Voluminöse Karosserieteile effizienter fertigen
Drehtische, auf denen komplexe und schwere Bauteile bearbeitet werden, stellen Anlagenbauer vor Herausforderungen: Mit zunehmender Automatisierung steigt auch der Integrationsgrad. Eigens entwickelte Drehdurchführungen sorgen jetzt für 360°-Bewegungsraum – damit der Tisch rotiert und nicht das Personal.
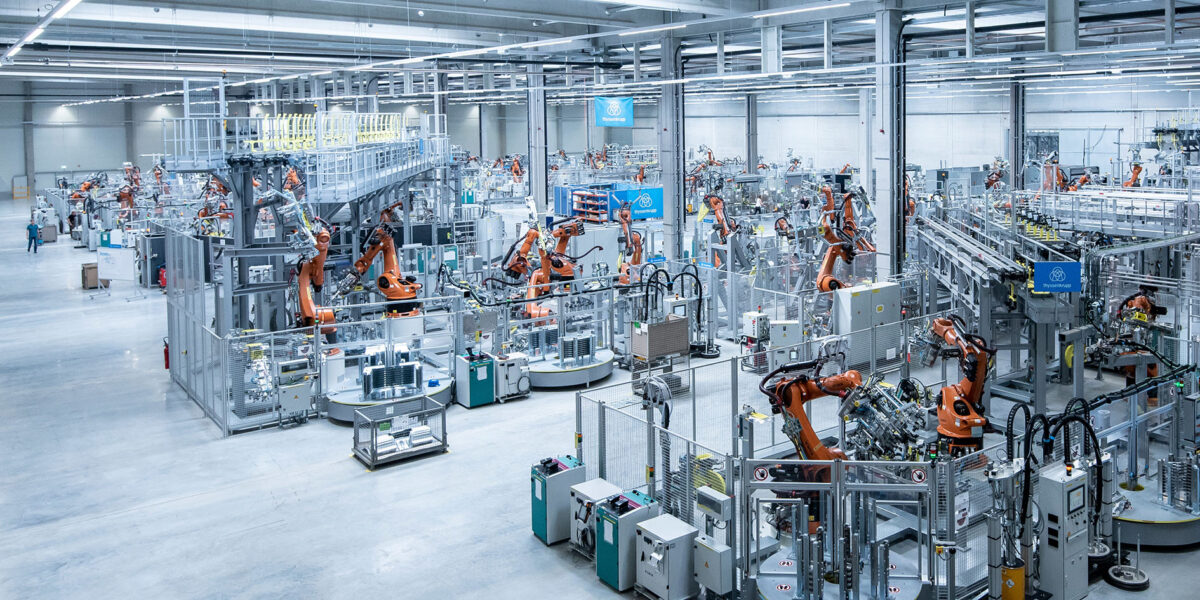
Produktionshalle: Potentielle Problemstellen wie die Befestigung der Komponenten an den Drehtischen bei thyssenkrupp Automotive Body Solutions ließen sich anhand von 3D-Modellen identifizieren und in der Konstruktion von vorn herein berücksichtigen.
Foto: thyssenkrupp Automotive Body Solutions
Die Aufgabenstellung ist komplex: Neben dem vom System benötigten Medium – etwa Druckluft, Vakuum oder Hydrauliköl – müssen die Drehtische auch mit Strom und Datenschnittstellen versorgt werden. Um diese ausfallsicher von den feststehenden in die rotierenden Maschinenelemente einzuspeisen, sind aufwendige Drehdurchführungen erforderlich. Aufgrund der vielen Variablen sind diese oftmals anwendungsspezifisch auszulegen.
Pneumatikdurchführung mit Komponenten zur Strom- und Datenübertragung
Für neue Drehtische mit pneumatischen Spannvorrichtungen zur Fertigung von Karosserieteilen, die sich kontinuierlich um 360° rotieren lassen, kam thyssenkrupp Automotive Body Solutions mit Hauptsitz in Heilbronn daher auf die Firma Konstandin zu. Der Karlsbader Familienbetrieb konzipierte und fertigte daraufhin 24 Drehdurchführungen, die neben jeweils zwei Druckluftanschlüssen mit G 1/2‘‘-Gewinde auch mit einer Signalleitung für Profinet sowie zwei weiteren Stromleitern ausgestattet sind. Aufgrund der Lebensdauerschmierung sind die Drehdurchführungen komplett wartungsfrei.
