Die Automobilindustrie vor der Euro-7-Herausforderung
Die neuen Feinstaub-Grenzwerte machen Druck auf die Hersteller und ihre Supplier: Die Reifen und insbesondere die Bremsanlagen der Fahrzeuge müssen „neu gedacht werden“. Doch wie könnte das Bremssystem der Zukunft aussehen? Experten geben Auskunft.
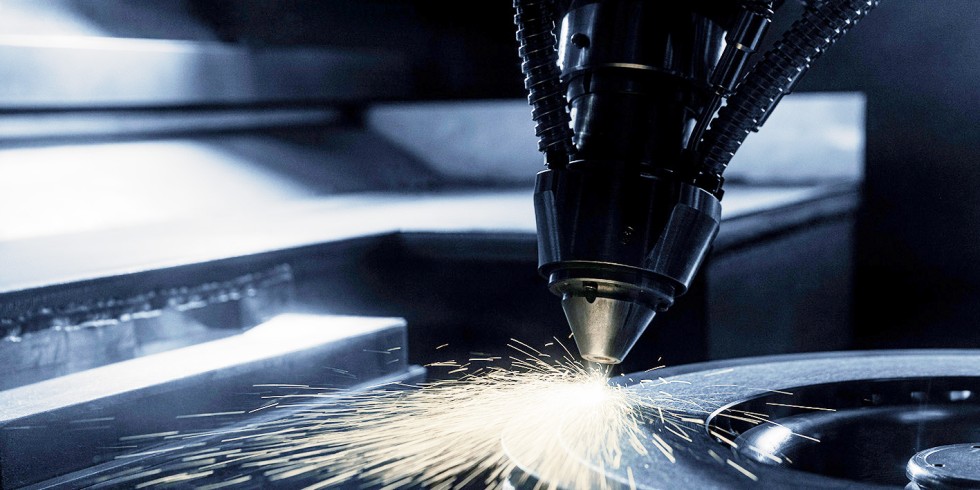
Tauglich für die automobile Großserie: Dank der Industrialisierung des Hochgeschwindigkeits-Laserauftragschweißprozesses lassen sich Bremsscheiben mit der „Wecodur“-Technologie nun reproduzierbar und wirtschaftlich beschichten.
Foto: HPL Technologies
Die EU-Kommission hat den Entwurf der neuen Euro-7-Abgasnorm präsentiert, der im Juli 2025 in Kraft treten soll. Besonders einem Thema widmet sich die neue Norm: Der ganzheitlichen Betrachtung aller Feinstaubquellen an jeder Art von Fahrzeug. Die VDI-Z sprach mit Dr.-Ing. Phillip Utsch, Gründer und Geschäftsführer der HPL Technologies GmbH, und Prof. Johannes Henrich Schleifenbaum, HPL-Gründer und Institutsleiter „Digital Additive Production“ an der RWTH Aachen, über das zukunftsfähige Bremssystem – und welche Rolle dabei Beschichtungen spielen.
VDI-Z: Sehr geehrter Herr Doktor Utsch, die Euro-7-Abgasnorm ist in aller Munde und soll ab Juli 2025 in Kraft treten. Was steckt drin im Regelwerk der neuen Abgasnorm?
Utsch: Die Euro-7-Norm ist die zukünftige Abgas- und Emissionsregulation, die für Pkw voraussichtlich zum 1. Juli 2025 eingeführt wird. Im Gegensatz zum aktuellen Regulationsstandard Euro 6 sollen nach dem gerade erst veröffentlichten EU-Entwurf nicht nur die Emissionen von Verbrennungsmotoren, sondern nun auch der Abrieb von Bremsen und Reifen reguliert werden. Im Entwurf kann man nachlesen, dass in diesem Bereich die stärksten Veränderungen vorgenommen werden. Tatsächlich werden die Abgas-Emissionsgrenzen dabei nur moderat gesenkt, die Neuerungen sind vor allem in der Bremse und bei den Reifen zu sehen. Das ist eine Besonderheit, die die Automobilindustrie nun auch jenseits des Verbrennungsmotors vor Herausforderungen stellt.
