Wie die digitale Zukunft des Maschinenbaus funktioniert
Automatisierung ist kein Automatismus – Maschinenbaubetriebe müssen ihren Teil dazu beitragen, zum Beispiel mit der Einführung digitaler Lösungen. Einige Leitlinien, die zum Erfolg führen, gilt es dabei zu beachten.
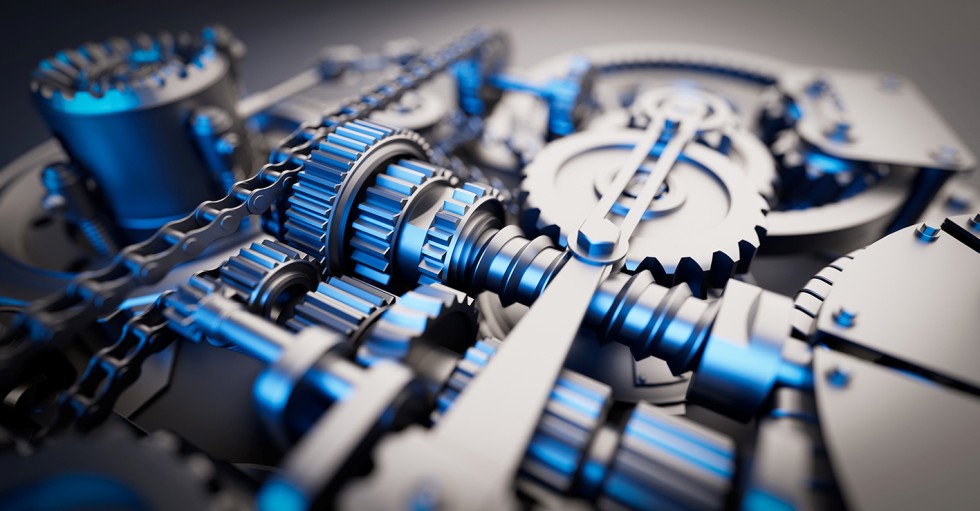
Maschinenbau-Unternehmen profitieren zum Jahresanfang 2022 von einer positiven wirtschaftlichen Entwicklung. Nun gilt es, die Engineeringprozesse entsprechend anzupassen.
Foto: stock.adobe.com
Die „Schonzeit“ im Maschinenbau ist längst vorbei. Laut VDMA (Verband Deutscher Maschinen- und Anlagenbau e. V.) ist die Digitalisierung in der Branche schon lange angekommen. Und der größte Verband für Maschinenbau in Europa prognostiziert darüber hinaus für 2022 ein Industriewachstum von 7 Prozent (Stand: Februar 2022). Es ist eine positive Entwicklung, bei der die Digitalisierung eine wichtige Rolle spielt. Denn mehr Effizienz bedeutet mehr Wachstum.
Umfragen bestätigen den Trend
Dem Trend folgend, steigt die Nachfrage für digitale Lösungen stets weiter an. Einer Studie von logi.cals und der Universität Magdeburg zufolge schreiben 65 Prozent der Befragten den cloudbasierten Lösungen in der Steuerungstechnik eine sehr hohe Bedeutung zu. Über 30 Prozent sind der Meinung, dass Engineering-Plattformen in der Cloud zu mehr Effizienz in Engineering führen würden.
Außerdem: Laut einer kürzlich durchgeführten McKinsey-Umfrage gaben 66 Prozent der Befragten an, dass sie sich bemühen, ihre Prozesse über mehrere Geschäftsbereiche hinweg zu automatisieren. Während die Automatisierung zunimmt, werden nur die Unternehmen, die ihr Controlling entsprechend anpassen, mit den rasanten Entwicklungen auf dem globalen Markt Schritt halten können. Die Automatisierung im Maschinenbau gilt nicht nur für die Produktion, sondern auch für das Datenmanagement im Allgemeinen. Automatisierung beeinflusst die komplette Wertschöpfungskette von der Produktion bis hin zur Finanzabteilung.
