Zusammenarbeit von Mensch und Roboter
Aktuell werden viele Szenarien diskutiert, wie die Arbeit in den Fabriken der Zukunft aussehen kann. Die Visionen reichen bis hin zu Aufträgen, die sich selbständig den Weg durch Fabriken suchen und in denen Menschen und Roboter Hand-in-Hand an gleichen Produkten arbeiten. Diese Szenarien werden in der Industrie mit großem Interesse verfolgt, weil sie Chancen zur Steigerung der globalen Wettbewerbsfähigkeit bieten.
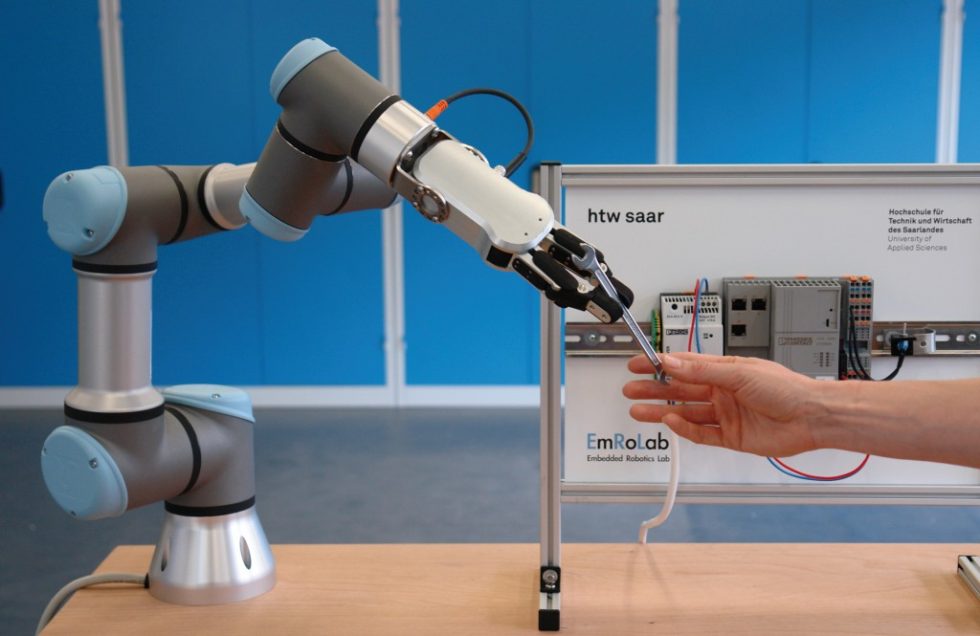
Bild 1. Bei der „Kollaboration“ arbeiten Mensch und Roboter direkt zusammen – in der Industrie wird dies bisher noch selten umgesetzt.
Foto: htw saar
Ein viel diskutiertes Anwendungsfeld ist dabei die Zusammenarbeit zwischen Mensch und Roboter. Der Aufsatz geht auf die kritischen Fragen ein, wie viel echte Mensch-Roboter-Kollaboration heute bereits existiert und was echter Kollaboration noch im Wege steht.
In der smarten Fabrik der Zukunft wird neben der Digitalisierung und der damit verbundenen Automatisierung von Informationsflüssen auch die weitere Optimierung und Automatisierung von Produktions- und Logistikabläufen bedeutsam sein. Gerade in letztgenannten Bereich werden aktuell große Erwartungen an die Robotik gerichtet.
Ausgangssituation
Industrieroboter haben sich in den letzten Jahrzehnten insbesondere im Einsatzbereich der 4D (dull, delicate, dirty, dangereous), also bei langweiligen beziehungsweise monotonen, filigranen, schmutzigen oder gefährlichen beziehungsweise wenig ergonomischen Tätigkeiten bewährt [1]. Durch die Entwicklung von Leichtbaurobotern mit entsprechenden Steuerungen und Sensoriken sind Kollaborationen von Menschen und Robotern auf engstem Raum möglich geworden.
