Künstliche Intelligenz zieht in die Fertigungshallen ein
Seit einiger Zeit ist Künstliche Intelligenz „in aller Munde“; doch was kann sie wirklich? Beispielhaft wird dies an drei Praxisfällen aus der industriellen Produktion gezeigt.
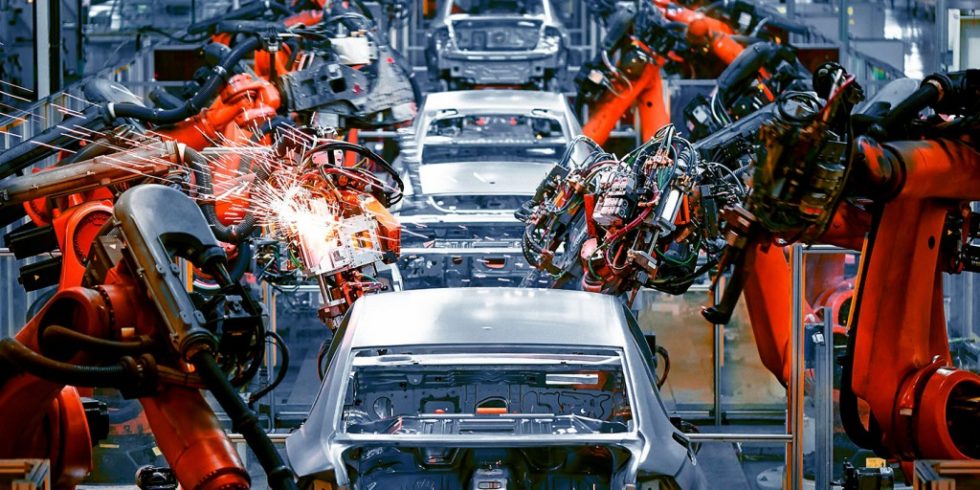
Wie lässt sich die Produktionsqualität von Automobilherstellern und -zulieferern zu verbessern? Betrachtet werden drei Fallbeispiele, in denen sich der Einsatz von Künstlicher Intelligenz bewährt hat.
Foto: iStock
Es geht in den betrachteten Szenarien immer darum, die Produktionsqualität von Automobilherstellern beziehungsweise deren Zulieferern zu verbessern. Hierbei werden unterschiedliche analytische Fragestellungen betrachtet: Einerseits die Bewertung hochfrequenter Produktionsschritte, andererseits die Prognose, welche Qualität erreicht werden kann, um ggf. den Produktionsschritt abzubrechen. Dies macht dann Sinn, wenn mit hoher Sicherheit Ausschuss entstehen wird. Der dritte Aspekt ist die komplexe Ursachenfindung, warum Minderqualität entsteht. Gerade in variantenreichen Produktionsprozessen ist das Aufdecken der verwobenen Störfaktoren ein hoch-komplexes Thema.
Fallbeispiel 1: Automatisierte Qualitätsbewertung kritischer Produktionsschritte
Die Ausgangssituation ist folgende: Das Werk eines Automobilzulieferers stellt in Stückzahlen von bis zu 600 Hüben pro Minute Metallkomponenten her. Diese werden verformt (pressen oder stanzen) und verbunden (löten, kleben, schweißen oder schrauben).
Selbstverständlich ist jeder Prozessschritt wichtig für die Stabilität und Qualität der Autokomponenten, jedoch ist es aufgrund der hohen Stückzahl nicht möglich, alle kritischen Arbeiten zu überprüfen. Daher werden Stichproben durchgeführt, beispielsweise bei Schweißungen kleiner 1 Prozent, da diese mit Ultraschalltechnik überprüft werden. Ultraschalltechnik erfordert einerseits entsprechend teure Investitionen in Prüfanlagen, aber auch stets zertifiziertes Prüfpersonal. Die Prüfungen sind außerdem zu zeitintensiv, als dass sie auf alle Schweißungen angewendet werden können.
Projektbeschreibung und Lösungsansatz
Mit diesem Datenanalysevorgehen hat der internationale Automobilzulieferer die Intention, etwaige Mängel direkt am Produktionsschritt zu erkennen und daher eine 100%ige Prüfung durchzuführen. Die Künstliche Intelligenz bewertet die Daten jedes einzelnen Produktionsschrittes, sodass auftretende Mängel behoben beziehungsweise die entsprechenden Komponenten direkt aussortiert werden können.
Selbstlernende Künstliche-Intelligenz-Lösungen wurden auf Produktionsdaten trainiert. Aufgrund der hohen Variantenkomplexität lagen jedoch nur vergleichsweise wenige Schlechtfälle vor. Die Algorithmik muss entsprechend abstrahieren, um trotz mangelnder Datenlage verlässliche Qualitätsbewertungen durchführen zu können.
Zu Beginn wurden noch Schweißungen aussortiert, die nicht genau bewertet werden konnten. Diese wurden durch die „Ultraschaller“ geprüft, deren Rückmeldung wiederum das kontinuierliche Lernen der Künstlichen Intelligenz unterstützte. So wurden die „Graufälle“ immer geringer bei gleichzeitiger Prüfabdeckung zu 100 Prozent.
Fallbeispiel 2: Zukünftige Qualität prognostizieren
Ausgangssituation: Im Werk eines internationalen Automobilzulieferers laufen viele Produktionsschritte automatisiert; so auch die Bearbeitung von Einspritzdüsen mithilfe von Spindeln. Es gibt knapp 20 dieser Zerspanungsmaschinen für diesen Produktionsschritt. Obwohl diese Maschinen alle das Gleiche tun, die gleichen Werkzeuge nutzen, gleich eingestellt sind, das gleiche Material des gleichen Lieferanten nutzen, usw., kommt es doch vor, dass – manchmal – die eine und manchmal die andere Maschine schlechtere Qualität erzeugt.