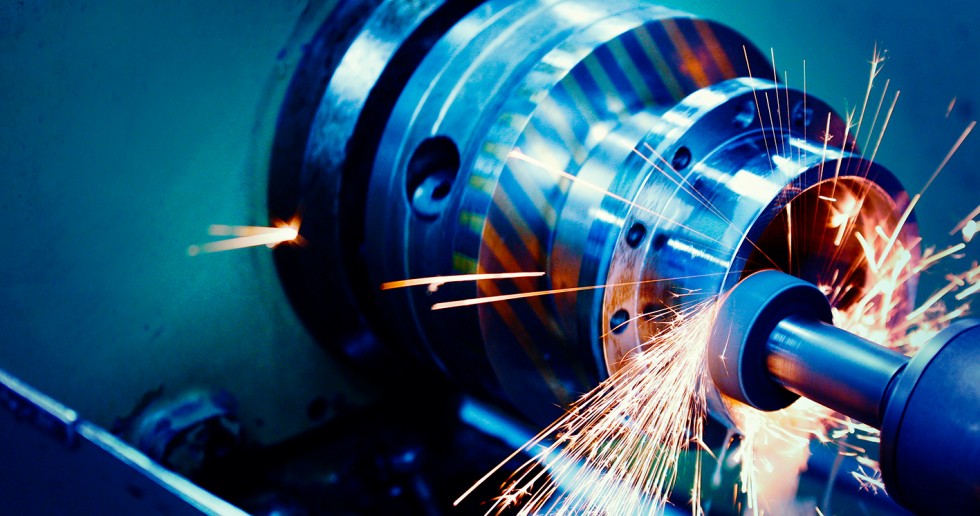
Zerspanende Fertigung: Die Automatisierung im Maschinenbau betrifft neben der Produktion ebenso das Datenmanagement im Allgemeinen.
Foto: stock.adobe.com
Erfolgsbeispiele: Fallstudie der MS Group
Die MS Group ist eine Industriegruppe mit den Geschäftsfeldern Antriebstechnik und Ultraschalltechnik unter dem Dach der börsennotierten MS Industrie AG. Zu den wesentlichen Kunden zählen unter anderem die Nutzfahrzeug- und die Pkw-Industrie sowie die Verpackungsmaschinenindustrie und der allgemeine Maschinen- und Anlagenbau. Das Unternehmen verfügt über Produktionsstandorte in Deutschland, den USA, China und Brasilien.
Als Spezialist für Sondermaschinenbau im Automotive-Bereich suchte die MS Group insbesondere eine leistungsfähige Lösung, die ein zentrales Multi-Projektmanagement mit automatisierten Workflows über alle Gesellschaften unterstützt. Die bislang manuell erstellten Excel-Pläne waren für die Abwicklung der komplexen Projekte – mit vielen Beteiligten, langen Laufzeiten und Risiken (wie Störfälle, Engpässe oder Vertragsstrafen) – nicht mehr angemessen. Das zuständige Projektteam entschied, eine in SAP integrierte Lösung mit der CPM-Software, die bereits für Standardreports im Haus existierte, zu kombinieren. CPM steht für „Corporate Performance Management“ und bezieht sich auf das Beobachten und Verwalten der Leistung eines Unternehmens.
Neues Projektreporting: Leistungsdaten permanent kontrollieren
Mit einem systemübergreifenden Blick auf den Gesamtprozess wurden mit CPM die Projektabwicklung über die gesamte Wertschöpfungskette mit der komplementären Softwarelösung neu aufgesetzt. Dadurch wurden Prozesse optimiert und ein übersichtliches Projektreporting gestaltet. Die Projekte werden weiterhin in SAP angelegt, wo auch die terminliche Eskalation mit aktiver Benachrichtigung der Nutzer definiert wird.
In der neu angebundenen CPM-Software läuft die Auswertung und transparente Visualisierung mit farblich kodierten Alarmstufen ab. Damit konnte die Unternehmensgruppe alle Projekte mit sämtlichen Akteuren synchron steuern und jederzeit einen Gesamtüberblick über den tagesaktuellen Status behalten. Zusätzlich wird so die Analyse von historischen Verläufen möglich.
Indem die MS Group ihren manuellen Projektplan durch ein tagesaktuelles Multi-Projektmanagement mit Real-time-Abbildung der Lieferkette ersetzt hat, haben Entscheidungsträger Zugang zu Daten ohne jegliche Zeitverzögerung. Zentraler Erfolgsfaktor des Projekts war die parallele Prozess- und Reportingumstellung im nahtlosen Zusammenspiel von SAP und der neuen Software. So konnte ein übersichtliches Projektreporting gestaltet werden, das zur hohen Akzeptanz der Steuerungslösung in der gesamten Unternehmensgruppe geführt hat.