Das müssen Sie ein wenig näher erläutern. Worin besteht diese neue Herausforderung für Fahrzeughersteller?
Utsch: Das Auto wird nun, aus meiner Sicht sinnvollerweise, als Ganzes betrachtet und somit auch die gesamten Fahrzeugemissionen in den Blick genommen. Denn Stand heute emittiert ein Pkw im standardisierten WLTP-Fahrzyklus – je nach Fahrzeug – etwa zwischen 5 und 40 Milligramm Feinstaub je Kilometer. Gemessen werden in diesem Fahrzyklus Partikel mit einer Größe kleiner 10 Mikrometer, die als PM10 bezeichnet werden. Im Euro-7-Entwurf ist die Obergrenze auf nur noch 7 Milligramm PM10 je Kilometer und Fahrzeug abgesenkt – und zwar völlig unabhängig von der Fahrzeuggröße. Egal ob Klein- oder Premiumfahrzeug: Mehr Feinstaubpartikel dürfen es nicht sein.

Dr.-Ing. Phillip Utsch (links), Gründer und Geschäftsführer der HPL Technologies GmbH, und Prof. Johannes Henrich Schleifenbaum, Professor an der RWTH Aachen, arbeiten mit Leidenschaft am Thema der Optimierung von Bremsscheiben.
Foto: HPL Technologies
Schleifenbaum: Das Ende des Verbrennungsmotors ist politisch gewollt und regulativ vorgeschrieben. Da beißt die Maus keinen Faden ab. Hier wird es also einen längeren Zeitraum des Auslaufens geben, in dem Verbrennungsmotoren nach alten Abgasnormen selbstverständlich weiter betrieben werden können. Aber die EU-Kommission geht nun den logischen Schritt mit dem Euro-7-Entwurf, um neben dem Abgas die weiteren, mittlerweile sogar dominanten Emissionsquellen an Fahrzeugen in den Griff zu bekommen: Die Emission von Mikroplastik und Feinstaub von Reifen und Bremsen. Und diese Quellen sind nur bedingt davon abhängig, welches Antriebskonzept das Fahrzeug hat.
Inwiefern ist Feinstaub denn überhaupt ein Problem? Was macht ihn gesundheits- und umweltschädlich?
Schleifenbaum: Wir diskutieren aktuell täglich über CO2-Emission und die Auswirkungen auf den Klimawandel. Und das ist auch richtig so. CO2 wirkt global in der Atmosphäre – egal wo es emittiert wird. Also brauchen wir auch globale Antworten. Beim Feinstaub sieht es anders aus. Er wirkt vorwiegend lokal und schädigt damit Mensch und Umwelt insbesondere in der direkten Umgebung der Emissionsquelle: An Kreuzungen, dicht befahrenen Straßen oder U-Bahnstationen sind wir also besonders gefährdet, Feinstaub einzuatmen. Wenn Sie mich ganz persönlich fragen, ist die Diskussion um einen unteren Grenzwert ohnehin müßig, denn jeder lungengängige Feinstaub ist potentiell gesundheitsschädlich.
Utsch: Die EU (Europäische Union) hat in ihrer Begründung zur neuen EURO-7-Norm von ca. 300.000 frühzeitigen Todesfällen durch Feinstaubbelastung in Europa geschrieben. Das Deutsche Ärzteblatt zitierte dieses Jahr eine US-Studie, die im Jahr 2019 weltweit 1,8 Millionen frühzeitige Todesfälle durch Luftverschmutzung belegt. In besonders feinstaubbelasteten Regionen wurde sogar eine erhöhte Corona-Mortalitätsrate nachgewiesen. Feinstaub ist ein ernstes Thema. Dieses Thema konsequent anzupacken, erscheint uns mit Blick auf eine nachhaltigere Mobilitätsentwicklung unumgänglich.
„Nehmen Sie uns einmal mit“, und zwar an eine der Quellen des Feinstaubs: die Bremse. Wie können Emissionen im Bremssystem eines Fahrzeuges denn überhaupt eingespart werden?
