Der Schaumkreislauf
Das Essener Unternehmen Evonik hat ein neues Verfahren entwickelt, um Schaum-Matratzen aus Polyurethan zu recyceln. Das Verfahren erzielt eine sehr hohe Ausbeute und kann so dazu beitragen, viel Energie und fossile Rohstoffe einzusparen. Und es ist bereits mehr als Forschung: Am Evonik-Standort Hanau entsteht eine Pilotanlage.
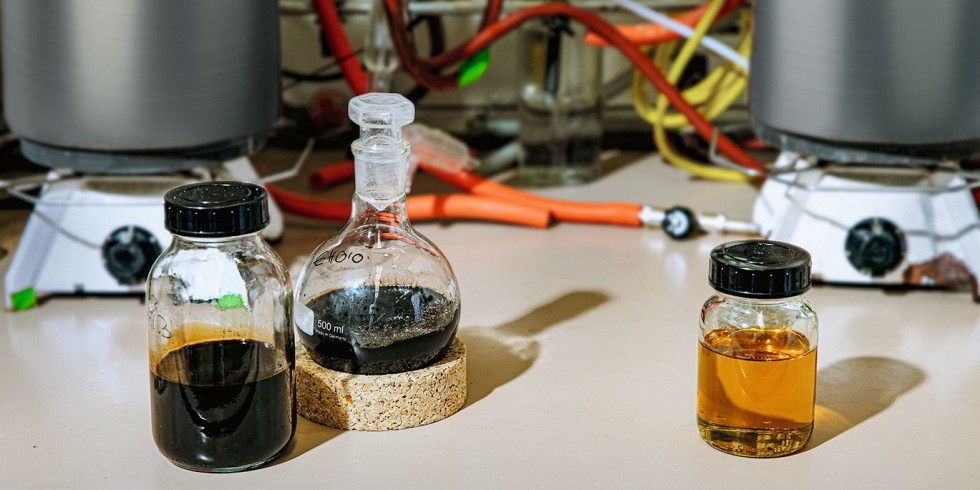
Bei Hilfe eines Katalystors werden Polyruethane in kleine Stücke gespalten. Es entsteht eine dunkelbraune Flüssigkeit, in der Polyole und Toluylendiamin (TDA) gelöst sind.
Foto: Evonik
Etwa alle fünf bis zehn Jahre wirft jeder von uns im Schnitt seine ausrangierte Matratze weg. Daraus ergibt sich ein riesiges Umweltproblem: Allein in der EU kommen Jahr für Jahr rund 40 Mio. Schlafunterlagen zusammen, die entsorgt werden müssen. Würde man sie aufeinanderlegen, ragte der Stapel 8 000 km in die Höhe. Dies entspricht einer Abfallmenge von rund 600 000 t – davon sind mehr als 300 000 t Polyurethanschaum.
Bislang landen die Matratzen zumeist auf der Mülldeponie oder werden thermisch verwertet – sprich in Kraftwerken beziehungsweise Müllverbrennungsanlagen verheizt. Klima- und umweltschonend ist das nicht: Mit jeder ausgedienten Matratze gehen die Rohstoffe und die Energie, die für Produktion und Transport verbraucht wurden, in Rauch und Wärme auf.
Das will das Essener Spezialchemikalienunternehmen Evonik ändern. Eine treibende Kraft ist die Chemikerin Annegret Terheiden. Sie hat 2018 mit Kollegen der Creavis, des Business Incubators von Evonik, ein Recyclingprojekt angestoßen. Das Ziel: ausgediente Matratzen in ihre chemischen Bestandteile zu zerlegen und wiederverwertbar zu machen. Der Prozess soll so gut sein, dass das Rezyklat mit konventionellen Rohstoffen mithalten kann.
Dieses Ziel scheint nun erreicht. Mehr als das: Anfang 2022 haben Evonik-Fachleute aus dem Life Cycle Management den ökologischen Fußabdruck des neuen Recyclingprozesses eingehend untersucht. Ihr Ergebnis: Der Prozess senkt im Vergleich zur Matratzenproduktion mit fossilen Rohstoffen den CO2-Fußabdruck deutlich um mehr als die Hälfte. „Das wollen wir noch weiter verbessern“, sagt Terheiden.
