Alte E-Bike-Motoren instand setzen
E-Mobilität wird nachhaltiger: Fachleute bereiten Motoren, Akkus und Displays gebrauchter E-Bikes für den Wiedereinsatz auf. Sie nennen dies Refabrikation.
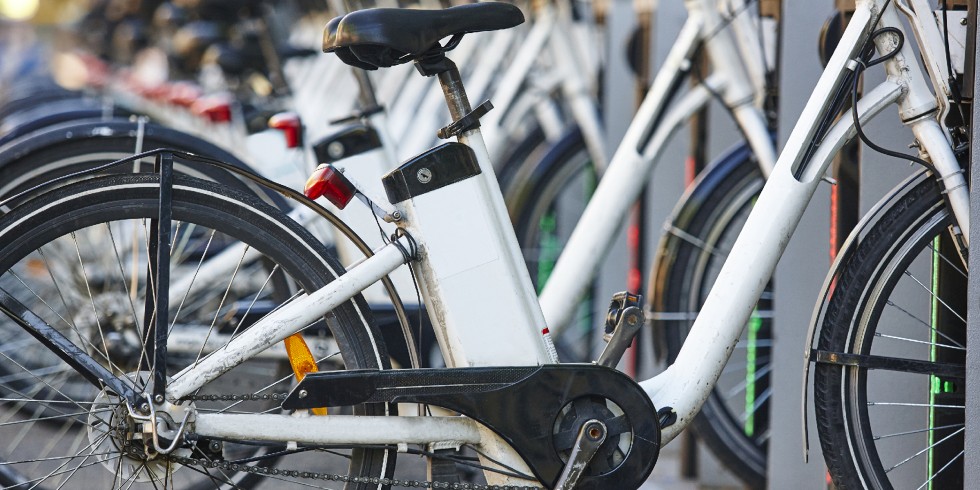
Immer mehr Elektrofahrrädern werden genutzt, immer mehr stehen an Ladestationen, immer mehr werden irgendwann nicht mehrh genutzt. Wie sich gebrauchte E-Motoren, Akkus und Displays der E-Bikes wieder in den Kreislauf zurückführen lassen, überlegen sich fünf Projektpartner.
Foto: PantherMedia/ABBPhoto
Elektrofahrräder erfreuen sich zunehmender Beliebtheit, da sie eine neue Art der Mobilität ermöglichen. Der Absatz von Elektrofahrrädern in Deutschland ist 2021 im Vergleich zum Vorjahr erneut gestiegen und hat zum ersten Mal die Marke von zwei Millionen verkauften Einheiten erreicht. Der Zweirad-Industrie-Verband (ZIV) geht in seiner Marktdatenpräsentation 2022 davon aus, dass sich dieses Wachstum weiter fortsetzt und bereits 2025 jedes zweite verkaufte Fahrrad ein Elektrofahrrad sein wird.
Die steigende Anzahl solcher Fahrräder rückt deren Lebensdauer und den Verbleib bei einem Defekt am Ende der Nutzungsphase in den Fokus. Bereits heute schätzt der ZIV den Elektrofahrradbestand in Deutschland auf rund 8,5 Millionen. Die klassische Fahrradreparatur stößt dabei an ihre Grenzen und ist häufig technisch und wirtschaftlich nicht realisierbar.
Elektrofahrrädern reparieren
Das Reparieren von Elektrofahrrädern ist aus zwei Perspektiven zu betrachten. Auf der einen Seite entspricht der Großteil der Komponenten denen eines konventionellen Fahrrads. Es handelt sich dabei meist um mechanische Bauteile, die weitgehend standardisiert und gut reparierbar sind.
Auf der anderen Seite kommen elektronische Komponenten wie Akkumulatoren, Motoren und Displays zum Einsatz. Diese teuren Komponenten lassen sich meist zwar gut ausbauen, eine Reparatur ist jedoch häufig nicht wirtschaftlich. Dies liegt unter anderem an der steigenden Variantenvielfalt, der mangelnden Standardisierung der Komponenten, dem notwendigem Spezialwerkzeug beispielsweise für die Demontage oder die Fehleranalyse, der mangelnden Verfügbarkeit von Ersatzteilen und dem notwendigen Fachwissen.