„Für unsere Drehtische mit Spannvorrichtung benötigten wir speziell angefertigte Drehdurchführungen, um eine kontinuierliche Bewegungsfreiheit auf 360° ohne Beschädigung der Leitungen zu erzielen“, berichtet Patrick Hofsommer, Head of Assembly Service Body-in-White bei thyssenkrupp Automotive Body Solutions.
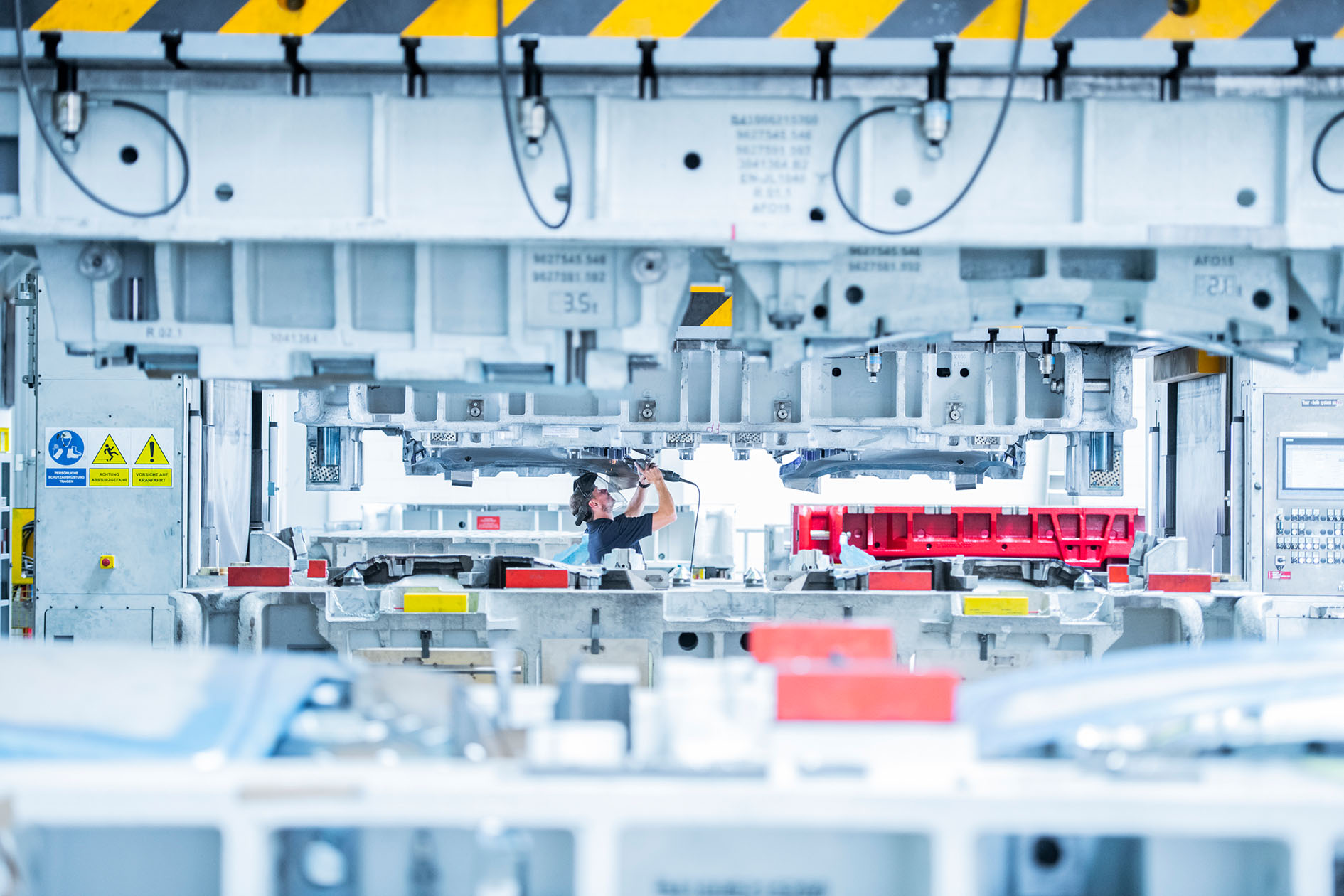
Blick in den Karosseriebau: Drehtische, auf denen komplexe und schwere Bauteile bearbeitet werden, stellen Anlagenbauer vor Herausforderungen.