Fallstudie Steinert: Flexible Anpassung an neue Geschäftsentwicklungen
Ein zweites Beispiel aus dem Maschinenbau erläutert den Erfolg von automatisierten Prozessen für eine renommierte Firma aus Köln. In den Bereichen der Aufbereitung von Sekundär- und Primärrohstoffen bewegt sich das 1889 gegründete Familienunternehmen Steinert in der Entsorgungs- und Recyclingwirtschaft sowie im Bergbau. Zudem ist der Betrieb ein führender Anbieter für innovative Magnet-Separationstechnik und Sensor-Sortierung. Die Globalität des Kölner Unternehmens bringt komplexe Geschäftsprozesse mit sich, welche von der Lieferung einzelner Sortiermaschinen bis hin zur Verfolgung mehrjähriger Projekte in der Entsorgungs- und Recyclingwirtschaft sowie im Bergbau reichen.
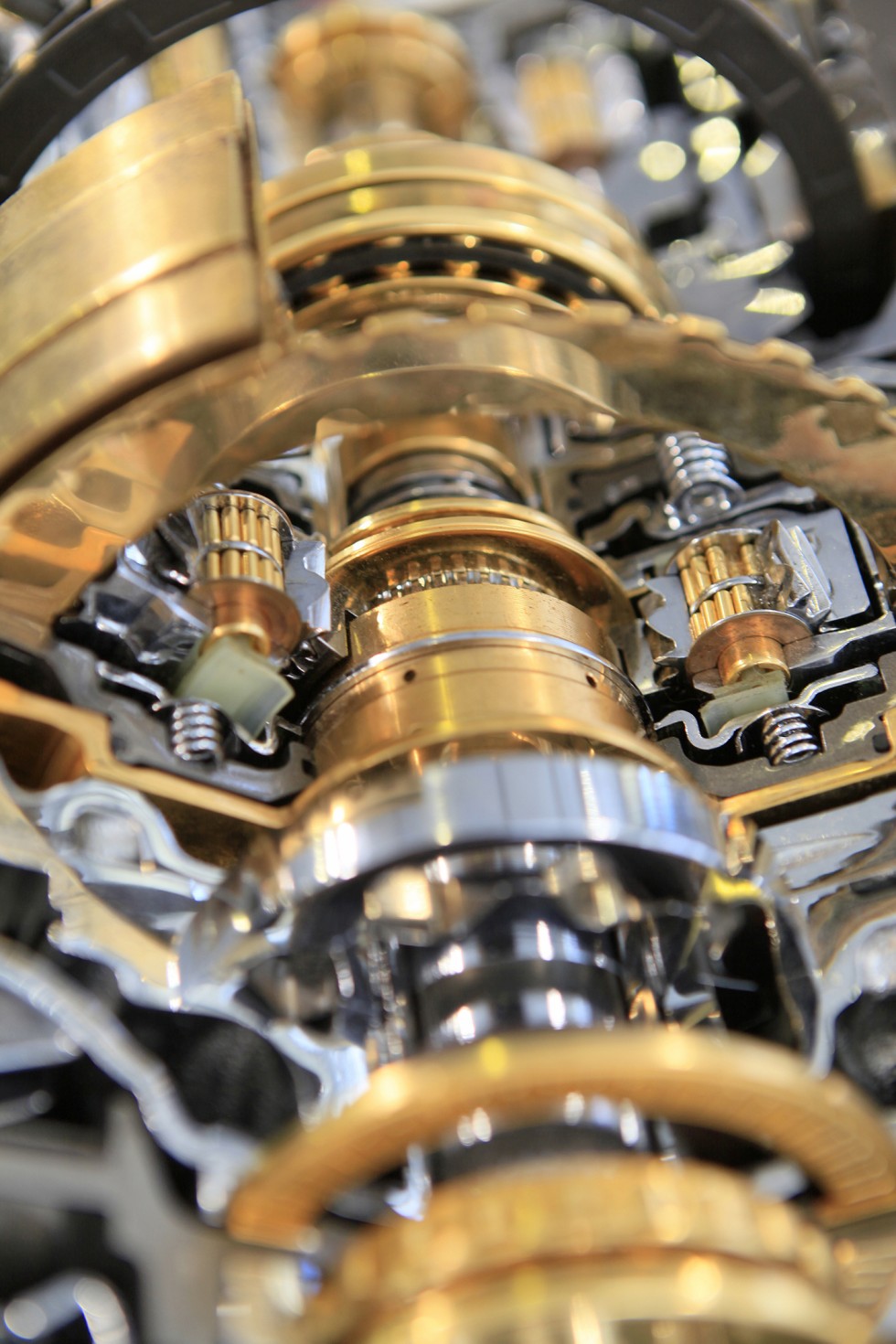
Bei komplexen Geschäftsprozessen ist das Controlling der diversen Projekte anspruchsvoll – notwendig ist ein flexibles Planungs- und Reportingsystem.
