Echtzeit-Tracking und Ortung mit 5G
Viele Branchen stehen vor der Herausforderung, mit technologischen Innovationen Schritt zu halten. Sie müssen Abläufe und die Lieferkette digitalisieren und die gestiegenen Erwartungen an Geschwindigkeit und Genauigkeit erfüllen – dies betrifft auch die Automobilhersteller.
![[Category, Subcat or Product] Representational Image 16:9](https://www.ingenieur.de/wp-content/uploads/2023/08/auto-manufacturing-vision-study-16x9-3600-1.jpg)
In einer Studie wurden Stimmungen aus der Automobilindustrie abgefragt: Ein Drittel der befragten Entscheidungsträger meint, dass Radiofrequenz-Identifikation (RFID) das Lieferkettenmanagement verbessern wird. In den nächsten fünf Jahren wollen sie verstärkt auf die Verbindung von Echtzeit-Datensystemen setzen.
Foto: Zebra
Produzenten in Deutschland stellen vermehrt auf 5G um – und mit dem neuen Sendestandard eröffnen sich neuartige RTLS (Real-Time Locating System)-Möglichkeiten. RTLS ist eine Kombination aus speziellen Funk-Komponenten mit einer für die Verwendung in Echtzeit (real-time)-tauglichen Software, mit deren Hilfe über eine mehrfach wiederholte Laufzeitmessung die Orte von Objekten, Fahrzeugen oder Personen kontinuierlich bestimmt werden. Problematisch: Wenn zum Beispiel ein Meter Netzwerkkabel verlegt werden muss, kostet das mehr als tausend Euro pro Meter. Aber: Mit 5G gibt es jetzt viel weniger Infrastruktur bei gleichem Ergebnis.
Gute Nachrichten für Anwender aus dem Automobilsegment
Führungskräfte aus der Automobilindustrie sprechen oft darüber, 5G zu implementieren, wenn es darum geht, Herausforderungen in den Werken zu meistern. Während es bisher keinen „Goldstandard“ für RTLS gab, werden mit 5G gleich mehrere Technologien kombiniert und so die Regeln im gesamten Automobilbereich grundlegend neu geschrieben.
Eine Reihe von 5G-Netzen gibt es bereits, in die Unternehmen einsteigen können. Einige davon sind öffentlich und Unternehmen können dafür zahlen, über einen „Access Point Name“ (APN) einen Teil des Bandes nutzen zu dürfen. Dies ist entweder möglich in einem bestimmten Bereich einer Stadt, oder weil Pop-up-Events (wie ein Musikfestival), Geschäfte oder Logistik- und Notfalldienste bei Bedarf Zugang zu schneller Konnektivität benötigen.
Einige 5G-Netze sind spezifisch für ein Unternehmen eingerichtet. Diese sind oft wegen der Anzahl der Nutzer, der über das Netz übertragenen Datenmengen und der Datenschutz- und Sicherheitsbedenken erforderlich.
Wie sind die Zukunftsprognosen?
Mit 5G können Unternehmen in der Automobilindustrie viel Geld sparen, da sie weniger Access Points für die verschiedenen Technologien benötigen, die sie einsetzen wollen: wie RTLS, industrielle Bildverarbeitung, Roboterautomatisierung und mehr. 5G ermöglicht die gleichzeitige Verbindung zu mehreren Geräten und Sensoren und kann so riesige Datenmengen erzeugen, die von Anwendungen in der Cloud oder über Edge Computing verarbeitet werden können.
5G wird in Unternehmen zur Entwicklung einer nahtlosen IoT (Internet-of-Things)-Umgebung am Arbeitsplatz führen, die eine sektorübergreifende Echtzeit-Zusammenarbeit zwischen Menschen und Geräten unterstützt.
Tatsächlich glauben 35 Prozent der OEMs, die an der „Automotive Ecosystem Vision Study“ von Zebra teilgenommen haben, dass Radiofrequenz-Identifikation (RFID) das Lieferkettenmanagement verbessern wird. Fast ein Drittel aller befragten Entscheidungsträger gibt an, sie werden in den nächsten fünf Jahren verstärkt auf die Verbindung von Echtzeit-Datensystemen setzen. Diese ermöglichen eine ganzheitliche Sicht auf die Abläufe und erhöhen die Transparenz der Produktion und der gesamten Lieferkette.
Das weltweit tätige Unternehmen Zebra, das die Studie durchgeführt hat, ist führend bei Geräten für Mobile Computing, Datenerfassung, Barcode-Druck und RFID für Unternehmen. Mehr als 8.800 Mitarbeiter unterstützen Kunden in über 170 Ländern. Die Standorte in Deutschland sind Berlin, Offenbach und Ratingen.
