen, die deutlich unter denen der heutigen Marktführer aus China liegen, meint Reber: „Wir können als deutscher Hersteller ein auf dem Weltmarkt konkurrenzfähiges Produkt anbieten.“
Geklonte Wafer auch sehr dünn
Die hergestellten Wafer sind quasi Klone des Saatwafers. Sie können direkt in bestehende Solarzellen- und Modulfertigungen eingesetzt werden. Und es lassen sich kontinuierlich auch sehr dünne Wafer herstellen. Dies wiederum senkt den elektrischen Widerstand in den Wafern und erhöht damit den Wirkungsgrad der Solarzellen. In Zahlen: Heutige Wafer aus der Massenfertigung sind 140 bis 180 Mikrometer dick. Die Freiburger Experten können 50 Mikrometer dünne Wafer herstellen. Hiermit öffnet NexWafe die Tür zu höchsten Wirkungsgraden in der Massenfertigung und zu einer massiven Senkung der Stromentstehungskosten der Solaranlagen. Reber ist überzeugt „Wir beschleunigen die Energiewende“.
Produktionsanlage in Planung
Nach der Gründung des Unternehmens in 2015 konnten Reber und sein Team Investoren aus der Schweiz, Saudi-Arabien, Italien und Deutschland für die Idee begeistern. Inzwischen hat NexWafe mit dem eingeworbenen Kapital die Pilotfertigung in Freiburg aufgebaut, um weltweit Kunden bemustern zu können. In Bitterfeld-Wolfen in Sachsen-Anhalt, dem ehemaligen Solar-Valley Deutschlands, wurde im Dezember 2019 der erste Schritt für dem Eintritt in die Massenfertigung getan: Die NexWafe Si-Fab GmbH wurde gegründet und hat die Anlagen zum Prozessgas-Recycling einer ehemaligen Polysiliziumfabrik erworben.
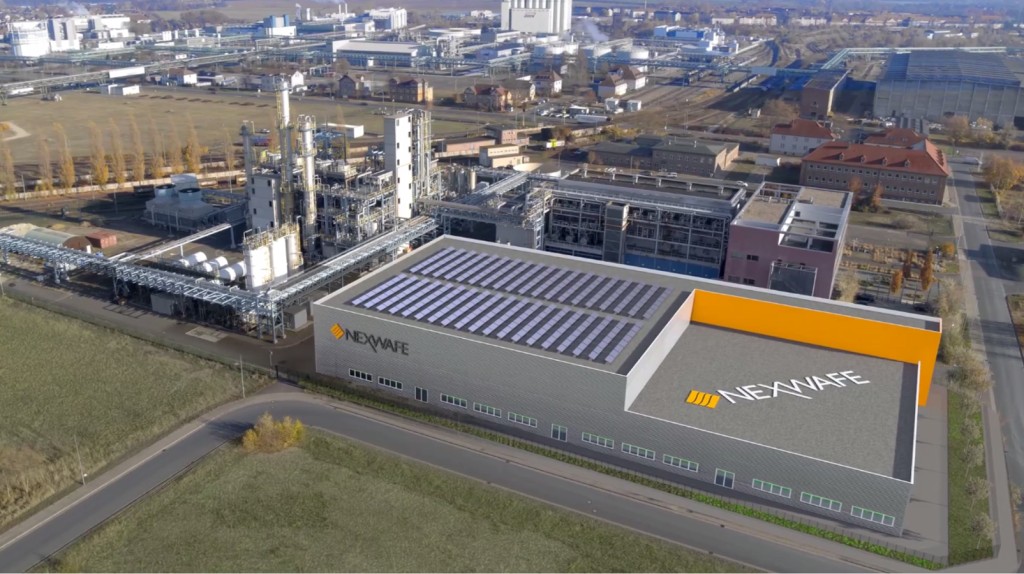
In Bitterfeld-Wolfen in Sachsen-Anhalt hat eine NexWafe-Tochter die Anlagen zum Prozessgas-Recycling einer ehemaligen Polysiliziumfabrik erworben. Hier will NexWafe die Waferfabrik, die mehr als 300 Millionen Wafer pro Jahr herstellen kann, integrieren. Bild: NexWafe
Die GmbH will diese Anlage in die Bitterfeld geplante Waferfabrik integrieren, um bis zu 300 Millionen Wafer pro Jahr herstellen zu können. Mit diesen Wafern können Solarmodule mit einer Leistung von bis zu drei Gigawatt produziert werden. Karl Friedrich Haarburger, Geschäftsführer der NexWafe Si-Fab ist voller Tatendrang: „Wir wecken die Anlage aus dem Dornröschen-Schlaf und bieten den Mitarbeitern vor Ort eine neue Perspektive“. In der Produktion sollen mehr als 200 neue Mitarbeiter eingestellt werden. „Wir sehen in Bitterfeld die idealen Rahmenbedingungen für den Bau unserer Fertigung und haben mit dem Chemiepark und Evonik zwei starke Partner, die unsere Vision teilen“, sagt Reber. Der erste Spatenstich ist für 2021 geplant, dann sollen die Fertigungskapazitäten rasch ausgebaut werden. Schon in 2024 soll eine Kapazität von drei Gigawatt überschritten werden.
Gelingen Reber, Haarburger und ihren Teams die Überführung der am Fraunhofer ISE entwickelten Technologie in die Massenfertigung, kann in Deutschland ein neuer Weltmarktführer entstehen.
www.nexwafe.com
Frank Siebke, Kaufmännischer Leiter von NexWafe, Frank.siebke@nexwafe.com