Foto: thyssenkrupp Automotive Body Solutions
Während Drehdurchführungen für unterschiedliche Medien wie Druckluft, Vakuum oder Hydrauliköl als Standardmodule erhältlich sind, musste die Kombination der in diesem Fall geforderten Pneumatikdurchführung mit Komponenten zur Strom- und Datenübertragung anwendungsspezifisch konzipiert werden.
International aktiver Karosseriebau-Dienstleister
thyssenkrupp Automotive Body Solutions ist ein integrierter Karosseriebau-Spezialist: Das Produkt- und Serviceportfolio erstreckt sich vom Prototypen-, Werkzeug- und Anlagenbau bis hin zur Serienfertigung von Karosseriebauteilen. Das Unternehmen verfügt über sechs Entwicklungs- und Produktionsstandorte in Deutschland und weitere sechs Standorte im Ausland. Insgesamt werden weltweit rund 2300 Mitarbeitende beschäftigt. Die Geschäftseinheit gehört zum automobilen Zuliefer- und Service-Segment (Automotive Technology) der thyssenkrupp-Gruppe. Im Geschäftsjahr 2022/23 erwirtschaftete dieses Segment einen Umsatz in Höhe von 7,9 Milliarden Euro.
Schnelle und variable Rotation von Großbauteilen
Die neu entwickelte Drehdurchführung ist in fünf bis sechs Sekunden um 180° rotierbar, wobei die Drehbewegung taktend, oszillierend oder kontinuierlich stattfinden kann. „Grundsätzlich versuchen wir auch bei neuen Bauteilen auf bewährte Standardkomponenten zurückzugreifen, um die Fertigungskosten so gering wie möglich zu halten“, erklärt Mathias Kraft, Technischer Leiter bei Konstandin. „So haben wir es auch in diesem Fall gehalten und den Mediumteil, wie bereits mehrfach in der Vergangenheit, durch die Nachbearbeitung eines Standardmoduls realisiert.“
