Kupfer: vereinzelt statt verhakt
Ein bayrisches Unternehmen verbessert das Kupferrecycling. Mit einem angepassten Schredder und einer Prallmühle lässt sich mehr des Metalls zurückgewinnen.
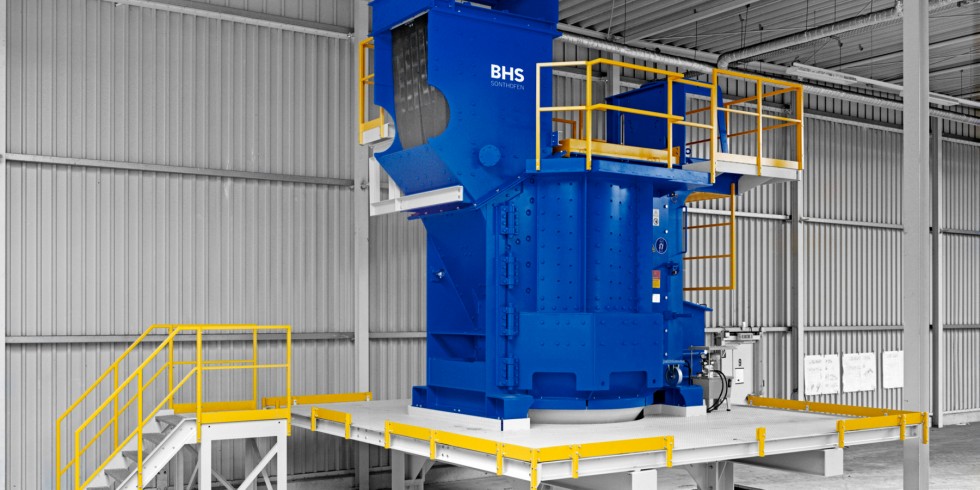
Der Rotorshredder vom Typ RS der Firma BHS-Sonthofen beim Aufbau einer E-Schrott-Recyclinganlage eines Kunden in Deutschland.
Foto: BHS-Sonthofen
Kupfer ist ein besonderes Metall. Es leitet sehr gut Strom und Wärme und wird etwa in elektrische Leitungen, Wärmetauschern und Elektromotoren eingesetzt. Es ist auch wertvolles. Für Recycler lohnt es sich, Kupfer aus alten Geräten und Maschinen auszusortieren.
Der Allgäuer Maschinen- und Anlagenbauer BHS-Sonthofen hat nun ein neues Verfahren entwickelt, um die Kupferausbeute bei der Verarbeitung sogenannter „Meatballs“ zu erhöhen. Unter diesen „Fleischklößchen“, so die direkte Übersetzung, verstehen Recycler Elektromotoren und Motoranker, also die drehbaren Teile von Motoren. Diese Meatballs enthalten bis zu 22 % Kupfer und sind eine Restfraktion aus der Müllverbrennung oder einem Großschredder, die sich nur schwer sortenrein aufschließen lässt.
Das ändert sich. Das neue Allgäuer Verfahren basiert auf einen auf diese Verarbeitung angepassten Rotorshredder vom Typ RS, der anschließenden stofflichen Trennung und der qualitativen Aufbereitung des Kupfers in einer Rotorprallmühle.
Höhere Recyclingquoten …
Der Anlass für das Unternehmen, den Rotorschredder zu optimieren, war, dass ein Kunde aus den Niederlanden sein Verfahren zur Verwertung von Meatballs verbessern wollte, um deutlich höhere Gehalte an Nichteisenmetallen wie Kupfer zu gewinnen.
Klassisch zerkleinert eine Hammermühle die Motoren und Anker. Die zerkleinerten Teile berühren sich dabei und können sich ineinander verhaken. Die resultierenden Metallverbunde machen eine sortenreine Trennung fast unmöglich. Auch sind die Auswürfe bei Hammermühlen so konstruiert, dass sich Einzelteile zwangsläufig verhaken.
Die größte Herausforderung bestand also darin, den wertvollen Schrott bei dem Zerkleinern so zu vereinzeln, dass eine anschließende sortenreine Trennung möglich ist.
Die BHS-Fachleute haben mit dem Kunden den Prozess analysiert und verschiedene Versuche mit dem Kundenmaterial im BHS-Testzentrum in Sonthofen durchgeführt. Das Ergebnis ist ein in vielen Details verbessertes Verfahren, das exakt auf diese Anwendung zugeschnitten ist.
… durchs Vereinzeln
Im Rotorshredder werden die Meatballs auseinandergebrochen. Einzelne Teile wie Stahlwellen bleiben erhalten und lassen sich aussortieren. Der Auswurf aus dem Schredder ist zudem so konzipiert, dass die zerkleinerten Teile auf voller Breite und ohne sich zu berühren auf das Austragsband fallen. Dies stellt sicher, dass sich das Material nicht mehr verhaken kann.
Eisen abtrennen
Nach dem Auswurf läuft das geschredderte Metall unter einem längs zum Austragsband angeordneten Überbandmagneten durch, der eisenhaltige Teile abtrennt. Auch dieser Recyclingschritt wurde verbessert: Wäre dieser Magnet, wie üblich, quer angebracht, würden längere Eisenteile über das Band schleifen und sich mit anderen Stücken verhaken. Dank der Anpassung können die restlichen Teile unbehindert über das Band laufen. Ein Querstromsichter befreit schließlich die Kupferfraktion mithilfe eines Luftstroms von Edelstahlteilen und erhitzten unmagnetischen Eisenteilen.
Saubere Kupferfraktion
Um die gewonnene Kupferfraktion von Unreinheiten zu befreien, kombiniert BHS-Sonthofen den Schredder mit der Rotorprallmühle vom Typ RPMX. Diese zeichnet sich durch eine hohe Umfangsgeschwindigkeit und einen schmaleren Mahlspalt aus. Dies gewährleistet einen gleichbleibend guten Output über die Lebensdauer der Maschine. Das Ergebnis ist hochwertiges Metallkonzentrat, das qualitativ auf einer Stufe mit aus Kabeln recyceltem Kupfer steht.
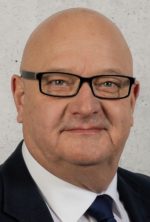
Ulrich Kanzleiter
Gebietsverkaufsleiter im Bereich Recycling & Umwelttechnologie BHS-Sonthofen GmbH
ulrich.kanzleiter@bhs-sonthofen.de
Foto: BHS-Sonthofen