Technologischer Durchbruch: Beschichtete Bremsscheiben vermeiden Feinstaubemissionen
Eine spektakuläre Durchbruchsinnovation zum Thema „Feinstaub beim Bremsen“ unterstützt seit Kurzem die im „Green Deal“ formulierten Klimaziele der Europäischen Union: Beschichtete Bremsscheiben sorgen für eine deutliche Reduktion der Feinstaubemissionen.
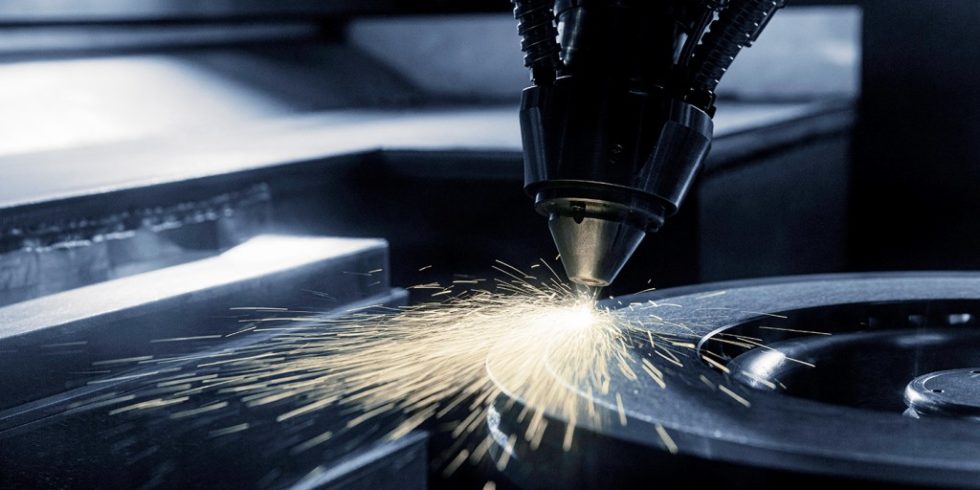
Die Wecodur-Technologie ist ein neues, in Aachen entwickeltes Laserbeschichtungsverfahren. Herkömmliche Bremsscheiben erhalten damit eine verschleißarme Hartstoffbeschichtung.
Foto: HPL Technologies
Im Januar 2021 sind rund 66,9 Millionen Fahrzeuge in Deutschland zugelassen, 48,2 Millionen davon sind Personenkraftwagen – dies belegt die aktuelle Statistik des Kraftfahrt-Bundesamtes aus Flensburg. Bremsscheiben von Automobilen beeinflussen bekanntermaßen – neben den Fahrzeugantrieben – sehr stark die Feinstaub- und CO2-Emissionen im Straßenverkehr. Hartstoffbeschichtungen zeigen hier eine deutliche Gegenwirkung. Mit der neuen in Aachen entwickelten „Wecodur“-Beschichtungstechnologie steht seit kurzem ein revolutionäres Verfahren mit vielen Vorteilen zur Verfügung: Bremsscheiben erhalten damit quasi ihr Öko-Siegel.
Große Beeinträchtigungen für Mensch und Umwelt
Luftverschmutzung führt zu 4,5 Millionen vorzeitigen Todesfällen pro Jahr – so mahnte das Deutsche Ärzteblatt am 12. Februar 2020. Der Abrieb einer Bremsscheibe trägt dabei nicht unwesentlich zur Schädigung von Umwelt und Gesundheit bei: 2020 veröffentlichte die OECD eine Studie zum Thema Feinstaub im Straßenverkehr. Die Autoren unterscheiden zwischen den abgasinduzierten Emissionen („Exhaust-Emissionen“) und den durch Reifen, Straßenbelag und Bremsen verursachten Varianten („Non-Exhaust-Emissionen“). Konnten in den letzten Jahren dank verschiedener Entwicklungen im Motorenbau die Exhaust-Emissionen deutlich reduziert werden, so blieben die Non-Exhaust-Emissionen auf einem konstanten Niveau.