Diese Einsatzszenarien werden von vielen Firmen mit großem Interesse beobachtet, weil sie letztendlich einige Vorteile – zum Beispiel neue Möglichkeiten im Bereich der Produktionsoptimierung, kurze Amortisationszeiten, Flexibilitätssteigerungen oder Flächeneinsparungen – versprechen. In Gesprächen mit Firmenvertretern ist jedoch immer wieder festzustellen, dass neben dem großen Interesse auch häufig eine große Unsicherheit hinsichtlich der realen Umsetzbarkeit solcher Szenarien ausgedrückt wird. Mehr als 20 Jahre nach der Präsentation der ersten Leichtbauroboter und mehr als ein halbes Jahrzehnt nach den ersten Applikationsbeispielen zu Mensch-Roboter-Kollaborationen (MRK) [2] ist dies sicherlich verwunderlich.
Dies ist Grund genug, auf Basis publizierter Applikationsbeispiele zu untersuchen, wie der Umsetzungsstand der MRK in deutschen Betrieben tatsächlich ist. Dazu wird zunächst der Begriff MRK genauer geklärt. Anschließend werden auf Basis der Erkenntnisse von publizierten Anwendungsbeispielen Ursachen für die beschriebene Zurückhaltung gesucht.
Begriffsklärung
Eine für die Abgrenzung regelbetrieblicher Anwendungsfälle der Interaktion von Menschen und Robotern gut geeignete Kategorisierung beschreiben Onnasch et al. in [3], Bild 1:
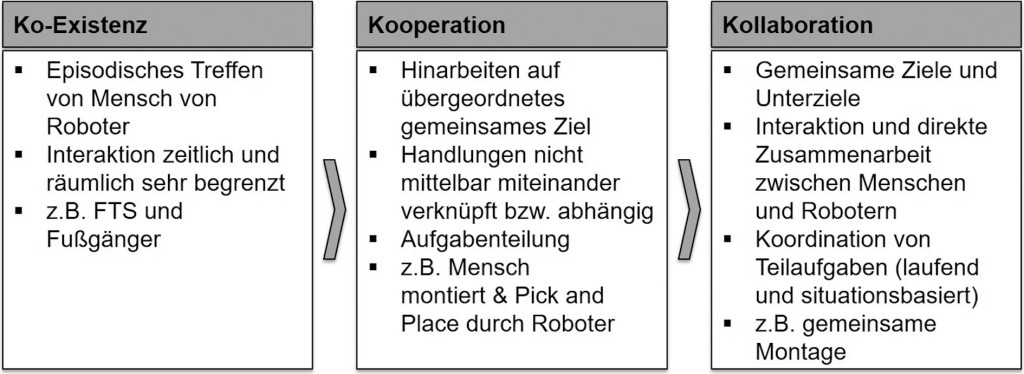
Bild 1. Interaktionskategorien zwischen Mensch und Roboter (angelehnt an [3]).
Foto: htw saar
- Ko-Existenz,
- Kooperation,
- Kollaboration.
Der Zustand der Ko-Existenz liegt vor, wenn Mensch und Roboter nur sporadisch in einem begrenzten Raum für eine begrenzte Dauer interagieren müssen, wie dies beispielsweise beim Aufeinandertreffen zwischen einem fahrerlosen Transportsystem und einem Fußgänger der Fall ist. Eine Kooperation zwischen Mensch und Roboter setzt voraus, dass Mensch und Roboter ein gemeinsames Arbeitsziel verfolgen. Es liegt dabei eine klare Aufgabenteilung zwischen Mensch und Roboter vor und die Handlungen sind nicht direkt miteinander verknüpft beziehungsweise voneinander abhängig. Ein Beispiel hierfür wäre, dass ein Mensch Montagetätigkeiten durchführt, das Objekt definiert ablegt und der Roboter das montierte Objekt später in einem Handhabungsprozess weiterreicht. [3]
Im Falle einer Kollaboration verfolgen Mensch und Roboter gemeinsame Ziele beziehungsweise sogar Unterziele. Um diese zu erreichen, arbeiten Mensch und Roboter direkt zusammen, was bedeutet, dass sie ständig sowie in Abhängigkeit der jeweiligen Arbeitssituation ihre Teilaufgaben koordinieren müssen. Dies ist beispielsweise bei der gemeinsamen Montage eines Produkts der Fall. Die Kollaboration stellt somit die komplexeste Form der Interaktion zwischen Mensch und Roboter dar. [3]
Feststellungen aus Anwendungsfällen
Um ein Gefühl dafür zu entwickeln, wie kollaborativ die Applikationen kollaborationsfähiger Roboter in den Fabriken Deutschlands zurzeit sind, erscheint die genauere Analyse von Anwenderberichten in industrienahen Fachzeitschriften (inklusive deren Onlineportalen) sowie von dokumentierten Anwendungsbeispielen der Nutzer, der Hersteller beziehungsweise Systemlieferanten kollaborationsfähiger Robotik als geeignet. Im Bereich Fachzeitschriften wurde der Zeitraum 2009 bis Februar 2017 als relevant betrachtet. In der Analyse nicht berücksichtigt wurden Messe(vor)berichte mit idealisierten Anwendungsszenarien und Forschungsprojekte ohne eindeutige beziehungsweise mit idealisierten praktischen Anwendungsszenarien.