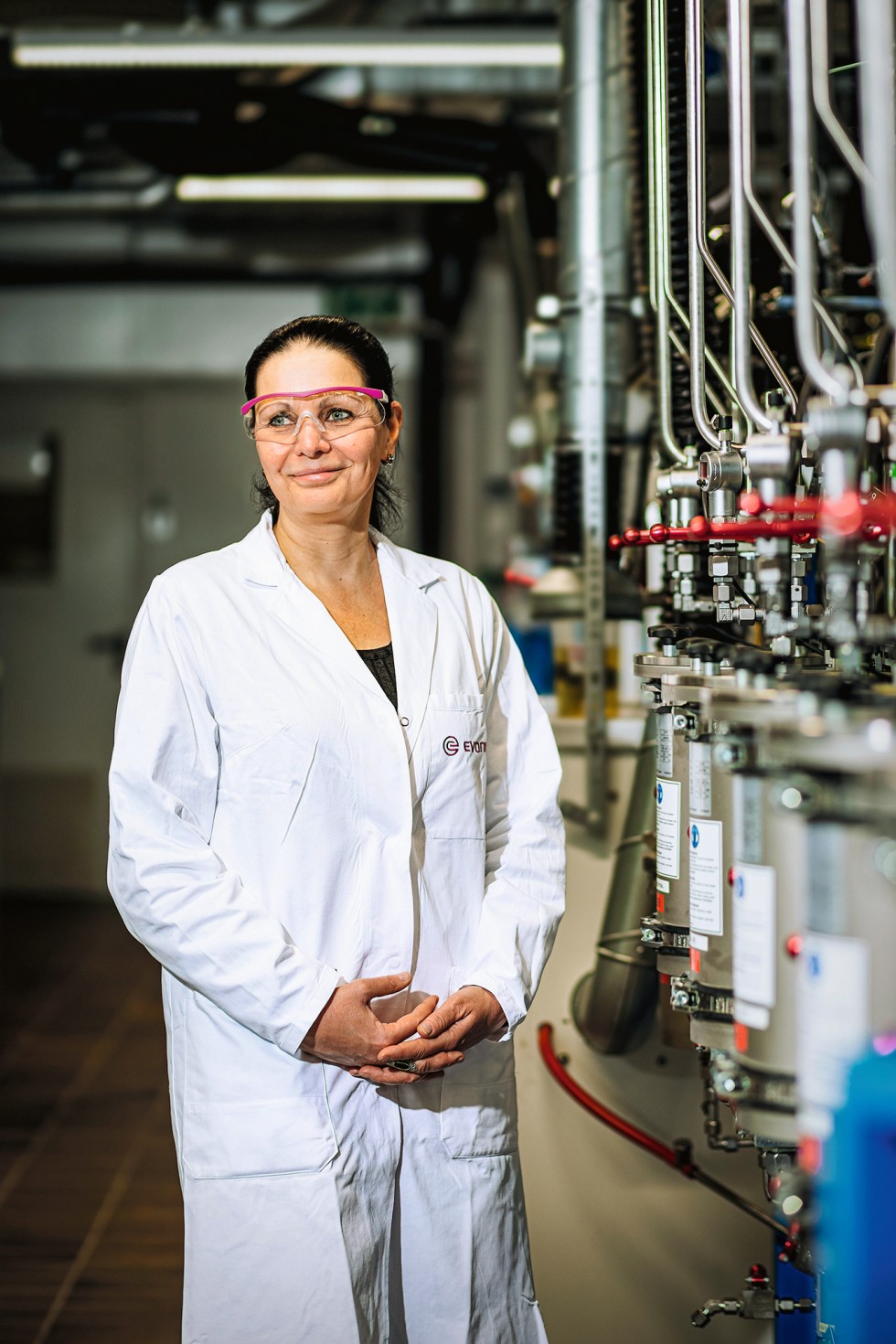
Die Chemikerin Annegret Terheiden steht im Technikum der Schaumstoffspezialisten am Standort Essen Goldschmidtstraße.
Foto: Evonik
Langlebig & schwer zu trennen
Das Material, um das es geht, ist Polyurethan. Es wird zur Herstellung unter anderem von Matratzen oder Polstermöbeln genutzt. Typische Polyurethanschäume für Matratzen entstehen aus der Reaktion von Toluol-Diisocyanaten (TDI) mit Polyetherpolyolen und Wasser unter Zugabe diverser Additive. Als Nebenprodukt der Reaktion entsteht CO2. Dieses Gas lässt das Gemisch wie eine heiße Quelle aufbrodeln. Anstatt danach wieder in sich zusammenzustürzen, behält Polyurethan seine weitmaschige Netzstruktur.
Polyurethanverbindungen sind verschleißfest. Dies kommt der Lebensdauer des Endprodukts zugute. Fürs Recycling ist diese Eigenschaft jedoch hinderlich, denn dafür müssen diese Verbindungen aufgebrochen werden.