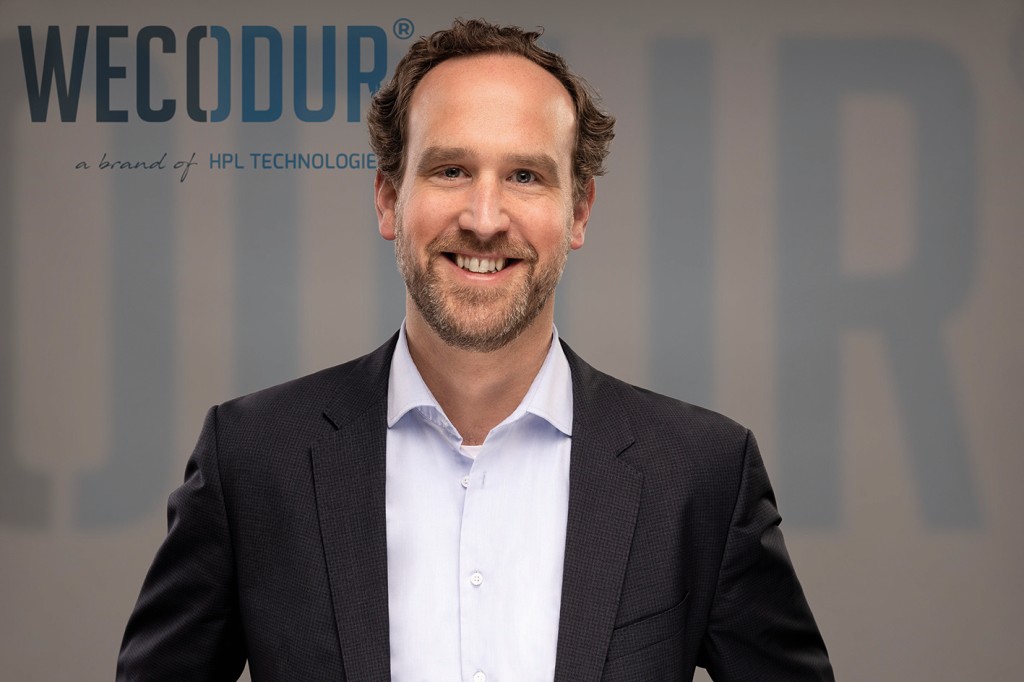
Dr.-Ing. Phillip Utsch, Geschäftsführer von HPL Technologies, kommentiert: „Auf Basis von Prüfstandsergebnissen gehen wir davon aus, dass der beim Bremsen entstehende Feinstaub um bis zu 90 Prozent reduziert wird.“
Foto: HPL Technologies
Die Bremsscheiben von Fahrzeugen werden in der Regel aus Grau- oder Sphäroguss hergestellt. Im Betrieb entsteht Feinstaub, der in die Umgebung gelangt. Für Abhilfe sollen verschleißbeständige Hartstoffbeschichtungen sorgen: Denn die Wecodur-Technologie kann den Anteil an den Non-Exhaust-Emissionen nun spürbar reduzieren. „Auf Basis von Prüfstandsergebnissen gehen wir davon aus, dass der beim Bremsen entstehende Feinstaub mit unserer Technologie um 70 Prozent bis hin zu sogar 90 Prozent reduziert wird“, erklärt Dr.-Ing. Phillip Utsch, einer der „Väter“ der neuen Technologie. Er ist Managing Director der Firma HPL Technologies, ansässig am „Campus-Boulevard“ in unmittelbarer Nähe zur RWTH Aachen.
Bei der Technologie handelt es sich um ein neues, in Aachen entwickeltes Laserbeschichtungsverfahren (www.wecodur.de). Die Lösung eignet sich, um extrem verbesserte Standzeiten von Bauteilen zu erzielen oder um spezielle Fertigungsaufgaben zu lösen. Durch die fast immer gleiche Prozesskette ist eine hohe Zuverlässigkeit in der Produktion gegeben, insbesondere in der Serienfertigung. Typische Anwendungsfelder sind Hydraulikbauteile, Walzen, Umformmatritzen sowie (allen voran) die kostengünstige Herstellung von wartungsfreien Bremsscheiben für die Automobilindustrie.
Wie wirkt sich die neue Technologie aus?
Bremsscheiben, die eine zusätzliche Wecodur-Beschichtung erhalten haben, sind um ein Vielfaches robuster als unbeschichtete Exemplare. Sie können daher dünner ausgelegt werden. „Bei einem Oberklasse-Pkw lassen sich aufgrund der reduzierten Masse der beschichteten Bremsscheiben rund 80 Gramm CO2 pro 100 km einsparen“, betont Utsch. Aber nicht nur auf der Straße, sondern bereits während der Herstellung ergeben sich deutliche Vorteile für die Umwelt: „Bei der Beschichtung einer entsprechend ausgelegten Bremsscheibe entstehen ca. 85 Prozent weniger CO2-Emissionen als bei konventionellen Beschichtungsverfahren.“
Die Experten sind sich sicher, dass ihre Technologie die Herausforderung der Zeit trifft: Nachhaltigkeit ist gesellschaftlicher Konsens. Beschichtete Bremsscheiben setzen laut Utsch einen neuen Maßstab mit großer Wirkung – und dies auf sehr lange Sicht. Werden zunehmend größere Pkw mit Elektro- oder auch Hybrid-Antrieben ausgestattet, so sind auch weiterhin klassische Bremsanlagen notwendig. Selbst E-Kleinwagen, die in den meisten Fällen mit Rekuperationsbremsen verzögern können, benötigen aus Sicherheitsgründen zusätzliche Scheibenbremsen. Hier kommen die „geballten“ Vorteile – wie etwa der Korrosionsschutz – zum Tragen. Gerade bei Ausbleiben der „Reinigung“ durch den Bremsvorgang stellt die Korrosion ein enormes Problem im Rekuperationsbetrieb dar. Durch die extrem beständige Beschichtung hat der Rost zu-künftig jedoch keine Chance mehr.
