Dichtheitsprüfung für Elektrofahrzeuge – Teil 2
Wenn bei einem modernen Elektrofahrzeug die Kühlung der Batterie ausfällt, schaltet eine Sicherheitselektronik die Batterie nach kurzer Zeit ab; das Fahrzeug bleibt stehen. Auf den verschiedenen Stufen des Fertigungsprozesses der Batteriekühlung führt deswegen kein Weg an einer sorgfältigen industriellen Dichtheitsprüfung vorbei.
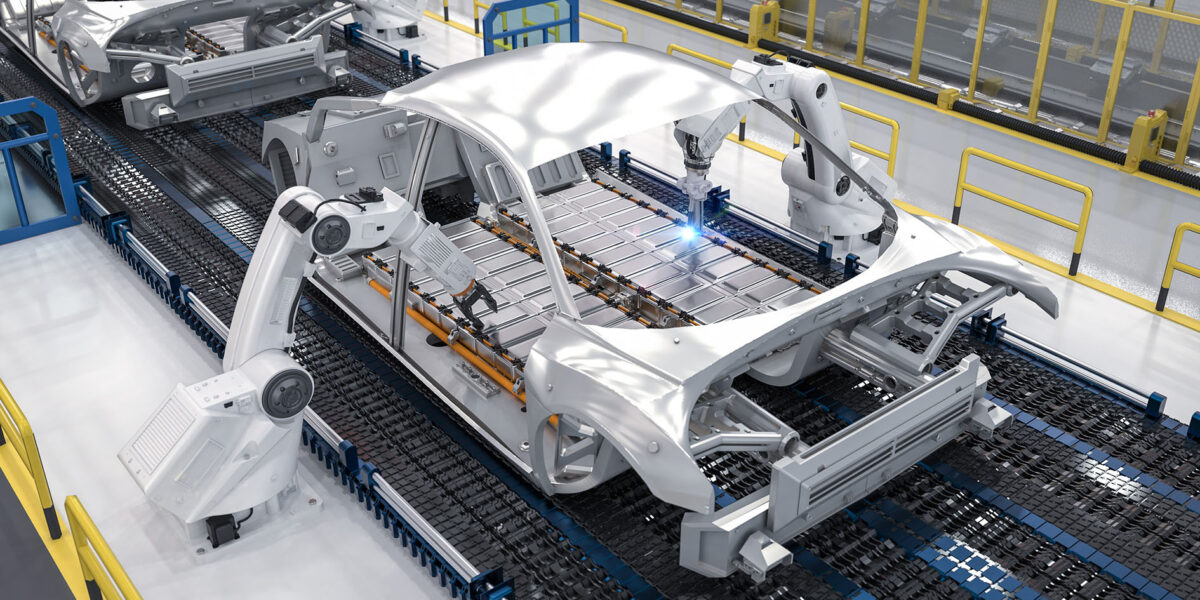
In der Automobilfertigung sind heute - zusammen mit den meisten Herstellungsschritten - auch viele Dichtheitsprüfprozesse bereits automatisiert. Grafik: Shutterstock
Bei einem Electric Vehicle (EV) sind die Folgen eines Klimaanlagen-Ausfalls gravierend. Bei Lithium-Ionen-Batterien reduziert eine zu hohe Betriebstemperatur nicht nur die Leistung – es besteht sogar die Gefahr eines desaströsen „Thermal Runaways“. Solch eine ungebremste Überhitzung der Traktionsbatterie führt in der Regel zu einem Brandgeschehen und zur völligen Zerstörung des Fahrzeugs. Teil 1 des zweiteiligen Fachbeitrags stellte die Wechselwirkungen zwischen der Dichtigkeit des Kühlsystems und dem Thermomanagement vor. Außerdem wurden Methoden der Vorprüfung beschrieben. In Teil 2 des Beitrags wird auf verschiedene Prüfvarianten und -systeme in den weiteren Schritten der Fahrzeugproduktion eingegangen.
Schnüffellecksuche an den Verbindungsstellen
Wenn die Kühlung der Antriebsbatterie „schwächelt“, führt dies zur Sicherheitsabschaltung, ansonsten wären die Folgen fatal. Vorgestellt wurde in Teil 1 des Beitrags bereits die industrielle Helium-Dichtheitsprüfung und die entsprechenden Geräte wie das „LDS3000“, außerdem die Schnüffellecksuche zur Vorprüfung von Kompressoren.
