Batterie-Recycling: Vom Problemfall zum erfolgreichen Geschäftsmodell
Die Elektrifizierung unserer Welt schreitet in atemberaubendem Tempo voran. Doch was passiert mit den ganzen dabei benötigten Batterien am Ende ihrer Nutzungsdauer?
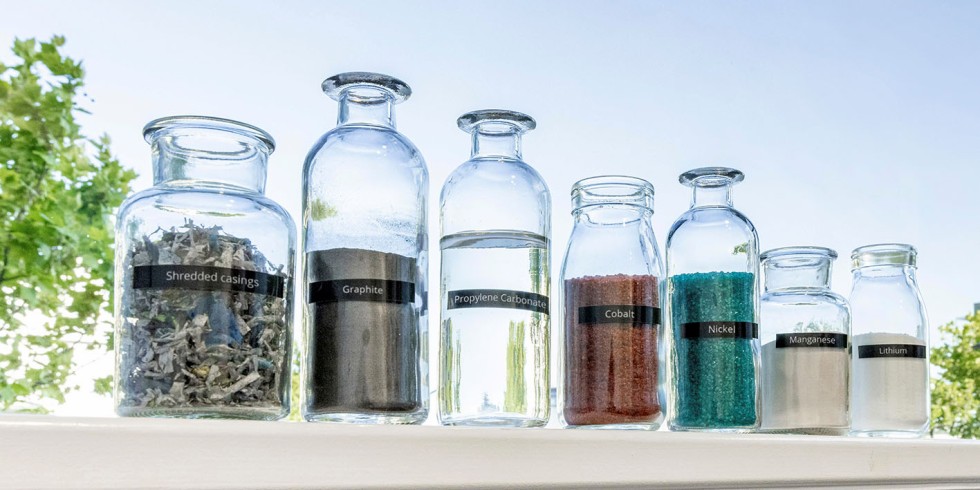
Im Recyclingprozess herausgelöste Wertstoffe: Die direkte Integration des hydrometallurgischen Prozesses führt bei der Primobius-Anlage zu den höchsten Rückgewinnungsquoten, die es bei der Verwertung von Lithium-Ionen Batterien bislang gibt.
Foto: SMS
Mit dem Zuwachs der Elektromobilität erhöht sich der Bedarf an Speicherlösungen ebenso rasant, wie die Nachfrage nach Rohstoffen für deren Produktion. Bis 2030 sind in Europa neue Produktionsstätten für Lithium-Ionen-Batterien (LiB) mit einem Output von über 700 Gigawattstunden geplant. Doch diese benötigen viele kostbare Rohstoffe, die bisher überwiegend in umweltschädigenden Verfahren abgebaut werden. Wie sich ein alternativer Weg beschreiten lässt, und was sich der Laie unter einer „schwarzen Masse“ vorstellen darf, wird im Folgenden beschrieben.
Der Rohstoffbedarf ist enorm – die Belastung ebenso
Aufgrund der zunehmenden Batterieproduktion wächst auch der Bedarf an Nickel, Lithium und Kobalt rasant. Die weltweit seltenen Rohstoffe werden heute CO2-intensiv über komplexe Produktions- und Logistikketten gewonnen – teilweise in Entwicklungsländern. Die CO2-Bilanz von LiB ist – kurzfristig betrachtet – deshalb negativ belastet. Batteriebetriebene E-Fahrzeuge erreichen erst nach vielen Jahren einen Break-Even-Punkt in der CO2-Bilanz.
Im Fokus der meisten Nachhaltigkeitsinitiativen steht die Reduzierung der CO2-Emissionen und die damit verbundene Optimierung des CO2-Fußabdrucks von Prozessen und Produkten. Um die ambitionierten Dekarbonisierungsziele erreichen zu können, benötigt die Industrie, allen voran die Automobilbranche, innovative Ansätze – insbesondere für bessere und nachhaltigere Recycling-Lösungen für Lithium-Ionen-Batterien.

Pilotanlage in Hilchenbach: Bereitgestellt wird ein sicherer geschlossener Kreislauf, bei dem sämtliche Prozessschritte aufeinander abgestimmt sind und aus einer Hand stammen.
