Fahrzeugbau: Energieeffizienz steigern dank Gewichtsreduktion
Mit Blick auf die globalen Entwicklungen in der Automobilindustrie zeigt sich: Bei neuen Personenkraftwagen und leichten Nutzfahrzeugen in Europa ist die Masse in den zurückliegenden Jahren permanent gestiegen: von circa 1.268 kg im Jahr 2000 über 1.360 kg im Jahr 2010 auf etwa 1.420 kg im Jahr 2020. Doch wie lässt sich gegensteuern?
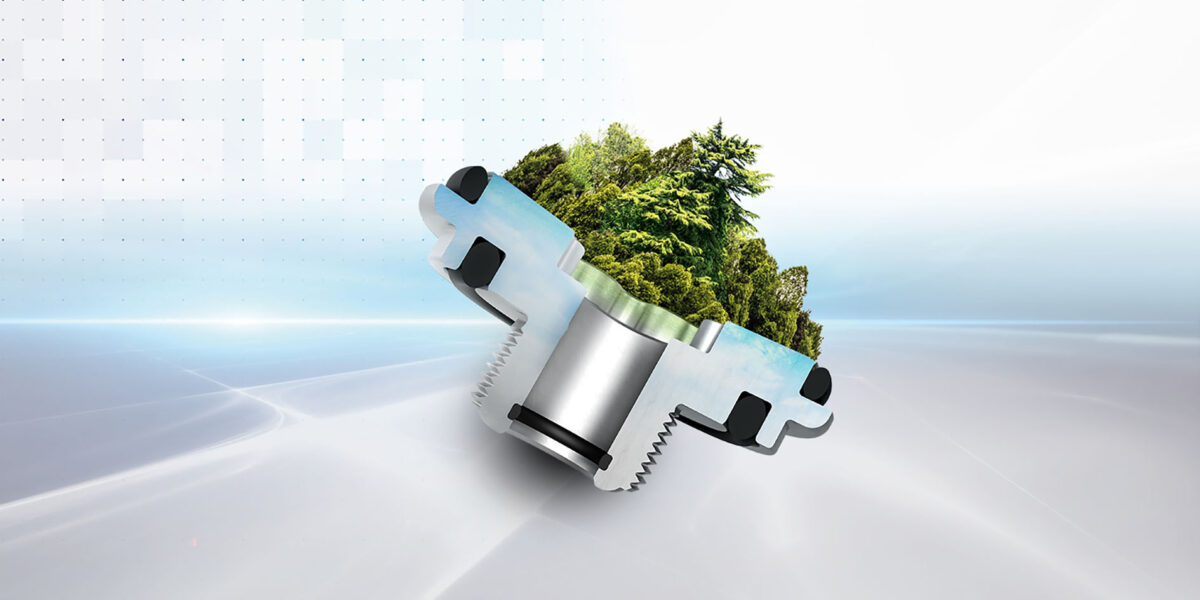
Durch "ACO2-Save" und den damit einhergehenden Wechsel der Produktionstechnologie ließen sich deutliche Einsparungen erzielen: Die CO2-Emissionen, die durch diese Schraube bei der Produktion entstehen, wurden um 45 Prozent gesenkt. Grafik: Arnold Umformtechnik
Durch die Entwicklung hin zu mehr Hybrid- & Elektrofahrzeugen wird sich die skizzierte Entwicklung eher noch verstärken, wiegt doch ein Elektrofahrzeug alleine aufgrund des Gewichts der Batterie im Durchschnitt 300 Kilogramm mehr als ein Fahrzeug mit herkömmlichem Motor. Mithilfe der Optimierung des Kraftstoffverbrauchs sowie Innovationen in neue Antriebskonzepte konnte zwar bereits eine deutliche Reduktion der CO2-Emissionen erreicht werden – von etwa 175 g CO2/km im Jahr 2000 auf 140 g CO2/km im Jahr 2010 und 95 g CO2/km im Jahr 2020. Dieser Trend muss sich in den nächsten Jahren jedoch fortsetzen, wenn die Klimaschutzziele der nächsten Jahre erreicht werden sollen.