2018 und 2019 war die Zeit günstig für den Start eines Recyclingprojekts: Evonik hat beschlossen, sich verstärkt den Themen Kreislaufwirtschaft und nachhaltige Produktion anzunehmen. Neue Produkte sowie solche aus dem vorhandenen Portfolio sollen fortan nicht nur durch ihren konkreten Nutzen, sondern auch in Nachhaltigkeitsanalysen überzeugen.
Zusätzlich bestärkt wurde Terheiden durch ein Treffen 2018 mit Fachleuten der Einrichtungskette Ikea, einer mächtigen Stimmen in der Schaumbranche. „Sie sagten uns, dass all ihre Matratzen von 2030 an vollständig aus zurückgewonnenen und erneuerbaren Rohstoffen hergestellt sein sollen“, erinnert sich Terheiden.
Hinzu kam der Blick nach Brüssel. Die EU verabschiedete die „Richtlinie über die Verringerung der Auswirkungen bestimmter Kunststoffprodukte auf die Umwelt“ – kurz „Plastik-Richtlinie“. Diese schreibt vor, dass einige Kunststoffprodukte ab 2025 zu einem Viertel aus Rezyklat bestehen müssen. „Noch wird Polyurethan nicht so streng gesehen wie Einwegplastik“, sagt Terheiden. „Es geht aber nicht darum, ob das passieren wird, sondern nur, wann.“
Doch die bis dahin kommerzialisierten Verfahren erlauben es nicht, Polyurethan wieder vollständig in Polyol und Isocyanat aufzuspalten. Statt einzelner Moleküle entstehen dabei Mischungen kurzkettiger Oligomere, die zu weit schlechteren Schaumeigenschaften führen als die ursprünglichen Zutaten. Maximal 20 % fossiles Polyol lassen sich mit diesen Verfahren bei der Herstellung neuer Matratzen ersetzen, da sonst die Produkteigenschaften leiden.
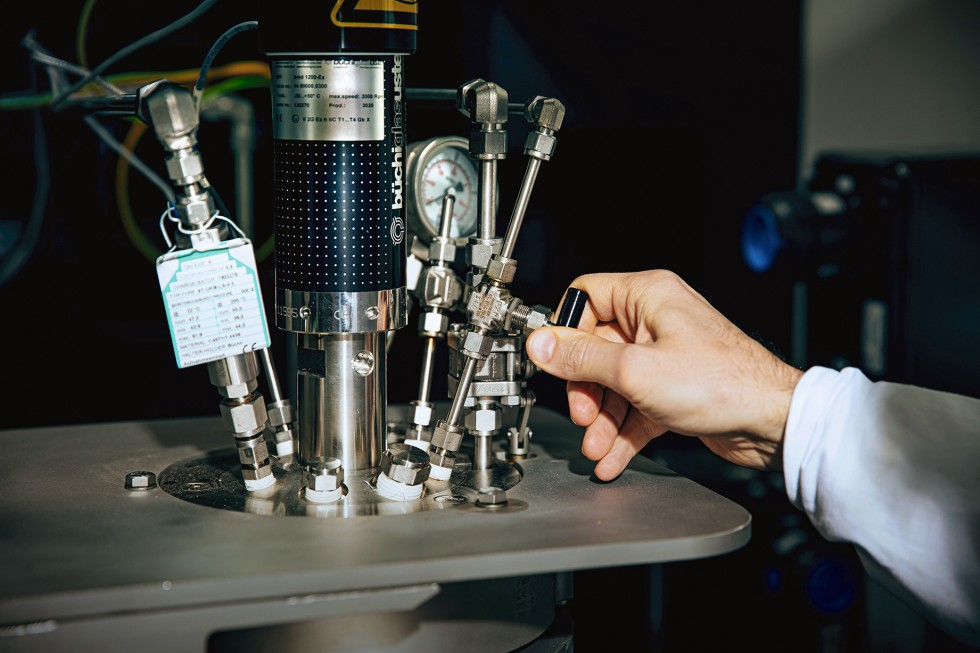
Bevor die Hydrolyse in dem 5-Liter-Reaktor startet, werden alle Leitungen überprüft und die Sensoren kalibriert.
