Energieeffizient Schadstoffe oxidieren
Mit regenerativ-thermischen Oxidationsanlagen einer baden-württembergischen Firma werden Schadstoffe und Geruchsemissionen nahezu vollständig entfernt. Dafür wird kaum Energie benötigt. Solche Anlagen zur Abgasreinigung schützen also Umwelt und Klima.
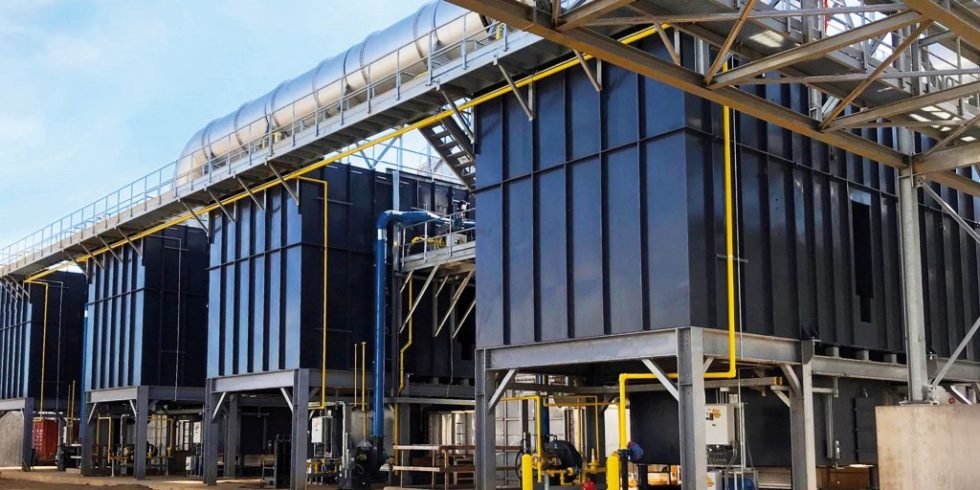
Die RTO-Anlage des Unternehmens Dürr verarbeitet die Abgase zweier mit Biomasse befeuerten Drehtrommeltrocknern im neuen Spanplattenwerk der Firma Egger Wood Products in Lexington, USA. Bild: Dürr
Oxidationsanlagen entfernen Schadstoffe mithilfe von thermischen Verfahren aus der Abluft. Diese Technik eignet sich für ein breites Spektrum an Industrien und Schadstoffarten. Dürr bietet mehr als zehn verschiedene Produkte im Bereich der thermischen Oxidation an. Die Anlagen sind hocheffizient, wartungsarm und überzeugen durch einen hohen Wirkungsgrad.
Bei der regenerativ-thermischen Oxidation (RTO) wird die mit Schadstoffen belastete Abluft durch einen regenerativen Wärmetauscher mit sehr großer Oberfläche geleitet. Die Abluft heizt sich auf und verlässt den Wärmetauscher mit einer Temperatur nahe der Reaktionstemperatur. In der nachfolgenden Brennkammer werden die Schadstoffe durch die entsprechend hohe Temperatur in unschädliche Bestandteile umgewandelt. Die gereinigten Gase werden wieder durch einen Wärmetauscher geleitet, in dem sie ihre Wärmeenergie abgeben – der regenerative Kreislauf schließt sich. Danach verlässt die gereinigte gekühlte Abluft die Anlage. Durch diese Wärmerückgewinnung unterscheiden sich Ein- und Austrittstemperatur der Abluft nur um 30 bis 50 °C.

Foto: Kai Dauvermann
Autotherme Schadstoffverbrennung
Die Oxidationsanlage „Oxi.X“ von Dürr aus Bietigheim-Bissingen reinigt je nach Ausführung Luftmengen von 1 500 bis über 360 000 m3 pro Stunde. Noch größere Abluftmengen können durch Parallelschaltung mehrerer Einheiten gereinigt werden. Die zulässige Schadstoff-Eingangskonzentration liegt dabei je nach Lösemittel bei bis zu 10 g/m3. Liegt eine höhere Konzentration vor, kann etwa Frischluft oder Rezirkulationsgas beigemischt werden. Die Effizienz der Wärmerückgewinnung liegt üblicherweise bei etwa 95 bis 97 %. Dies hält den Bedarf an Zusatzbrennstoff für den Brenner gering.
Ab einer Schadstoffkonzentration von rund 1,5 g/m3 können die Systeme autotherm, also ohne Zusatzbrennstoff betrieben werden. Bei höheren Schadstoffkonzentrationen kann die Überschussenergie über einen heißen Bypass ausgeschleust, optional zurückgewonnen und beispielsweise im Produktionsprozess in Form von Dampf, Thermoöl oder Warmwasser genutzt werden.