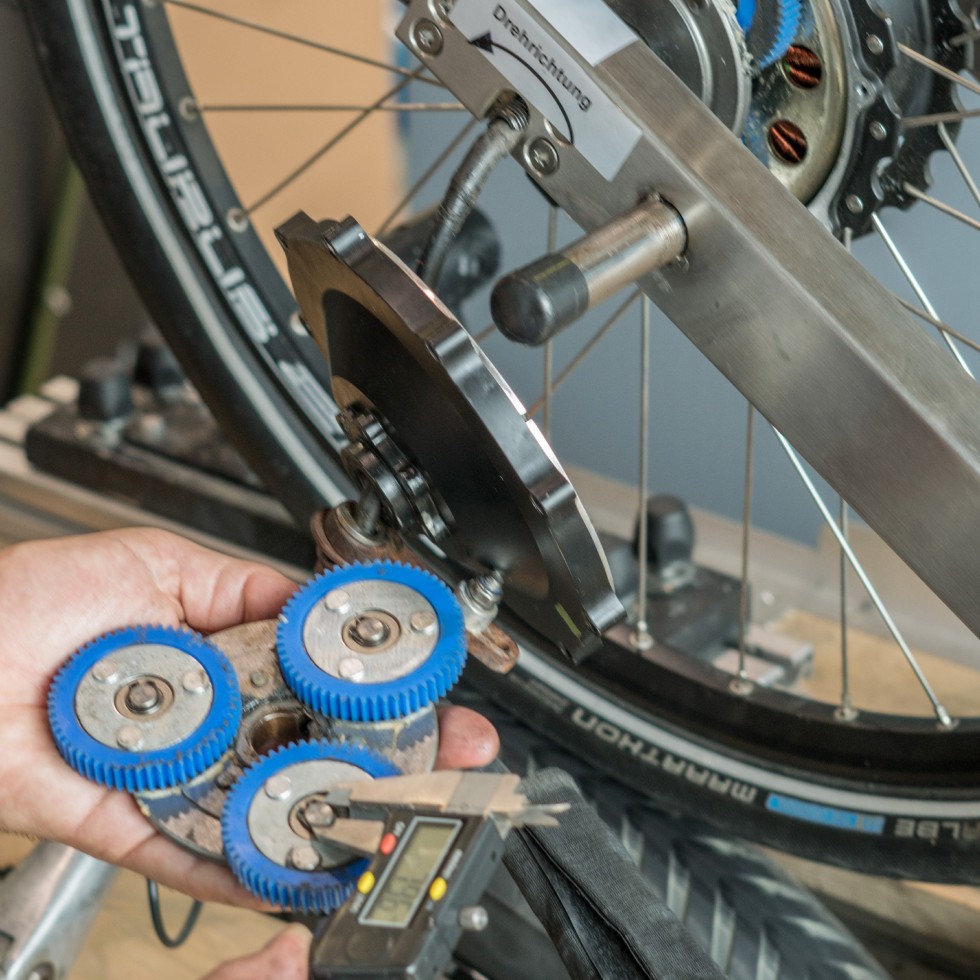
Ein aus einem E-Bike-Motor am Hinterrrad ausgebautes Planetengetriebe, das jetzt auf seine Funktionsfähigkeit geprüft wird.
Foto: David Gnad/ebike-solutions.com
Statt eine aufwendige Fehlersuche und Reparatur durchzuführen, werden defekte Motoren, Akkumulatoren und Displays aktuell in etwa zwei Drittel der Fälle durch die Fahrradwerkstatt als Ganzes gegen neue Komponenten getauscht. Dies zeigt eine Umfrage des Stuttgarter Fraunhofer-Institut für Produktionstechnik und Automatisierung IPA im Jahr 2021.
Kreislaufführung durch Aufarbeiten
Eine Alternative ist die Kreislaufführung durch das Aufarbeiten gebrauchter Geräte, also durch die so genannte Refabrikation. Wie dies in der Praxis bei Elektrofahrradmotoren gelingen kann, erforschen fünf Partner im Projekt „Werterhaltungsszenarien für urbane Elektromobilität der Personen und Lasten durch additive Fertigung und Refabrikation“, kurz AddRE-Mo. Zum Konsortium gehören die beiden Firmen Electric Bike Solutions aus Heidelberg, die auch Fahrräder zu E-Bikes umrüstet, und cirp aus dem baden-württembergischen Heimsheim, einem Dienstleister für Prototypen- und Kleinserienfertigung, sowie der Umweltcluster Bayern und das Wuppertal-Institut für Klima, Umwelt, Energie. Konsortialführer ist die Projektgruppe Prozessinnovation des Fraunhofer IPA in Bayreuth.
