Komplexer Entwicklungsprozess von Skizzen bis zum Fräsen
Designstudien reichen in der Automobilindustrie vom ersten Skizzieren eines geplanten neuen Fahrzeugmodells bis zum Fräsen mithilfe von Robotern. Die Synergie von „Mensch und Maschine“ formt so das Auto der Zukunft.
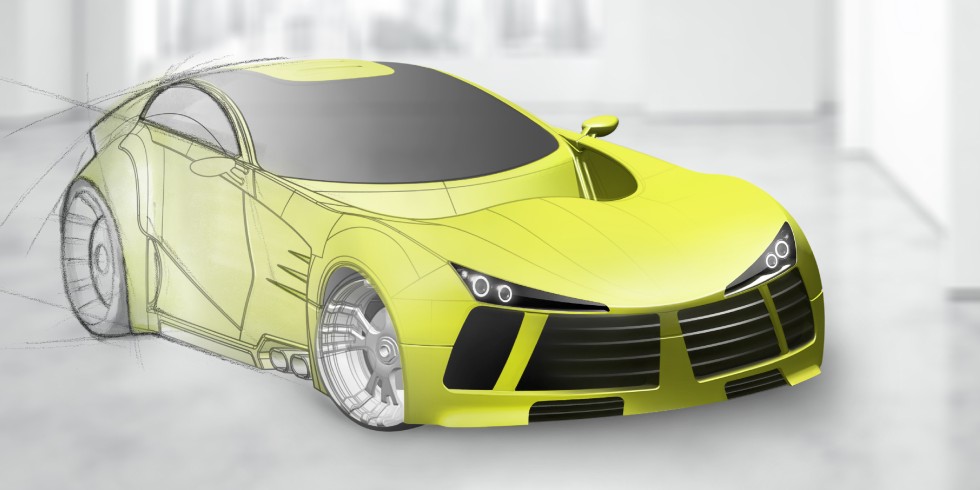
In der Automobilindustrie sind kürzere Entwicklungszyklen – mit immer neuen Innovationen und ohne Qualitätsverlust – zwingend erforderlich. Eine Innovation ist das Roboterfräsen der Modelle aus Blockmaterial. Grafik: invenio
Die Technik sowie die Formgebung zeitgenössischer Personenkraftwagen haben sich in der Historie der Automobilindustrie fundamental weiterentwickelt. Das Ergebnis ist ein sowohl in gestalterischen, als auch technischen Komponenten stimmiges Gesamtbild eines jeden Fahrzeuges. Auch der Entwicklungsprozess als solcher hat in den vergangenen Jahrhunderten einen umfassenden Wandel erfahren, um leistungsstarke und qualitativ anspruchsvolle Verkehrsmittel zeitsparend zu entwerfen und schlussendlich in Serie zu fertigen: Digitale Lösungen, flexible Industrie-Roboter und smarte Software-Technologien prägen das Bild der Automobil-Produktion unserer heutigen Zeit. Die Industrie 4.0 ermöglicht in der Fahrzeugentwicklung einen hohen Automatisierungsgrad und steigert nachhaltig die Effizienz.
Große Anzahl an Entwicklungsschritten bewältigen
Die Vielzahl der Schritte bei der Konzeption von Kraftfahrzeugen beginnt bereits bei Designstudien für Automobil-Messen. Diese Studien dienen dazu, ein neuartiges Automobil-Konzept, auch Show-Modell oder Showcar genannt, dem Messe-Publikum vorzustellen und aus den Reaktionen herauszulesen, welche Aspekte möglicherweise in die Serienfertigung übernommen werden können.
Technische und funktionale Parameter müssen noch nicht zwingend gegeben sein – es soll lediglich der äußere Charakter der Karosserie zur Schau gestellt werden. Dennoch ist ein solches Show-Modell sehr zeitintensiv. Dank modernster Automatisierungslösungen können bereits in der frühen Gestaltungsphase Arbeitsaufwände reduziert werden – mit individuellen Lösungen wird eine Vielzahl von Handgriffen durch Knopfdruck auf ein Minimum beschränkt. Doch trotz des Computer-Zeitalters ist die manuelle Arbeit an Ton-Modellen aus Industrieplastilin (Clay) nicht wegzudenken. Es gilt, das Zusammenspiel von moderner Technik und präziser Handarbeit miteinander zu kombinieren. In abstimmungsintensiven Designstudien werden diese Synergien bereits erfolgreich genutzt, um sowohl Zeit als auch Kosten einzusparen.
