Wenn die Klimaanlage ausfällt, bleibt das E-Auto stehen
Wenn in einem gebräuchlichen Automobil die Klimaanlage wegen eines zu hohen Kältemittelverlusts ausfällt, ist das lästig. Wenn aber bei einem modernen Elektrofahrzeug die Kühlung der Batterie ausfällt, schaltet eine Sicherheitselektronik die Batterie nach kurzer Zeit ab: Das Fahrzeug bleibt stehen.
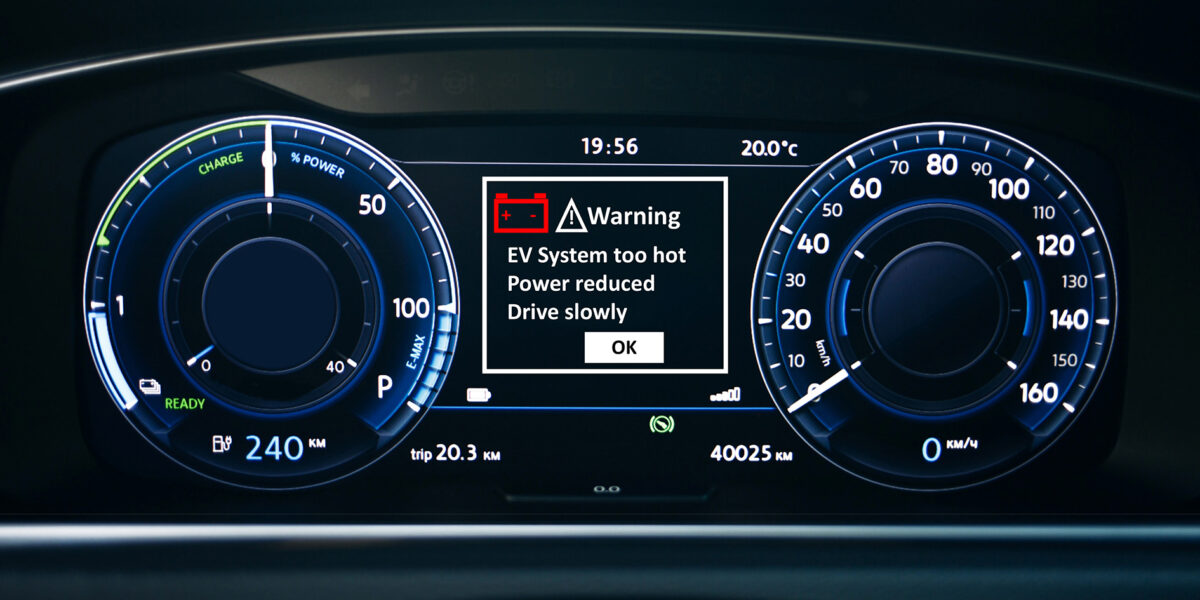
Bei einer überhitzten Antriebsbatterie gibt es mitunter zuerst eine Warnung, nebst Leistungsreduktion... im schlimmsten Fall folgt dann die Komplettabschaltung.
Foto: Inficon
Ein Klimaanlagen-Ausfall bedeutet für die Insassen üblicherweise Komforteinbußen, für den Fahrzeughersteller oft Garantiekosten und für die Werkstatt Reparaturaufwand. Doch bei einem Electric Vehicle (EV) sind die Folgen deutlich weitreichender: Bei Lithium-Ionen-Batterien reduziert eine zu hohe Betriebstemperatur nicht nur die Leistung – es besteht sogar die Gefahr eines desaströsen „Thermal Runaways“. Solch eine ungebremste Überhitzung der Traktionsbatterie führt in der Regel zu einem Brandgeschehen und zur völligen Zerstörung des Fahrzeugs.
Teil 1 des zweiteiligen Fachbeitrags stellt die Wechselwirkungen zwischen der Dichtigkeit des Kühlsystems und dem Thermomanagement vor. Außerdem werden Methoden der Vorprüfung beschrieben. In Teil 2 des Beitrags wird auf verschiedene Prüfvarianten und -systeme in den weiteren Schritten der Fahrzeugproduktion eingegangen.
Der Kühlkreislauf muss zuverlässig funktionieren – wie gelingt dies?
Wenn Kältemittel aus einer Klimaanlage austritt, ist das unschön, wenn aber die Kühlung der Antriebsbatterie schwächelt, wird das ohne Sicherheitsabschaltung fatal. Auf den verschiedenen Stufen des Fertigungsprozesses der Batteriekühlung führt darum an einer sorgfältigen industriellen Dichtheitsprüfung kein Weg vorbei.