Alle Fünf entwickeln gemeinsam die prototypische Prozesskette der Refabrikation unter Einsatz der additiven Fertigung, also dem 3D-Druck insbesondere von Getriebezahnrädern für Elektromotoren.
Refabrikation führt zum Kreislauf
Durch die Refabrikation werden Produktkreisläufe geschlossen und unter Wahrung oder Wiederherstellung der Produktgestalt und der zugehörigen Produkteigenschaften eine Wiederverwendung gebrauchter Produkte am Ende der Nutzungsphase ermöglicht.
Im Gegensatz zur Reparatur stellt Refabrikation einen industriellen Aufarbeitungsprozess dar, bei dem das aufgearbeitete Produkt auf mindestens das Qualitätsniveau eines neuen Produkts gebracht und ein neuer Produktlebenszyklus ermöglicht wird.
Mit der Refabrikation sind sowohl ökologische und ökonomische als auch soziale Vorteile verbunden. Zum einen können hierdurch der Materialverbrauch sowie Umweltwirkung deutlich verringert werden. Zum anderen können durch den Erhalt der Produktgestalt und den verringerten Materialeinsatz Kosten gesenkt werden. Die Preise für aufgearbeitete Produkte liegen in der Regel zwischen 40 bis 80 % unter denen äquivalenter Neuprodukte, wie das Zentrum Ressourceneffizienz des VDI 2017 in der Veröffentlichung „Ressourceneffizienz durch Remanufacturing – Industrielle Aufarbeitung von Altteilen“ gezeigt hat.
Prozesskette der Refabrikation
Die Refabrikation lässt sich in sechs Hauptprozessschritte unterteilen und kann um die additive Fertigung erweitert werden. Die technische Machbarkeit der einzelnen Prozessschritte der erweiterten Prozesskette wurde im Projekt AddRE-Mo für Elektrofahrradmotoren geprüft und erprobt.
(1) Zu Beginn erfolgt die Eingangsprüfung. Dabei wird das Produkt gegebenenfalls zunächst hinsichtlich Hersteller, Modelljahr und so weiter klassifiziert und eine erste Befundung auf Produktebene durchgeführt.
(2) Anschließend wird das Produkt möglichst zerstörungsarm in Bauteile oder Baugruppen wie Gehäuseschalen, Planetengetriebe, Steuereinheit oder Stator- und Rotorsystem zerlegt.
Komponenten, die wie gebrochene Teile offensichtlich nicht für die Wiederverwendung geeignet sind, werden bereits in diesem Prozessschritt aussortiert.
(3) Anschließend werden die Komponenten gereinigt und unter anderem von Staub, Schmutz und Öl befreit.
(4) Daraufhin wird der Zustand im Rahmen der Inspektion und Sortierung beurteilt. Dazu wird eine Kombination aus Sichtprüfung zur optischen Beurteilung sowie Messungen zur Beurteilung der Funktionen durchgeführt. Basierend darauf werden die Komponenten in drei Kategorien sortiert:
- wiederverwendbar ohne Aufarbeitung
- wiederverwendbar nach Aufarbeitung
- nicht wiederverwendbar.
Komponenten die nicht wiederverwendbar sind, werden dem stofflichen Recycling zugeführt und müssen durch Neuteile ersetzt werden. Hier setzt die additive Fertigung an, mit deren Hilfe auch kleine Losgrößen und unterschiedlichste Geometrien wirtschaftlich hergestellt werden können.
Dazu wurden im Projekt AddRE-Mo die Eignung der zu ersetzenden Komponenten hinsichtlich einer additiven Nachfertigung analysiert. Einen Anwendungsfall stellen Getriebezahnräder dar, die je nach Modell unterschiedliche Geometrien aufweisen. Die additive Nachfertigung dieser Zahnräder wurde im Projekt anhand von mehr als 120 Versuchsbauteilen aus 20 verschiedenen Werkstoffen untersucht und an einem Prüfstand validiert.
(5) Anschließend erfolgt die Komponenten aufgearbeitet, um einen neuwertigen Zustand aller Komponenten sicherzustellen. Welches Verfahren für eine mechanische Aufarbeitung geeignet ist, hängt vom jeweiligen Teil und den Anforderungen an etwa der Maßhaltigkeit, dem Abnutzungsvorrat und der Haltbarkeit ab.
