Aluminium-Schweißen: Bewährte Technologie jetzt für Zulieferer der Automobilbranche verfügbar
Probleme beim Aluminium-Punktschweißen sind ein weitverbreitetes und bekanntes Thema. Diese führen zu unsauberen Schweißpunkten, erhöhtem Elektrodenverschleiß und häufigem Nachfräsen – alles Faktoren, die in der Produktion von Fahrzeugen Zeit und Kosten verursachen.
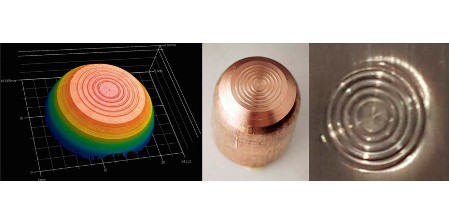
Eine Schweißkappe mit wegweisender MRD-Struktur für Aluminium-Anwendungen: Die fortschrittliche Technologie steht jetzt auch für OEMs und Zulieferer der Automobilindustrie zur Verfügung.
Foto: Kyokutoh
Eine Lösung dafür ist die MRD (Multi-Ringed Dome)-Technologie, die seit Jahren erfolgreich bei Automobilherstellen wie GM (General Motors) eingesetzt wird. Dank einer kürzlich unterzeichneten Lizenzvereinbarung mit der General Motors Company ist es dem japanischen Spezialisten Kyokutoh nun möglich, diese revolutionäre und patentierte Technologie in die eigenen Produkte zu integrieren. Somit lässt sie sich auch OEM (Original Equipment Manufacturer)- und Zulieferer-Kunden zur Verfügung stellen. Damit können auch diese von deutlich verbesserten, langlebigen Schweißverbindungen auf Aluminium profitieren.
Game-Changer für die Automobilproduktion
„Die MRD-Technologie ist ein echter Game-Changer für alle, die an der Lieferkette der Automobilproduktion beteiligt sind,“ erklärt Tamer Demirkaya, Geschäftsleitung von Kyokutoh Europe. „Unsere Kunden profitieren von einer signifikant besseren Durchdringung des Oxidfilms auf Aluminiumblechen, was die Qualität und Effizienz ihrer Produktionsprozesse spürbar steigert. Damit setzen wir einen neuen Standard im Schweißen von Aluminium.“
Zum Hintergrund: Punktschweißelektroden (Schweißkappen) am Ende einer Schweißzange übertragen den Schweißstrom und die Elektrodenkraft auf das Werkstück. Bleche, die im Schweißprozess miteinander verbunden werden, hinterlassen dabei stetig Rückstände auf den Zangenkappen, was Qualitätsverluste zur Folge hat. Früher wurden die Kappen händisch mit Zange und Feile gereinigt – dies ist bei immer schnelleren Taktraten an den Fertigungslinien für Automobile keine Option mehr, sodass inzwischen Fräsautomaten zum Einsatz kommen.
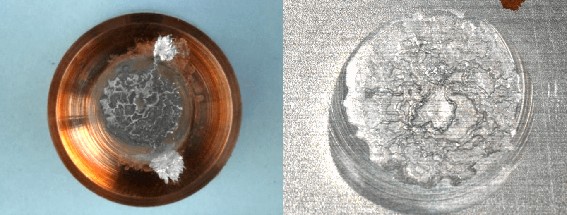
Die konventionell gefräste Schweißkappe (links) zeigt eine geschädigte Kontaktfläche. Rechts ist die dazugehörige Blechoberfläche zu sehen.
Foto: GSImbH, Niederlassung SLV München
Herkömmlich gefräste Schweißkappen führen zu Legierungseffekten zwischen den Schweißkappen und den Aluminiumbauteilen. Ursache dieses Effekts ist das ungenügende Durchbrechen der isolierenden Oxidschicht auf dem Aluminiumblech durch konventionell bearbeitete Elektroden. Daraus ergibt sich eine Überhitzung an diesen Durchbruchstellen bei Einleiten des Schweißstroms, was zu metallischen Verbindungen zwischen Kupfer und Aluminium führt.