Foto: Etmanski
Energiesparendes Verfahren für ein standortnahes Batterie-Recycling
Um das enorme Marktpotenzial mit einer emissionsarmen Recycling-Lösung für Lithium-Ionen-Batterien im industriellen Maßstab zu erschließen, bündeln zwei kompetente Partner ihre Kräfte. „Primobius“ ist ein Joint-Venture, das im Jahr 2020 zwischen dem australischen Unternehmen Neometals Ltd. und dem deutschen Technologieunternehmen SMS group gegründet wurde.
In seinem zweistufigen Recycling-Prozess – und dem sogenannten „Hub and Spoke“-Ansatz folgend – werden mechanische und hydrometallurgische Verfahren kombiniert. Diese gelten als besonders energieeffizient, erlauben eine Dekarbonisierung der Lieferkette und bieten eine hohe Rückgewinnungsquote für die in den Batterien enthaltenen Materialien. Somit wird erstmals der komplette Prozess der Rückgewinnung in einem integrierten System abgebildet:
- In der ersten Stufe werden Lithium-Ionen-Altbatterien verschiedener Größen und Typen geschreddert und in Kunststoffteile, Metallteile sowie ein als Black Mass bezeichnetes Zwischenprodukt sortiert. Diese mechanischen Prozesse können dezentral stattfinden, zum Beispiel bei Kundenunternehmen.
- Die zweite Stufe – die nasschemische Rückgewinnung von Materialien aus der Black Mass – erfolgt in zentral gelegenen Anlagen, auch bekannt als „Hubs“. In diesem Prozess werden wertvolle Stoffe extrahiert, darunter Lithium, Nickel und Kobalt. Die so zurückgewonnenen Materialien sind von hoher Reinheit und können im Rahmen einer Kreislaufwirtschaft direkt in die Lieferkette und den Produktionsprozess neuer Zellen eingebracht werden.

Blick auf die Primobius-Recyclinganlage für Lithium-Ionen-Batterien am SMS-group-Standort in Hilchenbach.
Foto: SMS
Zusatznutzen: Der gewählte Prozess läuft auch noch CO2-frei ab. Brand- und Gefahrstoffrisiken werden durch den Hub and Spoke-Ansatz gesenkt. Außerdem werden Kosten und CO2-Ausstoß eingespart, weil sich Transporte der Batterien vermeiden lassen.
Hydrometallurgie „arbeitet“ emissionsarm und effizient
Hersteller von Lithium-Ionen-Batterien sind gesetzlich verpflichtet, Batterien am Ende ihrer Nutzung zurückzunehmen und zu verwerten. Aktuell wird dieses Ziel jedoch häufig nicht erreicht, sodass viele der Batterien auf Mülldeponien enden. Häufig werden sie auch ineffizienten, auf dem Einschmelzen der Batterien basierenden Recyclingverfahren zugeführt. Diese erzielen nur eine geringe Rückgewinnungsquote der Bestandteile. Die Innovation des von Primobius entwickelten Recyclingprozesses liegt insbesondere darin, dass auf einen energieintensiven, pyrometallurgischen Prozess gänzlich verzichtet wird. Dies unterscheidet das Verfahren von alternativen Methoden des Wettbewerbs.
Das hydrometallurgische Verfahren bietet bei niedrigen Temperaturen einen höheren Wirkungsgrad. Rückgewinnungsquoten von über 95 Prozent (speziell für Nickel und Kobalt) beziehungsweise größer als 85 Prozent (bei Lithium) setzen neue Maßstäbe. Ziel ist eine Rückgewinnung von über 90 Prozent, gemessen am gesamten stofflichen Einsatz. Bereits heute werden die Vorgaben der Europäischen Kommission für das Jahr 2025, die eine Rückgewinnungsquote von 65 Prozent vorschreiben, deutlich übertroffen.

Ulf Rademacher (rechts), Corporate Development Specialist Primobius, erklärt Pressevertretern die Funktionsweise der Anlage in Hilchenbach.