Konzepte und Zeichnungen – die Ausgangsbasis
Neben den individuellen Bedürfnissen und Anforderungen entscheidet maßgeblich der erste Eindruck über den Verkaufserfolg eines Fahrzeuges. Um bei der Ideenfindung eines neuen Autos die ersten Zielvorstellungen zu visualisieren, bedienen sich die Fachabteilungen nach wie vor der klassischen Skizzen-Konstruktion. Ein vorher erarbeitetes Konzept beschreibt den Charakter der zu entwickelnden Karosserie. Die darin definierten Begrifflichkeiten müssen in der Linienführung von einfachen, zweidimensionalen Skizzen, sogenannten Daumennagel-Skizzen, berücksichtigt und bestmöglich umgesetzt werden. Aus der Entwurfssammlung werden diejenigen Zeichnungen selektiert und in Schnell-Skizzen ausgearbeitet, die den Anforderungen und Eingrenzungen der Designer entsprechen.
Die Ausführung dieser Schnell-Skizzen – retuschiert in Farbe und in der Größe eines DIN A4-Blattes – erfolgt seit Mitte der neunziger Jahre des vergangenen Jahrhunderts vermehrt durch den Einsatz von Computer-Software. Die digitale Bearbeitung erleichtert und unterstreicht die skizzenbasierte Gestaltung natürlicher Phänomene bei der gewünschten Formgebung, wie beispielsweise Aussehen, Reflexionen und Schatten. Die Fahrzeugentwürfe erhalten dadurch einen realistischen Charakter anhand dessen die Erfüllung des definierten Konzeptes nochmals geprüft wird.
Auf Basis der Zeichnungen wird anschließend ein favorisiertes Design ermittelt, das bis zum maßstäblichen Modell ausgearbeitet wird. Die ausgewählte Karosserie erfährt die Umsetzung perspektivischer, dreidimensionaler Skizzen, die dazu dienen, einen ersten Eindruck der Gesamt-Geometrien zu erlangen. Zum ersten Mal steht hier nicht nur die reine Seitenansicht im Vordergrund, sondern vor allem die Symbiose aus Felgen, Front- und Heckbereich. Bei den Details ist es wichtig, die perspektivische Darstellung der vorangegangenen Skizzen deutlich zu verringern, um eine gleichmäßige Flächendarstellung zu gewinnen.
Diese Zeichnungen werden im Anschluss, beispielsweise mit der „Adobe Creative Suite“, mittels klarer, erfassbarer Linien dargestellt. Wichtig bei dieser Art von Renderings ist, dass in allen Darstellungen (Front-, Seiten-, Heck- und Topansicht) keinerlei perspektivische Verzerrung entsteht, um den Gesamteindruck der Außen-Geometrien und -maße nicht zu verfälschen. Das Rendering dient als Basis für das noch folgende Plastilin-Modell – siehe Bild – und die dreidimensionale digitale Umsetzung.
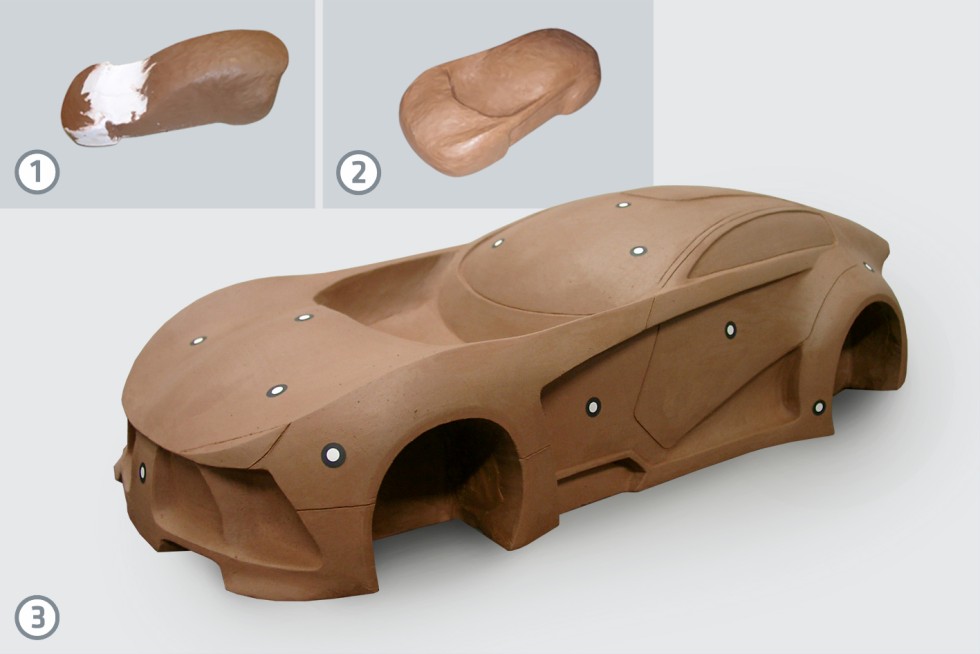
Tonmodellierungsprozess: Die Technik des Roboterfräsens kann auch hierbei dank der Bearbeitung in sechs bis acht Achsen einen großen Nutzen bieten.
