Schwäbische Kooperation treibt die Elektromobilität an
Zwei mittelständische Maschinenbauer aus der Nähe Stuttgarts bündeln seit Kurzem ihr Know-how. Gemeinsam sind die Technologieführer in der Lage, der weltweiten Automobilindustrie komplette Turnkey-Fertigungslinien für die wichtige Komponente Hairpin-Statoren anzubieten.
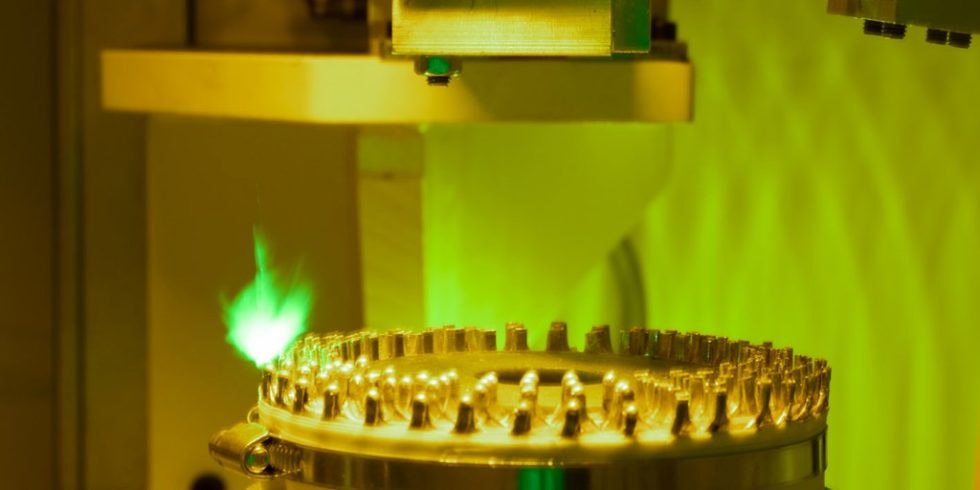
Laserschweißen eines Stators: Der Technologieführer aus Ostfildern hat umfangreiches Wissen in den unterschiedlichen Kerntechnologien der Statorenproduktion aufgebaut.
Foto: Gehring
Der erste Schritt zum neuen, mittelständischen Netzwerk ereignete sich bereits im November 2020, als die familiengeführte Nagel-Gruppe aus Nürtingen den Anlagen- und Maschinenhersteller Gehring im benachbarten Ostfildern übernahm. Damit verbesserte er seine Position als Technologiepartner bei Produktionssystemen für die Elektromobilität weiter. Der nächste wichtige Schritt ist jetzt die intensive Kooperation mit dem Umformspezialisten Wafios aus dem benachbarten Reutlingen. Beide Partner sind Technologieführer in ihrem jeweiligen Bereich. Somit wächst zusammen, was technologisch und strategisch bestens zusammenpasst.
Wenn ein schwäbisches Netzwerk erfolgreich elektrifiziert
Im Großraum Stuttgart, einem der wichtigsten Standorte der Automobilbranche in Deutschland, entsteht damit ein Verbund aus zwei starken Mittelständlern mit insgesamt fast 3000 Mitarbeitern. Gemeinsam planen die Partner, Stator-Montagelinien für alle wichtigen Automobilstandorte weltweit – und von der Idee bis zur Inbetriebnahme – zu realisieren. So können sie der aufstrebenden E-Mobilität in Deutschland und weltweit wichtige Impulse geben.
„Dank der Kooperation lässt sich die gesamte Prozesskette effizienter aufbauen, weil wir die Technologien übergreifend betrachten und uns nicht nur auf Einzelprozesse konzentrieren“, erklärt Dr. Wolfram Lohse, CTO bei Gehring. Die Kooperation bietet alles „aus einer Hand“, von der Prototypenfertigung bis hin zu Anlagen für die Serienproduktion. Ein weiterer wichtiger Aspekt: Der OEM (Original Equipment Manufacturer), der in Anlagentechnik investieren möchte, hat für die gesamte Prozesskette nur einen Ansprechpartner. „Der größte Profiteur ist der Automobilhersteller. Alle unnötigen Schnittstellen und Reibungspunkte von Einzellösungen wurden beseitigt“, erklärt Tobias Single, Leiter E-Mobility bei Wafios. Gebündelt wird nun die jahrzehntelange Erfahrung von Gehring bei der Auslegung von Anlagen für die automobile Serienfertigung und die Technologieführerschaft von Wafios im Bereich der Richttechnologie und Drahtumformung. Diese ist insbesondere für die Fertigung der „Hairpins“ sehr wichtig.
Welche Technologien steuern die erfahrenen Partner der Automobilbranche bei?