Anwendungen aus der Industrie zeigen den Nutzen
Ein Praxisbeispiel: Toyota Material Handling musste sicherstellen, dass die Produkte ohne Unterbrechung oder Verzögerung von Punkt A nach Punkt B gelangen, um so die Produktionsquoten von 180 Flurförderzeugen, Gabelstapler und Hubwagen pro Tag zu erfüllen. Das Unternehmen konnte durch die Installation einer MotionWorks-Lösung, die vorhandenen Anwendungsprogrammschnittstellen (APIs), mehr als 400 Ultrabreitband-Tags und 60 RFID-Sensoren die Analyse des Produktflusses automatisieren und die Reaktionszeiten bei Ausreißern verbessern. So konnten Unterbrechungen oder Verzögerungen in der Produktion und bei der Auslieferung vermieden werden. Außerdem hat die Echtzeit-Überwachung der Produktbewegungen geholfen, die Produktivität der Mitarbeiter zu steigern, Arbeitsabläufe zu rationalisieren und die Erwartungen der Kunden zu erfüllen.
Ein anderer großer Automobilhersteller setzte einen Logistikmitarbeiter ein, um Fahrzeuge manuell zurückzuverfolgen, manchmal unter Verwendung einer Excel-Tabelle. Dadurch war der Prozess sehr langsam und fehleranfällig. Durch die Implementierung einer Lösung aus RFID-Druckern, mobilen Computern und fest installierten RFID-Lesegeräten konnte der Hersteller die Betriebskosten senken und Einsparungen erzielen. Er konnte die Ressourcenzuweisung um 50 Prozent verbessern und die Zahl der unfreiwilligen und menschlichen Fehler um 10 Prozent reduzieren.
Welche Technologie ist am besten geeignet?
Es geht nun darum, herauszufinden, welches RTLS am besten geeignet ist – vor allem, wenn Faktoren wie die Anforderungen an die Konnektivität und die dazugehörige Infrastruktur mit einbezogen werden. Zu den RTLS-Systemen gehören sogenannte „aktive“ Transponder-Etiketten, die mithilfe der „Spread-Spectrum-Technologie“ regelmäßige Signale mit einer Reichweite von 1000+ Metern gemäß ISO/IEC 24730–2 senden. Ortungssensoren empfangen und verarbeiten die Tag-Signale, und ein Ortungsgerät sammelt und korreliert die Daten.
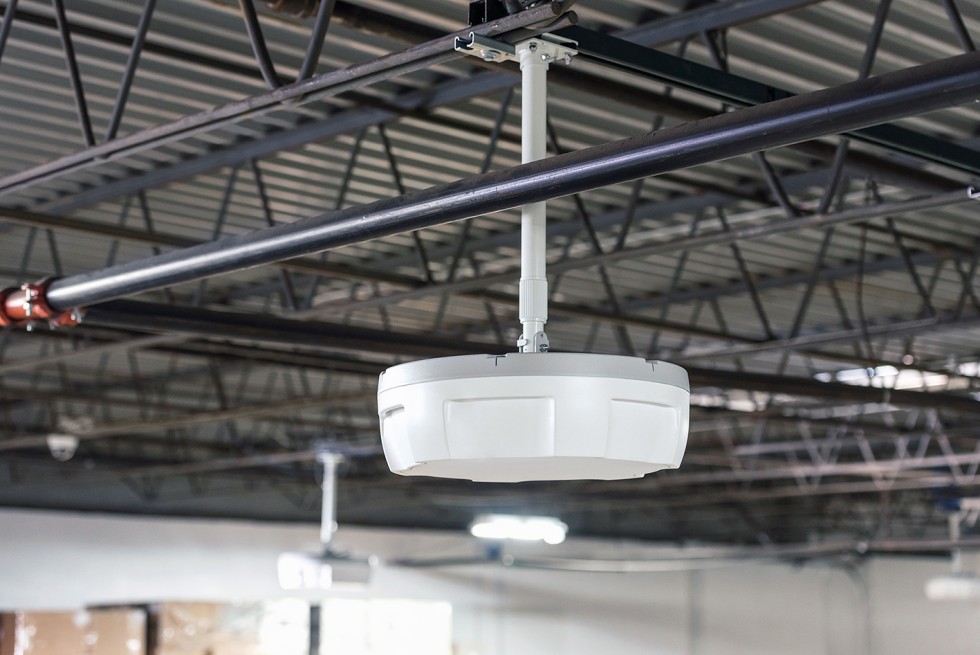
Durch kombinierte Lösungen aus RFID-Druckern, mobilen Computern und fest installierten RFID-Lesegeräten wie dem „ATR7000“ können (Automobil)Hersteller die Betriebskosten senken und Einsparungen erzielen.