Foto: invenio
Anhand dieser Adobe-Darstellung(en) wird eine Ergonomie-Studie oder auch Package-Untersuchung durchgeführt, die den Platzbedarf der Insassen über die menschliche Körpergeometrie ermittelt. So muss – auch bei den nicht funktionalen Showcars – garantiert sein, dass die Raumaufteilung und die Außenabmessungen eine angenehme Sitzposition, Beinfreiheit und das problemlose Bedienen der Pedalerie für alle Geschlechter gewährleistet.
In mehreren Iterationsschritten – und unter Beachtung von ergonomischen und gestalterischen Merkmalen – folgt die Auswahl des finalen Stylings der Karosserie – festgehalten mit zahlreichen perspektivisch korrekten Zeichnungen – die die Ausgangsbasis für das Plastilin-Modell darstellen.
Das Modellieren – Formfindung zwischen Roboterzellen und Handarbeit
Nach der zum Großteil manuellen Arbeit von der Konzepterstellung über Skizzen bis hin zu ausgereiften perspektivischen Zeichnungen, bekommen die Designer im Tonmodellierungs-Prozess einen ersten dreidimensionalen Eindruck nach bisher überwiegend zweidimensionalen Entwürfen. In Form eines physischen Gesamtmodells werden die Proportionen und die Linienführung des Personenkraftwagens erstmals klar ersichtlich. Anhand des Modells wird ein erster Eindruck des Gesamtfahrzeuges geschaffen, mit dessen Hilfe die Design-Ideen neu beurteilt und überarbeitet werden können.
Für das Clay-Modell wird zunächst ein Grundkörper aus Styrol auf Basis des Adobe-Tape-Renderings erstellt. Die verschiedenen Seitenansichten bilden die Konturen, die auf das Styrol gezeichnet und ausgeschnitten werden, sodass ein Grundkörper mit maßstabsgetreuer Länge, Breite und Höhe entsteht. Anschließend wird der Styrol-Korpus so in Form gebracht, dass er in seiner Form beinahe dem gewünschten Endmodell entspricht. Diese manuellen Arbeitsschritte der Grundkörper-Erstellung können mittels robotergestützter Automation sowie moderner CAD-/CAM-Systeme deutlich vereinfacht und zeitlich verkürzt werden. Hier kommt auch das Engineering- und Technologieunternehmen invenio mit ins Spiel.
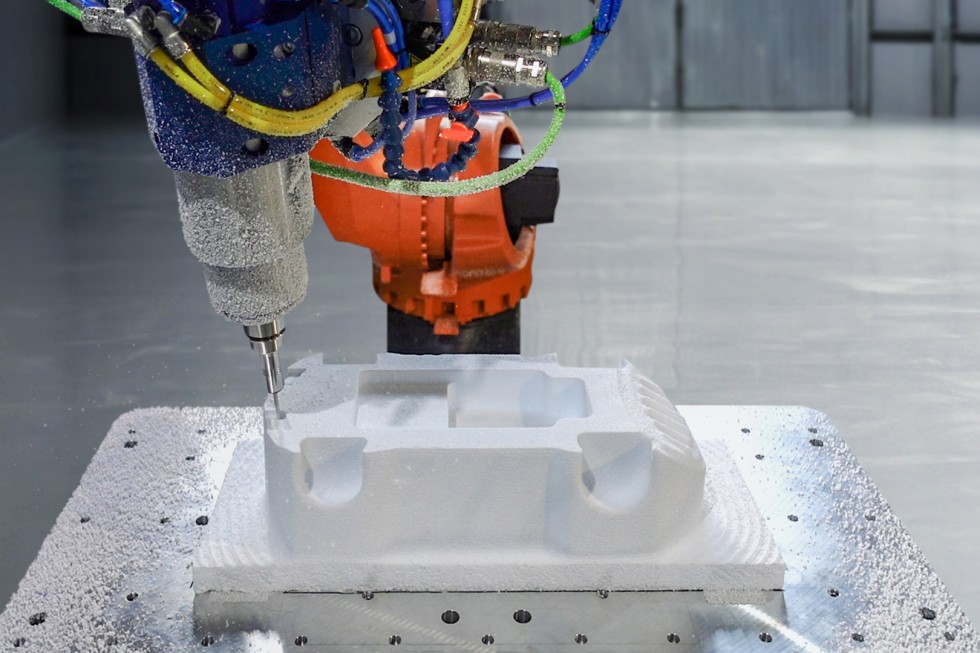
Das Roboterfräsen sorgt für hohe Detailtreue und verschafft den Designern einen dreidimensionalen Eindruck des Gesamtmodells.
