„Die Fabrik von morgen wird ein Rechenzentrum sein“
Wie lassen sich IT und OT, also Informationstechnologien und operative Technologien, erfolgreich in der Fertigungsautomation miteinander vernetzen? Welche Herausforderungen haben Unternehmen für einen zielführenden Einsatz von Industrial Metaverse & KI noch zu meistern?
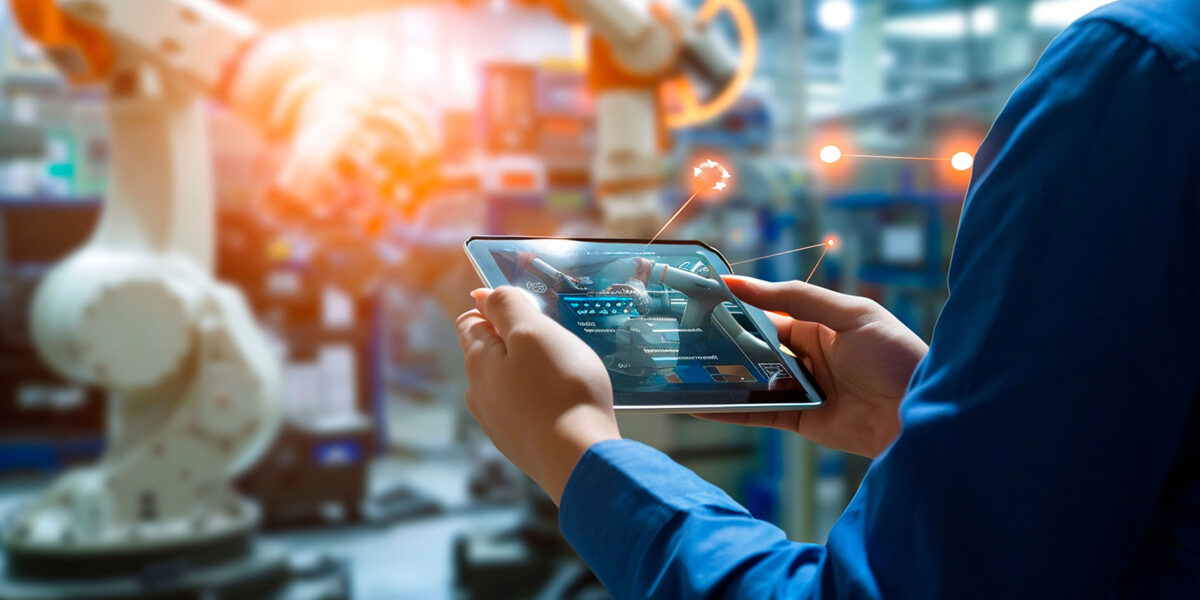
Fertigungsunternehmen kommen in den sich ständig ändernden Marktumfeldern mit hoher internationaler Wettbewerbsdynamik schnell an ihre Grenzen. Die „Fabrik als Rechenzentrum“ kann für Abhilfe sorgen. Grafik: stock.adobe.com
Und nicht zuletzt: Wie können die Technologien zu einer nachhaltigen und resilienten Produktion beitragen? Über diese und weitere Fragen wird die internationale Fachwelt im Rahmen des „Automatisierungskongresses“ 2024 am 2. und 3. Juli 2024 im Kongresshaus in Baden-Baden diskutieren. „Die Fabrik der Zukunft ist ein Rechenzentrum“, so lautet der Vortrag von Jens Mueller, CEO der Ascon Systems Holding GmbH, Stuttgart. Im Interview gibt er vorab erste Einblicke in seine Thesen.
VDI-Z: Herr Müller, welche Erwartungen verknüpfen Sie mit dem Bild von der „Fabrik als Rechenzentrum“?
