Tipps für eine sichere Mensch-Roboter-Kollaboration
Nach einer Prognose des IFR werden von 2020 bis 2022 weltweit rund 2 Millionen neue Industrie-Roboter in Fabriken installiert. Sie ebnen dabei den Weg für mehr Flexibilität in der Produktion. Doch wie sieht in der Fabrik der Zukunft die Zusammenarbeit zwischen Mensch und Roboter aus und welche Richtlinien sind zu beachten?
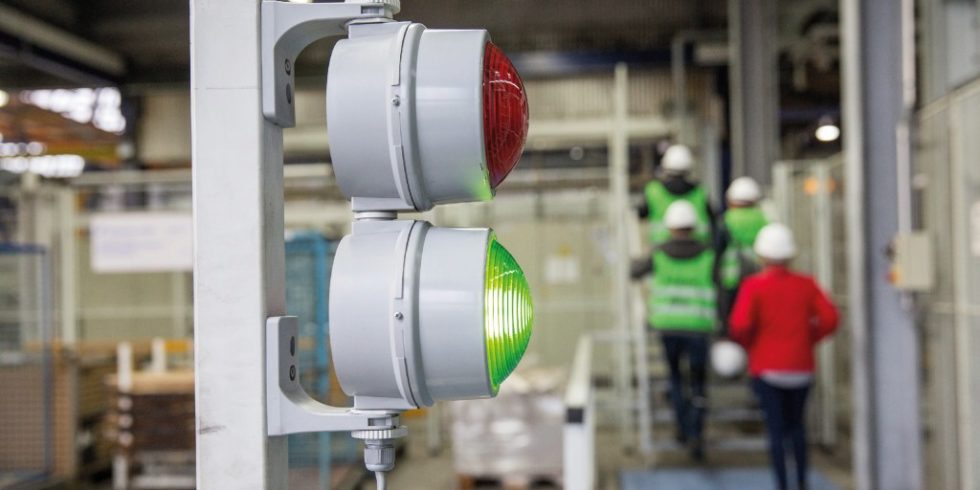
Bei der Zusammenarbeit von Mensch und Roboter ist es wichtig, Sicherheitsanforderungen einzuhalten und die Bestimmungen der Maschinenrichtlinie zu beachen.
Foto: Ce-CON / Tristan / Vankann / Fotoetage
„Ein Roboter ist eine technische Apparatur, die üblicherweise dazu dient, dem Menschen häufig wiederkehrende mechanische Arbeit abzunehmen. Roboter können sowohl ortsfeste als auch mobile Maschinen sein und werden von Computerprogrammen gesteuert“, so lautet aktuell, beispielsweise auf Wikipedia, die Definition – noch. Denn künftige Roboter können auch autonom und selbstlernend sein. Und sie interagieren bereits mit dem Menschen. Umso wichtiger ist es, darauf zu achten, dass vom Roboter keine Gefahr für den Bediener ausgeht.
Roboter-Trends laut IFR-Top-Thema
Die International Federation of Robotics (IFR) hat in ihrer jüngsten Umfrage drei Technologietrends identifiziert, die den Robotereinsatz weiter „befeuern“ werden. Die erste lautet: Roboter werden immer „smarter“ – denn die Programmierung und Installation wird immer einfacher. Digitale Sensoren in Verbindung mit intelligenter Software machen das direkte Anlernen möglich – etwa in Form von „Programmierung durch Demonstration“. Dabei wird die Aufgabe, die der Roboterarm ausführen soll, zuerst vom Menschen ausgeführt und die Daten werden anschließend von der Software in das digitale Programm des Roboterarms umgewandelt. In Zukunft können automatische Lernprogramme das Anlernen weiter optimieren.
Roboter arbeiten mit Menschen zusammen
Die mögliche Zusammenarbeit von Mensch und Roboter ist der zweite wichtige Trend. Moderne Robotersysteme können sich dadurch an schnell veränderliche Umgebungen anpassen. Die nutzbaren kollaborativen Anwendungen werden ständig ausgebaut. Häufig befinden sich Mensch und Maschine in einem gemeinsamen Arbeitsraum und erledigen Aufgaben schrittweise nacheinander. Es kommt aber auch vor, dass Mensch und Roboter gleichzeitig am selben Teil arbeiten und sogar in Echtzeit interagieren. Roboter sollen dazu die menschliche Stimme oder Gestik zu erkennen. Die Mensch-Roboter-Kooperation (MRK) bietet zahlreiche Chancen für Unternehmen aller Größenordnungen und Branchen. Auch kleine und mittlere Unternehmen (KMU) werden inzwischen angesprochen.