Foto: invenio
Die Roboter fräsen mit hoher Detailtreue 3-D-Geometrien mit sehr anspruchsvollen Freiformflächen aus dem Blockmaterial. Dabei ermöglicht das feinporige Styrol eine ausgesprochen ansprechende Oberflächengüte – bei dem der Basiskörper des Show-Modells durch diese Frästechnik maßstabsgetreu deutlich schneller und kosteneffizienter angefertigt werden kann. Ein weiterer Vorteil ist die hohe Genauigkeit beim Fräsen: Ist der Grundkörper bereits detailliert ausgearbeitet, wird weniger Clay benötigt und dieser kann direkt – auf die mittels Roboterfräse ausgeführte Form des Styrols – aufgebracht werden.
Styrol-Körper oder Clay-Modelle – erstellt mit hochpräziser Roboter-Frästechnik
Nach Abschluss der Grundkörper-Erstellung folgt die Arbeit mit dem „Clay“ – einer schwefelhaltigen Modelliermasse auf Wachsbasis, die zu 100 Prozent recyclebar ist uns erst nach einer Erwärmung auf circa 60 °C aufgetragen werden kann. Nach dem Auskühlen bildet sie weder Haut noch Risse, somit sind eine saubere und detaillierte Darstellung der Karosserie-Oberfläche sowie die Bearbeitung durch eine Roboterlösung sehr gut möglich. Ohne den zunehmenden Einsatz von Robotik in der Industrie, dauert der Prozess der Clay-Bearbeitung deutlich länger, weil dann mittels Negativ-Schablonen, die die Silhouette der Karosserie aufzeigen, so viel von der Clay-Grundschicht wieder abgetragen werden muss, dass diese der gewünschten Form entspricht. Erst danach werden – ebenfalls in Handarbeit – Details und Konturen im Clay ausgearbeitet.
Moderne Automation vereinfacht und beschleunigt diesen Industrieprozess der spanenden Bearbeitung deutlich: Der maßstabsgetreue Plastilin-Körper wird mittels einer Roboterzelle bereits detailliert auf Basis der CAD-Daten vorgefräst. Bei der endgültigen Formgebung allerdings legt immer noch mal der Tonmodelleur Hand an, um letzte Feinheiten in der Kontur zu vollenden.
In beiden Entwicklungsschritten – ob beim Fräsen des Styrol-Körpers oder des anschließenden Clay-Modells – kann die Technik des Roboterfräsens einen hohen Nutzen bei gleichbleibender Qualität gewährleisten. Die präzise Bearbeitung der Modelle in sechs bis acht Achsen haben sowohl in Sachen Kosten- als auch Zeitersparnis großes Potenzial. Besonders weil die Roboterzelle die Möglichkeit bietet, ihre Arbeit nachts zu verrichten, sodass bei zeitkritischen Show-Modellen für Automobil-Messen, sozusagen bis buchstäblich zur letzten Minute am finalen Design gearbeitet werden kann.
Digitalisierung und Prototypenbau – Fertigstellen der Designstudie
Nach der Finalisierung der Form am Clay-Modell wird dieses berührungsfrei photogrammetrisch digitalisiert. Zudem wird eine Datenoptimierung und -konvertierung der Hauptkoordinatenrichtungen in das CAD-/CAM-/CAE-System durchgeführt. Dort wird das Modell konstruktiv, fertigungsgerecht und dreidimensional umgesetzt.