Jens Mueller: Das Bild von der Fabrik, die als Rechenzentrum geführt wird, ist die Schlussfolgerung aus den Entwicklungen, die wir derzeit in der Fertigungsindustrie sehen. Dazu gehören eine datenzentrierte Entscheidungsfindung, Automatisierung und natürlich der Einsatz von maschinellem Lernen und Künstlicher Intelligenz (KI). Die Vernetzung von und mit Geräten und die Integration verschiedener Technologien sorgen für eine verbesserte Koordination und Flexibilität in der Produktion. Sensoren, IoT-Geräte, digitale Zwillinge und Simulationen liefern permanent Datenströme. Datenanalyse und Datenverarbeitung sind zentral für den Betrieb. Diese Herangehensweise an Fertigungsprozesse ist vergleichbar mit der Art und Weise, wie Rechenzentren funktionieren, wie sie ihre Ressourcen verwalten und verteilen. Und das verändert von Grund auf, wie Fabriken für die Zukunft geplant und entwickelt werden. Dabei sind alle Bereiche der Produktlebenszyklen mit einbezogen, von der Materialbeschaffung über die Produktion bis zur Qualitätssicherung und Logistik.
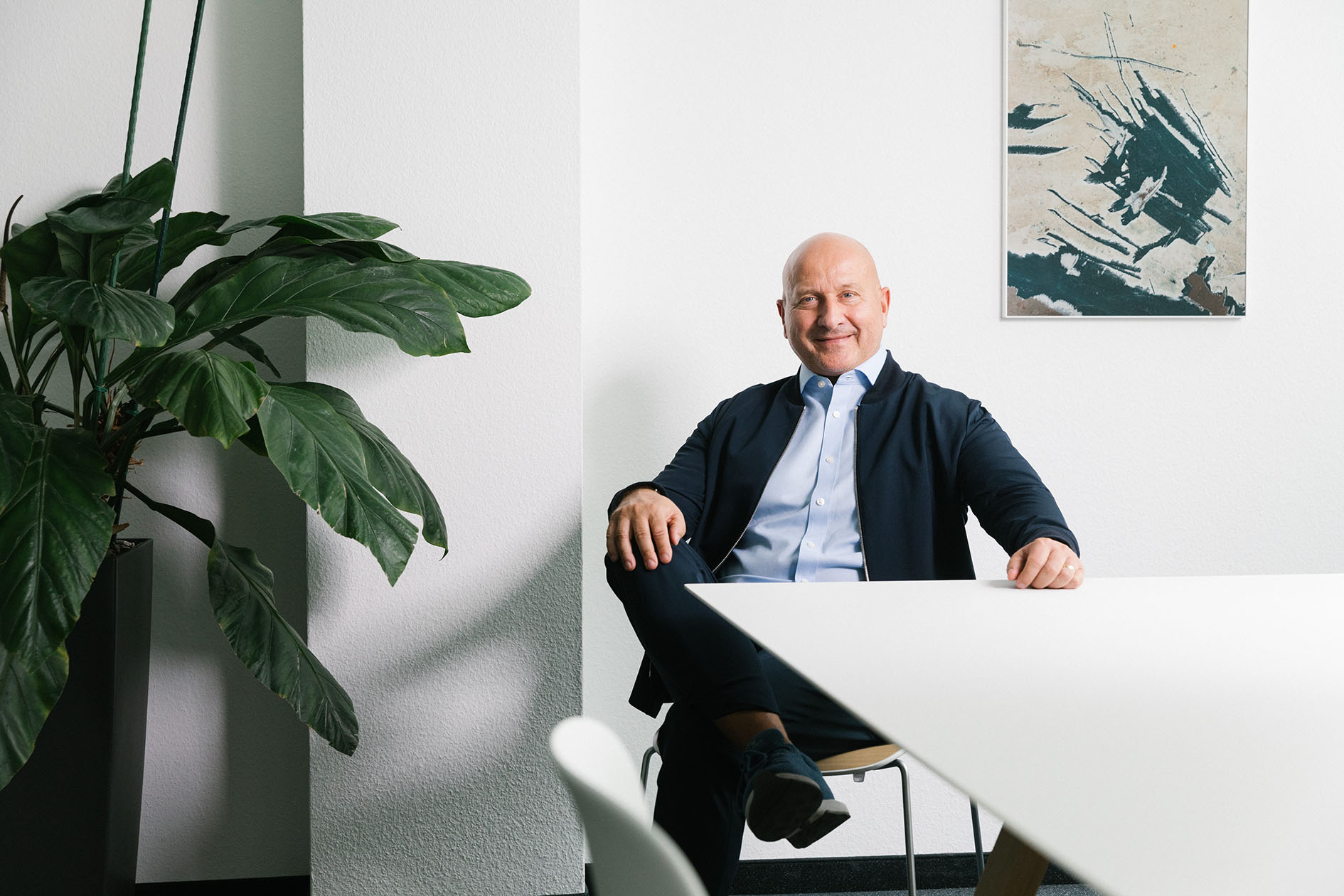
Jens Mueller, CEO der Ascon Systems Holding GmbH aus Stuttgart, stellt seine spannenden Thesen auf dem 25. VDI-Kongress Automation in Baden-Baden vor.