Schleifenbaum: Es ist nun mal so: Beim Bremsen entsteht Abrieb von der Bremsscheibe und vom Bremsbelag und damit auch Feinstaub. Und wir können natürlich jetzt nicht ohne Bremsen durch die Gegend fahren. Wir verlassen uns zurecht seit gut 70 Jahren auf die Bremsscheibe, wie wir sie heute kennen.

Die Bremsscheibe, wie sie seit langem bekannt ist, muss zeitnah optimiert werden. Das Ziel lautet, die Feinstaubemission an der Bremse zu reduzieren.
Foto: HPL Technologies
So einfach eine Bremsscheibe mit Bremssattel und Bremsbelägen aussehen mag, so hochgradig komplex ist das System im Detail. Dabei ist es als sicherheitskritisches Bauteil umfangreichen Auslegungen, Tests und Freigabeprozeduren unterworfen. Weiterentwicklungen an diesem System sind daher immer aufwendig – aber eben auch nicht unmöglich. Im Gegenteil, es gilt, das System zu verstehen, beide Reibpartner zu betrachten und zu innovieren: Bremsscheibe und Bremsbelag. Ihr Zusammenwirken und der damit verbundene Verschleiß verzögert unsere Fahrzeuge in atemberaubender Geschwindigkeit – die meisten haben das schon einmal bei einer, hoffentlich seltenen, Vollbremsung erlebt – und erzeugt gleichzeitig den Bremsstaub. Betrachtet man beide Partner, kann man verschiedene Möglichkeiten analysieren, die Feinstaubemission an der Bremse zu reduzieren. Und diese Möglichkeiten kann man bewerten: Welche sind effektiv? Welche sind wirtschaftlich? Und welche sind vielleicht sogar beides?
Sie beschäftigen sich mit der Entwicklung und der Produktion von Bremssystemen. Welche Möglichkeiten werden denn diskutiert?
Schleifenbaum: In den letzten Monaten habe ich mitunter von Bremsstaubfiltern und Absaugmechanismen als mögliche Lösung gelesen. Unseres Wissens nach ist eine flächendeckende Erreichung der genannten Feinstaubgrenzwerte damit nur schwer möglich. Es werden nur Teile der Emissionen „abgesaugt“. Zudem müsste der Fahrzeughersteller zusätzlichen Bauraum, höhere ungefederte Massen und direkte Zusatzkosten in Kauf nehmen. Und die liegen laut Herstellerangaben bei einigen Hundert Euro je Fahrzeug. Hinzu kommt, dass auch für den Kunden ein solches System durch Filtertausch und Entleerung anstrengend ist – nicht nur aber auch wegen der Entsorgungskosten. Am meisten aber stört mich als Ingenieur: Das Problem der Emission wird damit nicht „an der Wurzel gepackt“. Die Emissionen werden nicht in der Entstehung vermieden. Deshalb werden sich diese Lösungen, jedenfalls aus meiner Sicht, technisch wohl kaum durchsetzen.
Utsch: Das denke ich auch. Eine andere Lösung wird aber unter Bremsenexperten tatsächlich immer wieder diskutiert: Man könnte die in Europa eingesetzten ECE-Bremsbeläge durch die in den USA eingesetzten NAO-Beläge zu ersetzen. Das erscheint erst einmal sinnvoll, da diese „Non-Aspestos-Organic“-Beläge unter bestimmten Randbedingungen tatsächlich einen geringeren Abrieb verursachen. Allerdings würde man damit das in Europa gewünschte, dynamische Bremsverhalten verlieren. Es ist fraglich, ob ein europäischer Kunden das so akzeptieren würde?