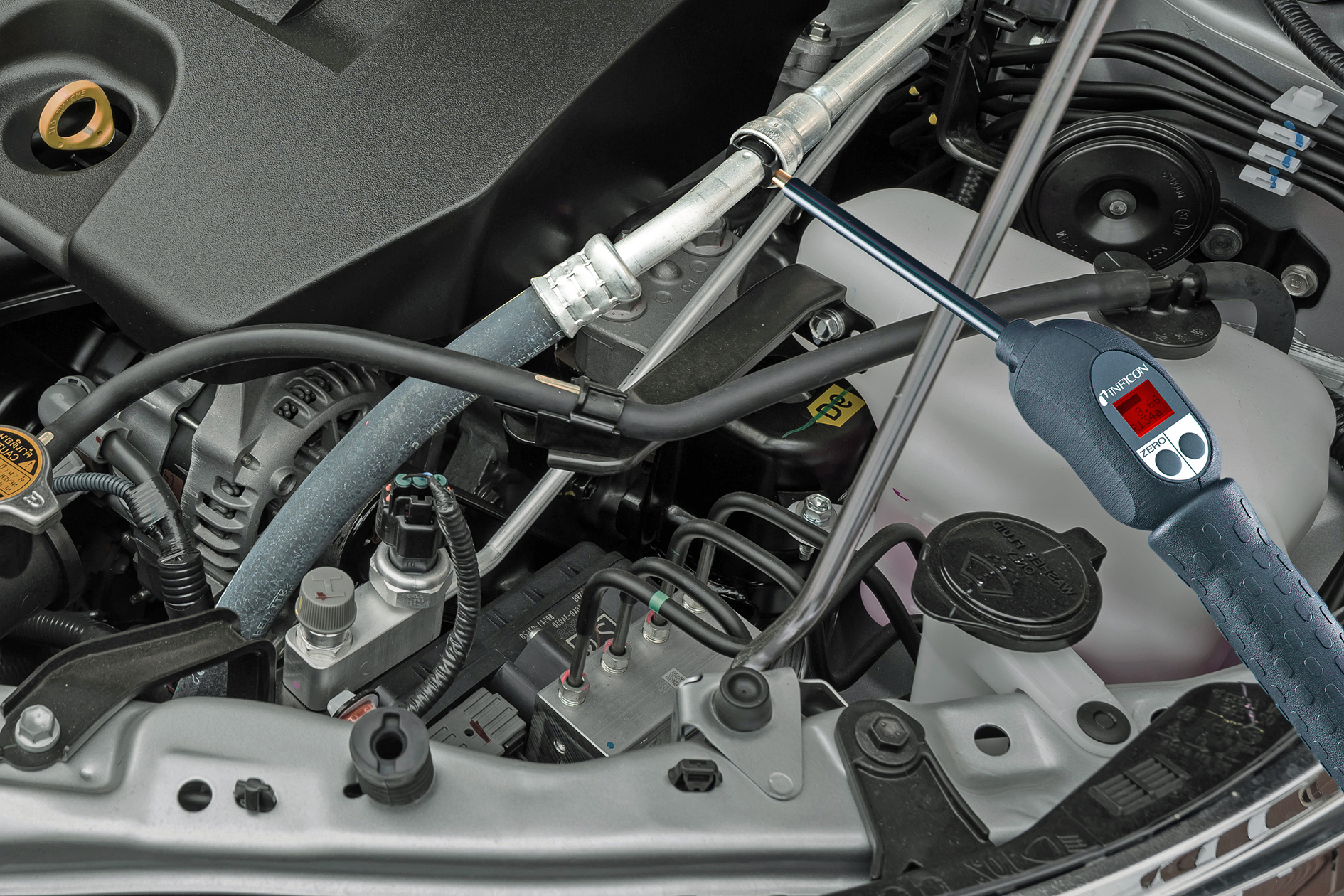
End-of-Line-Prüfungen per Schnüffellecksuche sind auch bei der Fertigung von Verbrennerfahrzeugen Standard.