Foto: Ascon
VDI-Z: Was sind aktuell die größten Kernherausforderungen, die auf diesem Weg noch zu lösen sind?
Jens Mueller: Die Lösungen sind da, die Herausforderungen liegen darin, sie ein- und umzusetzen. Wir sehen ein nach wie vor ausgeprägtes Silo-Denken und eine starre Automatisierungspyramide, die Konvergenzen zwischen IT und OT verhindert. Die Geräte sind unzureichend mit Sensoren ausgestattet. Das sorgt für Hürden bei der Vernetzung und für eine schlechte Datenbasis. Dazu kommen Engpässe in Lieferketten, Dekarbonisierung und Fachkräftemangel. Das sind Rahmenbedingungen, mit denen Unternehmen in den sich ständig verändernden Marktumfeldern und mit einer hohen internationalen Wettbewerbsdynamik schnell an ihre Grenzen kommen. Wir können das ändern, denn wir haben die Technologien und das Prozesswissen, mit denen wir die Transformation abschließen können. Wenn wir diese Lösungen orchestrieren, führt das zu einer vernetzten Produktion – mit einer konvergenten IT-Infrastruktur, hoher Skalierbarkeit, Effizienzgewinnen, mehr Flexibilität und damit Vorteilen gegenüber Mitbewerbern.
VDI-Z: Wann und in welcher Form wird das Industrial Metaverse das vollständige Potenzial ausschöpfen können?
Jens Mueller: Im Industrial Metaverse verschmelzen die digitale und die reale Welt in der Fertigung. Das volle Potenzial ist immer dann ausgeschöpft, wenn die aktuellen Technologien ineinandergreifen und zusammenspielen. Das Industrial Metaverse entwickelt sich ständig weiter und ist in einem Prozess der permanenten Optimierung und Integration neuer Technologien. Im Arbeitsalltag sind Virtual Reality und Augmented Reality für Simulationen und Ergänzungen von realen physischen Umgebungen in der digitalen Welt allgegenwärtig. Genauso wie digitale Zwillinge: Sie bilden jeden Aspekt der Fertigung ab und ermöglichen Interaktionen und Anpassungen in Echtzeit. Alle Daten-relevanten Geräte sind an das Internet der Dinge angebunden. Daten-Operationen erfolgen über skalierbares Cloud-Computing und hochleistungsfähige Netzwerktechnologien. In einigen Unternehmen ist das Industrial Metaverse bereits Realität.
