Agile Prozesse für die E-Motoren-Produktion in Deutschland
Hybride sowie vollelektrische Fahrzeuge benötigen elektrische Traktionsmotoren – und diese müssen in bester Qualität und höchstmöglicher Leistungsdichte produziert werden. Kann dies am Standort Deutschland gelingen?
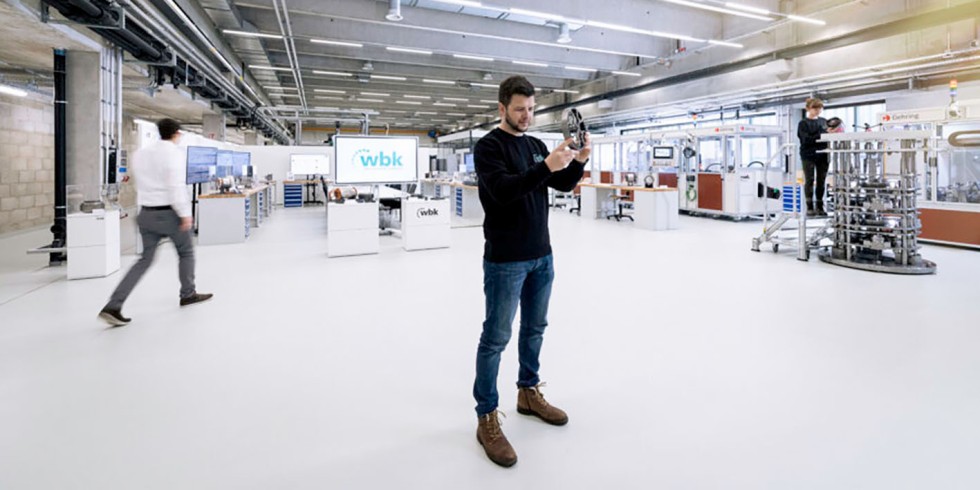
Versuchsumgebung der Ausbildungsfabrik "Statorfertigung" in der Karlsruher Forschungsfabrik. Das Ziel lautet hier, etablierte Prozesse zu optimieren und unreife Prozesse zu ertüchtigen. Praxisnahe Forschung wird an realen Fertigungsverfahren vorangetrieben - zum Beispiel für die E-Motoren-Produktion.
Foto: wbk Karlsruhe/Bramsiepe
Im Vorhaben „AgiloDrive2“, das am Karlsruher Institut für Technologie (KIT) koordiniert wird, sollen genau dafür die Grundlagen geschaffen werden. Im Projekt entwickeln seit Kurzem ForscherInnen besonders agile Fertigungs- und Montageprozesse, die eine wirtschaftliche Produktion von E-Motoren in Deutschland möglich machen sollen.
Klimawandel erfordert besondere Maßnahmen – und zwar sofort
Vor dem Hintergrund der weltweiten Anstrengungen gegen den Klimawandel ist im Verlauf des aktuellen Jahrzehnts von einer grundlegenden Transformation der automobilen Wertschöpfungsketten auszugehen. Diese führt weg vom konventionellen Verbrennungsmotor, hin zur Entwicklung und Produktion elektrischer Mobilitätslösungen.
Der elektrische Traktionsmotor nimmt – unabhängig von der Art des Energie-Speichersystems – eine leistungs- und effizienzbestimmende Rolle in hybriden sowie vollelektrischen Antriebssträngen ein und muss daher bei geringen Kosten in höchster Qualität und Leistungsdichte produziert werden. Die Topologie und die funktionellen Eigenschaften der eingesetzten Elektromotoren unterscheiden sich dabei je nach Art des Antriebsstrangs sehr deutlich – etwa bezüglich der Wicklungsart, des Bauraums und des Betriebsverhaltens.
Volatile Märkte, sich verändernde wirtschaftliche und rechtliche Rahmenbedingungen sowie technische Weiterentwicklungen führen zudem zu einer großen Unsicherheit hinsichtlich der zu erwartenden Stückzahlen und eingesetzten Technologien. Das Risiko, in starre Produktionssysteme zu investieren, die sich nicht weiterentwickeln können, ist daher als vergleichsweise hoch einzustufen.