Industrie-Roboter stellen außerdem zentrale Komponenten der digitalen und vernetzten Produktion dar und unterstützen Ansätze von Industrie 4.0. Industrie-Roboter müssen folglich miteinander kommunizieren können – und das unabhängig vom Hersteller. Hierfür wurde eine standardisierte Schnittstelle entwickelt, die eine Anbindung von Industrie-Robotern an das Industrial Internet of Things (IIoT) erlaubt. Dies rückt insbesondere für KMU neue Geschäftsmodelle in den Fokus, die zuvor aus wirtschaftlichen Gründen außer Reichweite waren. Dank der Möglichkeit, Roboter zu leasen, bieten sich für KMU Vorteile wie der Entfall einer Kapitalbindung, fixe laufende Kosten, automatische Upgrades, zudem ist kein qualifiziertes Personal vonnöten.
Sind Roboter wie Maschinen zu betrachten?
Die geschilderten Technologietrends erleichtern den zunehmenden Einsatz von Robotern, werfen aber für die (neuen) Anwender auch aktuelle Fragen auf. Sind Roboter auch nur Maschinen? Müssen die Anforderungen an die Maschinenrichtlinie erfüllt werden? Welche Schutzmaßnahmen sind bei der Zusammenarbeit von Mensch und Roboter wirklich notwendig?
Einige Beispiele aus dem Alltag machen deutlich, worauf beim Einsatz von Robotern zu achten ist. Lautet der Verwendungszweck beispielsweise, dass der Roboter für Ausbildungszwecke der Instandhaltung montiert, erprobt und wieder demontiert werden soll, so fällt dieser in den Anwendungsbereich der Maschinenrichtlinie (MRL). Die MRL 2006/42/EG setzt voraus, dass eine „Maschine“ für eine bestimmte Anwendung zusammengefügt wurde – in diesem Fall für die praxisgerechte Erprobung. Der Roboter ist in diesem Zustand für eine diese Anwendung voll funktionsfähig; somit wird die bestimmungsgemäße Verwendung für ihn erfüllt.
Wann greift die Maschinenrichtlinie und wann nicht?
Häufig werden Industrie-Roboter in andere Maschinen eingebaut oder mit anderen (auch unvollständigen) Maschinen zusammengefügt. Beispiele sind Schneid-, Schweiß- oder Lackierroboter, die in Fertigungsprozessen der Automobil- oder der Metallindustrie häufig anzutreffen sind. Sie stellen im Sinne der MRL eine „unvollständige Maschine“ dar. Erst durch das notwendige Werkzeug, zum Beispiel durch das Anbringen eines Greifers, erhält der Roboter einen bestimmten Zweck und müsste dann als vollständige Maschine betrachtet werden.
Der Hersteller ist verpflichtet, die speziellen technischen Unterlagen entsprechend Anhang VII der Maschinenrichtlinie zu erstellen, darüber hinaus eine Montageanleitung und eine Einbauerklärung. Diese Dokumente sind der unvollständigen Maschine bis zu ihrem Einbau in die vollständige Maschine beigefügt und anschließend Teil der technischen Unterlagen des Gesamtkonstrukts.
Sicherheitsvorkehrungen für eine Gesamtheit von Maschinen
Im Zuge der Digitalisierung werden immer öfter mehrere Maschinen zusammen betrieben, sodass sie am Ende als Gesamtheit funktionieren. Ein Blick auf die Schnittstellen zwischen den am Prozess beteiligten Maschinen gibt einen genaueren Einblick auf das Thema „Gesamtheit“. Drei Punkte müssen dabei zutreffen:
- Die Maschinen führen eine gemeinsame Aufgabe aus.
- Sie sind funktional so miteinander verbunden, dass sie sich im Betrieb gegenseitig beeinflussen.
- Sie verfügen über eine gemeinsame Steuerung.
