Wie gelingt die Transformation einer Werkstattmontage in laufender Serie?
Der Markt der Elektromobilität ist in starkem Wachstum begriffen. Dies machte es erforderlich, dass ein Mittelständler sein Produktionssystem im Segment Wallboxen in kurzer Zeit komplett umstellen musste – gezeigt wird, wie das gelang.
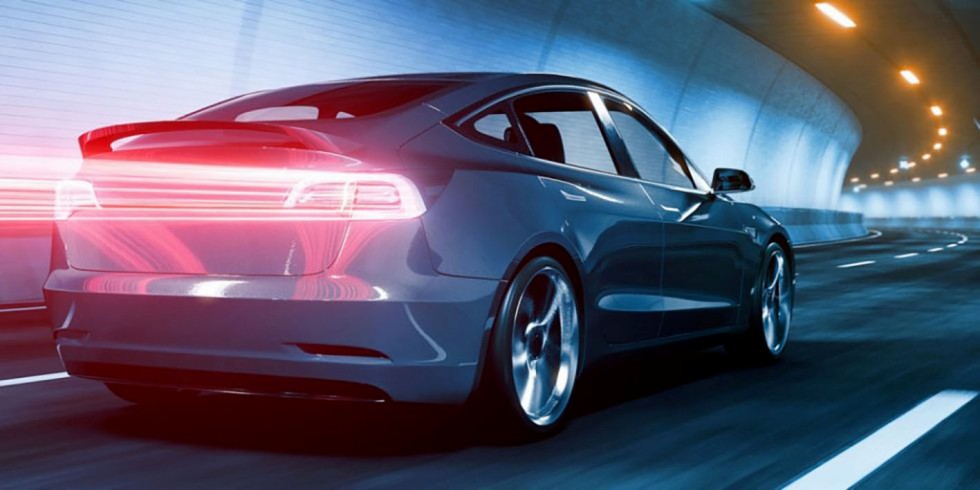
Die Elektromobilität ist ein Wachstumsmarkt: Erfolgreiche Zulieferer dürfen sich auf steigende Nachfrage einstellen und sollten ihre Produktionen frühzeitig entsprechend anpassen. Grafik: Continental
Durch die Produktionsumstellung bleibt nun die Wettbewerbsfähigkeit erhalten, die gestiegene Nachfrage kann bedient werden und das Unternehmen ist für die Zukunft gut aufgestellt. Was im Automotive-Bereich teilweise bereits Usus ist, wird im starken Mittelstand mindestens so wichtig und wird hier an einem Beispiel erklärt.
Mit smarten Ladelösungen die Energiewende unterstützen
ABL gehört zu den Pionieren der Elektromobilität. Das unabhängige Familienunternehmen aus Franken produziert unter anderem Wallboxen und Ladesäulen für den privaten, halböffentlichen und öffentlichen Einsatz. Mit seinen smarten Ladelösungen entwickelt sich ABL zu einem richtungsweisenden Player bei der Energiewende [1]. Im Segment Wallboxen setzt das Unternehmen aktuell auf drei Produktlinien, die sich im Funktionsumfang sowie im Design unterscheiden und alle in der Unternehmenszentrale in Lauf a.d. Pegnitz produziert werden: „Wallbox eMH1“, „Wallbox eMH2“ und „Wallbox eMH3“.

Wallboxen: Das Familienunternehmen aus Franken entwickelt sich mit seinen smarten Ladelösungen zu einem richtungsweisenden Player bei der Energiewende.
Foto: ABL
Der hier beschriebene Wandel der Produktionslinien der Bestandsprodukte – bis hin zur Linie des Neuproduktes „Wallbox eM4“ – ist ein wichtiger Baustein in der Modernisierung und Transformation der gesamten ABL Produktion. Dabei wird ein zweistufiges Veränderungskonzept umgesetzt, das den Weg von der früheren Produktionslinie hin zu einer taktgebundenen Linie für die Wallbox eMH2 beschreibt und in einer modernen, Werkerführungssystem-basierten Linie für das Neuprodukt Wallbox eM4 mündet. Motivation für diesen Wandel sind zum einen die Erhaltung von attraktiven Herstellkosten am Standort Deutschland und zum anderen das erforderliche Wachstum im Bereich intelligenter Ladelösungen.