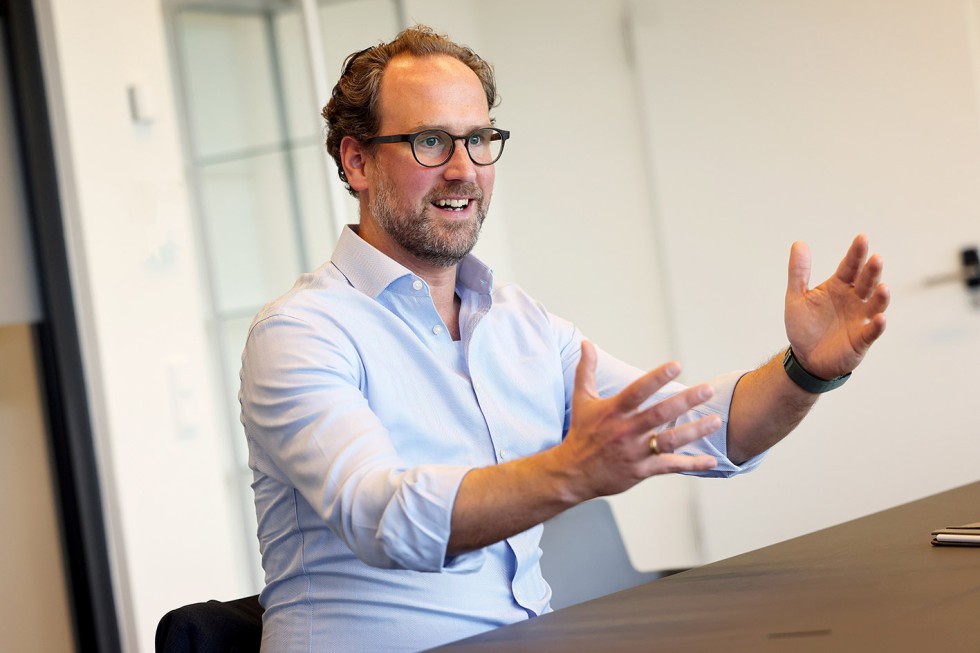
Dr.-Ing. Tobias Phillip Utsch hat sich in seinem Unternehmen der Optimierung von Bremsscheiben verschrieben und hierfür „Wecodur“ entwickelt.
Foto: HPL Technologies
Aber grundsätzlich sind die NAO-Bremsbeläge ein möglicher Baustein zur Lösung? Wurde dies auch schon im Hinblick auf Euro-7 überprüft?
Utsch: Ja, wir haben das mit unseren Entwicklungspartnern getestet. Mit so einem Bremsbelag und in Kombination mit dem in den USA verbreiteten Korrosionsschutzverfahren Nitrokarburieren, eine Art Wärmebehandlung in besonderer Atmosphäre, kurz FNC, wurden die Grenzwerte zumindest bei einem Kleinstfahrzeug gerade so erreicht. Allerdings auch nur mit einer fabrikneuen Bremsscheibe. Aufgrund der Oberflächeneigenschaften und der begrenzten Eindringtiefe des FNC ist jedoch zu erwarten, dass der scheibenseitige Abrieb nach kurzer Zeit deutlich ansteigt und die Emissionen wieder auf das Niveau von heute ansteigen. Damit wäre dann auch die Fahrzeughomologation gefährdet. Und die Einführung des äußerst ressourcenintensiven Herstellungsprozesses wäre auch aus Gründen des Umweltschutzes in Europa ohnehin fraglich.
In welcher Technologie sehen sie einen Ausweg für die Fahrzeughersteller?
Utsch: Neben den technisch-wirtschaftlich begrenzten Alternativen hat sich tatsächlich die mit Hartstoff beschichtete Bremsscheibe als effektivste und mittlerweile auch effizienteste Lösung durchgesetzt. Dabei wird eine konventionelle Bremsscheibe lediglich um eine zusätzliche Korrosions- und Verschleißschutzschicht auf der Reibfläche – zum Beispiel aus rostfreiem Stahl und Hartstoffpartikeln– veredelt. Das Prinzip der beschichteten Bremsscheibe gibt es zwar schon einige Jahre am Markt, war jedoch aufgrund einer enorm teuren und äußerst qualitätssensiblen Fertigungsfolge nur einer Nische von Premium-Sportfahrzeugen vorbehalten.
Das ist aber inzwischen nicht mehr so. In den letzten Jahren konnten wir ein innovatives Beschichtungsverfahren von der RWTH Aachen und Fraunhofer auf Bremsscheiben adaptieren und – sozusagen von der Wissenschaft auf die Straße – großserienfähig machen: Durch die Weiterentwicklung und Industrialisierung des Hochgeschwindigkeits-Laserauftragschweißprozesses können Bremsscheiben heute mit der „Wecodur“-Technologie reproduzierbar und damit skalierbar für die automobile Großserie wirtschaftlich beschichtet werden.