Ein gemeinsamer Not-Halt-Kreis bedeutet jedoch nicht, dass hier ein steuerungstechnischer Zusammenhang besteht.
Bei der Automation von zerspanenden Bearbeitungsprozessen werden beispielsweise Roboter eingesetzt, um Bauteile von einer zur anderen Werkzeugmaschine zu transportieren. Sie können auch Bearbeitungsschritte wie das Bohren oder Entgraten übernehmen, zeitgleich zur Zerspanung in der Maschine. Oft handelt es sich dabei gemäß der Maschinenrichtlinie um eine Gesamtheit, da mehrere Werkzeugmaschinen und Roboter steuerungs- und sicherheitstechnisch miteinander verknüpft sind und als Gesamtheit zusammenarbeiten. Betritt ein Mitarbeiter die Roboterzelle bei offener Schutztür, um Arbeiten durchzuführen, müssen die Werkzeugmaschinen sicherheitsgerichtet still gesetzt werden.
Die sichere Interaktion ist grundlegende Voraussetzung
Häufig werden Industrieroboter ohne Applikation sowie ohne Absicherung geliefert – denn diese Roboter sind dazu bestimmt, in andere Maschinen eingebaut oder mit anderen zusammengefügt zu werden. Jedoch müssen dann zusätzlich zu den Gefahren, die vom Roboter ausgehen, die Bewegungen des Menschen und die auszuführenden Prozesse berücksichtigt werden.
In Schweißzellen bei Automobilzulieferern arbeiten Mensch und Roboter in vielen Fällen eng zusammen. Zum Beispiel werden dort Karosserieteile zusammengefügt, die später zu neuen Fahrzeugen oder als Ersatzteile weiterverarbeitet werden. Dazu legt ein Arbeiter Einzelteile in eine Vorrichtung, die dann gespannt und anschließend von einem Roboter geschweißt, geklebt oder genietet werden. Dabei entstehen für den Menschen sowohl durch den Roboter als auch durch den Bearbeitungsprozess Gefährdungen. Diese sind in einer Risikobeurteilung zu analysieren und einzuschätzen. Aufgrund der Risikobeurteilung können technische, organisatorische und personenbezogene Maßnahmen notwendig werden, um die Maschine sicher zu machen.
Arten von Schutzeinrichtungen
Bisher ist es üblich, den Roboter an mindestens drei Seiten von einer feststehenden trennenden Schutzeinrichtung (zum Beispiel einem Schutzzaun) zu umgeben. Die vierte Seite ist häufig für einen Bediener zugänglich. Um den Arbeiter vor Bewegungen des Roboters zu schützen, wird sie abgesichert – zum Beispiel über ein Rolltor oder eine Tür. „Eleganter“ sind nicht trennende, berührungslos wirkende Schutzeinrichtungen wie Scanner oder Lichtvorhänge.
Bild 3. Berührungslos arbeitende Schutzeinrichtung: Die Annäherung eines Menschen an den Roboter wird frühzeitig erkannt. Foto: Ce-CON / Tristan / Vankann / Fotoetage
Soll ein Robotersystem ohne trennende Schutzeinrichtung direkt mit dem Menschen interagieren („kollaborierender Roboter“), ist darauf zu achten, dass weder der Roboter noch die angebauten Komponenten oder der Prozess Gefährdungen für den Mitarbeiter verursachen. Technologien wie Radarüberwachung oder Kamerasysteme sollten die Annäherung eines Menschen frühzeitig erkennen, die Geschwindigkeit oder die Kraft des Roboters anpassen oder ihn bei Bedarf stillstehen lassen.
Für einzelne Aufgaben wie das Greifen und Transportieren von Teilen kommt die MRK schon infrage. Allerdings muss auch hier darauf geachtet werden, dass der Anbau eines Greifers an den kollaborierenden Roboter diesen zu einer vollständigen Maschine macht und eine CE-Kennzeichnung erfordert. Für die Integration von kollaborierenden Systemen sind die Sicherheitsanforderungen gemäß der Norm DIN EN ISO 10218–2 zu erfüllten.
Mit der zunehmenden Verbreitung der Industrie-Roboter und der Aufgaben, die diese übernehmen können, wird das Thema Normung und Sicherheitstechnik auch in KMU künftig zum Alltag gehören.
https://ifr.org/
www.ce-con.de