Von der Einzelplatz- über die Taktmontage hin zu einer modernen Montagelinie
Die bisherige Montage ist nach dem Prinzip der Einzelplatzmontage strukturiert – das heißt, dass die Wallboxen von Mitarbeitenden nahezu vollständig montiert werden. Die steigende Marktnachfrage, aber auch die Zunahme der Komplexität in der Montage gaben den Anstoß, das Montagesystem auf eine Taktmontage mit erhöhter Transparenz und Sichtbarkeit der Prozesse umzustellen. Das bedeutet, dass der Montageprozess auf mehrere Arbeitsstationen mit geringerem Arbeitsinhalt aufgeteilt wird. Einzelne Mitarbeitende sind nun für einen definierten Arbeitsinhalt zuständig und nicht mehr für die vollständige Montage eines Produktes. Im gleichen Zuge ist die Materialbereitstellung für die Taktmontage dahingehend optimiert worden, dass die benötigten Materialien den jeweiligen Arbeitsplätzen eindeutig zugeordnet sind.

Taktzeitdiagramm: Der Montageprozess wird auf mehrere Arbeitsstationen mit geringerem Arbeitsinhalt aufgeteilt. Grafik: ABL
Darüber hinaus ist der verbesserte Herstellprozess zum ersten Mal im Unternehmen nach dem Kundentakt ausgerichtet. Die zeitliche Ausrichtung der Arbeitsschritte richtet sich nach der Kundennachfrage und erfolgt in einem fest definierten Takt [2].
Deutliche Vorteile im Produktionsprozess generiert
Das Material fließt von Arbeitsstation zu Arbeitsstation und wird dabei kontinuierlich zu einem fertigen Produkt weiterverarbeitet. Stillstände und Materialbestände innerhalb des Arbeitsprozesses werden somit reduziert beziehungsweise komplett vermieden. Auch Montagefehler werden durch die umgestellten Produktionsprozesse deutlich verringert und sorgen für einen harmonischen Produktionsfluss. Zusätzlich hat sich die Transparenz hinsichtlich etwaiger Störungen verbessert. Störfaktoren werden durch das neue Produktionssystem sichtbar und können mit entsprechenden Maßnahmen zielgerichtet beseitigt werden. Insgesamt konnte die Durchlaufzeit je nach Variante um bis zu 80 Prozent verringert werden.
Herausforderungen im Betrieb
Die Organisation der Arbeitsvorgänge anhand einer Taktmontage war ein Novum bei ABL, weshalb ein ausgerichtetes Veränderungsmanagement erforderlich war, um beteiligte Führungskräfte und Werker sowie den Betriebsrat einzubinden. Die Mitarbeitenden der Montage und ihre Führungskräfte wurden im Vorfeld intensiv in der neuen Arbeitsweise geschult. Darüber hinaus ist von der Logistik und den Schnittstellenpartnern ein neues intra-logistisches Versorgungskonzept erarbeitet und erfolgreich eingeführt worden. Zum einen geschah dies, um Bedenken gegenüber dieser Veränderung zu begegnen und zum anderen, um mit Hinblick auf den Wandel der Produktion die Mitarbeitenden frühzeitig zu sensibilisieren. Die erfolgreiche Einführung der Taktmontage und die daraus gewonnenen Erfahrungen sind ein wichtiger Zwischenschritt bei der Transformation der ABL-Produktion.
Neue Generation einer Montagelinie
Die gewonnenen Erkenntnisse der getakteten Wallbox-Montage sowie die speziellen Produktanforderungen, welche sich hinsichtlich Varianten, Prüfprozessen, Variabilität und Herstellkosten kontinuierlich weiterentwickeln, legen den Grundstein für die Konzeption der neuen Montagelinie für die Wallbox eM4. Drei Faktoren erhalten hierbei besondere Beachtung.