Wir testen die Wecodur-Ergebnisse derzeit „auf Herz und Nieren“. Je nach Schichtsystem, Bremsbelag und kinematischer Masse können wir bis zu 97 Prozent Bremsstaub reduzieren. Der Fahrzeughersteller erfüllt damit die vorgegebenen Emissionsregulation allein durch den Einsatz unserer hartstoffbeschichteten Bremsscheiben in Kombination mit einem darauf adaptierten Bremsbelag. Es sind keinerlei Veränderungen am Fahrzeug notwendig. Gleichzeitig bringt unsere Scheibe ein Leichtbaupotenzial mit, durch welches über 100 Gramm CO2 je 100 Kilometer eingespart werden kann.
Schleifenbaum: Damit wird das Problem also bei der Wurzel gepackt und die Emissionen an der Quelle reduziert.
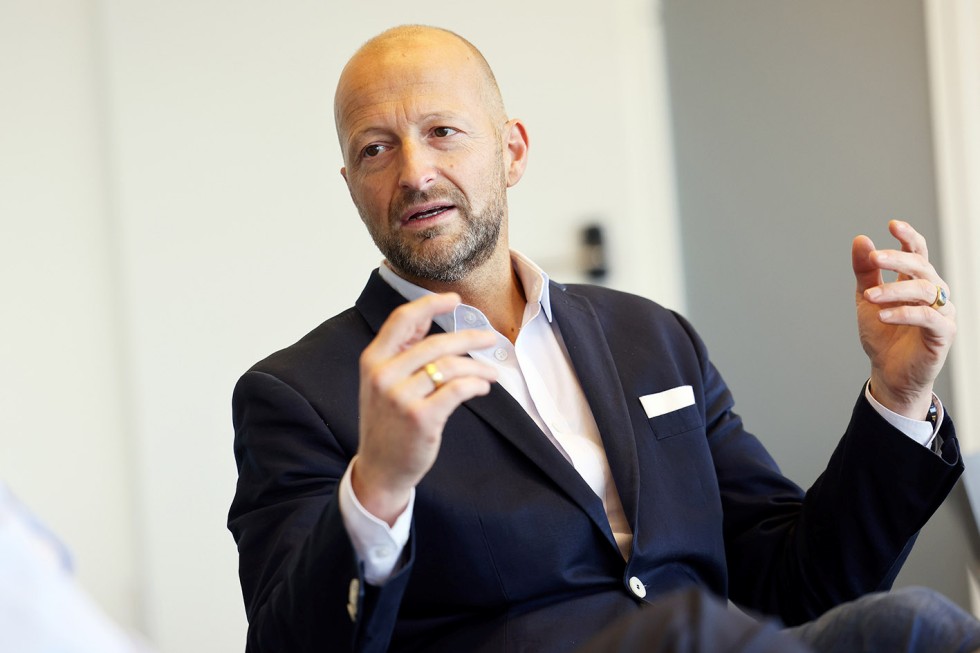
Prof. Johannes Henrich Schleifenbaum, HPL-Mitgründer, befasst sich an der RWTH Aachen mit der Entwicklung hochinnovativer Additive-Manufacturing-Verfahren.
Foto: HPL Technologies
Das klingt vielversprechend. Aber was bedeutet das für die Automobilindustrie? Was muss getan werden?
Schleifenbaum: In automobilen Entwicklungszyklen gedacht, kommt die Euro-7-Norm ja schon „übermorgen“. Das stellt ein echtes Risiko dar: Denn jedes Neufahrzeug, das ab dem Stichtag die Feinstaubregulation nicht erfüllt, kann nicht zugelassen werden. Für uns alle – Fahrzeughersteller wie Endkunden, die auf individuelle Mobilitätslösungen angewiesen sind – kein gutes Szenario, sondern ein echtes Risiko. Die Fahrzeughersteller müssen nun also zwei Dinge gleichzeitig tun: Einerseits müssen beschichtete Bremsscheiben und Bremsbeläge als tribologisches System – fahrzeugbezogen aufeinander abgestimmt – erprobt und homologiert werden. Mit Blick auf die Beschaffungs- und Anlaufzeiten für eine Serienproduktion muss aber auch andererseits die Produktionstechnik umgehend geplant, beschafft und aufgebaut werden. Und aufgrund der Neuheit des Produktionsverfahren ist die Qualität hier besonders gut abzusichern.