(6) Im letzten Schritt werden aufgearbeitete und neue Teile zu neuwertigen Produkten zusammengesetzt. Schließlich wird jedes Produkt einer abschließenden Endprüfung unterzogen.
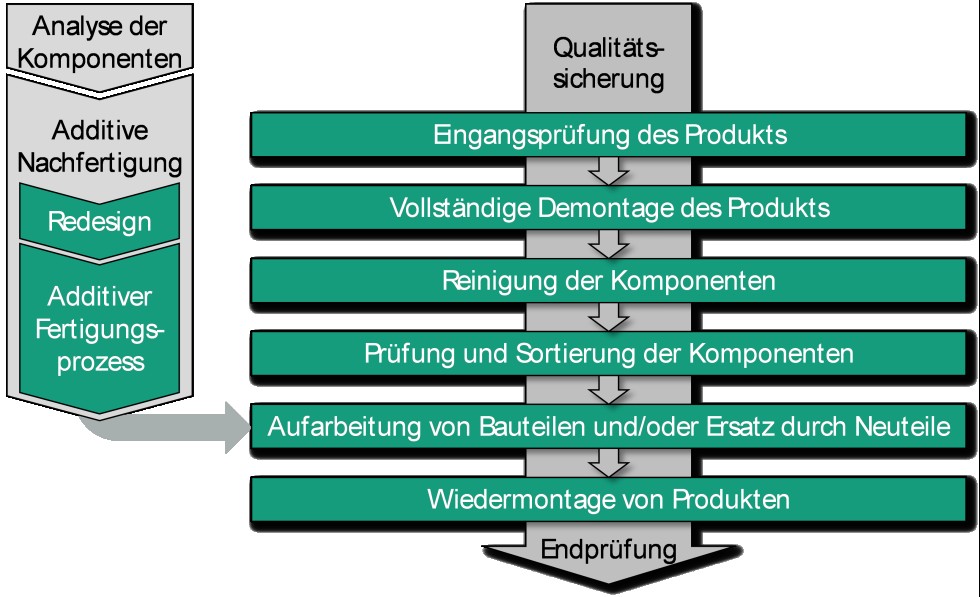
Erweiterte Prozesskette der Refabrikation unter Berücksichtigung der additiven Fertigung. Grafik: Fraunhofer IPA, modifiziert nach Kleylein-Feuerstein, J., Autarkie der Langzeitverfügbarkeit technischer Produkte mittels additiver Fertigung. Shaker Verlag, Düren, 2019
Chancen und Herausforderungen
Künftig werden modulare, flexible und automatisierte Prozessschritte eine wichtige Grundlage für eine wirtschaftliche Refabrikation von Elektrofahrradmotoren bilden. Dies ermöglicht sowohl die Bewältigung des zu erwartenden hohen Mengenaufkommens an solchen Motoren am Ende der Nutzungsphase, als auch die Anpassung an Mengenschwankungen im saisonalen Elektrofahrradgeschäft.
Voraussetzung für die Refabrikation dieser Motoren ist zunächst deren Rückführung vom einzelnen Nutzer zum Aufarbeitungsunternehmen. Dies ist vor allem für Komponentenhersteller eine Herausforderung, weil das Eigentum am Motor an den Endkund*innen übergeht und der direkte Kontakt zu denen fehlt und erst später punktuell etwa bei der Wartung des Elektrofahrrads in einer angebundenen Fachwerkstatt hergestellt werden kann. Wann und in welcher Menge Elektrofahrradmotoren von den Nutzer*innen zurückgegeben werden und in welchem Zustand sich diese befinden kann daher nur bedingt beeinflusst werden. Hier bieten Geschäftsmodelle in Form von Produkt-Service-Systemen wie das Leasing oder Mietmodelle eine Chance, um Mengenschwankungen zu glätten und bereits in der Nutzungsphase Daten über den Zustand des Motors zu erheben.
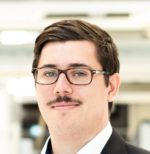
Jan Koller
Gruppenleiter, Fraunhofer-Institut für Produktionstechnik und Automatisierung IPA
jan.koller@ipa.fraunhofer.de
Foto: Fraunhofer IPA