Maschinendaten erfassen und auswerten
Zuerst wurden Sensoren an die Zerspanungsanlagen angebracht, um Vibration, Temperatur, …. zu messen. Die Maschinendaten wurden über einen Zeitraum aufgenommen inklusive der Qualitätsbewertung, ob das Bauteil gute Qualität hat. Hierbei wurden 11 Qualitätskennzahlen bewertet wie Rauheit, Genauigkeit, Profiltiefe, …
Künstliche Intelligenz-Verfahren wurden auf die Daten angewendet, um verlässliche Muster zu erkennen, die zu schlechter Qualität führen. Prognose-Algorithmen sagten etwa nach der Hälfte der jeweiligen Führungsspindel- und Unterstützungsspindel-Bearbeitung die Werte der entsprechenden Qualitätskennzahlen voraus.
Lösung liefert stabile Vorhersagen auch bei Prozessveränderungen
Selbstlernende Künstliche-Intelligenz-Lösungen wurden auf einem Teil der Daten antrainiert. Es wurden versteckte und vielschichtige Datenmuster aufgedeckt, um automatisiert stabile Vorhersagen treffen zu können, welchen Wert die jeweilige Qualitätskennzahl erreichen wird.
Die antrainierten Algorithmen wurden auf unbekannten Daten – also Daten, die nicht für das Trainieren genommen wurden – angewendet. Erst dies zeigt, ob die Datenmuster auch korrekt aufgedeckt werden konnten. Bei Prozessveränderungen passt die Selbstlernalgorithmik eigenständig das Prognosemodell an, sodass kein Data Scientist einschreiten muss.
Fallbeispiel 3: Komplexe Ursachen für Minderqualität im Produktionsprozess aufdecken
Die Ausgangssituation im dritten Projekt lautet: Das Werk eines internationalen Automobilzulieferers produziert ca. 11.000 Automobilteile täglich, in 700 Varianten. Jedes Produkt, das aus bis zu 600 Teilen besteht, durchläuft einen technischen 100-Prozent-Test, bevor es ausgeliefert wird.
Obwohl während des Produktionsprozesses kritische Schritte immer wieder überprüft werden und nur die Komponenten weiter bearbeitet werden, die in der Spezifikation sind, wird bei der Endkontrolle Ausschuss aufgedeckt. Es galt also, im Ende-zu-Ende-Produktionsprozess die Gründe für die Minderqualität aufzudecken.
Eine riesige Datenmenge gilt es zu bewältigen
Terabyte an Daten standen für die Analyse zur Verfügung, nämlich Produktdaten (Stücklisten, Lieferantenzuordnungen, …), Prozessdaten (Fertigungsmaschinen, Rückverfolgbarkeit, …) sowie Qualitätsdaten. Besteht ein Produkt am Ende der Produktion im Prüfstand die Funktionsprüfung nicht, läuft die Künstliche Intelligenz los und durchforstet die Daten, die dieses Produkt während seiner Entstehung verursacht oder berührt hat. Anomalien werden einerseits aufgedeckt und andererseits bewertet, ob diese prozessual bedingt sind oder ob diese die Ursache für Minderqualität sein können. Den verantwortlichen Entscheidungsträgern wird schnell die Empfehlung gegeben, wo sie in der komplexen Produktionskette von an die 1.000 Fertigungsmaschinen eingreifen sollen, so dass keine Minderqualität mehr produziert wird.
KI-Lösung deckt Fehler deutlich schneller auf
Selbstlernende Künstliche Intelligenz-Lösungen ermitteln verlässlich und schnell die Ursache-Wirkungs-Zusammenhänge. Geschwindigkeit ist wichtig, da die Produktion 24 Stunden / 7 Tage in der Woche durchläuft. Je schneller die tatsächlichen Gründe für fehlerhafte Produkte aufgedeckt werden, desto schneller können Gegenmaßnahmen ergriffen werden, um zukünftige Fehlfunktionen zu vermeiden. Dies spart Zeit und reduziert deutlich den Ausschuss.
Zitat des Automobilzulieferers: „Wir konnten beweisen, dass wir um 20 Prozent schneller sind, den Fehler zu finden.“ Der Haupterfolgsfaktor ist der schnelle Detektionsmechanismus innerhalb der Produktionskette, der durch Künstliche Intelligenz realisiert wird. Komplexe Ursache-Wirkungs-Erkenntnisse können von mehreren Tagen auf Stunden reduziert werden.
Für eine nachhaltige Qualitätsoptimierung ist es wichtig, dass die KI mitlernt und sich bei Änderungen der Prozesse, der Produkte, der Einflüsse, … eigenständig – also ohne Zutun eines Data Scientist – an die Veränderungen anpasst. Hierfür kommt eine Selbstlernalgorithmik mit dynamischem und adaptivem Lernen zum Tragen.
Das könnte Sie auch interessieren:
Erfolgsfaktoren für KI und Data Mining in der Produktion
Auftragslokalisierung erhöht die Fertigungstransparenz
Wie Künstliche Intelligenz Einzug in den Fertigungsprozess hält
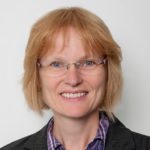
Britta Hilt ist Geschäftsführende Gesellschafterin und verantwortlich für Marketing und Vertrieb bei der IS Predict GmbH in Saarbrücken (www.ispredict.com). Foto: Autorin
Richard Martens ist dort Geschäftsführender Gesellschafter und zuständig für Forschung und Entwicklung.