Grundsätzlich lässt sich festhalten, dass es nur eine geringe Anzahl publizierter unterschiedlicher Anwendungsfälle gibt, deren überwiegender Anteil in Zusammenarbeit mit den Herstellern oder Systemlieferanten publiziert wurde. Darin werden in der Regel erstmalige, abgegrenzte sowie erfolgreiche Einführungsprojekte beschrieben. Unabhängige Berichte finden sich vergleichsweise selten. Berichte mit dem Charakter einer mehrjährigen Anwendererfahrung wurden nicht identifiziert.
Diese Feststellungen sind aus mehreren Gründen nicht verwunderlich: Einerseits sollen Fachzeitschriften auf neue Technologien und erste Anwendungsfälle aufmerksam machen. Somit sind Berichterstattungen in Kooperation von Hersteller und Anwender zu erwarten. Anderseits entspricht es der hiesigen Kultur, mit Innovationen in den eigenen Herstellprozessen nicht unmittelbar an die Öffentlichkeit zu gehen. Letzteres lässt die Möglichkeit offen, dass es eine Reihe weiterer Anwendungsbeispiele gibt, die öffentlich nicht bekannt sind – aus wissenschaftlicher Sicht sehr bedauerlich.
Interessanter ist aber die Feststellung, dass der überwiegende Anteil der Anwendungsfälle entsprechend der Taxonomie von Onnasch als kooperierend zu bezeichnen ist. Hierzu gehören insbesondere Anwendungsfälle, die die Eigenschaft ausnutzen, dass kollaborationsfähige Roboter sich flexibel einsetzen sowie platzsparend und ohne Schutzzaun betreiben lassen – zum Beispiel der Einsatz klassischer Handlingroboter oder achsenbasierter Pick-and-Place-Systeme zur Bestückung von Maschinen. Nur in Ausnahmefällen können die Anwendungsfälle als kollaborierend eingestuft werden. Als positives Beispiel sei diesbezüglich die Montage der Stoßdämpfer des „Ford Fiesta“ im Werk Köln erwähnt: Hier teilen sich Mensch und Roboter die Arbeitsinhalte hinsichtlich ihrer Stärken auf [4].
Erklärungsversuch
Worin begründet sich die einerseits subjektiv wahrnehmbare und andererseits in den Erfahrungsberichten belegte Zurückhaltung bezüglich der breiten Umsetzung von Mensch-Roboter-Kollaborationen? Aus der Analyse der publizierten Anwendungsbeispiele ergeben sich zwei mögliche Erklärungsansätze.
Der erste Erklärungsansatz bezieht sich auf die als geeignet erscheinenden Einsatzszenarien selbst: Das geeignete Einsatzfeld für eine vollständige MRK erscheint, wie in Bild 2 dargestellt, vergleichsweise begrenzt.