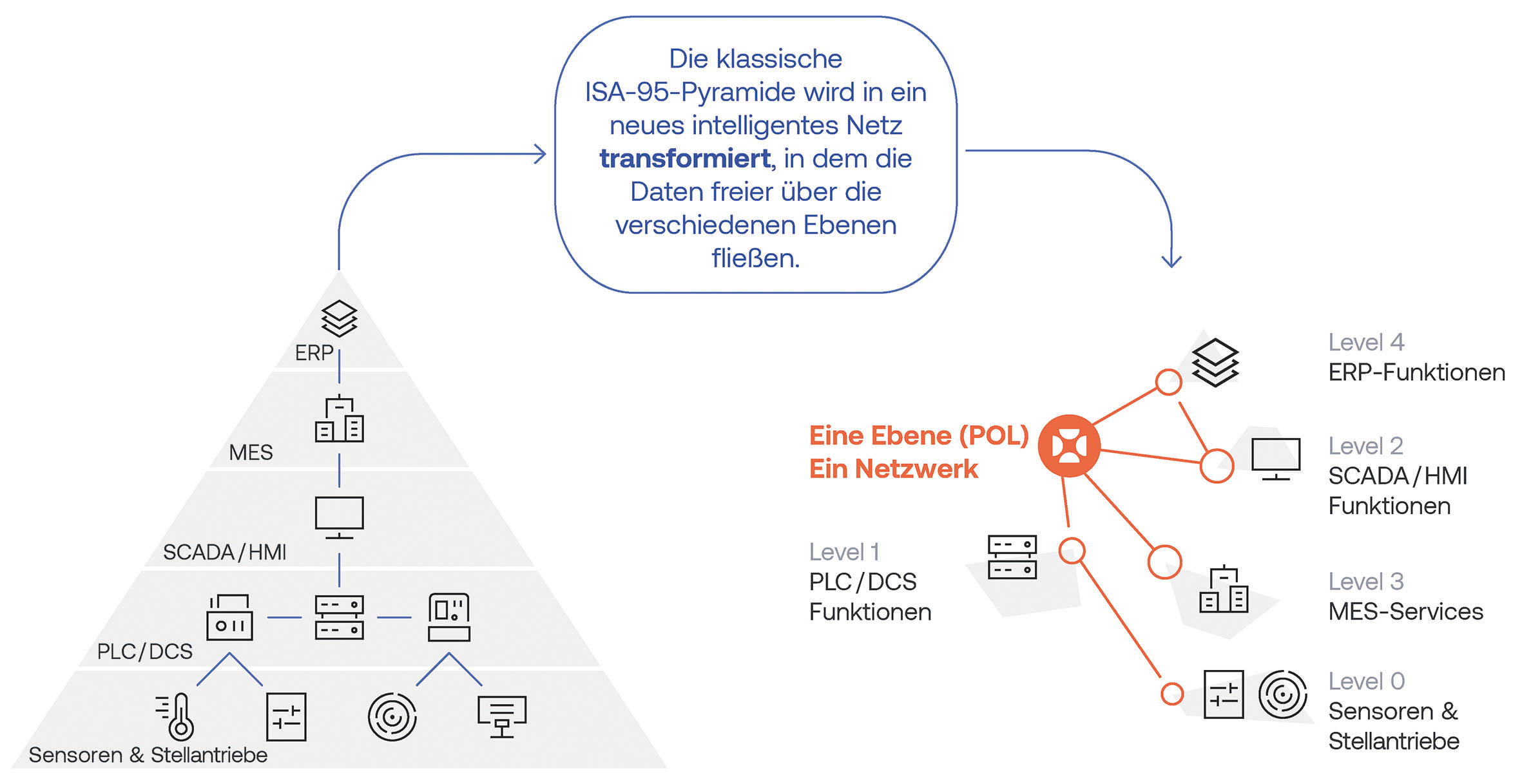
Grundvoraussetzung ist die Transformation der klassischen starren Automatisierungspyramide, die Konvergenzen zwischen IT und OT verhindert, zum intelligenten Netzwerk. Grafik: Ascon
VDI-Z: In welcher Weise können die neuen Konzepte zu mehr Nachhaltigkeit und zu mehr Resilienz beitragen?