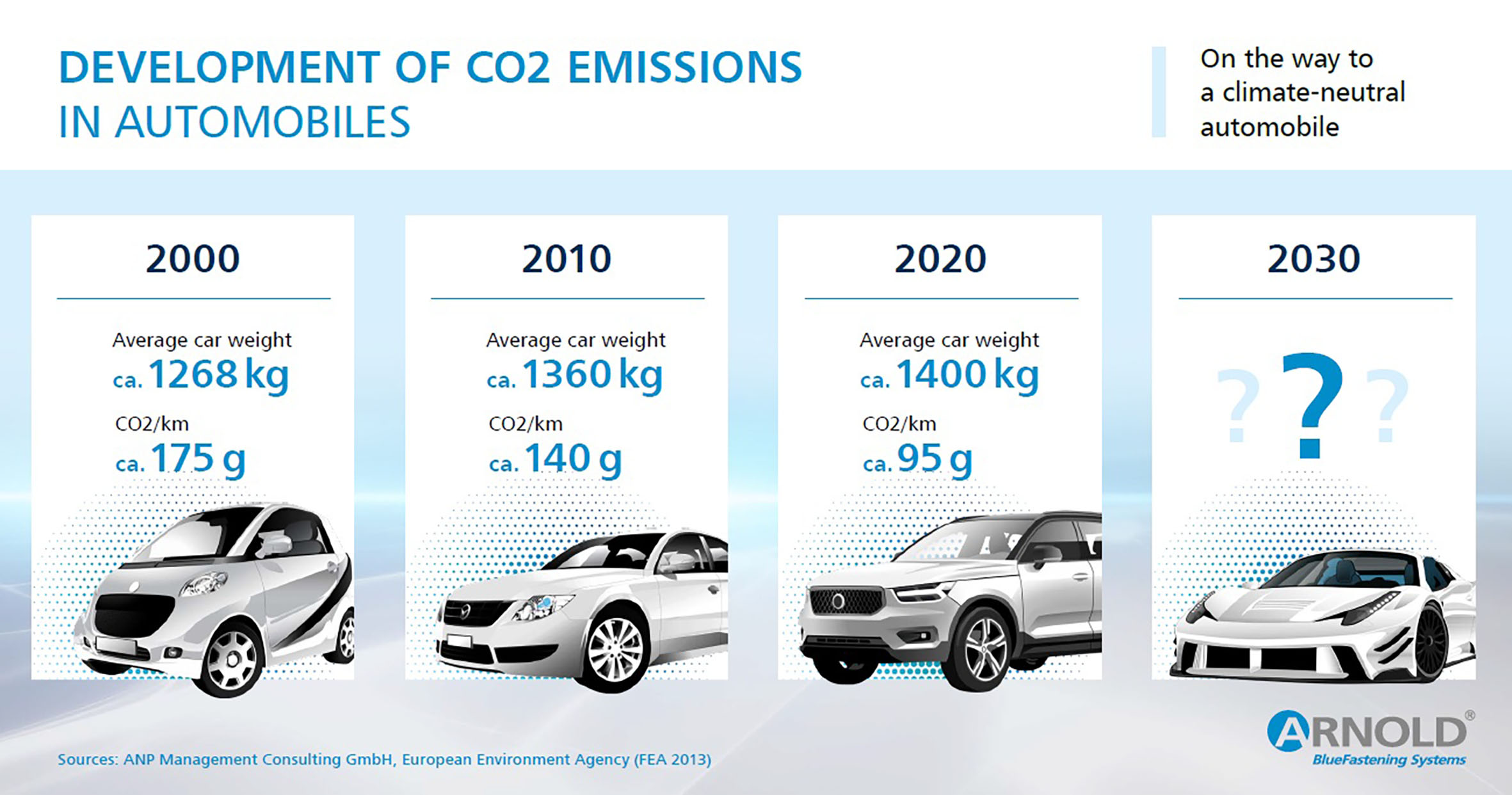
Trotz steigendem Fahrzeuggewicht müssen die CO2-Emissionen der Pkw in Europa weiter reduziert werden, um die proklamierten Klimaschutzziele zu erreichen. Grafik: Arnold Umformtechnik
Nachhaltigkeitsziele über die komplette Wertschöpfungskette betrachten
Zur Erreichung der geforderten Ziele möchte auch die deutsche Industrie beitragen. So hat das Thema Nachhaltigkeit zum Beispiel für die Arnold Group aus Forchtenberg-Ernsbach eine große Bedeutung. Neben E-Mobility, Internationalisierung, Lightweight-Engineering und Digitalisierung zählt es zu den fünf definierten strategischen Stoßrichtungen des Verbindungselemente-Herstellers. Die Arnold-Gruppe ist eine 100-prozentige Tochter des global agierenden Würth-Konzerns, der mit über 65.000 Mitarbeitern und mit 420 Gesellschaften weltweit über 8 Milliarden Euro erwirtschaftet.