Foto: Inficon
Auch wenn die Sicherheitsmechanismen greifen und das Thermal Management die Batterie automatisch abschaltet, ist die anschließende Reparatur doch mit erheblichen Kosten verbunden. Ein Kältemittelverlust durch ein Grobleck im ersten Jahr bedeutet meist, dass der Hersteller für die Reparatur aufkommt, im zweiten und dritten Jahr trägt die Werkstatt die Kosten, und erst von Jahr vier an zahlt der Käufer des Fahrzeugs die Reparatur selbst. Ein erheblicher Faktor sind neben den Kosten für die Reparatur aber auch die Preise für die Kältemittel. Immerhin kosten moderne, weniger klimaschädliche Kältemittel wie R1234yf oder R1234ze oft das Vier- bis Fünffache des alten, in der EU verbotenen R134a.
Kein erfolgreiches Temperaturmanagement ohne dichte Kühlsysteme
Die Klimaanlage hat also in Elektrofahrzeugen eine für den Betrieb sehr wesentliche Funktion – auch wenn die Batterie meist nicht durch denselben Kühlkreislauf gekühlt wird wie der Fahrzeug-Innenraum. In der Regel arbeitet die entsprechend groß dimensionierte Klimaanlage mit einem Kältemittel. Sie hat dann zum einen die Aufgabe, den Fahrgastraum zu kühlen, und zum anderen – über einen Wärmetauscher – den mit einem Wasser-Glykol-Gemisch befüllten Kühlkreislauf der Antriebsbatterie auf der optimalen Betriebstemperatur zu halten. Manche Fahrzeughersteller ziehen es jedoch vor, auch die Batterie mit Kältemittel zu kühlen – über einen Abzweig im Kältemittelkreislauf der Klimaanlage. In jedem Fall existiert beim Elektrofahrzeug die Erfordernis, die Batterie stets auf einer idealen Betriebstemperatur zu halten, in einem sehr eng definierten Temperaturfenster. Beim Kaltstart des Elektrofahrzeugs fungiert die Klimaanlage darum sogar als Wärmepumpe, damit die Traktionsbatterie schnell die optimale Temperatur erreicht.