Jens Mueller: Die Resilienz der Fabriken wächst über die Steigerung der Anpassungsfähigkeit und Flexibilität, wie sie durch Automatisierung, digitale Zwillinge, Simulationen und Data Science und die vernetzten Systeme entstehen. Durch die cloudbasierten Technologien wird eine weltweite Zusammenarbeit möglich. Das ist unter dem Gesichtspunkt Nachhaltigkeit wichtig, denn es fallen beispielsweise erheblich weniger Geschäftsreisen an. Enorm großes Potenzial vor allem auch für eine zirkuläre Wirtschaft liegt in digitalen Zwillingen. Sie sorgen dafür, dass Maschinen nicht mehr neu gebaut, sondern über Software neu- oder umprogrammiert werden können. Das spart Rohstoffe und Energie, vorhandene Ressourcen werden effizienter genutzt. Weitere Nachhaltigkeitsgewinne entstehen durch die Verfügbarkeit von Daten, die Auskunft über den Material- und Ressourcenverbrauch entlang der Produktlebenszyklen geben. Je nach Unternehmen und Ursprungsland ist es sogar bereits gesetzlich vorgeschrieben, diese Informationen zu dokumentieren. Unabhängig davon besteht aber auch den Wunsch auf Seiten der Unternehmen, ihre Lieferketten besser zu kennen, um sie auf dieser Wissensbasis optimieren zu können. Zumal mit der Datentransparenz Einbußen in der Qualität aufgedeckt werden können, was dann im weiteren Verlauf zu weniger Ausschussware, Abfall und Elektroschrott führt.
VDI-Z: Herr Müller, wird es Zeit für die „Industrie 5.0“? Und was bedeutet das für die Fertigungsindustrie in fünf bis zehn Jahren?
Jens Mueller: Der Übergang zur Industrie 5.0 läuft bereits. Die Errungenschaften aus der Industrie 4.0 mit KI, Echtzeit-Datenanalysen, Automatisierung und intelligenter Vernetzung bleiben erhalten. Aber sie werden holistisch ausgebaut und erweitert. Der Fokus liegt jetzt auf humanzentrierten Technologien, Nachhaltigkeit und resilienten Lieferketten. Zu den Prinzipien der Industrie 5.0 und damit auch zu den Leitplanken für die Fertigungsindustrie der Zukunft gehört, die Kreativität des Menschen mit KI und der Präzision der Maschinen und automatisierten Prozessen zu verbinden.
Mensch und Maschine arbeiten zusammen: Der Mensch denkt – gerne auch KI-unterstützt–, und die Maschine handelt. Produkte werden aufgrund der Flexibilität der Prozesse personalisierter und in kleineren Mengen produzierbar. Das Zusammenspiel von Industrial Metaverse und Industrie 5.0 ist dabei ideal. Die Synergien entstehen, indem fortschrittlichste Technologien und menschliche Werte zusammenkommen. Sie ermöglichen eine nachhaltige und zukunftsfähige Industrie 5.0
VDI-Z: Herr Müller, wir danken Ihnen für die spannenden Ausführungen.
Mehr Infos zum Kongress
Im Rahmen des 25. Automatisierungskongresses werden die betrachteten Zukunftsthemen breiten Raum einnehmen. Mit über 100 Fachbeiträgen, einer interessanten Fach- und Posterausstellung, anregenden Diskussionsrunden, ausreichend Raum für vertiefende Gespräche sowie der exklusiven Abendveranstaltung im Kurhaus Baden-Baden begeistert der Kongress regelmäßig um die 500 Experten der Mess- und Automatisierungstechnik. Fachlicher Träger ist die VDI/VDE-GMA (Gesellschaft Mess- und Automatisierungstechnik): In der GMA bündeln der VDI und der Verband der Elektrotechnik Elektronik Informationstechnik (VDE) die gemeinsamen Aktivitäten im Bereich Mess- und Automatisierungstechnik. Anmeldung und Programm gibt es unter www.automatisierungskongress.de oder über das VDI Wissensforum Kundenzentrum, Postfach 10 11 39, 40002 Düsseldorf, E-Mail: wissensforum@vdi.de, Telefon: +49 211 6214–201, Telefax: -154.
Das könnte Sie auch interessieren:
Mehr Sicherheit: Lastenheft für industrielle Bildverarbeitungssysteme
Arbeitsgruppe „OPC UA für KI“ soll Fertigungslösungen vorantreiben