Die nächsten Dichtheitsprüfaufgaben stehen dann nach dem Zusammen- sowie Einbau der Klimaanlage beim Fahrzeughersteller an. Nach dem Einbau gibt es oft rund sechs bis acht Verbindungsstellen, deren Dichtheit überprüft werden sollte – bevor eventuell mehrere Liter recht teuren Kältemittels darauf verschwendet werden, einen undichten Kühlkreislauf zu befüllen. Das heißt: Werden Lecks schon vor den abschließenden End-of-Line-Tests erkannt, erspart dies unnötige Arbeitsschritte und Kosten in der Produktion. Bei dieser industriellen Schnüffellecksuche – sei sie mit Helium oder Formiergas – spielt ein Gerät wie der „XL3000flex“ (siehe Teil 1 des Fachbeitrags) einen weiteren Vorzug aus: Er kann die zu prüfende Gas- und Luftwolke mit einem sehr hohen Gasstrom von 3000 sccm ansaugen. So ist das Gerät in der Lage, auch Lecks an schwer zugänglichen Stellen zuverlässig zu detektieren.
Druckmessung allenfalls für die Grobleck-Erkennung geeignet
Auf diese Dichtheitsprüfung vor dem Befüllen verzichten zu wollen, wäre kurzsichtig. Denn bei genauer Betrachtung verfängt das Argument nicht, die Druckprüfung beim anschließenden Befüllschritt reiche doch aus. Die Befüllanlage muss zunächst die Atmosphärenluft aus dem Kältemittelkreislauf evakuieren, bevor sie ihn mit dem gasförmigen Kältemittel befüllen kann. In die Befüllanlage ist darum mitunter eine Druckanstiegsprüfung integriert, die es gestattet, Groblecks in dem evakuierten Kreislauf zu identifizieren. Wegen ihrer hohen Temperaturabhängigkeit eignet sich solch eine Druckmessung aber nicht für Prüfungen gegen sehr kleine Leckraten, weder bei der Vorprüfung der Komponenten durch den Zulieferer noch bei der Prüfung der eingebauten Klimaanlage durch den Fahrzeughersteller.
Wenn es darum geht, kleine Lecks in der erforderlichen Größenordnung von 0,5 bis 2 g Kältemittelverlust pro Jahr zu erkennen, versagen Druckprüfungen, weil bereits Temperaturänderungen von Bruchteilen eines Grads dazu führen, dass das Druckverfahren entweder reale Lecks nicht erkennt oder aber falsch positive Leckalarme generiert. Das recht große Füllvolumen des Kältemittelkreislaufs verschärft dieses Problem noch. Für das Anwendungsszenario, kleine Kältemittellecks aufzuspüren, ist die Druckmessung in der Regel um den Faktor 100 oder sogar 1000 zu unempfindlich. Und wird erst nach dem Befüllen festgestellt, dass die Dichtheit den Anforderungen doch nicht genügt, sind der Arbeitsaufwand für das Befüllen und das verwendete Kältemittel verloren.
End of Line: Das Kältemittel dient selbst als Prüfgas
Selbst wenn eine Prüfung mit Spürgas vor dem Befüllen mit Kältemittel stattgefunden hat, ist eine abschließende Prüfung auf austretendes Kältemittel unverzichtbar. Denn: Um die Dichtheit des Befüllstutzens zu testen, nachdem die Klimaanlage mit dem Kältemittel befüllt und verschlossen wurde, eignen sich weder die Vorprüfung mit Spürgas noch eine Prüfung mittels Druckverfahren. Für End-of-Line-Prüfungen am Ende der Fertigungslinie bieten sich stattdessen Schnüffellecksuchgeräte an, die die gasförmigen Kältemittel detektieren können, wenn sie aus etwaigen Lecks austreten – auch aus undichten Befüllstutzen. Einige moderne Multigas-Lecksuchgeräte können eine Vielzahl möglicher Kältemittel parallel erfassen, ob dies nun R1234yf, R1234ze, CO2 oder R600a ist.