Die Experten des Unternehmens wissen: Über eine komplette Wertschöpfungskette hinweg betrachtet, entsteht für jedes Produkt ein individueller Footprint. Die Emissionen der Lieferketten-Mitglieder werden dabei aufsummiert. Das bedeutet, dass Unternehmen, welche in der Lieferkette nachgelagert sind, über die bezogenen Produkte und Leistungen die Emissionen ihrer Lieferanten übernehmen. Diese geben sie dann – mit den eigenen CO2-Ausstößen aufaddiert – an ihre Kunden weiter.
Vielfältige Möglichkeiten für CO2-Einsparungen
Vor diesem Hintergrund hat Arnold Umformtechnik die Initiative „ACO2-Save“ ins Leben gerufen (das A steht hierbei für Arnold.) Dabei werden Kunden aktiv bei der Reduktion von CO2-Emissionen unterstützt, indem Verbindungselemente und Kaltumformteile nachhaltig ausgelegt und angewendet werden.
So startet eine begleitende CO2-Kalkulation bereits im Entwicklungsprozess. Mit einem eigens entwickelten CO2-Kalkulator kann der sogenannte Product Carbon Footprint für das bei Arnold angefragte Teil ermittelt und dann gemeinsam eine Optimierung durchgeführt werden. Ziel dabei ist, am Ende des Entwicklungsprozesses ein technisch hochwertiges Produkt zu erhalten, das sowohl kosten- als auch CO2-optimiert ist. Gestaltungsbausteine sind dabei: ein CO2-optimiertes Engineering durch digitale Prognosetools, die Analyse der CO2-Optimierung durch einen möglichen Wechsel der Produktionstechnologie oder einen Wechsel der Verbindungstechnik sowie der Einsatz innovativer Verbindungselemente oder -systeme.
Dass genau dieser ACO2-Save-Ansatz funktioniert, belegt ein Beispiel: Eine Sonderschraube aus Aluminium mit einem Volumen von 8.733 mm3 und einer Masse von 23,58 Gramm pro Stück wurde bisher traditionell spanabhebend hergestellt. Zur Produktion wurde ein Drehteilrohling verwendet, der ein Ausgangsvolumen von 25.630 mm³ und 69,2 Gramm pro Stück hatte. Durch eine ACO2-Save-Analyse konnte dieses Teil auf ein Umformteil der Produktreihe „Conform Next“ umgestellt werden. Das Resultat: Nach der Optimierung hat der Umformrohling gerade noch ein Volumen von 9.135 mm³ und 24.82 Gramm pro Stück. Neben einer erheblichen Kostenoptimierung, die durch den geringeren Materialeinsatz beim Kaltumformen entsteht, hat dies einen erheblichen Einfluss auf den Product Carbon Footprint der Sonderschraube.
Das könnte Sie auch interessieren:
Intelligente Technologiekette optimiert das Nachbearbeiten additiv gefertigter Bauteile
Karosseriebearbeitung: Fehlstellen erkennen und zuverlässig beseitigen
Dipl.-Ing. Annedore Bose-Munde ist Fachredakteurin für Wirtschaft und Technik in Erfurt.