Die Komponente ist aus Edelstahl sowie Aluminium gefertigt, verfügt über ein austauschbares NBR-Dichtungssystem und leitet Druckluft sowie Vakuum zwischen –0,8 und 8 bar auf zwei Kanälen. So wird die Funktionalität der Spannvorrichtung auf dem Drehtisch sichergestellt, da eine kontinuierliche Bewegung sowohl unter Druck als auch drucklos erforderlich ist.
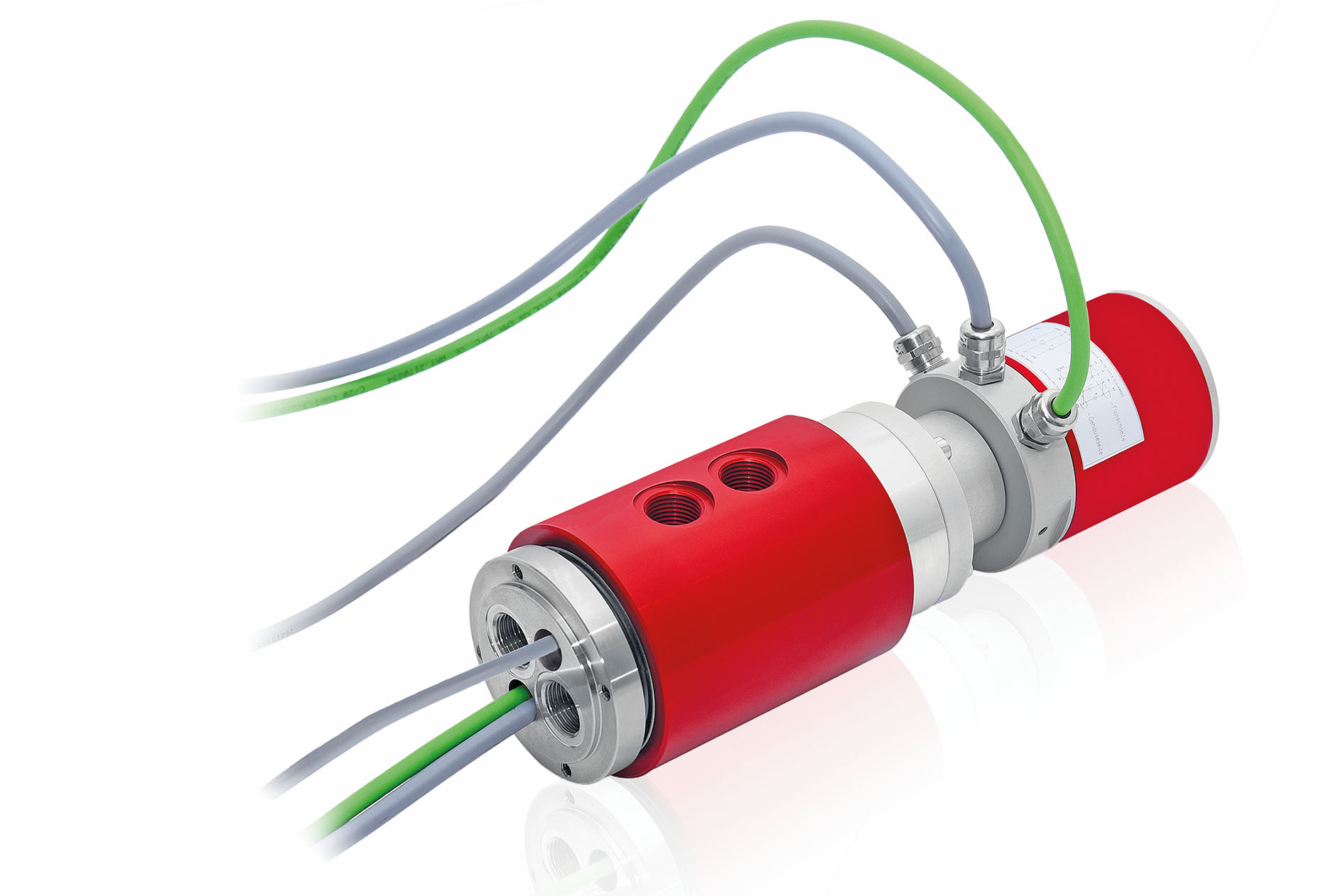
Für die Automotive-Anwendung wurden insgesamt 24 Drehdurchführungen konzipiert und gefertigt, die neben jeweils zwei Druckluftanschlüssen auch mit einer Signalleitung für Profinet sowie zwei weiteren Stromleitern ausgestattet sind. Grafik: Konstandin
Den notwendigen Stromüberträger musste der Hersteller hingegen eigens für die Anwendung bei thyssenkrupp Automotive Body Solutions entwickeln und auslegen. Für den Einsatz in der rauen industriellen Fertigung ist der Stromteil gemäß IP64 staubdicht und gegen Spritzwasser geschützt. Zudem verfügt die Drehdurchführung über eine Lebensdauerschmierung, sodass die vor Ort austauschbare Dichtung das einzige Verschleißteil ist.
Eine Kombination aus Standardmodulen und einer Spezialanfertigung
Da alle technischen Anforderungen im Vorfeld besprochen und klar kommuniziert wurden, konnte Konstandin die ersten acht Drehdurchführungen in nur drei Monaten realisieren und fristgerecht ausliefern. Auch potentielle Problemstellen wie die Befestigung der Komponenten an den