Durch wiederholtes Punktschweißen verstärkt sich dieser Effekt und erhöht den Kontaktwiderstand zwischen Kappe und Blech immer weiter. Die Folgen sind eine negative Anmutung der Blechoberfläche und eine Zunahme der Porosität im Schweißpunkt. Abhilfe schafft bisher nur frühzeitiges Fräsen, was zu enorm hohem Kappenverbrauch und längeren Taktzeiten führt.
Neuartige Elektroden-Geometrie löst die Probleme
Die MRD-Technologie löst diese Aufgabenstellung, in dem die Elektroden nicht mehr glatt, sondern rillenförmig gefräst werden. Die dreidimensionale Geometrie aus kreisförmigen Erhöhungen und Vertiefungen durchdringt beim Kontakt der Kappe mit dem Aluminium die Oxidschicht in definierter Form und großer Fläche. Das ergibt ein Höchstmaß an Leitfähigkeit für den Schweißstrom. Damit können deutlich mehr Schweißpunkte erstellt werden, die sich zudem durch einer perfekten Punktoberfläche ohne Nachfräsen der Schweißkappen erstellt werden.
Die Technologie ist mit den neuen Kappenfräser-Modellen von Kyokutoh namens „CDF“ und der Kappenfräser-/wechsler-Kombination „XCD“ verfügbar. Beide Produkte sind speziell auf die hohen Anforderungen in der Automobilindustrie abgestimmt. Die Fräser-Wechsler-Kombinationen erhöhen die Automatisierung des Kappenhandlings noch weiter. Das Kappenfräsen und Kappenwechseln wird in einer Geräteeinheit zusammengeführt. Die beiden Prozesse lassen sich dadurch optimal aufeinander abstimmen und effizienter erledigen.
Zu beachten ist, dass die MRD-Technologie vorerst nicht für die Produktion von Full-Size-Pickup-Trucks verwendet werden darf. Dennoch bieten die neuen Modelle vielfältige Anwendungsmöglichkeiten, die sich perfekt für die Herstellung von Aluminiumkomponenten in anderen Fahrzeugklassen eignen. Tamer Demirkaya fügt hinzu: „Unser Ziel ist es, unseren Kunden die fortschrittlichsten Werkzeuge an die Hand zu geben, damit sie in dieser wettbewerbsorientierten Branche erfolgreich bleiben. Die MRD-Technologie steht für unser Engagement, innovative und praxistaugliche Lösungen zu entwickeln.“
Über den japanischen Schweißtechnik-Experten
Kyokutoh, 1953 in Nagoya in Japan gegründet, gilt als Spezialist für intelligente Anwendungen in der Schweißtechnik. Effektive und kostenbewusste Fügetechnik ist in der modernen Karosserie-Produktion unverzichtbar und gilt als das Fundament automatisierter Produktionsstraßen. Als global agierendes Unternehmen unterstützen die Experten partnerschaftlich fast alle großen Automobilkonzerne und -zulieferer und haben es sich zur Mission gemacht, für jeden Bedarf die passende Lösung anzubieten. Die Japaner gehören zu den Weltmarktführern für effiziente, automatische Elektroden-Kappenfräser und -wechsler. Die Expansion nach Europa fand ab dem Jahr 2008 statt. Der Hauptsitz der Kyokutoh Europe GmbH mit Zuständigkeit für den Wirtschaftsraum EMEA (Europe, Middle East, Africa) wurde 2011 in München/Deutschland eröffnet und über die Jahre stetig erweitert. Im November 2022 folgte die Verlegung des Hauptsitzes nach Unna bei Dortmund, um diesen mit dem dortigen Technik- und Logistikzentrum zu vereinen. Seitdem unterstützt die Europäische Zentrale von Unna aus die Kunden im Wirtschaftsraum EMEA bei der Optimierung ihrer Schweißprozesse.
Das könnte Sie auch interessieren:
Karosseriebearbeitung: Fehlstellen erkennen und zuverlässig beseitigen