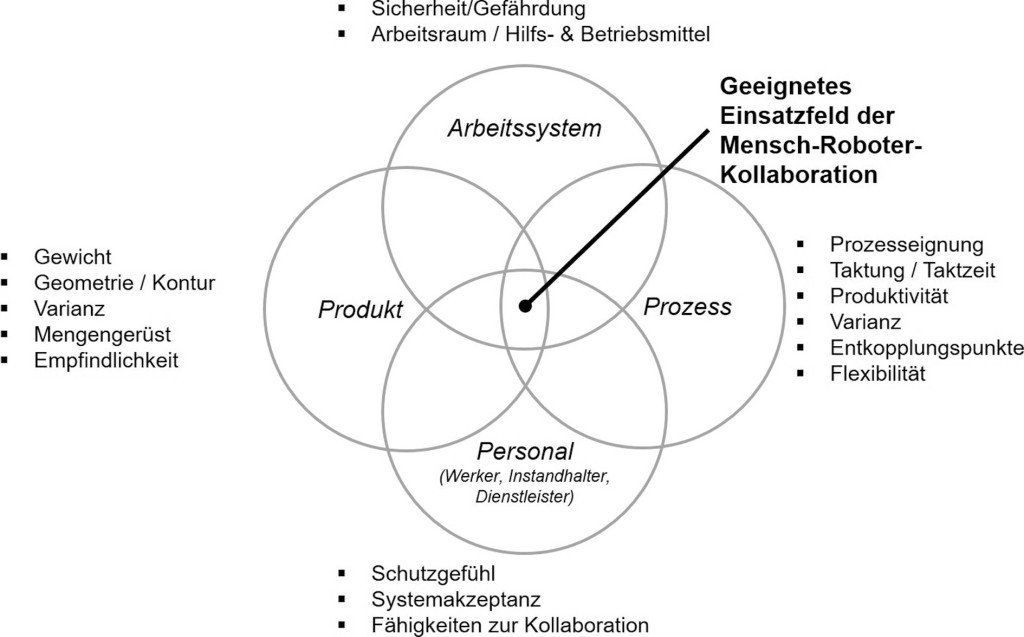
Bild 2. Die Schnittmenge des geeigneten Einsatzes der Mensch-Roboter-Kollaboration ist gering.
Foto: htw saar
Als Grundvoraussetzung muss zunächst einmal der Arbeitsprozess selbst – zumindest teilweise – zur Roboterautomation geeignet sein. Zweitens muss das herzustellende Produkt einen kollaborativen Einsatz zulassen. In dieser Kategorie schränkt einerseits das Teilegewicht die Auswahl der möglichen Roboter ein, andererseits ist durch das ungeschützte Handling von Teilen auch deren konstruktive Gestaltung nicht unerheblich (vergleiche spitze oder scharfkantige Konturen).
Als dritter Aspekt kommt das gesamte Arbeitssystem hinzu, welches letztendlich hinsichtlich seines Risikos bewertet und freigegeben werden muss. Zwar verfügen kollaborationsfähige Roboter bereits über eine Reihe von Sicherheitsfunktionen (zum Beispiel Geschwindigkeitsbegrenzung oder Einklemmschutz), jedoch müssen diese in der Gesamtheit mit Produkt, Greifern und sonstigen Betriebs- und Hilfsmitteln bewertet werden (Übersicht in [5]). Als positive Entwicklung zu werten ist, dass im Februar 2016 mit der ISO/TS 15066 ein erster Standard publiziert wurde, der Hilfestellung in diesem Kontext gibt. Allerdings ist dieser Standard aktuell nur in englischer Sprache verfügbar.
Den vierten relevanten Faktor bezüglich des Einsatzes von Mensch-Roboter-Kollaborationen bildet der Mensch selbst. Das kollaborierende (Werker) und das interagierende Personal (zum Beispiel Instandhalter und sonstige Dienstleister) müssen sich zunächst einmal ausreichend geschützt fühlen, um dann in einem zweiten Schritt die Zusammenarbeit mit einem Roboter im selben Arbeitssystem akzeptieren zu können. In einem dritten Schritt benötigen diese Mitarbeitergruppen gegebenenfalls neue Fähigkeiten zur erfolgreichen Zusammenarbeit in kollaborativen Arbeitssystemen.
Der zweite Erklärungsansatz bezieht sich auf das planerische Verständnis des praktischen Einsatzes kollaborationsfähiger Robotik: Die betrachteten Anwendungsfälle scheinen kollaborative Roboter als eine Art Industrieroboter ohne Schutzzaun zu verstehen, das heißt die Einsatzfelder werden analog zu den Einsatzfeldern der klassischen Robotik gedacht. Dies führt zunächst zur gedanklichen und dann zur praktischen Substitution klassischer Robotik durch kollaborationsfähige Roboter.