Hilfreich: Ein modularer Baukasten für Traktionsmotoren
Das wbk Institut für Produktionstechnik des KIT – ein Institut der WGP (Wissenschaftlichen Gesellschaft für Produktionstechnik) –, hat sich aus diesem Grund zum Ziel gesetzt, ein agiles Produktionssystem und einen zukunftsrobusten Produktbaukasten für elektrische Traktionsmotoren zu entwickeln. Dies geschieht gemeinsam mit dem Institut für Produktentwicklung (IPEK) und dem Elektrotechnischen Institut (ETI), die ebenfalls am KIT angesiedelt sind. „Mit im Boot“ sind außerdem der Automobilzulieferer Schaeffler sowie 16 weitere Forschungspartner.
Das Ziel lautet: Die Forschenden wollen es Automobilzulieferern und -herstellern ermöglichen, Produktionssysteme in bedarfsgerechten Betriebspunkten zu betreiben und kostensenkende Skaleneffekte durch software-basierte Prozessanpassungen über verschiedene Produktbaureihen und Technologien hinweg zu nutzen. Hierfür wird das Forschungsvorhaben AgiloDrive2 vom Bundesministerium für Wirtschaft und Klimaschutz (BMWK) in der Förderrichtlinie „Digitalisierung der Fahrzeughersteller und Zulieferindustrie“ bei einem Gesamtvolumen von 33,7 Millionen Euro über drei Jahre mit rund 16,4 Millionen Euro gefördert.
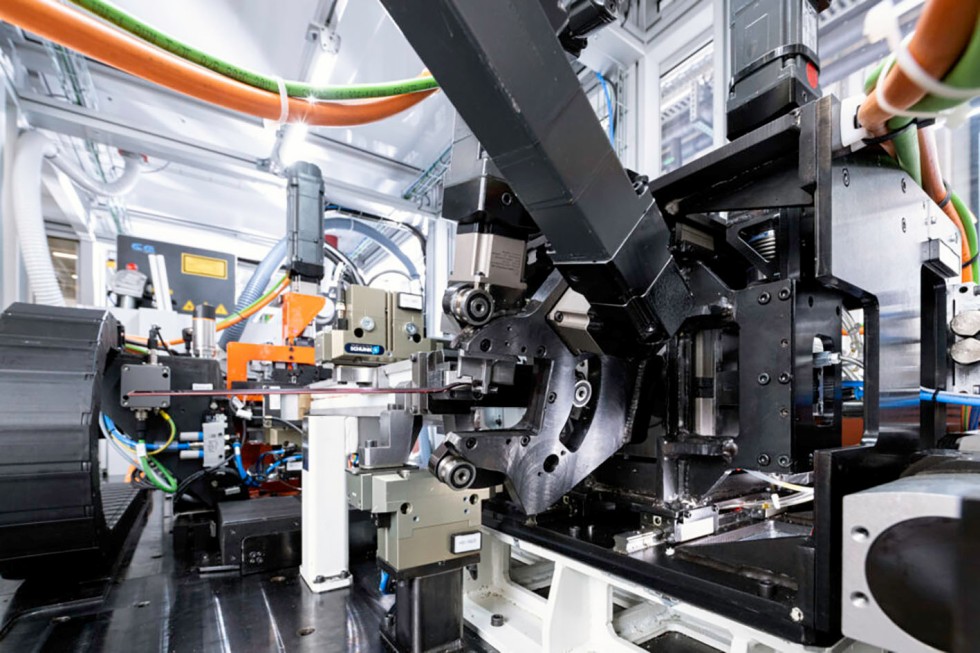
Formgebung von Hairpin-Steckspulen für die Fertigung von Statoren im Kontext der Elektromobilität.
Foto: wbk Karlsruhe/Bramsiepe
Um die Projektziele zu erreichen, wird unter der wissenschaftlichen Leitung des WGP-Professors Jürgen Fleischer erforscht, wie elektrische Traktionsmotoren – auf der Grundlage möglichst software-basierter Fertigungstechnologien, wandlungsfähiger Prozessketten und intelligenter Steuerungsarchitekturen – flexibel und nachhaltig gefertigt werden können. Durch den durchgängigen Einsatz modularer Funktionsstrukturen kann das Produktionssystem bedarfsgerecht skaliert, konfiguriert und verkettet werden. Dies reicht von der Topologie- bis zur Prozessebene. Vor diesem Hintergrund werden durch die Forschungspartner standardisierte Hard- und Softwareschnittstellen sowie herstellerübergreifende Kommunikationsstandards erarbeitet und implementiert.