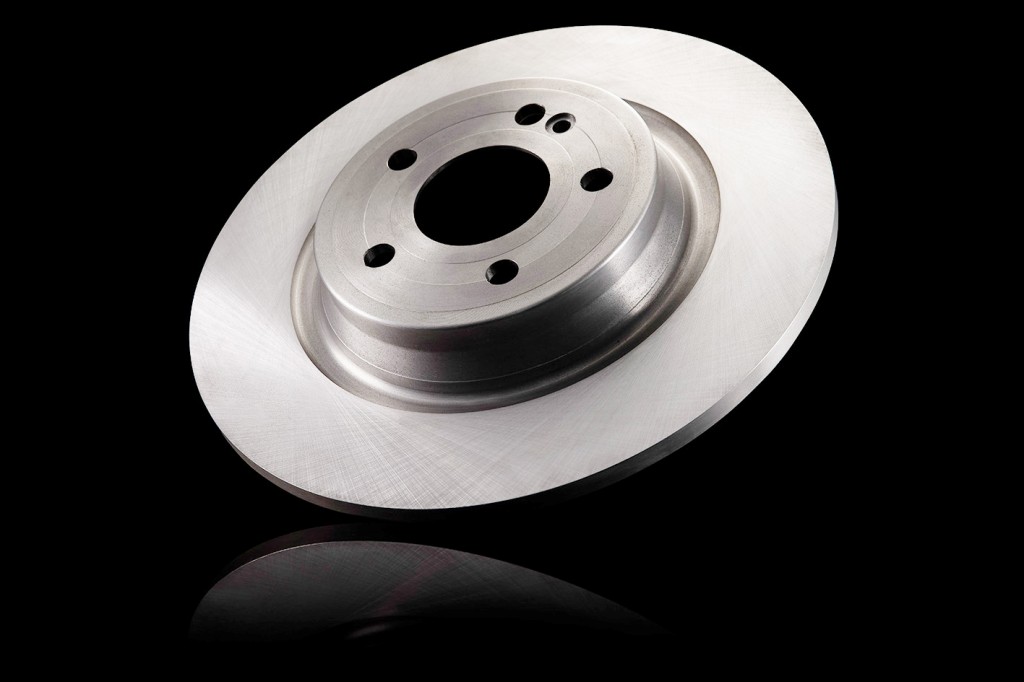
Feinstaub lässt sich durch verschleißbeständige Hartstoffbeschichtungen vermeiden. Die abgebildete Bremsscheibe wurde mithilfe der Wecodur-Technologie beschichtet und gefinisht.
Foto: HPL Technologies
Konventionelle Bremsscheiben, die eine Wecodur-Beschichtung erhalten haben, zeigen einen deutlich reduzierten Verschleiß bzw. Abrieb. Auch Korrosion ist kein Problem mehr, denn die Beschichtung schützt wirksam vor den Angriffen aggressiver Substanzen wie Streusalz. Dadurch nimmt die Lebensdauer signifikant zu. Für den Verbraucher bedeutet das: die Service-Zyklen reduzieren sich, die Werkstatt muss die Bremsscheiben kaum noch erneuern. Dies schont zum einen wertvolle Ressourcen, zum anderen den „Geldbeutel“ der Autobesitzer.
Für die nachhaltige und wirtschaftliche Bremsscheibe ist die gesamte Prozesskette zur Herstellung entscheidend. Die Aachener Produktionsexperten haben daher neben der Technologie auch komplette, vollautomatisierte Fertigungsanlagen entwickelt. Auf Basis von Standard-Bremsscheiben entstehen damit extrem ressourcenschonend veredelte, einbaufertige Wecodur-Bremsscheiben.
Die Entwickler
Zielsetzung und Ausrichtung von HPL Technologies ist die industrielle Vermarktung der Technologie. Dazu gehören die Schichtsystementwicklung, Prototypenproduktion, der Aufbau von Produktions- und Anwendungs-Know-how, die Herstellung von Produktionsanlagen und Komponenten sowie die Unterstützung im laufenden Produktionsprozess. Im Unternehmen vereinen sich die Kompetenzen der Kooperationspartner rund um die Wecodur-Prozesskette: von der Technologieentwicklung über den Maschinen- und Anlagenbau bis hin zur Automatisierungstechnik. Die technologischen Grundlagen der Hochgeschwindigkeitsbeschichtung wurden an der RWTH Aachen und vom Fraunhofer ILT (Institut für Lasertechnik) entwickelt. Mit diesen Partnern arbeitet HPL auch in Zukunft an der Weiterentwicklung der Schichtsysteme eng zusammen. Die für das Finishing notwendige Präzisions-Schleiftechnik wird von einem auf diesem Gebiet namhaften deutschen Unternehmen beigesteuert.
Das könnte Sie auch interessieren:
Vielfältige Herausforderungen beim Reinigen im E-Fahrzeugbau