Die parametrisch-assoziative Flächenrückführung bestimmter (Teile)-Geometrien einer Karosserie im Flächenverbund mit anschließender Volumenbildung stellt die aufwendigste und größte Herausforderung heutiger Designer und Ingenieure dar. Hier sind – unter Berücksichtigung der vorgegebenen Toleranzen – die gewünschten Design-Geometrien für Kurven und Flächen auszuführen. So kann anhand eines digitalen Modells sukzessive der Fortschritt kontrolliert und auch gesteuert werden. Nach einem ausführlichen Vergleich aller CAD-Daten auf ihre Genauigkeit werden noch Details – wie Scheinwerfer, Scheiben sowie der Motor und die Lenkung inklusive Felgen – ausgearbeitet.
Auch Additive Fertigung wird bereits genutzt
Mittels des Verfahrens des „Selektiven Lasersintern“ (SLS) wird schließlich der Prototyp erstellt. Das Vorgehen ist eine Art des 3D-Drucks, das die schichtweise Herstellung komplexer Bauteile durch die selektive Verschmelzung von Kunststoffpartikeln auf der Basis von dreidimensionalen CAD-Daten erlaubt. Die Oberfläche des Modells wird nun genauestens digital erfasst – in Schichten mit Dicken von üblicherweise 0,15 bis 0,2 mm zerlegt. Anschließend wird der in Pulverform vorliegende Ausgangsstoff mittels Laserstrahl punktgenau verschmolzen und zu einem bruchfesten Modell aufgebaut. Der einfarbige Prototyp wird zur Fertigstellung grundiert und geschliffen, abgeklebt und für das Oberflächenfinish lackiert. Bei großen 1:1-Modellen wird häufig auch das Plastilin-Modell direkt lackiert oder mit einer lackähnlichen Folie überzogen.
Effiziente Designstudien – mit modernen industriellen Automatisierungslösungen
Nach dem aufwendigen Designprozess kann ein Show-Modell auf Automobil-Messen dem breiten Publikum vorgestellt werden. Je nach Geschmack und Bedürfnis der Zielgruppe gibt es unzählige gestalterische und stilistische Möglichkeiten – es geht stets darum neue Fahrzeugmodelle vorzustellen. Dafür sind kürzere Entwicklungszyklen – mit immer neuen Innovationen und ohne Qualitätsverlust – zwingend erforderlich.
Dank moderner Automatisierungslösungen gelingt es den Automobilherstellern, dem Wachstums- und Wettbewerbsdruck des Marktes standzuhalten: Das Ziel der Automation mittels Robotik-Lösungen ist es, Industrieprozesse effizienter zu gestalten. Genau diese Umstrukturierung verspricht kürzere Entwicklungszeiten, niedrigere Kosten und ist von hoher Qualität geprägt. Gerade kleinen und mittelständischen Betrieben bieten Industrieroboter daher ein hohes Automatisierungspotenzial durch Ihre flexible und besonders individuelle Einsetzbarkeit.
Das Roboterfräsen ist in der Automobil-Industrie aber nicht nur für Show-Modelle bestens geeignet, sondern auch Interieur- und Exterieur-Bauteile profitieren von dieser Frästechnik. Oftmals sind Öffnungen und Durchbrüche in den Teilen notwendig, die mit anderen Verfahren entweder nicht gefertigt werden können – oder bei denen sich ein Spritzgusswerkzeug aufgrund der Stückzahl nicht lohnt, wie es bei Sonderserien oder Sportmodellen häufig der Fall ist.
Angefangen beim Designprozess neuer Fahrzeuge, überzeugen moderne Fräsroboter mit Individualisierungsmöglichkeiten ganz nach Kunden-Anforderungen – ob auf einer Ebene oder in allen Positionen und Konturen. Denn die manuelle Bearbeitung bleibt bis zur Formvollendung des Produktes unverzichtbar. Der Einsatz eines Roboters belegt eben genau diese These und ist in diesem Industrieprozess eine wertvolle Unterstützung. Das Potenzial von Designstudien in der Automobilindustrie kann nur mit ‚Mensch und Maschine‘ gemeinsam – Hand in Hand – voll ausgeschöpft werden. Das Engineering- und Technologieunternehmen invenio aus Rüsselsheim am Main (www.invenio.net) ist in diesem Fall der Partner für wirtschaftliche und individuelle Robotik-Lösungen mit hochpräziser Frästechnik.
Das könnte Sie auch interessieren:
So optimieren Betriebe Produktentwicklung und Fertigung mit virtueller Simulation
Neue Prozesskette sorgt für Tempo: Großbauteile per 3D-Druck