Foto: Zebra
Eine Lösung besteht aus drei primären Ebenen. Die erste ist die physische Ebene, die die Tags und die Empfänger umfasst. Diese greifbaren Komponenten speisen die Daten in die zweite, die grundlegende Geschäftsprozessebene ein. Dabei handelt es sich um eine Softwareanwendung innerhalb des breit angelegten ERP (Enterprise Resource Planning)-Systems, die eine oder mehrere Funktionen übernimmt. Sie stellt Standortinformationen zu den Anlagen bereit oder verwaltet den Materialflusses in einer Produktionsumgebung.
Die dritte und letzte Ebene ist die anschließende Analyse der Geschäftsprozesse. Sie ergibt sich aus den Erkenntnissen, die aus der vorangegangenen Geschäftsprozessebene gewonnen wurden. Im Wesentlichen stellen Unternehmen fest, dass sie durch die Nutzung der Daten aus der Plattform für Standortlösungen, fundiertere Entscheidungen treffen und Maßnahmen zur Geschäftsoptimierung ergreifen können.
Außerdem werden Netzwerke mit geringer Latenz für SPS-gesteuerte Umgebungen, wie z. B. Fertigungsstraßen, verwendet. Ihre ultrahohe Bandbreite wird für industrielle Bildverarbeitung und videobasierte Anwendungen genutzt. Weiterer Vorteil: Der User erhält garantierte Antwortzeiten. Das ist ebenfalls sehr wichtig, wenn man mit SPS-gesteuerten Umgebungen arbeitet, da viel mehr Clients pro Access Point erhalten werden, einschließlich derer, die für RTLS relevant sind.
Außerdem bieten immer mehr Dienstanbieter eigenständige/private 5G-Netze an. Die sind sehr wertvoll, da sie in der Automobilindustrie Sicherheit und Zuverlässigkeit bieten. Eine konsistente Netzwerkkonnektivität ist der Schlüssel zur Wertschöpfung, die durch RTLS gewonnen wird.
Die Betriebsbandbreite mit dem richtigen Ansatz erhöhen
Um die Möglichkeiten von RTLS für eine Fabrik oder ein Werk zu nutzen, ist zu Beginn eine aufwendige Planungs- und Implementierungsphase nötig, die nicht unterschätzt werden sollte. Auch wenn der Aufwand viel geringer ist als noch in der Vergangenheit: Unternehmer müssen sicherstellen, dass sie dieses Projekt – basierend auf klar definierten Anforderungen – einteilen und gestalten.
Dies mag als erster Schritt selbstverständlich erscheinen. Es gibt jedoch viele Projekte, bei denen der Kunde eine anfängliche Vorstellung davon hat, wie er die Ortungstechnologie nutzen möchte. Im weiteren Verlauf vergrößert sich dann aber der Umfang, warum auch immer, und das Projekt wird unübersichtlich und sehr teuer. Wenn der Systementwurf und der Implementierungsansatz nicht genau definiert sind, wird es zudem schwieriger, die Beteiligten zum „Mitmachen“ zu bewegen. Daher ist es wichtig, zu Beginn der Entwurfsphase wirklich sicherzustellen, dass die geplante Technologie in ihrer Umgebung und für den speziellen Anwendungsfall funktioniert.
Pilotprojekte zeigen Übertragbarkeit
Ebenso wichtig ist es, dass das Pilotprojekt unter kontrollierten Bedingungen – und vorzugsweise in einer bestimmten Anlage – durchgeführt wird. Wenn das Unternehmen sich vergewissert hat, dass die Technologie für den angestrebten Prozess geeignet ist oder das Problem behebt, das zuvor den Betrieb behindert hat, wird die Übertragung der Technologie auf andere Anlagen einfacher.
Wenn die Technologie jedoch nicht wie gewünscht funktioniert oder schwer zu skalieren ist, müssen das System oder die Strategie nur an einer Stelle angepasst werden. Das ist weniger riskant. Um erfolgreich zu sein, sind Projekte im Hinblick auf die Skalierung auf andere Geschäftsbereiche oder Anlagen gut zu durchdenken – selbst wenn es sich im Wesentlichen um denselben Prozess handelt, der nur repliziert wird. Daher ist es wichtig, mit einem vertrauenswürdigen Team von Lösungsingenieuren und Technologieintegratoren zusammenzuarbeiten, das durch die Prozesse der Entwicklung, des Entwurfs, der Bereitstellung, der Verfeinerung und der Skalierung führen kann.
Das könnte Sie auch interessieren:
KI-basierte Symbol- und Texterkennung zur Automatisierung der Arbeitsplanung
Perfekte Technologie für Schweißprozesse an gebauten Rotorwellen
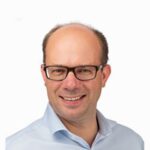
Stephan Pottel ist „Practice Lead“, Bereich Fertigung, bei Zebra Technologies. Foto: Zebra