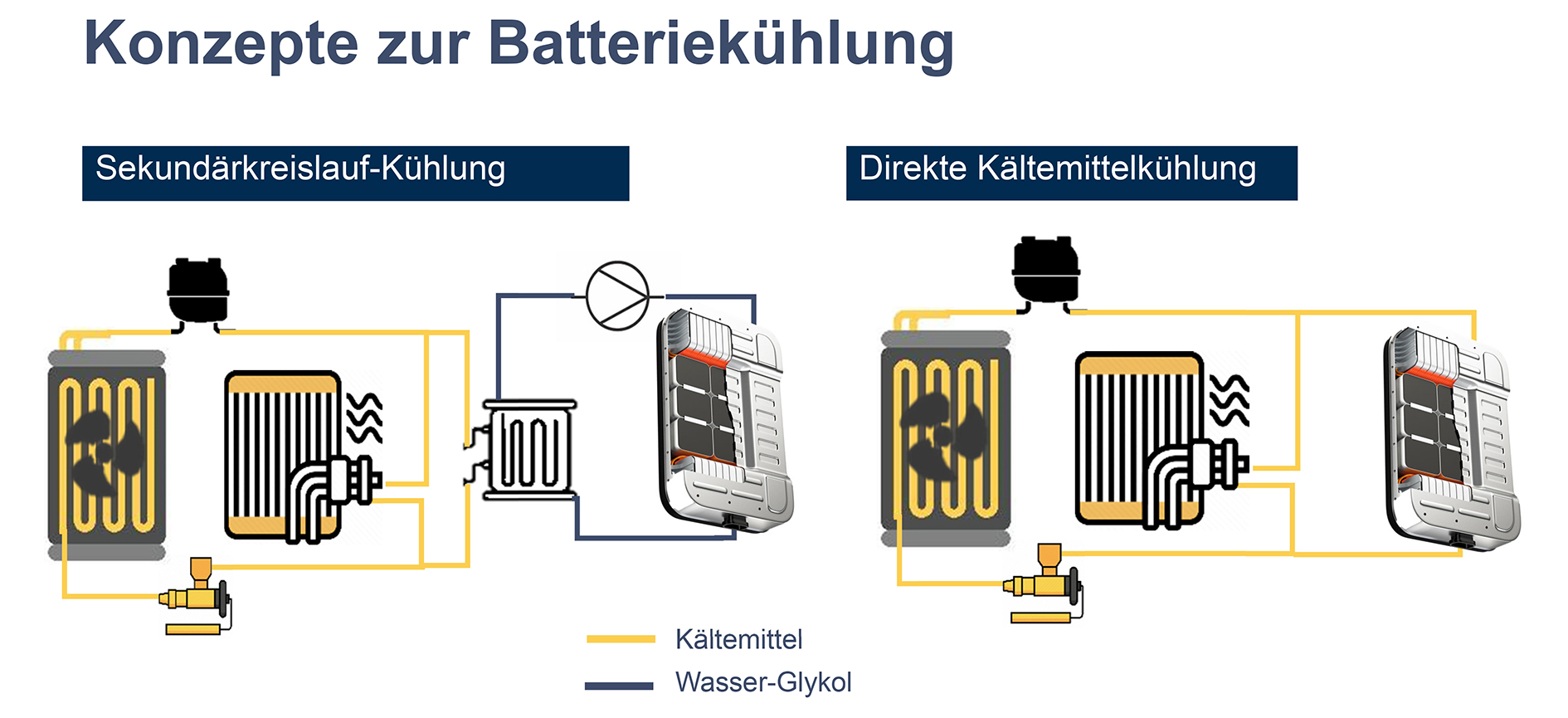
Antriebsbatterien werden entweder direkt gekühlt, und zwar mit dem Kältemittel der Klimaanlage, oder per Wasser-Glykol-Sekundärkreislauf und Wärmetauscher. Grafik: Inficon
Das Temperaturmanagement ist für die Funktionsfähigkeit eines Elektrofahrzeugs von zentraler Bedeutung. Darum werden sorgfältige Dichtheitsprüfungen bei der industriellen Fertigung und beim Einbau der Klimaanlage unverzichtbar. Die Klimaanlage eines herkömmlichen Fahrzeugs mit Verbrennungsmotor hat Herstellern bei der Qualitätssicherung noch einen gewissen Spielraum gelassen – das Kühlsystem eines Elektrofahrzeugs tut dies nicht mehr. Hier braucht es höhere Sorgfalt und kleinere Leckgrenzwerte.
Die Helium-Vakuummethode zur Vorprüfung
Zur Vorprüfung der diversen Komponenten des Kühlsystems kommt in den Produktionslinien der Zulieferer Helium als Prüfgas zum Einsatz. Dabei werden Komponenten wie etwa Kondensatoren, Verdampfer, Klimaanlagenschläuche und Expansionsventile in der Regel in einer Vakuumkammer auf ihre Dichtheit geprüft. Der Vorteil der Vakuummethode ist zum einen ihre Genauigkeit und zum anderen ihre hohe Geschwindigkeit. Bei der Vakuummethode wird das Prüfteil zunächst evakuiert und mit Helium befüllt. In der Prüfkammer wird dann ein Vakuum erzeugt, sodass etwaig austretendes Heliumprüfgas schnell detektiert werden kann.
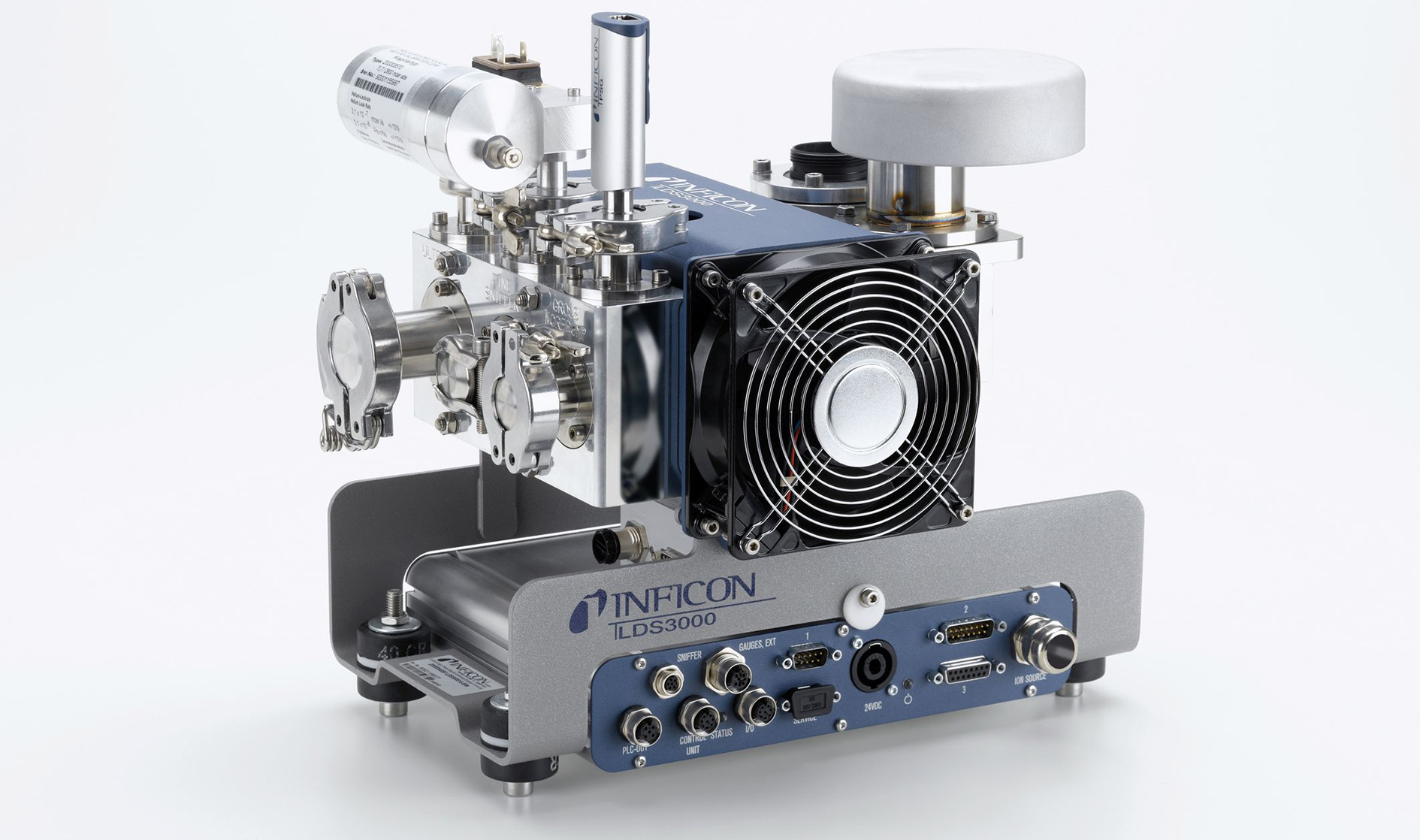
Der modulare Vakuumdichtheitsprüfer „LDS3000“ hat sich in unzähligen industriellen Fertigungslinien bewährt.