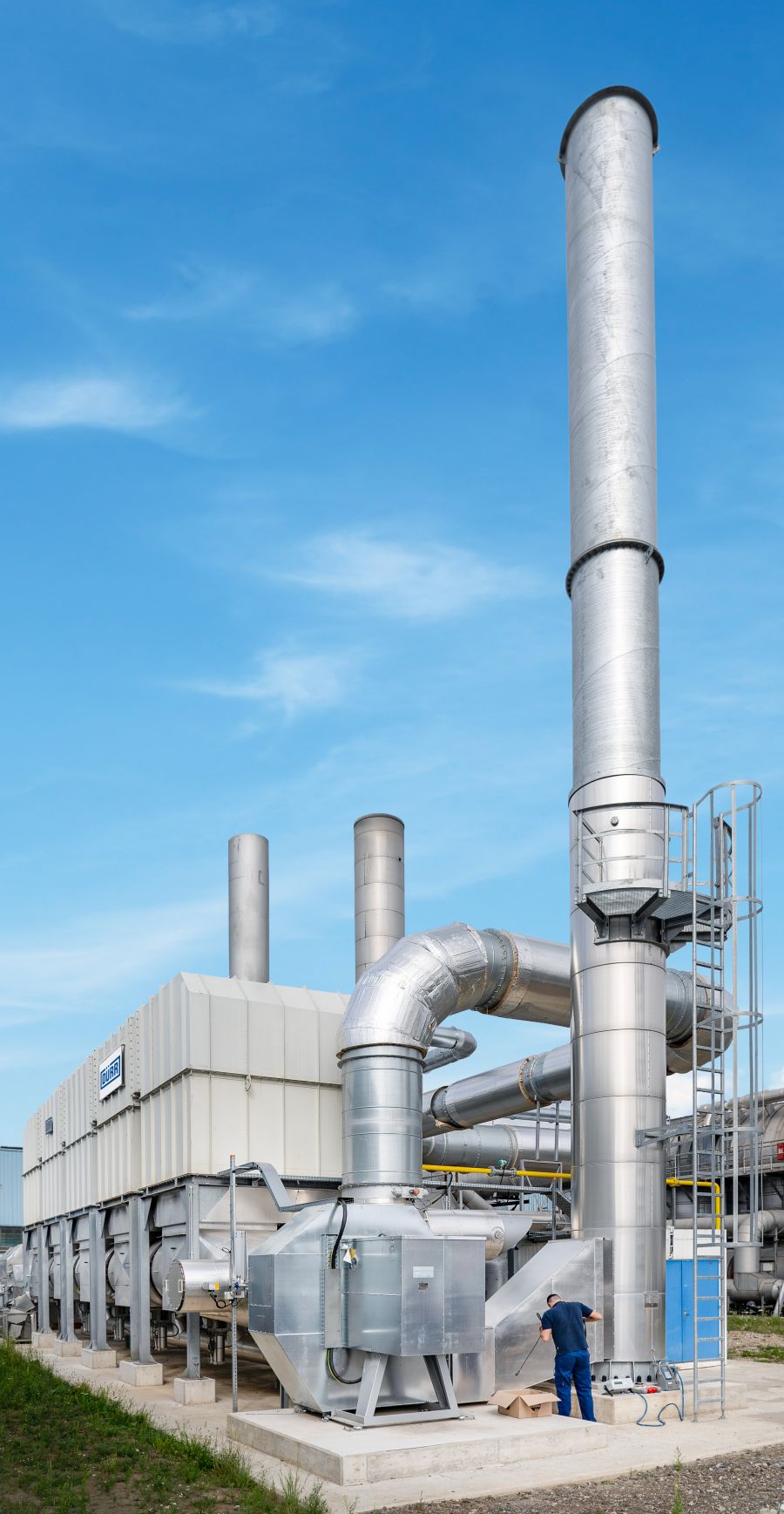
Foto: Kai Dauvermann
RTO für Dosenhersteller und Spanplatten
Zwei Anwendungsbeispiele: Beim Herstellen und Beschichten von Getränkedosen entsteht lösemittelhaltige Abluft. Die Firma Ball Beverage reinigt diese an ihrem Standort in Gelsenkirchen mit einer Dürr-RTO. Schadstoffe werden fast vollständig oxidiert, mehr als 95 % der eingesetzten Energie im Wärmespeicher zurückgewonnen und die in den heißen Abgasen enthaltene Energie zur Vorwärmung der Abluft genutzt. Die RTO verbraucht deutlich weniger Primärenergie als vergleichbare Anlagen.
In Lexington, USA, stellt das Unternehmen Egger aus St. Johan in Tirol, Österreich, seit September 2020 Spanplatten her. Bei der Spänetrocknung entstehen flüchtige organische Substanzen (VOC). Um diese zu kontrollieren, installierte Dürr ein System aus mehreren parallelen RTOs. Deren Nenndurchsatz beträgt 420 000 m3 stündlich bei einem Wärmerückgewinnungsgrad von bis zu 97 %. Die amerikanischen VOC-Grenzwerte werden damit sicher eingehalten. Jede der RTOs verfügt über ein patentiertes Schaltventil, das den Wartungsaufwand im Hinblick auf die im Rohgas enthaltenen Stäube minimiert und Druckspitzen zurück zum Trockner fast eliminiert, wodurch der Trockner sich besser steuern lässt und energieeffizienter arbeitet. Darüber hinaus hat Dürr für das verwendete Wärmespeichermaterial eine Materialkombination entwickelt, die exakt auf die Bedürfnisse der Holzwerkstoffindustrie zugeschnitten ist. Da es den thermischen Wirkungsgrad maximiert und die Wartung des Wärmetauscherbettes minimiert, streckt sich bei niedrigen Betriebskosten die Betriebszeit der Fertigung wesentlich.
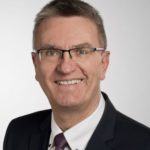
Matthias Hagen, Senior Manager Sales Clean Technology Systems, Dürr Systems AG
matthias.hagen@durr.com
Bild: Dürr