Nachhaltige Lösungen aus Aluminium für den Automobilbau
Mit dem Ziel, recycelbare und kosteneffiziente Aluminium-Leichtbaulösungen für den Automobilmarkt zu entwickeln, hat ein innovativer Leichtmetall-Zulieferer Mitte Januar 2021 seine Führungsrolle bei einer neuen F&E-Initiative bekannt gegeben.
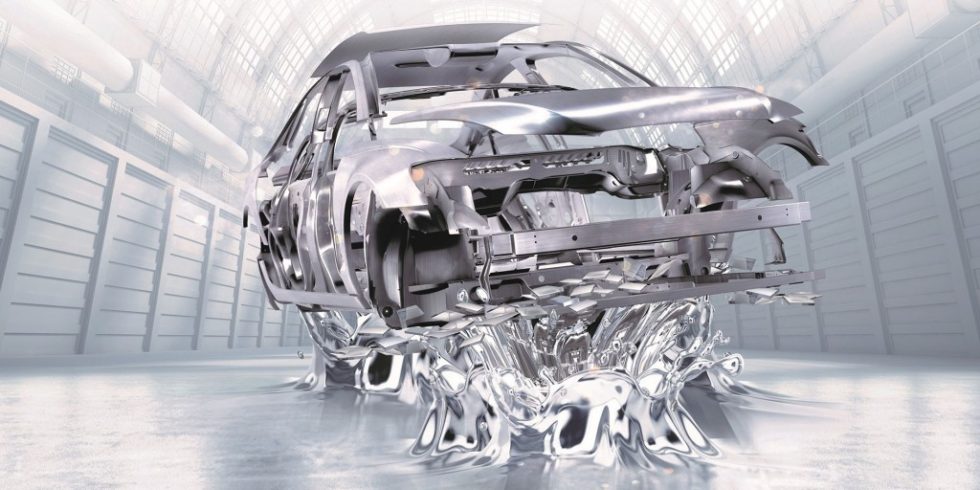
Lösungen für die fortschrittliche Mobilität: Aluminiumbleche senken das Gewicht im Automobilbau und erhöhen die Reichweite.
Foto: Constellium
Das zukunftsträchtige Projekt trägt den Namen „ISA3“ und hat eine Laufzeit bis 2023. Neben dem weltweit tätigen Aluminium-Spezialisten Constellium und der Renault Gruppe beteiligen sich auch die ESI-Gruppe (ein Spezialist für Lösungen zum Virtual Prototyping), das französische Institut de Soudure (Institut für Schweißtechnik) und die Universität Lothringen am Forschungsvorhaben, das mit rund 7 Millionen Euro gefördert wird. Für einen Teil davon kommt die Investmentbank Bpifrance auf.
Der zunehmende Aluminiumanteil bei Fahrzeugteilen für Karosserien und Strukturen macht bei den Forschungs- und Entwicklungsteams der Zulieferer kontinuierliche Optimierungsanstrengungen nötig. Denn mit der erweiterten Nutzung verändern sich auch die Ansprüche an das Material. So müssen die Bleche, aus denen Türen gefertigt werden, formbarer sein als andere Fahrzeugteile. Gleichzeitig wachsen die Sicherheitserwartungen: Moderne, hochfeste Crash Management Systeme an der Fahrzeugfront und am Heck schützen die Karosserie im Fall einer Kollision und erhöhen so die Sicherheit von Fahrer und Mitfahrern dank verbesserter Energieabsorption.
In allen Phasen des Lebenszyklus recycelbar
Mit ISA3 wollen der NE-Metall-Spezialist und die Forschungspartner den Leichtbau von Fahrzeugen vorantreiben. Ziel ist auch, bei den Automobilherstellern den Wechsel von Stahl zu Aluminium beschleunigen. Die Konzentration liegt auf Legierungen und Lösungen, die einen geschlossenen Recyclingkreislauf zulassen. Im Projekt sollen beispielsweise Aluminium-Autotüren entwickelt werden, die 15 Prozent leichter sind als der derzeitige Durchschnitt. Sie sollen drüber hinaus effizienter zu produzieren sein.
Constellium gilt als führender Full-Service-Anbieter von gewalzten und stranggepressten Aluminiumlösungen für den globalen Automobilmarkt. Das Portfolio umfasst Lösungen für Türen, Hauben und Klappen, Strukturkomponenten, Crash-Management-Systeme oder auch Batteriegehäuse. Weltweit gibt es mehr als 25 Produktionsstätten, unter anderen auch in Deutschland in Singen am Bodensee. Als erfahrener Systempartner arbeitet das Unternehmen mit nahezu allen Automobilherstellern eng zusammen.