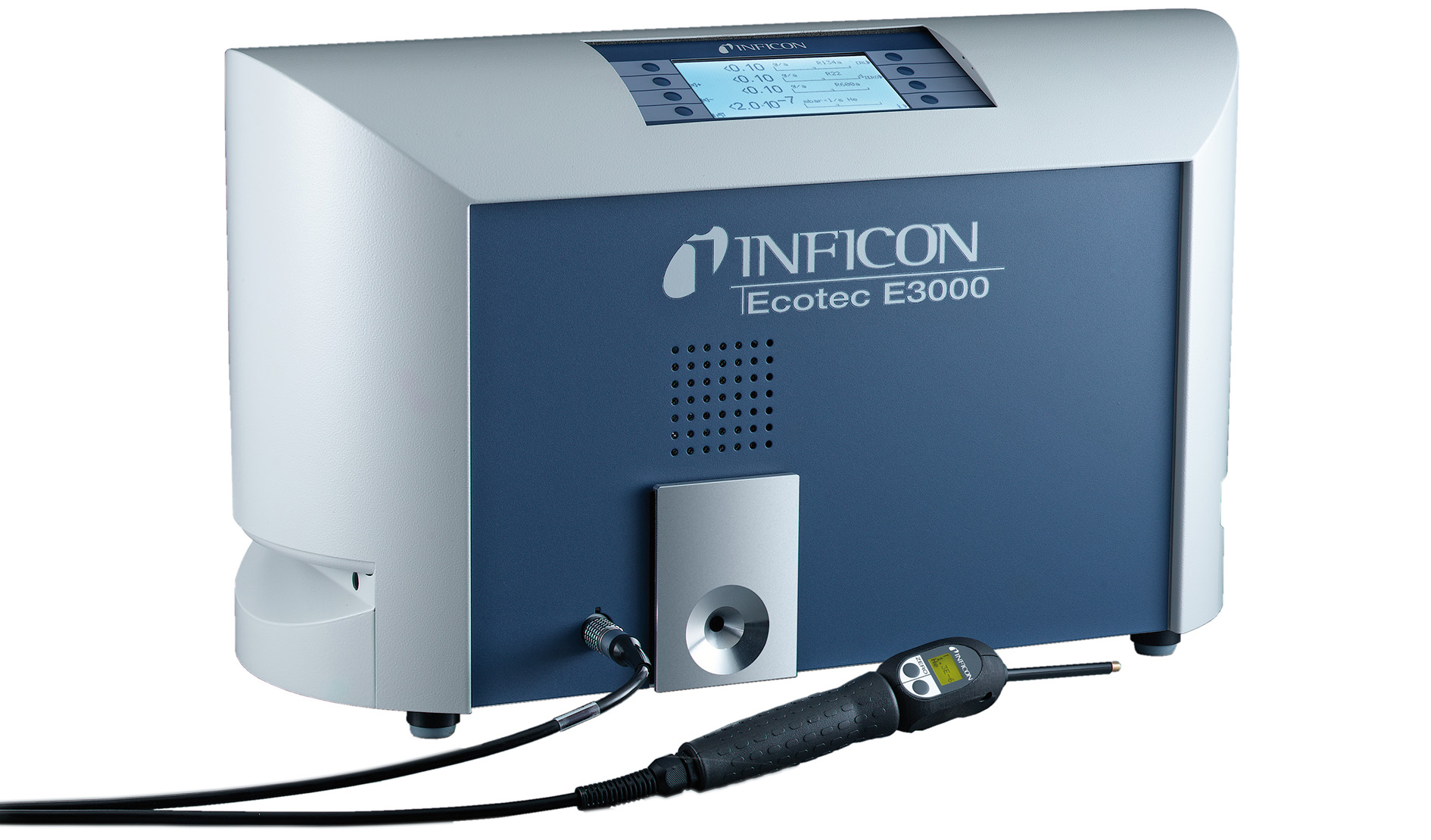
Bei End-of-Line-Dichtheitsprüfungen detektiert der Multigas-Schnüffellecksucher bis zu vier Kältemittelgase gleichzeitig.
Foto: Inficon
Die Nachweisgrenze des industriellen Multigaslecksuchers „Ecotec E3000“ von Inficon, der Luft ansaugt, um Gase mit einem Massenspektrometer zu detektieren, liegt bei ungefähr 0,05 g Kältemittelaustritt pro Jahr.
Infrarot-Technologie – ideal bei der Nacharbeit
Für die Nacharbeitsschleife, in der als undicht ausgeschleuste Klimaanlagen repariert werden, kann zur Leck-Lokalisierung und abschließenden Dichtheitskontrolle oftmals auch ein etwas weniger aufwendiges Gerät eingesetzt werden. Der „HLD6000“ beispielsweise ist ein Kältemittellecksucher, der mit einem Infrarotsensor arbeitet und so Lecks bis zu einer Größe von 0,5 g Kältemittelverlust pro Jahr lokalisiert.