Foto: Evonik
Klassische Hydrolyse mit Katalysator
Das war Terheiden nicht genug. Anfang 2019 begann die Forschungsarbeit. Im Forschungslabor in Essen steht hinter einer hochgefahrenen Sicherheitsscheibe ein Hydrolysereaktor mit fünf Liter Fassungsvermögen. In dieser mannshohen silbrig glänzenden Apparatur werden die Schäume mithilfe von Zusatzstoffen aufgetrennt. Für die Polyurethanspaltung nutzen der Chemiker Michael Ferenz mit seinen Kolleginnen und Kollegen ein katalytisches System. Durch die Verwendung eines Katalysators kann die Reaktion unter milderen Bedingungen ablaufen. Der Katalysator sorgt dafür, dass die nötigen chemischen Bindungen schnell und effizient gebrochen werden und die Reaktion überhaupt in einem akzeptablen Zeitraum ablaufen kann.
Wie das Ergebnis aussieht, zeigt Ferenz in einem Fläschchen. Es enthält, was nach erfolgreicher Hydrolyse von PU-Schaum übrig bleibt: eine tiefbraune Flüssigkeit, in der sich reines Polyol und ein Amin (TDA) befinden. Letzteres lässt sich in einer Folgereaktion zum Isocyanat TDI umsetzen, und so werden ebenjene Stoffe, die für die Produktion von Polyurethan benötigt werden, zurückgewonnen. Damit die Moleküle wieder zum Aufschäumen taugen, müssen sie sauber voneinander getrennt werden. „Es hat lange gedauert, bis wir so weit gekommen sind“, sagt Ferenz. Die Polyole hingegen lassen sich ohne weiteren Aufbereitungsschritt erneut verwenden.
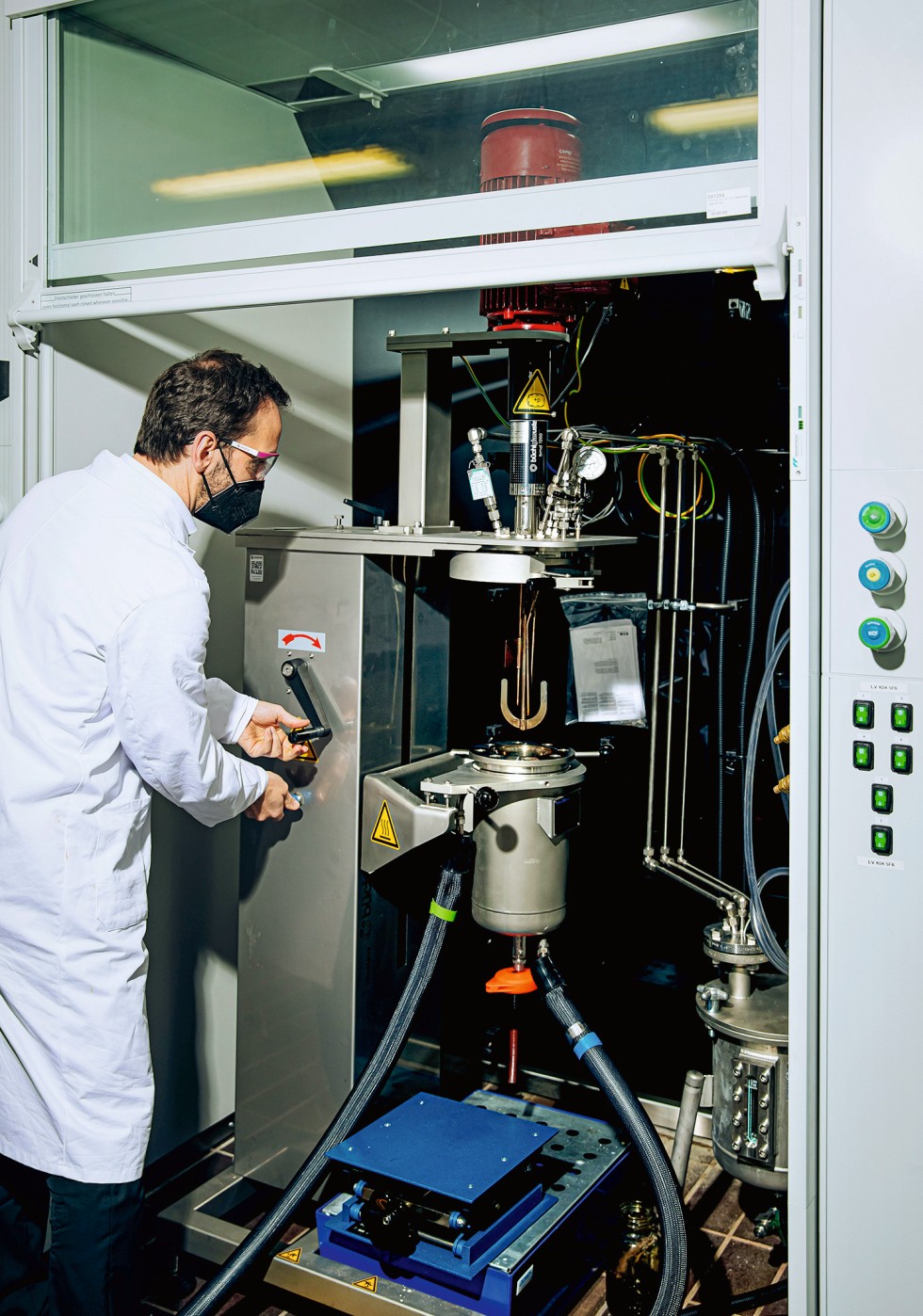
Um den Fünfliter-Hydrolyse-Reaktor mit den Reaktanden zu befüllen, muss Michael Ferenz kräftig kurbeln.