Utsch: Diese synchrone Entwicklung von neuem Produkt und neuer Produktionstechnologie stellt nicht nur eine große Herausforderung dar, sondern die beiden Stränge beeinflussen sich auch gegenseitig: Anders als bei der konventionellen Bremsscheibe üblich, ist die neue Beschichtungstechnologie kein zerspanendes, sondern ein urformendes, additives Verfahren. Das bedeutet, dass die Eigenschaften des Schichtsystems nicht nur durch das eingesetzte Material, sondern auch in hohem Maße durch diesen additiven Fertigungsprozess vorgegeben wird. Wenn man also nicht genau weiß, was man tut, werden die Schichteigenschaften verändert. Damit wird der frühzeitige und ungeplante Ausfall der Bremsscheiben riskiert. Das will man bei einem sicherheitskritischen Bauteil natürlich in jedem Fall vermeiden.
Das klingt aber nach einem großen Umsetzungsrisiko. Oder nicht?
Schleifenbaum: Ja. Und nein. Einerseits ist der Einfluss der Produktionstechnologie auf die Materialeigenschaften schon eine Herausforderung. Das ist eine hohe Eintrittsbarriere, auch für etablierte Maschinenlieferanten. Andererseits ist die Wecodur-Technologie hochgradig reproduzierbar, daran haben wir Jahre gearbeitet und massenhaft getestet Das heißt, wenn das Schichtsystem nun erprobt und freigefahren ist, kann es auch in Großserie stabil produziert werden. Voraussetzung dafür ist, dass die Material- und Technologieparameter der Beschichtung dieselben sind wie bei der Homologation.
Utsch: Um bei dieser Komplexität hier zu unterstützen, stellen wir der Automobilindustrie unsere mittlerweile tausendfach erprobten Schichtsysteme zur Verfügung. Gleichzeitig unterstützen wir bei der Skalierung der Produktion, indem unsere Beschichtungstechnologie und Qualitätssicherung in bestehende Systeme integriert und so hundertfach skaliert werden. Der Umsetzungszeitraum ist sicherlich nicht komfortabel im Hinblick auf 2025 – aber mit dem erarbeiteten Technologieniveau durchaus realistisch. Die nächsten zwei bis drei Jahre werden wohl äußerst dynamisch. Wir stehen bereit und sind gespannt, wie sich dieser Bereich entwickeln wird.
Über die Interviewpartner
Dr.-Ing. Tobias Phillip Utsch ist Mitgründer der HPL Technologies GmbH, die Wecodur® entwickelt hat. Er ist Maschinenbauingenieur und hat bei Fraunhofer und zwei führenden Maschinenherstellern für die internationale Automobilproduktion in Leitungspositionen gearbeitet, zuletzt sechs Jahre als Vorsitzender der Geschäftsführung. Seit 2020 ist Dr. Utsch als vollzeitlicher Geschäftsführer im eigenen Unternehmen tätig.
Prof. Johannes Henrich Schleifenbaum ist HPL-Mitgründer. Der Maschinenbauingenieur und Wirtschaftswissenschaftler ist Institutsleiter „Digital Additive Production DAP“ an der RWTH Aachen. Neben der Entwicklung hochinnovativer AM-Verfahren stehen beim DAP insbesondere die Produkt- und Produktions-Digitalisierung sowie die Entwicklung neuer Hochleistungsmaterialien für die additive Fertigung im Fokus der F&E Arbeiten.
Das könnte Sie auch interessieren:
Stanzteile für E-Motoren hartfräsen anstatt senkerodieren
Was das EU-Verbrenner-Aus für die Automobilproduktion bedeutet
Zuverlässige Qualitätsprüfung sicherheitsrelevanter Bremsscheiben