Der Nachteil eines infrarotbasierten Geräts gegenüber einem Lecksucher, der mit einem Massenspektrometer arbeitet, liegt allerdings in der Querempfindlichkeit. Die Infrarotmethode ist nicht vollständig selektiv und würde beispielsweise auch auf ein Wasser-Glykol-Gemisch ansprechen, wie es in den Kühlkreisläufen der Elektromotoren oder auch in der Scheibenwaschanlage des Fahrzeugs verwandt wird. Der Einsatz eines Geräts mit Infrarotsensor erfordert also eine entsprechend größere Sorgfalt in der Anwendung.
Prozesssicherheit durch Kalibrierung und Testlecks
Als industrielle Kältemittellecksucher haben der Ecotec E3000 oder der HLD6000 aber auch Gemeinsamkeiten: Sie sind beide genauestens kalibrierbar, und sie verfügen über eingebaute Testlecks. So kann wenigstens einmal in jeder Schicht innerhalb sehr kurzer Zeit verifiziert werden, ob das Gerät noch korrekt kalibriert ist und die Dichtheitsprüfung tatsächlich mit der gebotenen Zuverlässigkeit stattfindet.
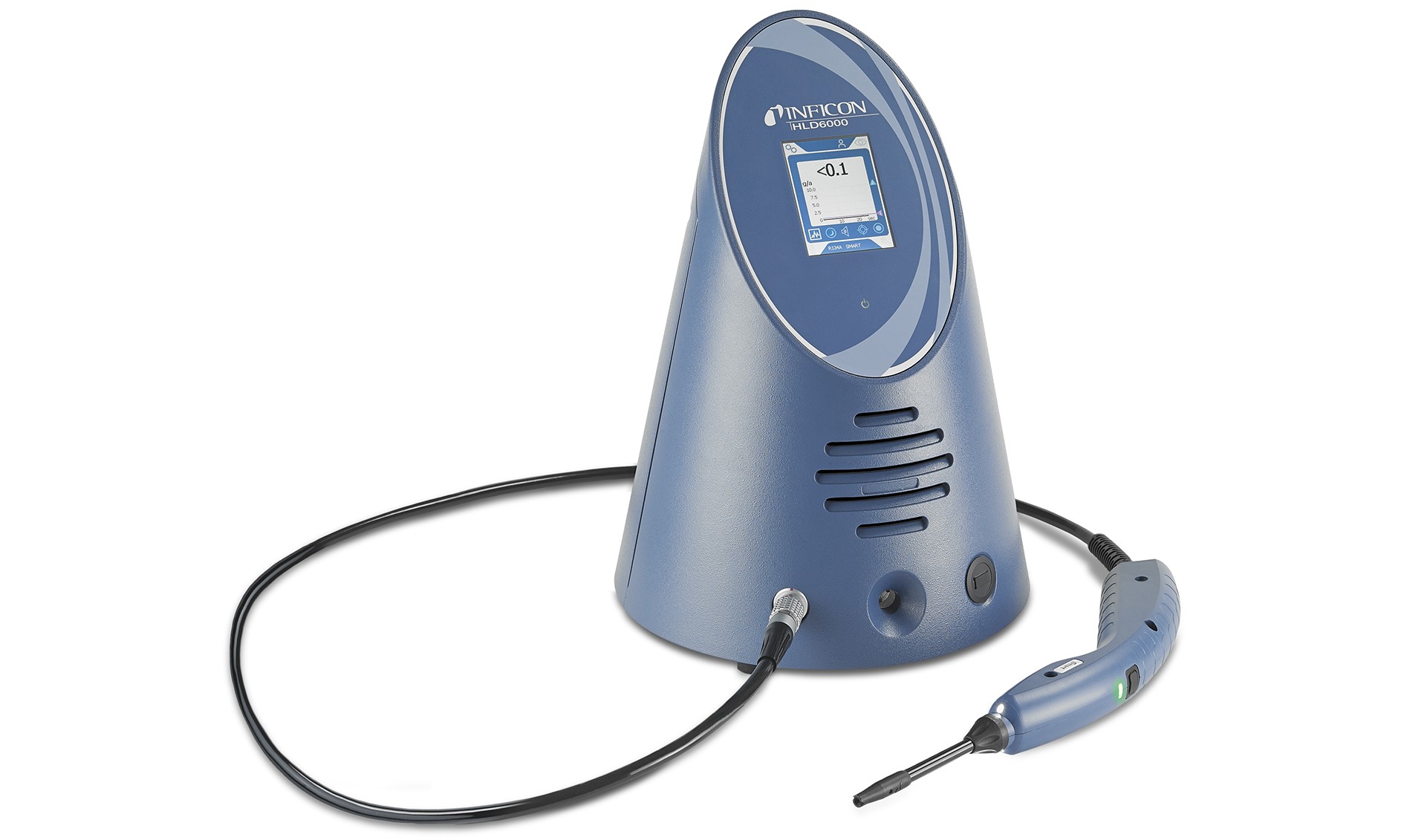
Der „HLD6000“ prüft mit einem Infrarotsensor und eignet sich besonders für die Schnüffellecksuche bei der Nacharbeit.