Foto: Inficon
Mit einem industriellen Helium-Dichtheitsprüfgerät wie dem „LDS3000“ von Inficon ist es einfach, gegen kleine Rückweisungsleckraten von bis zu 1·10–6 mbar·l/s zu prüfen – was einem Kältemittelverlust von 0,2 g pro Jahr entspricht. Während bei den Vakuumvorprüfungen der Komponenten oft noch mit Heliumleckraten gerechnet wird, ist für folgende Dichtheitsprüfungen der Kältemittelverlust pro Jahr die gebräuchliche Einheit. Oft besteht das Ziel darin, den Kältemittelverlust auf 0,5 bis 2 g pro Jahr zu begrenzen. Lecks in dieser Größenordnung entsprechen Helium-Leckraten von 1·10–5 bis 8·10–6 mbar·l/s.
Schnüffellecksuche zur Vorprüfung von Kompressoren
Der Kompressor der Klimaanlage eignet sich dagegen nicht für eine Vorprüfung in der Vakuumkammer. Stattdessen kommt hier eine Schnüffellecksuche zum Einsatz. Das Prüfteil wird dazu entweder mit Helium als Prüfgas befüllt oder mit dem kostengünstigeren Formiergas, einem unbrennbaren Gemisch aus 5 Prozent Wasserstoff und 95 Prozent Stickstoff. Fährt man dann mit der Schnüffelspitze eines Schnüffellecksuchers über die Oberfläche des Kompressors, lassen sich etwaige Leckstellen detektieren und lokalisieren. Auch die praktische Nachweisgrenze der industriellen Schnüffellecksuche bewegt sich im Bereich von 10–6 mbar·l/s. Ein industrielles Schnüffellecksuchgerät wie der XL3000flex detektiert sogar Lecks bis hinab zu 2·10–7 mbar·l/s, unabhängig davon, ob als Prüfgas Helium oder ein Wasserstoffgemisch zum Einsatz kommt. Oft wird diese Schnüffellecksuche auch in Form einer robotischen Prüfung automatisiert.