Zum ersten entsprechen die entstandenen Arbeitsplätze einem höchsten Maß an Ergonomie. Als Steh-Sitz-Arbeitsplatz ausgelegt, sind Greifwege zu Montagematerial, Werkzeugen oder Vorrichtungen optimiert. Das erleichtert die einzelnen Montageschritte. Ein zu 100 Prozent integriertes Werkerführungssystem leitet Schritt für Schritt durch die Montageumfänge und unterstützt sprachunabhängig durch kurze Videosequenzen sowie einem Pick-by-light-System. Schraubprozesse werden teils automatisiert ausgeführt sowie durch positionsüberwachte Linearführungen, welche bei Bedarf mit Zuführsystemen ausgestattet sind, anlagenseitig unterstützt. Dabei werden Drehwinkel und Drehmoment des Schraubfalls überwacht und dokumentiert. Um eine manuelle Handhabung der Wallbox zu vermeiden, kommt ein Werkstückträger zum Einsatz, der bei Bedarf geschwenkt werden kann. So kann die Montageposition immer ideal erreicht werden.
Zum zweiten wird zusammen mit der IT die Digitalisierung in der Produktion deutlich ausgebaut, was auch die Möglichkeiten zur Automatisierung der Montageprozesse erhöht. Führend aus dem ERP (Enterprise-Resource-Planning)-System werden Auftragsdaten über eine IoT (Internet of Things)-Plattform direkt mit der Montagelinie bidirektional ausgetauscht.

Auftragsdaten werden über eine IoT-Plattform direkt mit der Montagelinie ausgetauscht – und das bidirektional. Grafik: ABL
Im Vorfeld werden (ebenfalls systemunterstützt) Auftragsreihenfolgen generiert, die definierten und standardisierten Produktionsmustern folgen. Im Montageprozess selbst werden die intelligenten Werkstückträger individuell über automatisierte Fördertechnik an einzelnen Montagestationen, AOI (automated optical inspection)-Testzellen, Roboter-Handlingsystemen, Funktions- oder Leistungsprüfständen zugewiesen und relevante Daten ausgetauscht. Eine Erfassung von produkt-, anlagen- und produktionsspezifischer Daten wird so nahezu in Echtzeit möglich.
Flexibel bleiben, Herstellkosten dauerhaft senken
Und zum dritten liegt der Fokus auf der Zukunftsfähigkeit der Montagelinie. Daher werden alle Investitionen dahingehend überprüft. Auch bei einem hohen Automatisierungsgrad des Gesamtsystems werden Einzelanlagen immer maximal flexibel ausgelegt. Beispielsweise ermöglicht der adaptierbare Werkstückträger bereits jetzt, Wallboxen verschiedener Serien auf einer Linie zu montieren. Dies schafft die nötige Basis, um weiterhin attraktive Herstellkosten am Standort Deutschland erreichen zu können.
Literatur
- Internet: https://www.abl.de/de/unternehmen. Zugriff am 07.12.22.
- Erlach, K.: Wertstromdesign – Der Weg zur schlanken Fabrik. 3. Aufl. (2020), S.48, Springer Vieweg.
Das könnte Sie auch interessieren:
Wie sogar Nachzügler die digitale Transformation bewältigen
Nachhaltigkeit wird zur Pflicht: Ökobilanzierung für Automotive- und Industriebetriebe

Dr.-Ing. Manuel Norbert Loos, Maschinenbauingenieur, ist Chief Operations Officer und Prokurist bei der ABL GmbH in Lauf a.d. Pegnitz. Foto: ABL
Bernhard Helfer, Maschinenbautechniker, ist Director Manufacturing Engineering and Production Services bei ABL.
Dipl.-Wirtsch.-Ing. (FH) Sebastian Raschkowski ist Teamleiter IE Prozessplanung bei ABL.
Dominik Thönes, M. Sc., ist Project Manager Production Systems bei ABL.