Foto: Inficon
Langlebigkeit ist ein weiterer Pluspunkt von Lecksuchgeräten, die für den Einsatz in der industriellen Fertigung konzipiert sind, denn sie sind für die Verwendung im Zwei- oder Drei-Schicht-Betrieb gebaut – für einen Dauereinsatz über Jahre.
Exkurs: Dichtheitsprüfung für den Wasser-Glykol-Kreislauf
In den meisten Fällen wird die Kühlung der Traktionsbatterie über einen Kühlkreislauf realisiert, der mit einem Wasser-Glykol-Gemisch befüllt ist. Dieser Wasser-Glykol-Kreislauf kühlt, weil er seinerseits über einen Wärmetauscher mit dem Kältemittelkreislauf der Klimaanlage verbunden ist. Natürlich ist auch für diesen Kühlkreislauf der Antriebsbatterie dauerhafte Dichtheit eine wichtige Anforderung. Genauer gesagt: die Wasserdichtheit. Das gravierende Problem bei Lecks im Wasser-Glykol-Kreislauf ist aber gar nicht eine immer mangelhaftere Kühlung der Antriebsbatterie. Viel kritischer ist, dass Wasseraustritt eine unmittelbare Kurzschlussgefahr für die Batterie bedeutet. Es ist also ein Unterschied, ob ein einfacher Wischwasser-Behälter auf Wasserdichtheit zu prüfen ist, oder aber der Kühlkreislauf der Antriebsbatterie.
Während man üblicherweise nach einer Prüfung gegen eine Grenzleckrate von 1·10–3 mbar·l/s davon spricht, ein Prüfteil sei wasserdicht, gelten im Kontext der Batterie weit strengere Maßstäbe – mit zehn- bis hundertfach kleineren Leckraten im Bereich von 10–4 bis 10–5 mbar·l/s. Bei Leckraten dieser Größenordnung sind Verfahren wie eine krude Blasenprüfung oder die temperaturanfällige Druckabfallprüfung eindeutig „überfordert“. Prüfgasbasierte Methoden der Wahl sind hier die Helium-Vakuummethode oder die Akkumulationsprüfung. Die Akkumulationsmethode benötigt zwar kein Vakuum in ihrer (weit weniger aufwendigen) Prüfkammer, sie ist allerdings auch langsamer als die Vakuummethode. Als Prüfgase dienen bei der Akkumulationsmethode entweder Helium oder Formiergas.
Fazit: Keine Fertigung ohne engmaschige Qualitätssicherung
In Verbrennerfahrzeugen ist die Klimaanlage ein Komfortmerkmal. Bei Elektrofahrzeugen hängt von ihr aber die grundlegende Funktionstüchtigkeit ab. Wenn die Batterie überhitzt, bleibt das Elektroauto einfach stehen. Darum lohnen sich Dichtheitstests bei allen relevanten Produktionsschritten des Kälte-Klima-Systems – von der Vorprüfung der Komponenten über die Prüfung nach dem Zusammenbau bis zu End-of-Line-Tests nach dem Befüllen mit dem gewählten Kältemittel. Schon aus wirtschaftlichen Gründen gilt es, die für die jeweilige Produktionsstufe sinnvollste Dichtheitsprüfmethode zu wählen. Nach dem Befüllen gibt es allerdings nur noch eine Option: den Einsatz eines industriellen Kältemittellecksuchgeräts.
Das könnte Sie auch interessieren:
Wenn die Klimaanlage ausfällt, bleibt das E-Auto stehen
Fahrzeugbau: Energieeffizienz steigern dank Gewichtsreduktion
Karosseriebearbeitung: Fehlstellen erkennen und zuverlässig beseitigen
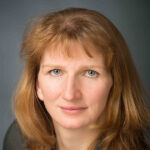
Sandra Seitz ist Market Manager Automotive Leak Detection Tools bei der Inficon GmbH in Köln. Foto: Inficon