Foto: Evonik
Kreislauf ist mehr als Chemie
Doch bei den Versuchen ging es nicht nur um Chemie. Zuerst wurde der Hydrolysereaktor mit fein gemahlenem Polyurethanschnee gefüllt. „Dieser hat jedoch eine sehr niedrige Schüttdichte, was die Befüllung des Reaktors deutlich erschwert hat“, erinnert sich Ferenz. Daher wurde an anderen Darreichungsformen gearbeitet.
Nach der Beladung stellt der Experimentalchemiker die Parameter für die Versuchsanordnung ein. Auf einem Laptop, der mit dem Reaktor verkabelt ist, kann er alles steuern und kontrollieren. Bunte Kurven zeigen Temperaturen und Druck an: Rot ist die Temperatur der Ummantelung, orange die im Reaktor und blau der Druck. Die letzte Kurve zeigt die Drehzahl des Rührers. Er sorgt dafür, dass alle Reaktanden gut vermischt werden.
Ein ganzes Heer von Fachleuten ist an der Forschung beteiligt: Partikeltechniker klären, wie Matratzen besser geschreddert werden sollten, Fluidverfahrenstechniker suchen nach einer Lösung, die dunkelbraune Flüssigkeit schneller und sauberer in ihre Bestandteile aufzutrennen, Digitalisierer, Mess- und Regeltechniker, Umwelttechniker, Sicherheitstechniker. Sie alle lösen Probleme rund um den Prozess.
Ganz perfekt ist das Ergebnis noch nicht. Zwar verhalten sich die Schäume aus den recycelten Molekülen tadellos, sie sind aber bräunlich gefärbt. Aus fossilen Quellen gewonnenes Polyol ist anders als sein recycelter chemischer Zwilling farblos.
Kreislauf-Meilensteine
Partner aus der Industrie sind dennoch von dem Prozess angetan – zum Beispiel der englische Weichschaumproduzent The Vita Group mit Hauptsitz in Manchester, der hochwertige Matratzen herstellt. „Wir haben recycelte Polyole von Evonik in mehreren unserer Weichschaumformulierungen getestet, und die Resultate waren sehr positiv“, sagt Vita-Chef Ian W. Robb. Die Firma betrachtet sich als Pionier einer umweltfreundlichen Matratzenherstellung. Die hervorragende Ökobilanz des Recyclingprojekts ist für Robb daher ein entscheidender Faktor. „Wir wollen bei der Entwicklung umweltfreundlicher Technologien Vorreiter sein. Dies ist ein Meilenstein auf dem Weg hin zur Kreislaufwirtschaft.“
Bei Evonik gleicht das Recyclingprojekt mittlerweile einem gewaltigen Mosaik, an dem in mehreren Standorten parallel gearbeitet wird. Geschäftsbereiche jenseits der Schaumfachleute von Comfort & Insulation unterstützen das Projekt. So haben im Chemiepark Marl die Kolleginnen und Kollegen aus dem Bereich Crosslinkers ihre Anlagen zur Verfügung gestellt.
Das große Bild soll aber schon in wenigen Monaten in Hanau in Hessen zu sehen sein. Dort entsteht eine Pilotanlage, in der die Bestandteile von Polyurethan in größeren Mengen gewonnen werden sollen. Dafür zuständig ist Andree Blesgen. Der Projektleiter der Verfahrenstechnik stieß 2020 zum Projekt. Statt fünf Litern, wie in den bisherigen Reaktoren, soll in der neuen Anlage ein Vielfaches herauskommen. „Wir hoffen, noch 2022 in Betrieb zu gehen und mit der neuen Anlage in den Tonnenbereich vorzustoßen“, sagt Blesgen.
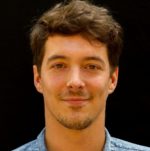
Johannes Giesler
Freier Journalist
jg@text-salon.de
Foto: Hamid Sadeghi