Foto: stock.adobe.com
Die einzelnen Aufträge sind sowohl vom Zeithorizont als auch vom Umsatz her enorm unterschiedlich. Dementsprechend ist das Controlling der diversen Projekte anspruchsvoll und komplex. Vor allem im Bereich Planung ist für das Unternehmen eine hohe Flexibilität wichtige Voraussetzung. Steinert benötigte daher ein sehr flexibles Planungs- und Reportingsystem, das die Fachabteilung eigenständig steuern und auch kurzfristig an neue Geschäftsentwicklungen anpassen kann. Das bestehende Berichtswesen auf Basis von Excel-Sheets sollte durch eine integrierte Softwarelösung mit zentraler Datenbasis ersetzt werden. Wichtig war auch eine anwenderfreundliche Plattform, welche vom zuständigen Controller eigenständig beherrscht und weiterentwickelt werden kann.
Workflow optimiert, Ressourcen gespart
Das Controlling konnte nach der Implementierung der neuen integrierten Softwarelösung multidimensionale Modelle selbst kreieren. Die in Echtzeit aggregierten Ist- und Plandaten lagen direkt als zentrale Datenbasis für das Berichtswesen vor. Plausibilisierungsfunktionen, Workflows und automatische Berechnungen sichern dabei effiziente, fehlerfreie Berichtsprozesse, die durch manuelle Eingaben niemals möglich gewesen wären. Besonders hilfreich sind die automatische Währungsumrechnung sowie die Deckungsbeitragsrechnungen in verschiedenen Perspektiven. Durch die Genauigkeit und Effizienz der digitalen Lösung hat die Automatisierung der Steuerungsprozesse der Firma Zeit und wertvolle Ressourcen gespart. Jetzt hat das Controlling einen besseren Überblick und kann schnell agieren, wenn akuter Handlungsbedarf besteht.
Fazit
In der Maschinenbau-Industrie besteht tatsächlich Handlungsbedarf für diejenigen, die noch nicht „auf den digitalen Zug gesprungen sind“. Die beiden Anwendungsbeispiele stehen stellvertretend für die umfangreichen Potentiale, die es zu erschließen gilt. Die Industrieprognose für 2022 ist gut – für die „Digitaltransformierten“ ist sie sogar noch besser.
Das könnte Sie auch interessieren:
Wie Maschinenbauer von den Vorteilen der Digitalisierung profitieren
Ist die Industrie auf dem Weg zur digitalen Exzellenz?
Wie eine zentrale Datenplattform die Digitale Fabrik voranbringt
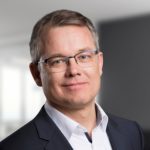
Dr. Rolf Gegenmantel ist CPO bei Jedox, einem führenden Anbieter von EPM-Softwarelösungen. Dort ist er seit 2011 ist er für die weltweiten Marktaktivitäten und die Unternehmensberatung verantwortlich. Er verfügt über mehr als 20 Jahre Erfahrung in den Bereichen BI (Business Intelligence) und Enterprise Performance Management. Nach seiner Promotion in Wirtschaftswissenschaften an der renommierten Goethe-Universität sammelte Gegenmantel Erfahrungen bei großen BI-Anbietern in Europa und Nordamerika – dazu gehört umfangreiche Expertise in der Positionierung, Implementierung und den Geschäftsergebnissen von BI-Lösungen. Foto: Autor