Foto: SMS
Auch für Materialien, die bislang nicht oder kaum zurückgewonnen werden konnten – wie Grafit oder der Elektrolyt –, wird eine Wiedergewinnung möglich. Alles in allem kann so der CO2-Fußabdruck einer LiB von aktuell etwa acht Tonnen um bis zu 70 Prozent reduziert werden.
Proof of Concept: Demonstrationsanlage in Hilchenbach
Nach erfolgreicher Entwicklung der Prozess-Technologie wurde bereits ein Jahr nach der Gründung eine vollständig funktionsfähige Anlage zum Recycling von Lithium-Ionen-Batterien errichtet. Das aktuell am SMS-group-Standort Hilchenbach aufgebaute Recyclingsystem ist die erste von Primobius errichtete Anlage. Sie diente Anfangs dazu, das Verfahren zu testen und seine Vorteile live zu demonstrieren. Bisher kam sie für das Erstellen von Machbarkeitsdaten und zur Unterstützung bei der Prozessoptimierung zum Einsatz. Die Schredderanlage – mit einer Kapazität von zehn Tonnen täglich – wurde aber von Anfang an im Hinblick auf den Bedarf der Lieferketten für LiB-Hersteller in Europa errichtet.
Im Frühjahr 2022 wurde die Demonstrationsanlage in Hilchenbach in den kommerziellen Betrieb überführt. Heute wird der komplette mechanische Separierungsbereich im Zweischichtbetrieb am Standort betrieben. Kunden haben somit die Möglichkeit, ihre Lithium-Ionen-Batterien der Typen NMC (Lithium-Nickel-Mangan-Cobalt-Oxide), NCA (Lithium-Nickel-Cobalt-Aluminium-Oxide) oder LCO (Lithium-Cobalt-Oxide) aus Unterhaltungselektronik oder E-Fahrzeugen in Hilchenbach nachhaltig zu entsorgen. Eine eventuell enthaltene Restladung wird entnommen und die Restenergie kann sogar im Recyclingprozesses genutzt werden. Module unterschiedlicher Herstellungsart werden vorsortiert und notwendige Demontagearbeiten in Handarbeit an entsprechenden Stationen vorgenommen.
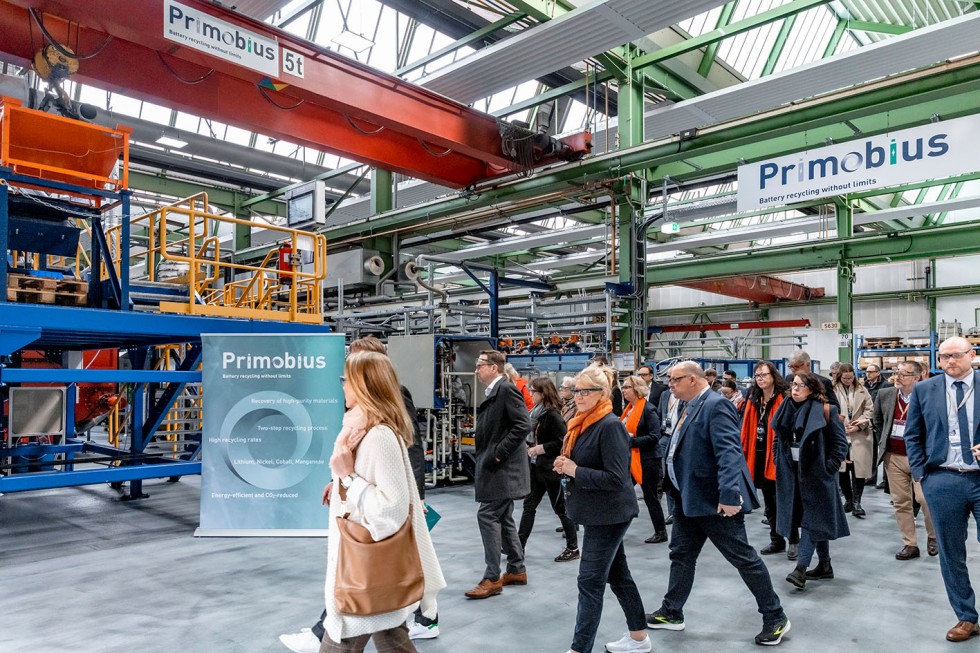
Rundgang durch die Primobius-Anlage: Die konsequente Reduzierung von CO2-Emissionen über alle Prozessstufen hinweg wirkt sich positiv auf die Klimabilanz des Produktlebenszyklus des Batteriemoduls aus – sowie des E-Fahrzeugs, in dem es eingesetzt wird.