Da das Produktionssystem sowohl seitens der Hardware als auch seitens der Software modular aufgebaut ist, wird es möglich, dessen zunehmende Komplexität zu beherrschen. Zudem kann die Produktionsausrüstung wiederverwendet werden – ganz im Sinne von Wirtschaftlichkeit und Nachhaltigkeit.
Digitale Zwillinge steigern die Fertigungsqualität
Der Einsatz digitaler Zwillinge – von den frühen Phasen der Produktentwicklung über die Produktionsplanung bis hin zur Inbetriebnahme der Fertigungs- und Montageprozesse – verkürzt die Time-to-Market signifikant. Diese stellt einen wichtigen Faktor zum Erhalt der internationalen Wettbewerbsfähigkeit der deutschen Automobil- und Zulieferindustrie dar. Eine durchgängige Datenerfassung entlang der Prozessketten zur Stator- und Rotorproduktion ermöglicht darüber hinaus den Einsatz datenbasierter Optimierungsalgorithmen, die die Fertigungsqualität steigern.
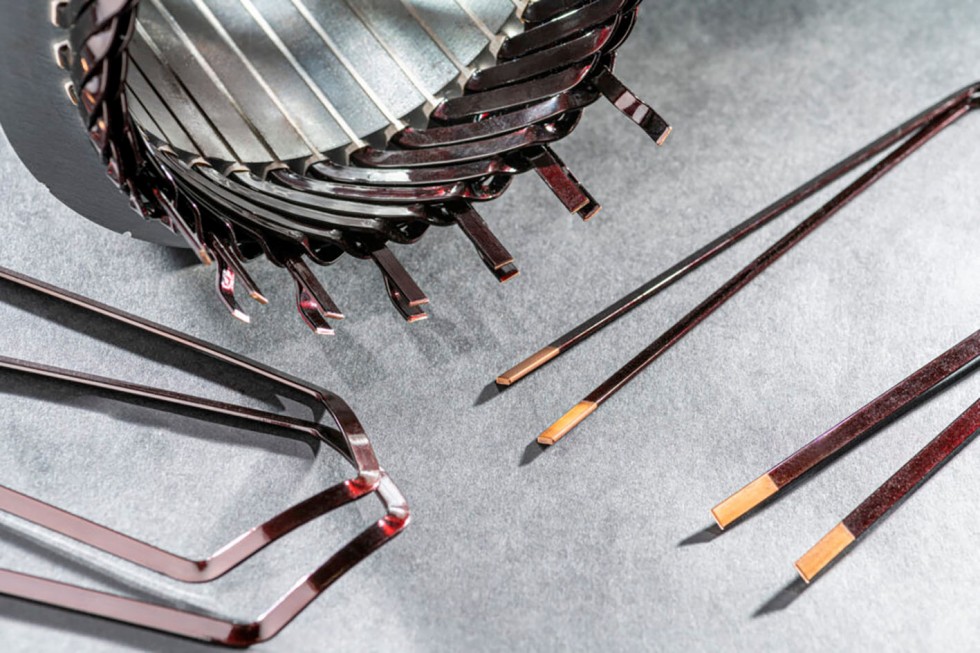
Stator mit Hairpin-Wicklung aus der Pilotphase des Forschungsvorhabens „AgiloDrive“ am wbk Institut für Produktionstechnik des KIT.
Foto: wbk Karlsruhe/Breig
Die im Forschungsvorhaben betrachteten Produktionstechnologien umfassen dabei klassische Handhabungs- und Fügeprozesse, aber auch hochkomplexe Sonderprozesse der E-Motoren-Produktion, wie die Formgebung und das „Twisten“ von Hairpin-Steckspulen aus isoliertem Kupferflachdraht.
Das könnte Sie auch interessieren:
Automobilbranche im Umbruch – welche Strategien helfen?