Drehtischen ließen sich anhand von 3D-Modellen identifizieren und in der Konstruktion von vorn herein entsprechend berücksichtigen. „Unsere Drehdurchführungen sind in der Regel Lösungen, die nach Kundenwunsch ausgelegt und optimiert wurden“, resümiert Kraft. „Aufgrund unseres umfangreichen Portfolios können wir aus bestehenden Einzelteilen von Drehdurchführungen mit wenig Aufwand anwendungsspezifische Produkte realisieren.“
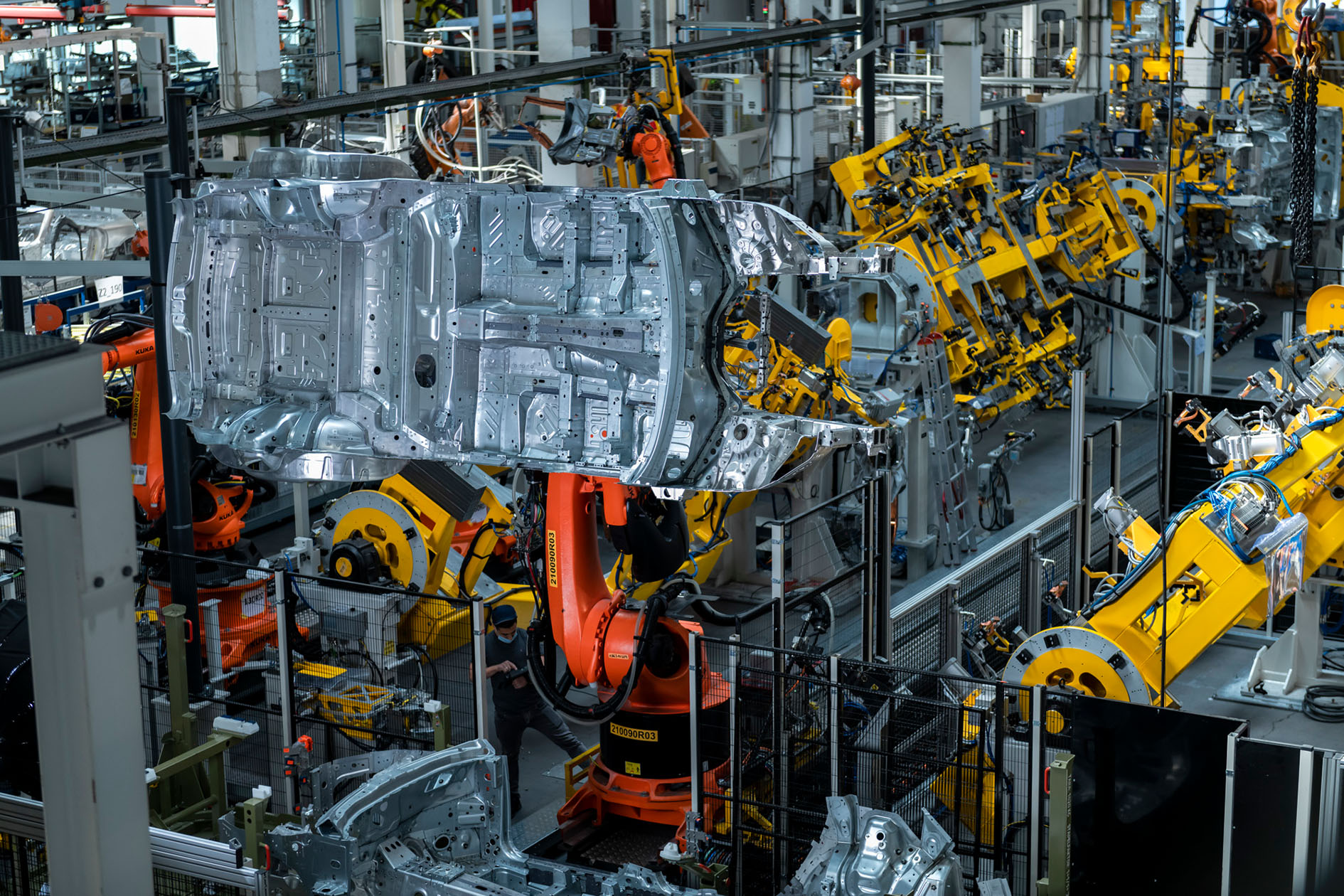
Eine Gesamtkarosse wird gehandhabt: Die Kombination der Pneumatikdurchführung mit Komponenten zur Strom- und Datenübertragung musste von Konstandin anwendungsspezifisch konzipiert werden.
Foto: thyssenkrupp Automotive Body Solutions
Auch Hofsommer zeigt sich sehr zufrieden mit der Zusammenarbeit mit Konstandin. Der Familienbetrieb, 1975 gegründet, befindet sich inzwischen in zweiter und dritter Generation und wird von den Geschäftsführern Jörg und Jonas Konstandin geleitet. Das badische Unternehmen entwickelt, produziert und vertreibt mit insgesamt 40 festangestellten Fachkräften erfolgreich technische Komponenten und Systeme sowie kundenspezifische Sonderlösungen in den Bereichen Pneumatik, Hydraulik und Vakuumtechnik.
Das könnte Sie auch interessieren:
Welchen Einfluss hat Sauberkeit auf die Dichtheit von Verbindungen?
Kann ein Roboter eigenständig Batteriesysteme demontieren?
Mehr Prozess- und Arbeitssicherheit in der Verpackungsproduktion
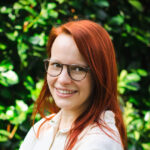
Sandra Walz arbeitet als freie Redakteurin in München. Foto: Autorin