Foto: SMS
Als Endprodukt, resultierend aus mechanischem Zerkleinern und Aufbereiten, entsteht in eine Mischfraktion aus Kupfer-, Aluminium- und Plastikteilen. Diese Materialien werden im Sinne einer Kreislaufwirtschaft dem Markt direkt wieder zugeführt. Die Black Mass als Zwischenprodukt der Schredderanlage wird derzeit noch verkauft, bis sie für die weitere Verarbeitung durch eine kommerzielle Primobius-Raffinationsanlage aufgenommen werden kann.
Die nachhaltige Schließung des Wertstoffkreislaufs
Diese Verwertung von Batterierückläufern als „urbane Mine“ – sowie die direkte Re-Integration des Rezyklats in die Kreislaufwirtschaft – sorgen für eine gewisse Unabhängigkeit von den Volatilitäten des Rohstoffmarktes. Damit können sie die deutsche und auch die europäische Automobilindustrie vor der strategischen Gefahr von Lieferengpässen schützen. Darüber hinaus verbessert die Technologie den nationalen Anteil der Wertschöpfung an der Batterie von derzeit rund 20 bis 30 Prozent auf 80 bis 90 Prozent. Dies kann ein wirkungsvoller Hebel sein, um die Umweltbilanz der Batterien und somit der gesamten Elektromobilität zu verbessern.
Die Vorteile dieses Recycling-Prozesses haben bereits namhafte Unternehmen erkannt. Erste Partnerschaften wurden bereits geschlossen. Mit Blick auf die zukünftige Rücknahme von Lithium-Ionen-Batteriesystemen erweitert beispielsweise Mercedes-Benz seine globale Recycling-Strategie. Am Mercedes-Benz Standort in Kuppenheim wird derzeit eine eigene Batterie-Recycling-Fabrik gebaut. Für die Anlage, die im Jahr 2024 in Betrieb gehen soll, wird Primobius seine Technologie in Lizenz zur Verfügung stellen. Die geplante Anlage soll CO2-neutral sein und eine Jahreskapazität von 2.500 Tonnen abdecken. Die zurückgewonnenen Materialien wird Mercedes-Benz wieder in den Herstellprozess von bis zu 50.000 neuen Batteriemodulen zuführen.
Eine große Summe an Vorteilen
Primobius beherrscht als nach eigenen Angaben einziger Anbieter in Europa sämtliche Stufen des Prozesskreislaufs – und bietet eine perfekt aufeinander abgestimmte Komplettlösung. Der Anbieter trägt dazu bei, die Lücke in der Lieferkette für Batteriezellen zu schließen, und fördert so den Aufbau einer nachhaltigen, Ressourcen schonenden sowie kompetitiven Batterieproduktion in Deutschland und Europa. Das junge Joint-Venture gewährleistet mit seinem umfassenden Know-how eine nachhaltige Rückgewinnungsmethode. Dabei sind gebrauchte und defekte LiB aus Elektrofahrzeugen und Unterhaltungselektronik die entscheidende Quelle. Die recycelten Rohstoffe senken wesentlich den CO2-Fußabdruck des Produktionsprozesses der LiB. Langfristig werden Planungs- und Versorgungssicherheit sichergestellt, Lieferketten stabilisiert und die Volatilität reduziert.
Das könnte Sie auch interessieren:
Batterien, Getriebe und Zahnräder im ökologischen Kreislauf
Nachhaltigkeit wird zur Pflicht: Ökobilanzierung für Automotive- und Industriebetriebe