Wafios bringt sein langjähriges Know-how im Umformen von Kupferdraht zu Steckspulen (Hairpins) ein. Dies ist eine auf Flachdraht basierende Alternative zu klassischen Runddrahtwicklungen. Mit Blick auf reibungslose Folgeprozesse wurde sie für Prototypen, Klein- und Großserien perfektioniert. Dank der neuartigen Biegetechnologie lassen sich die Hairpin-„Beine“ hochpräzise positionieren – ein wesentliches Qualitätsmerkmal. Eine bedeutende Rolle spielt das Biegen von beschichteten Stromleitern, bei denen es auf das Zusammenspiel von Drähten und Isolierschicht ankommt. Eine intelligente Kamera überprüft während des Biegens typische Geometriemerkmale und sorgt ggf. für eine automatische Kompensation. Die Biegewerkzeuge arbeiten weitestgehend geometrieunabhängig, um komplette Pin-Sätze für mehrere Statorvarianten ohne Werkzeugwechsel auf einer Anlage herstellen zu können.
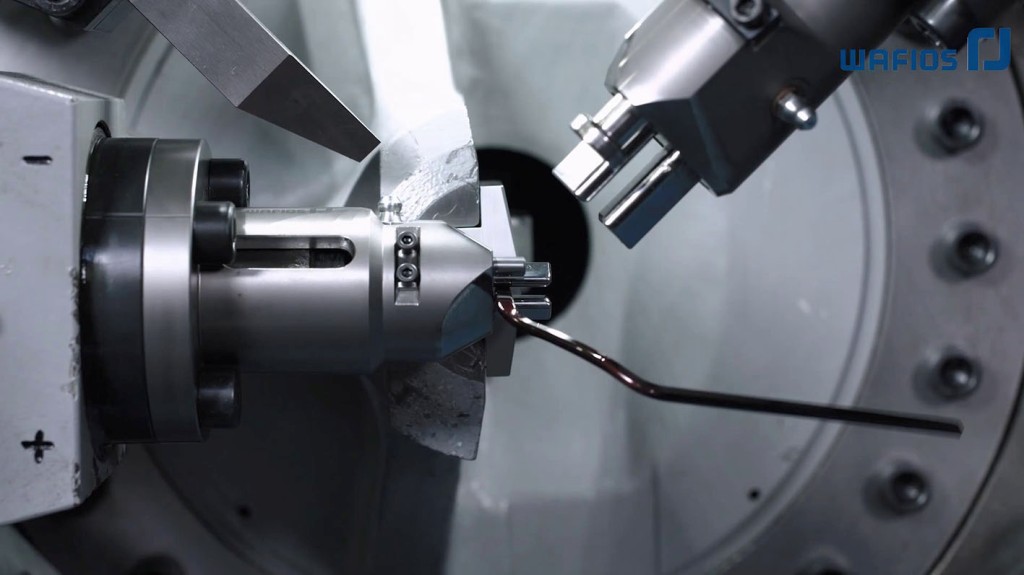
Hairpin-Biegeprozess auf einem „Speedformer“: Die entwickelte Anlagentechnik lässt sich „eins zu eins“ auf die Serienfertigung mit ihren extrem kurzen Taktzeiten übertragen.
Foto: Wafios
Die Bandbreite bei Gehring reicht von „kleinen“ Lösungen für den Stator-Musterbau bis hin zu großen vollautomatisierten Fertigungslinien. Das digitale Vernetzen der Anlagentechnik übernimmt die IoT (Internet of Things)-Plattform „Gehring-Core“. Die „SNT“-Maschinenbaureihe deckt hochproduktive Setzverfahren für unterschiedliche Hairpin-Wicklungen ab. Sie lässt sich nahtlos an die „Speedformer“-Maschinen von Wafios anschließen. Die redundant ausgelegten Stränge mit Pin-Produktion, Pin-Setzen und Einbringen des erzeugten Drahtkorbs steigern die technische Verfügbarkeit und die Skalierbarkeit. Für effizientere Fügeprozesse wurde zudem die Auslastung der energie- und kostenintensiven Laserquellen maximiert. Das senkt die Anzahl an Schweißmaschinen, den Investmentaufwand und den Flächenbedarf.
Hohes Fertigungstempo ist eine Herausforderung für das Drahtbiegen
Die schnelle Geschwindigkeit in der Großserien-Produktion, bei der im Takt von unter einer Minute E-Motoren entstehen, ist eine hohe Herausforderung für die Statorfertigung und seine sehr komplexen Drahtbiegeprozesse. Tobias Single von Wafios sagt dazu: „Wir beherrschen diese Komplexität und können auf der soliden Basis des vorhandenen Know-hows effiziente, prozessfähige und zukunftssichere Gesamtlösungen anbieten. Hinzu kommt: Der Biegeprozess trägt erheblich zur Qualität bei. Alles, was ich zu Beginn richtig oder falsch mache, erleichtert bzw. erschwert die weiteren Prozesse.“ Also kommt mit Wafios der richtige Partner „mit ins Boot“: Die Biegemaschine „FMU E“ des Umformspezialisten hat sich in der Automobilbranche bereits vielfach in der Kleinserienfertigung von Hairpins bewährt.