In der Konsequenz werden dadurch im überwiegenden Fall kooperierende Systeme entstehen. Dies führt umgekehrt jedoch zu dem Schluss, dass kollaborative Systeme nur geschaffen werden können, wenn bestehende Denkmuster überwunden und neue Einsatzmöglichkeiten für kollaborationsfähige Roboter erdacht werden, die dem Potential der Technologie gerecht werden. Als einfaches Beispiel sei hier die Anwendung des Roboterarms als dritten oder gegebenenfalls auch vierten Arm des Werkers genannt. Dies stellt neue Herausforderungen an den Planer des Arbeitssystems – sowohl hinsichtlich der Aufteilung der Tätigkeiten zwischen Mensch und Roboterarm als auch hinsichtlich der Koordination der zusätzlichen Arme .
Fazit und Ausblick
Die analysierten Anwendungsfälle zeigen, dass sich eine Vielzahl an Unternehmen – Konzerne wie Mittelständler – mit der Technologie kollaborationsfähiger Robotik beschäftigen. Dies ist aus Sicht des Autors positiv zu bewerten, da dies bedeutet, dass wertvolle Erfahrungen mit den technischen Eigenarten, dem Betrieb, der Sicherheit und Akzeptanz der Technologie gesammelt werden – zumindest trifft dies auf den derzeit offensichtlich dominierenden, kooperierenden Anwendungsfall zu.
Dies ist ein guter Ausgangspunkt, die Anwendungen evolutionär in Richtung einer vollständigen Kollaboration weiterzuentwickeln. Dazu wird neben unternehmerischem Mut auch eine Veränderung des technologischen Verständnisses sowie resultierend eine Anpassung der existierenden Planungssystematiken im Bereich Arbeitssystemgestaltung (in enger Kooperation mit der Produktgestaltung) notwendig sein. Dann besteht die Chance, dass sich die im Bild 3 dargestellte kleine Schnittmenge der MRK im Spannungsfeld zwischen den Faktoren Prozess, Produkt, Arbeitssystem und Personal signifikant vergrößert und die Anzahl der „echten“ Anwendungen ansteigen wird.
Literatur:
[1] Quirin, I.: Kollege Roboter. In: Creditreform – Das Unternehmermagazin, Nr. 10, 2016.[2] Leichtbaurobotik. Deutsches Zentrum für Luft- und Raumfahrt e.V., DLR Robotik und Mechatronik Zentrum. Online unter: http://www.dlr.de/rmc/rm/de/desktopdefault.aspx/tabid-3803/, abgerufen am 08.04.2017.[3] Onnasch, L.;Maier, X.; Jürgensohn, T.: Mensch-Roboter-Interaktion – Eine Taxonomie für alle Anwendungsfälle. In: baua: Fokus, Bundesanstalt für Arbeitsschutz und Arbeitsmedizin, Dortmund, 2016.[4] Arbeiten Hand in Hand: Ford in Köln setzt auf kollaborierende Roboter für zusätzliche Ergonomie. Ford Motor Company, Mitteilung vom 20.06.2016, online verfügbar unter: https://www.at.ford.com/de/homepage/deutsch/seiten/2016/6/kollaborierende-leichtbauroboter-uebernehmen-bei-der-stossdaempf.html, abgerufen am 10.04.2017.[5] VDMA-Positionspapier „Sicherheit bei der Mensch-Roboter-Kollaboration“. VDMA, Wissenschaftliche Gesellschaft für Montage, Handhabung und Industrierobotik (MHI) e.V., Frankfurt/Main, 2016.
Prof. Dr.-Ing. Christian Köhler, MBA, Jahrgang 1980, ist Professor für Wirtschaftsingenieurwesen an der Hochschule für Technik und Wirtschaft des Saarlandes (htw saar) in Saarbrücken und Mitglied der wissenschaftlichen Leitung des Wirtschaftsingenieurwissenschaftlichen Instituts (WIIN) der htw saar.