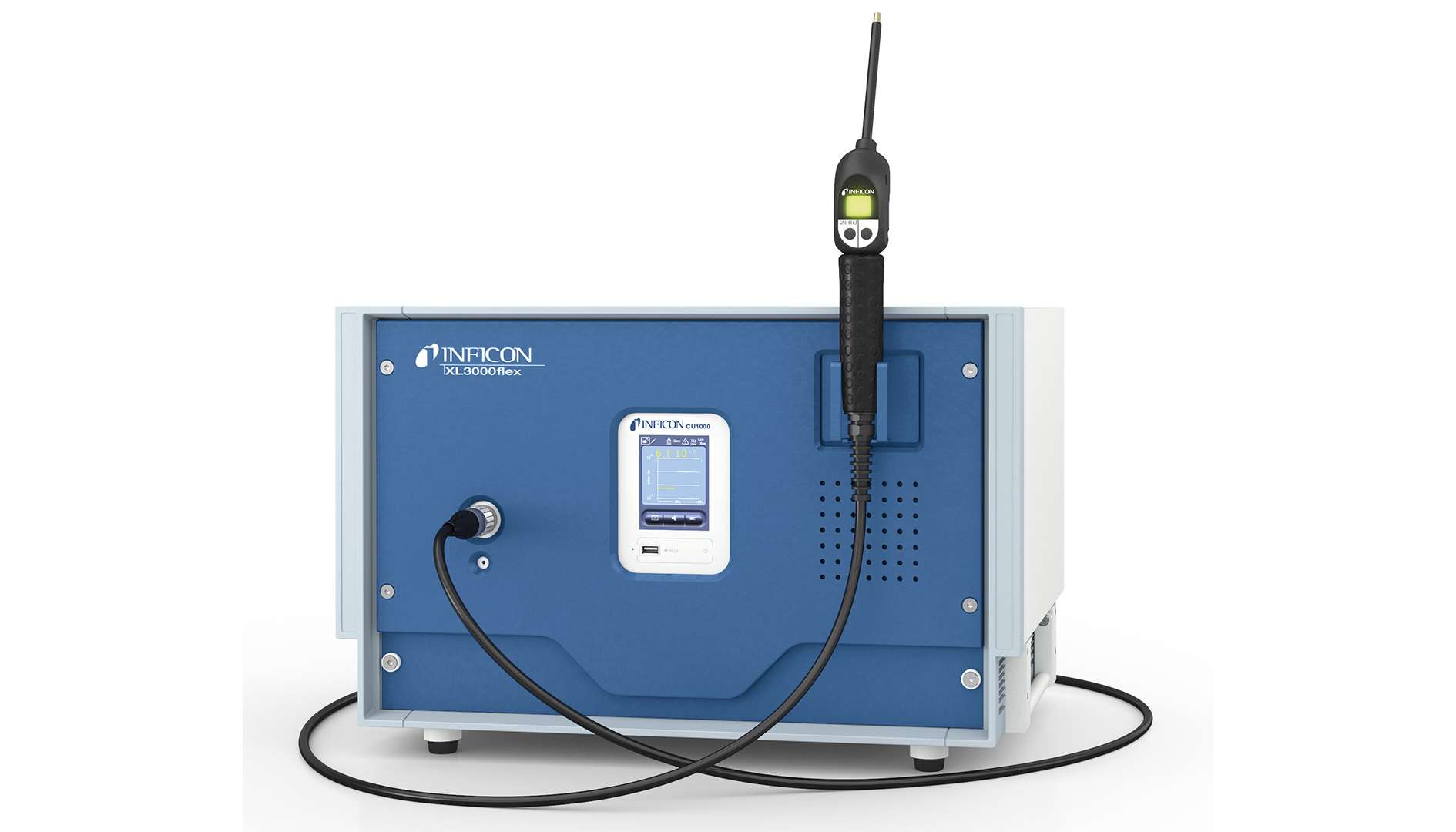
Der „XL3000flex“ erlaubt die industrielle Schnüffellecksuche, wahlweise mit Helium oder Formiergas als Spürgas.
Foto: Inficon
Die nächsten Dichtheits-Prüfaufgaben stehen dann nach dem Zusammen- beziehungsweise Einbau der Klimaanlage an. Dies geschieht beim Fahrzeughersteller. Sie werden in Teil 2 des Beitrags beschrieben.
Das könnte Sie auch interessieren:
Fahrzeugbau: Energieeffizienz steigern dank Gewichtsreduktion
Karosseriebearbeitung: Fehlstellen erkennen und zuverlässig beseitigen
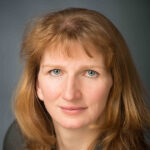
Sandra Seitz ist Market Manager Automotive Leak Detection Tools bei der Inficon GmbH in Köln. Foto: Inficon