Doch es geht nicht nur um die Überführung vorhandener Technologie in die Massenproduktion. Die Kooperation geht auch neue Entwicklungen an, um die Leistungsfähigkeit und den Wirkungsgrad der Elektromotoren zu verbessern. Hierfür kommt ein dritter Partner ins Spiel.
Speziell ausgelegtes Gießharz verbessert die Leistung von E-Motoren
Das Startup-Unternehmen copaltec entwickelt als Partner der Nagel-Gruppe spezielle Gießharze auf Polyurethan (PUR)-Basis. Die Harze werden mit einem Vakuumverfahren in die Motoren eingebracht, um diesen vor externen Einflüssen sowie Überhitzung zu schützen. „Das speziell für diesen Zweck formulierte Gießharz kann die Leistung von Elektromotoren um bis zu 20 Prozent steigern“, sagt dazu Jochen Nahl, beratender Ingenieur bei copaltec. „Unser Harz verfügt über eine hohe Wärmeleitfähigkeit. Die bisher eingesetzten Vergussmassen dienen zur Isolierung, zum Verkleben von Zellen und Magneten sowie als ,Gapfiller‘ – also zum Füllen von Spalten. Deshalb erhitzen sich Batterie und Elektromotor: Sie müssen üblicherweise aktiv gekühlt werden.“
Um für Abhilfe zu sorgen, setzt das Start-up auf das Prinzip „Einbringen von Wärmeleitfähigkeit über die Vergussmasse“, was die notwendige Kühlleistung erheblich senkt. Das neukonzipierte Harz hält den E-Motor auf niedrigerem Temperaturniveau und steigert auf der anderen Seite die Leistung. Gemeinsam mit Gehring erarbeitet copaltec nun Maschinenlösungen für die Industrialisierung im elektrischen Antriebsstrang.
Skalierbare Anlagentechnik lässt sich stets an den Kundenbedarf anpassen
Das neue mittelständische Netzwerk kann inzwischen alle wichtigen Kerntechnologien – vom Biegen bis hin zum Imprägnieren bzw. dem abschließenden Vergießen mit Harz – anbieten. „Wir entwickeln gemeinsam skalierbare und modulare Lösungen, die sich an der Produktionsphilosophie unserer Kunden orientieren“, so Bernd Nagel, Geschäftsführer von Nagel sowie von der neu erworbenen Gehring-Gruppe. „Als Systemausrüster integrieren wir die jeweils erforderliche Fördertechnik und Automatisierung, die von Zulieferern stammt. Denn beispielsweise ergibt eine Vollverkettung bei einer jährlichen Losgröße von maximal 50.000 in der Regel keinen Sinn.“ Jedoch dank der Skalierbarkeit kann eine ursprünglich für die Kleinserie ausgelegte Anlage bei Bedarf auch Richtung Großserie „wachsen“.
„Dank unserer gewinnbringenden Kooperation können die Partner alle Verfahren prozessübergreifend aufeinander abstimmen. So verbessern sie den gesamten Herstellungsprozess ganzheitlich über die komplette Technologiekette“, betont Dr. Uwe-Peter Weigmann, Vorstandsvorsitzender von Wafios. Problematisch ist für Anwender häufig das technische Risiko, das beim Know-how-Übertrag der Statorfertigung von der Klein- auf die Großserie gegeben ist. Dieses lässt sich dank der Zusammenführung des Wissens – von der Musterfertigung bei Wafios und Gehring bis hin zu konzipierten kompletten Serienanlagen – jetzt deutlich verringern. Die Unterstützung endet zudem nicht mit der Auslieferung: Hierfür stehen die langjährig im Praxiseinsatz erprobten Servicenetzwerke der beiden Partner bereit, die für raschen Support in allen wichtigen Ländern sorgen.
Die Entwicklung geht immer weiter
Um die Technik permanent weiter zu optimieren – und weil auch „elektromobile Theorie grau ist“ – steht inzwischen der neue Musterbau im Gehring-Stammwerk in Ostfildern bereit. Dort gibt es komplette Anlagen für Praxisversuche, auf denen sich beispielsweise Hairpin-Statoren und Elektromotoren produzieren lassen. Gemeinsam mit den Kunden entwickeln die Netzwerkpartner auf dieser Basis maßgeschneiderte Technik für die jeweiligen Einzeltechnologien wie Drahtbiegen oder Hairpin-Setzen.
Das könnte Sie auch interessieren:
Trends beim Lasereinsatz für die Elektromobilität
Leichtbau-Kosten bewerten am Beispiel eines modularen Batteriekonzepts