Jack Clark, Senior Vice President Manufacturing Excellence und Chief Technical Officer bei Constellium, äußert sich hocherfreut, dass sein Unternehmen im wegweisenden F&E-Projekt seine Expertise einbringen kann: „Damit können wir unser Engagement als Anbieter von nachhaltigen Lösungen für Kunden aus der Automobilindustrie erneut demonstrieren“, sagt er. Ziel ist unter anderem, die Umwelteinflüsse der gesamten Lieferkette für Aluminium im Automobilbau zu reduzieren. Ein Stichwort lautet „End-of-Life-Recycling“.
Fokus auf Elektromobilität und auf Kostenreduzierung
„Mit den Ergebnissen aus dem Projekt ISA3 sollte es gelingen, dass Aluminium eine noch bedeutendere Rolle auf dem Automobilmarkt spielen kann. Denn die Hersteller sind bestrebt, ihre CO2-Emissionen zu reduzieren und ihr Angebot an Elektrofahrzeugen zu erweitern“, erläutert Clark weiter.“ Die Forschungspartnerschaft mit einem strategischen Kunden wie Renault macht es für Constellium möglich, Lösungen zu erforschen, die auf eine breite Palette von Fahrzeugen anwendbar sind – und die sowohl ökologische als auch wirtschaftliche Vorteile bieten. So sollen sowohl leichtere, sicherere und kraftstoffeffizientere Fahrzeuge als auch Elektrofahrzeuge mit größerer Reichweite entstehen.
Für den Automobilbauer Renault stehen bei dem Projekt vor allem die möglichen finanziellen Ersparnisse im Mittelpunkt. Denn Leichtmetalle sind teurer als Stahl: „Wir müssen die Kosten pro Kilogramm Gewichtsersparnis bei Automobilkomponenten verringern. Dies trifft insbesondere auf Aluminiumteile zu“, erklärt Patrice Belliard, Expert Flat Products bei der Renault Gruppe. „Aus unserer Sicht lautet ein wichtiges Ziel des ISA3-Projekts, den Preis pro Kilogramm bei Aluminium-Türen um die Hälfte zu reduzieren, um Fahrzeuge durch den Einsatz von Aluminium leichter machen zu können.“
Ideale Entwicklungsumgebung dank Forschungspartnerschaft
„Mit unseren Lösungen ‚Pre-certification & Validation‘ sowie ‚Smart Manufacturing‘ können wir helfen, das Design und die Herstellung von Aluminium-Türen zu validieren, ohne dass dazu physische Prototypen benötigt werden“, ergänzt Pierre Culière, Pre-Certification & Validation Outcome Director der ESI-Gruppe. Durch diese Software und das Know-how von ESI in der Materialsimulation wird eine schnelle und präzise Entwicklung von neukonstruierten Bauteilen für Automobile möglich.
Erst Kürzlich hatte Constellium mit einem Großauftrag aus dem Automobilsektor auf sich aufmerksam gemacht. Im Sommer 2020 gab der Aluminiumspezialist bekannt, dass er ab sofort die Karosseriebleche für die europäische Fertigung des neuen „Toyota Corolla“ liefert. Er ist Alleinlieferant der Bleche, die für die Produktion der Motorhaube des neuen Kompaktmodells benötigt werden. Dieses entsteht in den Werken Burnaston, Großbritannien, und Arifiye, Türkei. Der japanische Volumenhersteller Toyota verwendet für diese Modellreihe zum ersten Mal Aluminiumbleche in seinen europäischen Produktionsstätten. Für deren Herstellung wird die High-Tech-Legierung „Surfalex HS“ genutzt. Diese Legierung bietet beste Oberflächen- und „Roping“-Eigenschaften; darüber hinaus auch eine hohe Korrosionsbeständigkeit.
Der globale Branchenführer liefert Aluminiumprodukte „mit Mehrwert“ nicht nur für den Automobilsektor, sondern auch für Branchen wie die Luft- und Raumfahrt oder die Verpackungsindustrie. 2019 wurde ein Umsatz von 5,9 Milliarden Euro verzeichnet.
Wissenswertes zum Thema Automobilbau finden Sie auch hier